Understanding particle size distribution is crucial in various industries, particularly those dealing with metal powders. This article provides a comprehensive look at particle size distribution, focusing on its importance, methods of measurement, characteristics, and applications, particularly in metal powders. We’ll explore specific metal powder models, their properties, and applications, and compare their advantages and limitations. So, let’s dive in!
Overview of Particle Size Distribution
Particle size distribution (PSD) is a key factor in the characterization of powdered materials. It describes the proportions of particles of different sizes in a sample and is vital for predicting the behavior of the powder in various processes.
Key Details of Particle Size Distribution:
- Definition: Measurement of the range and quantity of particle sizes in a given sample.
- Importance: Affects the physical and chemical properties of the material.
- Methods: Sieving, laser diffraction, dynamic light scattering, and sedimentation.
Understanding PSD helps in optimizing the performance and quality of products in industries such as pharmaceuticals, ceramics, and metallurgy.
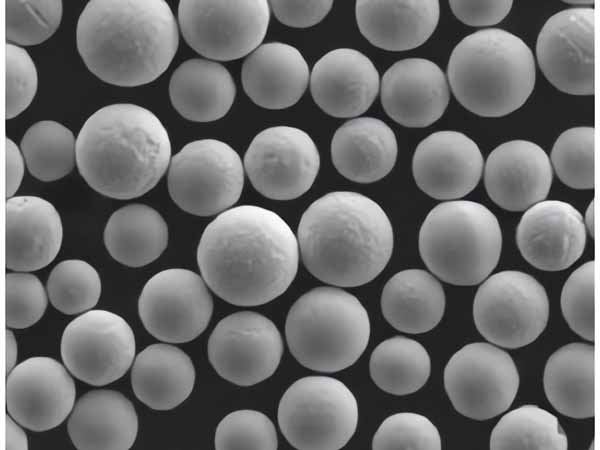
Types of Metal Powders and Their Particle Size Distribution
Here are specific metal powder models with their descriptions:
Metal Powder | Composition | Properties | Characteristics |
---|---|---|---|
Aluminum Powder | Pure Aluminum (Al) | Lightweight, high surface area, good thermal conductivity | Irregular shape, used in pyrotechnics |
Copper Powder | Pure Copper (Cu) | High electrical conductivity, corrosion-resistant | Spherical or dendritic shapes, used in electronics |
Iron Powder | Pure Iron (Fe) | Magnetic properties, reactive to oxygen | Irregular or spherical shapes, used in metallurgy |
Nickel Powder | Pure Nickel (Ni) | High melting point, resistant to oxidation and corrosion | Spherical shape, used in batteries |
Titanium Powder | Pure Titanium (Ti) | High strength-to-weight ratio, corrosion-resistant | Spherical shape, used in aerospace |
Tungsten Powder | Pure Tungsten (W) | High density, high melting point | Spherical shape, used in heavy metal alloys |
Zinc Powder | Pure Zinc (Zn) | Good electrochemical properties, used for galvanization | Irregular shape, used in batteries and coatings |
Silver Powder | Pure Silver (Ag) | Highest electrical conductivity, antimicrobial properties | Flaky or spherical shape, used in electronics and medical applications |
Gold Powder | Pure Gold (Au) | High conductivity, resistance to tarnish | Spherical or flaky shapes, used in electronics and jewelry |
Stainless Steel Powder | Alloy of Iron, Chromium, Nickel | Corrosion-resistant, high strength | Irregular or spherical shapes, used in 3D printing and manufacturing |
Composition of Particle Size Distribution
The composition of a particle size distribution is critical because it dictates the properties and behavior of the powder in different applications. For example, smaller particles have a higher surface area-to-volume ratio, which can influence reaction rates and sintering behavior.
Key Factors Affecting Composition:
- Material Type: Different materials have different particle size distributions.
- Production Method: Atomization, mechanical milling, and chemical processes can produce varying PSDs.
- Application Requirements: Different applications may require specific PSDs for optimal performance.
Properties and Characteristics of Particle Size Distribution
Understanding the properties and characteristics of PSD is essential for optimizing the use of metal powders in various applications.
Key Properties:
- Particle Shape: Spherical, irregular, dendritic, or flaky.
- Size Range: Microns to nanometers.
- Distribution: Unimodal, bimodal, or multimodal.
Characteristics:
- Flowability: How easily the powder flows.
- Packing Density: How densely the powder can pack.
- Surface Area: Influences reaction rates and sintering behavior.
Methods of Measuring Particle Size Distribution
There are several methods to measure PSD, each with its advantages and limitations. Here are some common techniques:
Method | Principle | Advantages | Limitations |
---|---|---|---|
Sieving | Separation by passing through sieves of different sizes | Simple, inexpensive | Limited to larger particles |
Laser Diffraction | Measuring light scattering from particles | Fast, broad size range | Requires calibration, sensitive to particle shape |
Dynamic Light Scattering | Analyzing fluctuations in light scattering | Suitable for small particles | Sensitive to impurities |
Sedimentation | Particles settle under gravity or centrifugal force | Good for fine particles | Time-consuming, affected by particle density |
Applications of Particle Size Distribution
PSD plays a crucial role in various applications, influencing properties like strength, reactivity, and density. Here are some common applications:
Application | Metal Powder Used | Importance of PSD |
---|---|---|
Additive Manufacturing | Stainless Steel, Titanium | Ensures uniform layer formation and sintering behavior |
Pharmaceuticals | Iron, Zinc | Affects dissolution rates and bioavailability |
Electronics | Copper, Silver, Gold | Influences conductivity and component miniaturization |
Catalysts | Nickel, Platinum | Higher surface area improves catalytic activity |
Battery Manufacturing | Nickel, Zinc | Impacts electrode performance and longevity |
Cosmetics | Titanium, Zinc | Affects texture and application properties |
Metallurgy | Iron, Tungsten | Determines sintering and mechanical properties of the final product |
Coatings | Aluminum, Zinc | Influences coating thickness and uniformity |
Aerospace | Titanium, Aluminum | Impacts strength-to-weight ratio and thermal properties |
Medical Devices | Stainless Steel, Silver | Ensures biocompatibility and precision in medical implants |
Specifications, Sizes, Grades, and Standards
Metal powders come in various specifications, sizes, grades, and standards to meet specific application requirements. Here is a detailed look:
Metal Powder | Specification | Size Range | Grades | Standards |
---|---|---|---|---|
Aluminum Powder | ASTM B212 | 1-200 microns | High Purity, Alloy | ISO 209-1:2007 |
Copper Powder | ASTM B170 | 0.1-100 microns | Electrolytic, Atomized | ISO 4289:1989 |
Iron Powder | ASTM B214 | 1-300 microns | Reduced, Atomized | ISO 3923-1:1976 |
Nickel Powder | ASTM B330 | 0.5-200 microns | Carbonyl, Electrolytic | ISO 4499-3:1988 |
Titanium Powder | ASTM B299 | 5-150 microns | Commercial, Grade 5 | ISO 4497:1983 |
Tungsten Powder | ASTM B777 | 1-100 microns | High Purity, Alloy | ISO 4491-2:1980 |
Zinc Powder | ASTM B328 | 1-200 microns | Electrolytic, Atomized | ISO 4498:1985 |
Silver Powder | ASTM B748 | 0.5-50 microns | High Purity | ISO 4497:1983 |
Gold Powder | ASTM B488 | 0.5-20 microns | High Purity | ISO 4498:1985 |
Stainless Steel Powder | ASTM B212 | 10-150 microns | 304, 316 | ISO 4499-3:1988 |
Suppliers and Pricing Details
When it comes to sourcing metal powders, it’s essential to consider both the supplier’s reputation and the pricing. Here’s a comparison of some suppliers:
Supplier | Metal Powder | Price per kg | Availability | Quality Certification |
---|---|---|---|---|
Sigma-Aldrich | Aluminum, Copper, Iron | $50 – $100 | High | ISO 9001 |
Höganäs AB | Iron, Stainless Steel | $30 – $150 | High | ISO 14001 |
American Elements | Titanium, Tungsten, Zinc | $100 – $500 | Medium | ISO 9001 |
Sandvik | Stainless Steel, Nickel | $40 – $200 | High | ISO 45001 |
Atlantic Equipment Engineers | Silver, Gold | $500 – $2000 | Low | ISO 9001 |
Advantages and Limitations of Particle Size Distribution
Understanding the pros and cons of different PSDs is vital for choosing the right metal powder for your application.
Metal Powder | Advantages | Limitations |
---|---|---|
Aluminum Powder | Lightweight, good thermal conductivity | Reacts with oxygen, needs careful handling |
Copper Powder | Excellent electrical conductivity, corrosion-resistant | Higher cost, can oxidize |
Iron Powder | Magnetic properties, cost-effective | Can rust, lower electrical conductivity |
Nickel Powder | High melting point, corrosion-resistant | Expensive, health hazards in powder form |
Titanium Powder | High strength-to-weight ratio, corrosion-resistant | Expensive, challenging to process |
Tungsten Powder | High density, high melting point | Very heavy, difficult to process |
Zinc Powder | Good electrochemical properties, cost-effective | Lower strength, can be brittle |
Silver Powder | Highest electrical conductivity, antimicrobial properties | Very expensive, prone to tarnish |
Gold Powder | High conductivity, resistant to tarnish | Extremely expensive, soft and malleable |
Stainless Steel Powder | Corrosion-resistant, high strength | Heavier, more expensive than plain steel |
Detailed Comparison of Metal Powders
To make an informed decision, it’s essential to compare metal powders on various parameters:
Parameter | Aluminum | Copper | Iron | Nickel | Titanium | Tungsten | Zinc | Silver | Gold | Stainless Steel |
---|---|---|---|---|---|---|---|---|---|---|
Density (g/cm³) | 2.7 | 8.96 | 7.87 | 8.9 | 4.5 | 19.25 | 7.14 | 10.49 | 19.32 | 7.8 |
Melting Point (°C) | 660 | 1085 | 1538 | 1455 | 1668 | 3422 | 419.5 | 961.8 | 1064 | 1400 |
Electrical Conductivity (S/m) | 3.77e7 | 5.96e7 | 1.03e7 | 1.43e7 | 2.38e6 | 1.79e7 | 1.69e7 | 6.3e7 | 4.1e7 | 1.45e6 |
Cost (per kg) | Low | Medium | Low | High | High | Very High | Low | Very High | Extremely High | Medium |
Corrosion Resistance | Moderate | High | Low | Very High | Very High | Very High | Moderate | High | High | Very High |
Typical Applications | Aerospace, Pyrotechnics | Electronics, Plumbing | Metallurgy, Magnets | Batteries, Catalysts | Aerospace, Medical | Heavy Metal Alloys | Batteries, Galvanization | Electronics, Medical | Electronics, Jewelry | 3D Printing, Manufacturing |
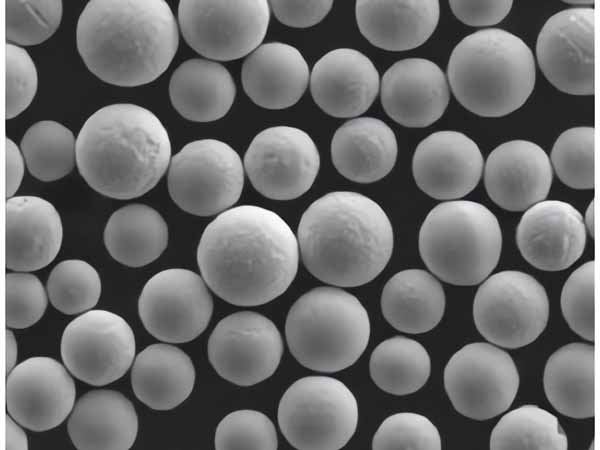
FAQs
Question | Answer |
---|---|
What is particle size distribution (PSD)? | PSD refers to the distribution of particle sizes in a material, indicating the range and quantity of different-sized particles in a sample. |
Why is PSD important? | PSD affects the material’s properties and behavior in applications, influencing factors like flowability, packing density, and reactivity. |
How is PSD measured? | Common methods include sieving, laser diffraction, dynamic light scattering, and sedimentation. |
What industries use PSD analysis? | Industries such as pharmaceuticals, metallurgy, ceramics, and electronics frequently use PSD analysis to optimize their products and processes. |
What are the characteristics of PSD? | Key characteristics include particle shape, size range, and distribution type (unimodal, bimodal, multimodal). |
How does PSD influence metal powders? | PSD affects properties like flowability, packing density, sintering behavior, and reaction rates in metal powders. |
Can PSD be customized for specific applications? | Yes, the PSD of metal powders can be tailored during production to meet specific application requirements. |
What are some challenges in measuring PSD? | Challenges include handling small particles, ensuring accurate calibration, and accounting for particle shape and density. |
Conclusion
Particle size distribution is a critical parameter in the characterization and application of metal powders. By understanding and controlling PSD, industries can optimize their products and processes for better performance and quality. Whether it’s for additive manufacturing, pharmaceuticals, or electronics, the right PSD can make a significant difference. So next time you’re working with metal powders, remember the importance of particle size distribution!