Overview
Powder Bed Fusion (PBF) is one of the most advanced and versatile additive manufacturing (AM) technologies, playing a crucial role in industries ranging from aerospace to medical implants. The quality of the metal powder used in the PBF technique directly impacts the final product’s properties, making it essential to choose the right powder. In this article, we’ll delve into the world of metal powders for PBF, providing you with an in-depth look at specific models, their compositions, characteristics, and applications.
We will discuss various types of metal powders, compare their properties, and examine their pros and cons. Additionally, we’ll explore their applications, specifications, and suppliers. This comprehensive guide is designed to help you make informed decisions about selecting the right metal powder for your PBF needs.
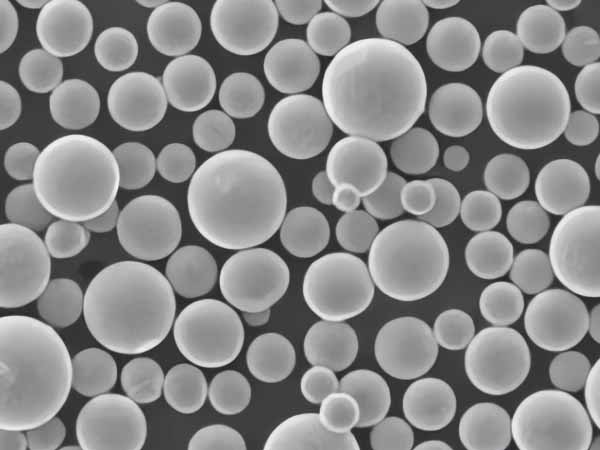
Understanding Powder Bed Fusion (PBF) and Its Importance
Powder Bed Fusion (PBF) is a group of AM technologies that use a heat source (usually a laser or electron beam) to selectively fuse powder particles layer by layer, creating a solid 3D object. The accuracy, strength, and overall quality of the final product largely depend on the characteristics of the metal powder used in the process.
Key Considerations for Metal Powders in PBF
- Particle Size Distribution: The powder’s particle size distribution affects the flowability and packing density, which in turn influences the quality of the printed object.
- Sphericity: High sphericity ensures better flowability and packing density, leading to higher quality parts.
- Purity: Impurities in metal powders can lead to defects in the final product, such as porosity or cracks.
- Chemical Composition: The chemical composition must be consistent to ensure the mechanical properties of the final product are as expected.
Types and Composition of Metal Powders for PBF
There are various types of metal powders available for PBF, each with unique compositions that make them suitable for different applications. Below is a detailed table listing some of the most common metal powders used in PBF, along with their compositions.
Metal Powder Model | Composition | Common Alloys | Notable Characteristics | Best Used For |
---|---|---|---|---|
316L Stainless Steel | Fe, Cr, Ni, Mo | 316L, 316 | Excellent corrosion resistance, high ductility | Medical implants, marine applications |
Ti-6Al-4V | Ti, Al, V | Grade 5 Titanium | High strength-to-weight ratio, biocompatibility | Aerospace, biomedical devices |
Inconel 718 | Ni, Cr, Fe, Nb, Mo | Inconel 718 | High temperature resistance, good weldability | Turbine blades, aerospace |
AlSi10Mg | Al, Si, Mg | AlSi10Mg | Lightweight, good thermal properties | Automotive, aerospace |
CoCrMo | Co, Cr, Mo | CoCrMo | High wear resistance, biocompatibility | Dental implants, orthopedic devices |
Maraging Steel | Fe, Ni, Co, Mo | 18Ni300 | High strength, easy heat treatment | Tooling, high-stress applications |
Copper (Cu) | Cu | Pure Cu, CuCrZr | High electrical and thermal conductivity | Electrical components, heat exchangers |
Hastelloy X | Ni, Cr, Mo, Fe | Hastelloy X | Excellent oxidation resistance, high temperature strength | Chemical processing, gas turbines |
Nickel Alloy 625 | Ni, Cr, Mo, Nb | Alloy 625 | High corrosion and oxidation resistance | Offshore, chemical processing |
Tool Steel H13 | Fe, Cr, Mo, V | H13, A2, D2 | High toughness, good heat resistance | Molds, dies, tooling components |
Characteristics of Metal Powders for PBF Technique
The characteristics of metal powders used in PBF determine the performance and quality of the final printed product. These characteristics include:
Characteristic | Description | Importance in PBF |
---|---|---|
Particle Size | Typically ranges from 15-45 microns | Smaller particles provide better resolution but may reduce flowability |
Sphericity | Measures how spherical the particles are | Higher sphericity improves flowability and packing density |
Flowability | The ability of the powder to flow smoothly | Essential for consistent layer deposition |
Purity | Absence of contaminants and impurities | Impurities can cause defects like porosity or cracks |
Density | The mass per unit volume | Affects the strength and structural integrity of the printed part |
Applications of Metal Powders in PBF Technique
Different metal powders are used for specific applications based on their properties. Here’s a table summarizing the typical applications of various metal powders in the PBF technique:
Metal Powder Model | Application | Industry | Key Benefits |
---|---|---|---|
316L Stainless Steel | Medical implants, marine components | Medical, Marine | Corrosion resistance, biocompatibility |
Ti-6Al-4V | Aerospace components, prosthetics | Aerospace, Medical | Lightweight, high strength-to-weight ratio |
Inconel 718 | Turbine blades, engine components | Aerospace, Power Generation | High-temperature resistance |
AlSi10Mg | Automotive parts, aerospace components | Automotive, Aerospace | Lightweight, good mechanical properties |
CoCrMo | Dental and orthopedic implants | Medical | Wear resistance, biocompatibility |
Maraging Steel | High-stress tooling, die casting molds | Tooling, Manufacturing | High strength, heat treatable |
Copper (Cu) | Electrical components, heat exchangers | Electronics, Energy | High conductivity |
Hastelloy X | Chemical processing, gas turbine components | Chemical, Aerospace | Oxidation resistance, high-temperature strength |
Nickel Alloy 625 | Offshore components, chemical processing | Oil & Gas, Chemical | Corrosion resistance |
Tool Steel H13 | Molds, dies, tooling components | Manufacturing | Toughness, heat resistance |
Specifications, Sizes, Grades, and Standards of Metal Powders
To meet the requirements of different applications, metal powders come in various grades, sizes, and standards. Below is a table summarizing these specifications:
Metal Powder Model | Grade | Particle Size (Microns) | Standards |
---|---|---|---|
316L Stainless Steel | AISI 316L | 15-45 | ASTM F138, ISO 5832-1 |
Ti-6Al-4V | Grade 5 | 15-45 | ASTM F1472, ISO 5832-3 |
Inconel 718 | AMS 5662 | 20-53 | ASTM B637, AMS 5662 |
AlSi10Mg | – | 20-63 | ASTM F3318 |
CoCrMo | ASTM F75 | 15-45 | ASTM F75, ISO 5832-4 |
Maraging Steel | 18Ni300 | 20-53 | AMS 6521 |
Copper (Cu) | CuCrZr | 15-45 | ASTM B170, ASTM B152 |
Hastelloy X | AMS 5536 | 20-53 | ASTM B435, AMS 5536 |
Nickel Alloy 625 | UNS N06625 | 20-53 | ASTM B446, AMS 5666 |
Tool Steel H13 | AISI H13 | 20-45 | ASTM A681 |
Suppliers and Pricing Details of Metal Powders
Selecting the right supplier for metal powders is crucial for maintaining quality and consistency in PBF processes. Below is a table listing some of the leading suppliers of metal powders, along with their pricing details:
Supplier | Metal Powder Model | Price per kg (USD) | Lead Time | Location |
---|---|---|---|---|
Carpenter Additive | 316L Stainless Steel | $80-$120 | 2-4 weeks | USA, Europe |
Arcam AB (GE Additive) | Ti-6Al-4V | $300-$400 | 3-5 weeks | USA, Sweden |
LPW Technology | Inconel 718 | $250-$350 | 2-4 weeks | USA, UK |
GKN Hoeganaes | AlSi10Mg | $70-$100 | 2-4 weeks | USA, Europe |
EOS GmbH | CoCrMo | $400-$600 | 3-6 weeks | Germany |
Höganäs AB | Maraging Steel | $100-$150 | 2-4 weeks | Sweden |
Ecka Granules | Copper (Cu) | $50-$80 | 2-3 weeks | USA, Europe |
Praxis Powder Technology | Hastelloy X | $300-$500 | 3-5 weeks | USA |
Sandvik | Nickel Alloy 625 | $250-$350 | 2-4 weeks | Sweden |
AP&C (GE Additive) | Tool Steel H13 | $80-$120 | 2-4 weeks | Canada |
Advantages and Limitations of Metal Powders in PBF
Choosing the right metal powder involves understanding the advantages and limitations of each type. Below is a comparison table outlining these aspects:
Metal Powder Model | Advantages | Limitations |
---|---|---|
316L Stainless Steel | Corrosion resistance, good weldability | Moderate strength |
Ti-6Al-4V | High strength-to-weight ratio, biocompatibility | Expensive, challenging to process |
Inconel 718 | High-temperature resistance, good fatigue strength | High cost, difficult to machine |
AlSi10Mg | Lightweight, good mechanical properties | Lower strength compared to other alloys |
CoCrMo | High wear resistance, excellent biocompatibility | Brittleness at high stress |
Maraging Steel | High strength, easily heat treatable | Expensive raw material |
Copper (Cu) | Excellent conductivity, good thermal properties | High oxidation rate, limited strength |
Hastelloy X | High-temperature oxidation resistance, good weldability | High cost, limited availability |
Nickel Alloy 625 | Corrosion resistance, good toughness | Expensive, difficult to weld |
Tool Steel H13 | High toughness, good heat resistance | Prone to cracking during cooling |
How to Select the Right Metal Powder for PBF
Selecting the right metal powder for PBF involves balancing various factors, such as mechanical properties, cost, availability, and compatibility with your specific application. Here are some key considerations:
- Application Requirements: Understand the mechanical, thermal, and chemical requirements of your final product.
- Powder Properties: Consider the particle size, distribution, sphericity, and flowability of the powder.
- Supplier Reputation: Choose reputable suppliers who provide consistent quality and reliable delivery.
- Cost: Balance the cost of the powder with the performance benefits it provides.
- Standards and Certifications: Ensure the powder meets relevant industry standards and certifications.
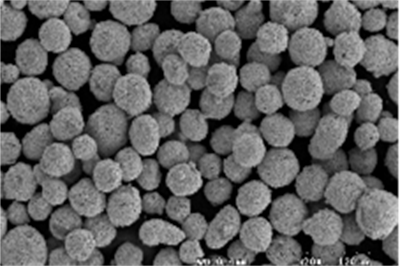
FAQs
Question | Answer |
---|---|
What is the ideal particle size for PBF metal powders? | The ideal particle size typically ranges from 15-45 microns, depending on the specific application and machine used. |
Can I reuse metal powder in PBF processes? | Yes, but the powder must be sieved and tested to ensure it maintains its quality. Repeated reuse can degrade the powder’s properties. |
How do I store metal powders for PBF? | Store in a dry, controlled environment to prevent contamination and oxidation. Use sealed containers and desiccants if necessary. |
What are the most common defects in PBF using metal powders? | Common defects include porosity, cracking, and incomplete fusion, often due to improper powder selection or processing parameters. |
How does powder sphericity affect PBF? | Higher sphericity improves flowability and packing density, leading to better layer formation and part quality. |
Is there a significant difference between gas-atomized and water-atomized powders? | Yes, gas-atomized powders tend to have higher sphericity and fewer impurities, making them more suitable for high-quality PBF processes. |
Conclusion
The selection of metal powders for the PBF technique is a critical decision that can significantly affect the outcome of your additive manufacturing project. By understanding the different types of metal powders available, their characteristics, and their applications, you can make informed choices that ensure the success of your production process.
Whether you are working in aerospace, automotive, medical, or any other industry, this guide provides you with the necessary information to select the right metal powder for your needs. Remember, the key to successful PBF is not just in the technology but in the materials you choose to work with.