Plasma atomization might sound like something straight out of a science fiction novel, but it’s actually a revolutionary process that’s reshaping industries from aerospace to medical implants. Whether you’re a seasoned engineer, a curious student, or someone interested in the latest advancements in material science, this guide will walk you through the fascinating world of plasma atomization.
Overview of Plasma Atomization
Plasma atomization is a sophisticated process used to produce fine, spherical metal powders. These powders are essential in various industries, especially in 3D printing, where uniformity and precision are key. But what makes plasma atomization so special? How does it differ from other atomization methods, and why is it becoming the go-to choice for creating high-quality metal powders?
In simple terms, plasma atomization uses a high-energy plasma torch to melt metal wires, which are then broken into fine droplets by a high-speed gas stream. These droplets solidify into spherical particles as they cool down. The result? Powders that are not just tiny but also incredibly uniform in size and shape, making them ideal for applications that demand high precision.
Why Plasma Atomization?
Imagine trying to bake a cake with unevenly sized grains of flour. The result would be less than ideal, right? The same concept applies to metal powders used in advanced manufacturing processes. The consistency and quality of the powder can make or break the final product. Plasma atomization ensures that every grain is just right, providing a level of precision that other methods simply can’t match.
Key Advantages of Plasma Atomization
Plasma atomization isn’t just another method of creating metal powders; it’s the gold standard. Why? Let’s dive into the key advantages:
- Spherical Powder Particles: Unlike other methods that produce irregular shapes, plasma atomization creates perfectly spherical particles, which flow better and pack more densely.
- High Purity: The process operates in a controlled environment, reducing contamination and resulting in powders with exceptional purity.
- Customizable Particle Size: Whether you need ultra-fine powders or slightly larger grains, plasma atomization can be tailored to produce the desired size distribution.
- Versatility: This method is compatible with a wide range of metals, including those that are difficult to process through other means.
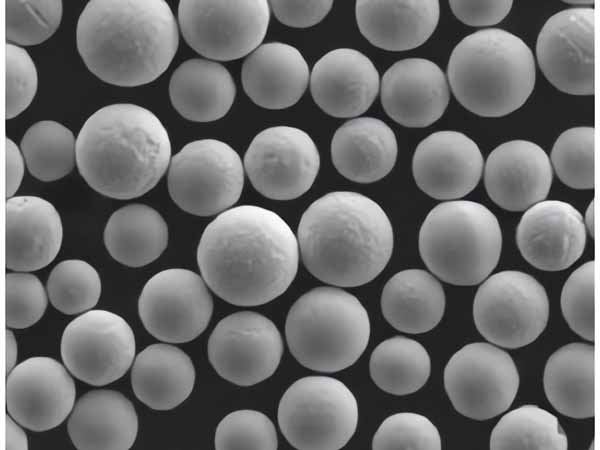
Composition and Characteristics of Plasma Atomized Powders
Understanding the composition and characteristics of plasma-atomized powders is crucial for selecting the right material for your application. Let’s explore the key attributes that make these powders stand out.
Composition of Plasma Atomized Powders
The composition of plasma-atomized powders depends on the type of metal used. Common metals include titanium, nickel, cobalt, and stainless steel. Each of these metals brings unique properties to the table, making them suitable for different applications.
Metal Type | Typical Composition | Primary Uses |
---|---|---|
Titanium (Ti) | 99.5% Ti, with small amounts of oxygen, nitrogen | Aerospace components, medical implants, high-performance coatings |
Nickel (Ni) | 99.8% Ni, trace elements | Superalloys, corrosion-resistant coatings, electronics |
Cobalt (Co) | 99.9% Co | High-temperature applications, wear-resistant coatings |
Stainless Steel (SS) | 18% Cr, 8% Ni, balance Fe | 3D printing, tooling, automotive parts |
Aluminum (Al) | 99.5% Al, small amounts of silicon, iron | Lightweight components, aerospace, automotive |
Characteristics of Plasma Atomized Powders
Plasma-atomized powders possess several unique characteristics that set them apart from powders produced by other methods.
- Particle Shape and Size Distribution: Plasma atomization produces powders with a highly uniform, spherical shape, which is critical for applications requiring high flowability and packing density.
- Purity and Contamination Levels: Due to the controlled environment of plasma atomization, the resulting powders have very low contamination levels, making them suitable for high-purity applications.
- Flowability: The spherical shape and consistent particle size distribution enhance the flowability of the powder, which is crucial in processes like additive manufacturing (3D printing).
- Density and Packing Efficiency: The uniformity in particle shape and size allows for higher packing efficiency, resulting in denser final products.
Specific Metal Powder Models: Detailed Descriptions
When it comes to plasma-atomized metal powders, not all are created equal. Each metal and alloy offers distinct advantages, and choosing the right one can significantly impact the performance of your final product. Here, we explore ten specific models of metal powders produced through plasma atomization, detailing their unique properties and best-use scenarios.
1. Ti-6Al-4V (Titanium Alloy)
Ti-6Al-4V is perhaps the most popular titanium alloy in plasma atomization, often used in the aerospace and medical industries due to its exceptional strength-to-weight ratio and biocompatibility.
- Composition: 6% Aluminum, 4% Vanadium, balance Titanium
- Key Properties: High strength, lightweight, excellent corrosion resistance
- Applications: Aircraft components, biomedical implants, high-performance sports equipment
2. Inconel 718 (Nickel-Chromium Alloy)
Inconel 718 is a superalloy known for its high strength and resistance to extreme temperatures, making it a staple in the aerospace and power generation industries.
- Composition: 50-55% Nickel, 17-21% Chromium, 4.75-5.5% Niobium, with traces of Molybdenum, Titanium, and Aluminum
- Key Properties: High-temperature strength, excellent corrosion resistance, good weldability
- Applications: Turbine blades, rocket engines, nuclear reactors
3. CoCrMo (Cobalt-Chromium-Molybdenum Alloy)
CoCrMo is a high-performance alloy widely used in medical implants and dental prosthetics due to its excellent wear resistance and biocompatibility.
- Composition: 60-65% Cobalt, 26-30% Chromium, 5-7% Molybdenum
- Key Properties: Exceptional wear resistance, biocompatibility, high corrosion resistance
- Applications: Hip and knee implants, dental prosthetics, surgical tools
4. 316L Stainless Steel
316L is a low-carbon version of 316 stainless steel, renowned for its corrosion resistance and high strength, making it ideal for marine and biomedical applications.
- Composition: 16-18% Chromium, 10-14% Nickel, 2-3% Molybdenum, balance Iron
- Key Properties: Corrosion resistance, high strength, good ductility
- Applications: Marine equipment, surgical instruments, chemical processing equipment
5. AlSi10Mg (Aluminum-Silicon-Magnesium Alloy)
AlSi10Mg is an aluminum alloy frequently used in additive manufacturing for producing lightweight components with excellent thermal properties.
- Composition: 10% Silicon, 0.25% Magnesium, balance Aluminum
- Key Properties: Lightweight, good thermal conductivity, high strength-to-weight ratio
- Applications: Automotive parts, heat exchangers, aerospace components
6. Hastelloy X (Nickel-Based Superalloy)
Hastelloy X is known for its high-temperature stability and oxidation resistance, making it suitable for extreme environments like gas turbines and petrochemical applications.
- Composition: 47-53% Nickel, 20-23% Chromium, 17-20% Iron, 8-10% Molybdenum
- Key Properties: Oxidation resistance, high-temperature strength, corrosion resistance
- Applications: Gas turbines, chemical reactors, furnace components
7. CuCrZr (Copper-Chromium-Zirconium Alloy)
CuCrZr is a copper alloy that combines high strength with excellent electrical and thermal conductivity, often used in electrical and thermal management applications.
- Composition: 0.5-1.2% Chromium, 0.03-0.3% Zirconium, balance Copper
- Key Properties: High strength, excellent thermal and electrical conductivity, good wear resistance
- Applications: Electrical connectors, heat sinks, resistance welding electrodes
8. NiTi (Nickel-Titanium Alloy)
NiTi, also known as Nitinol, is a unique alloy known for its shape memory and superelastic properties, widely used in medical devices and actuators.
- Composition: 55% Nickel, 45% Titanium
- Key Properties: Shape memory effect, superelasticity, biocompatibility
- Applications: Stents, orthodontic wires, actuators, eyeglass frames
9.17-4 PH Stainless Steel
17-4 PH is a precipitation-hardened stainless steel alloy that offers an excellent combination of high strength, hardness, and corrosion resistance.
- Composition: 15-17.5% Chromium, 3-5% Nickel, 3-5% Copper, balance Iron
- Key Properties: High strength, corrosion resistance, good toughness
- Applications: Aerospace components, nuclear reactors, injection molding tools
10. Maraging Steel (18Ni300)
Maraging steel is a high-strength, low-carbon alloy known for its excellent toughness and is commonly used in aerospace and tooling applications.
- Composition: 18% Nickel, 8-12% Cobalt, 4-5% Molybdenum, balance Iron
- Key Properties: Ultra-high strength, good toughness, ease of machining
- Applications: Aerospace components, tooling, high-performance sports equipment
Applications of Plasma Atomized Powders
Plasma atomized powders are used across a diverse range of industries due to their unique properties. From aerospace to healthcare, these powders play a crucial role in ensuring the quality and performance of various components. Here’s a closer look at where plasma atomized powders shine the brightest:
Aerospace Industry
In aerospace, every component must withstand extreme conditions. Plasma atomized powders are used to create high-performance parts that meet rigorous standards.
- Jet Engine Components: Parts such as turbine blades and nozzles benefit from the high strength and temperature resistance of plasma atomized powders like Inconel 718.
- Structural Parts: Titanium alloys, such as Ti-6Al-4V, are used in the structural components of aircraft due to their lightweight and strength properties.
Medical Industry
The medical field relies on the precision and biocompatibility of plasma atomized powders for various applications.
- Implants: Materials like CoCrMo and NiTi are used for implants and prosthetics due to their strength and biocompatibility.
- Surgical Tools: High-purity stainless steel powders are used to manufacture surgical instruments that require precision and durability.
Automotive Industry
In the automotive sector, plasma atomized powders contribute to performance and efficiency.
- Engine Components: Aluminum alloys like AlSi10Mg are used for lightweight engine parts that enhance fuel efficiency.
- Structural Parts: Stainless steel powders are used in components that need to withstand harsh conditions.
Tooling and Manufacturing
Plasma atomized powders are essential in tooling and additive manufacturing for their consistency and quality.
- 3D Printing: Uniform powder particles are critical for additive manufacturing processes, ensuring the production of high-quality parts.
- Tooling: Hardwearing powders like Maraging steel are used for making durable tooling components.
Electronics and Electrical
In electronics, the conductive properties of certain plasma atomized powders are crucial.
- Electrical Contacts: Copper-based powders are used for high-performance electrical connectors.
- Heat Sinks: Aluminum and copper powders help in manufacturing efficient heat sinks to manage thermal loads in electronic devices.
Specifications, Sizes, and Grades of Plasma Atomized Powders
When selecting plasma atomized powders, understanding the specifications, sizes, and grades is essential. Each application has specific requirements that dictate the choice of powder. Here’s a breakdown of the common specifications and standards:
Common Specifications for Plasma Atomized Powders
Specification | Description |
---|---|
Particle Size Range | Typically ranges from 5 microns to 150 microns, depending on the application and metal type. |
Particle Shape | Spherical, which enhances flowability and packing density. |
Purity Level | Generally high, with minimal contamination due to the controlled processing environment. |
Bulk Density | Depends on the powder type and size; typically ranges from 2.5 to 7.5 g/cm³. |
Flowability | Measured by the flow rate, which is crucial for powder handling and processing. |
Grades of Plasma Atomized Powders
Different grades of powders are available to meet various industrial standards and requirements. Here’s an overview of common grades:
Grade | Description | Applications |
---|---|---|
Commercial Grade | Standard grade with acceptable purity and performance. | General manufacturing and prototyping. |
High Purity Grade | Enhanced purity with very low contamination levels. | Aerospace and medical implants. |
Specialty Grade | Custom formulations for specific applications or conditions. | High-performance and extreme environments. |
Supplier and Pricing Information for Plasma Atomized Powders
Choosing the right supplier is critical for ensuring the quality and cost-effectiveness of plasma atomized powders. Here’s a look at some leading suppliers and typical pricing information.
Top Suppliers
Supplier | Specialty | Website | Contact Information |
---|---|---|---|
Ametek Specialty Metal | High-performance metal powders for aerospace and medical applications. | Ametek | [email protected] |
H.C. Starck Solutions | High-purity and specialty metal powders. | H.C. Starck | [email protected] |
EOS | Leading provider of metal powders for additive manufacturing. | EOS | [email protected] |
Carpenter Technology | Custom and standard metal powders for various industries. | Carpenter | [email protected] |
LPW Technology | Specialized in metal powders for 3D printing applications. | LPW Technology | [email protected] |
Pricing Information
The cost of plasma atomized powders can vary significantly based on factors like metal type, particle size, and quantity. Here’s a general idea of pricing:
Metal Powder | Estimated Price (per kg) | Comments |
---|---|---|
Ti-6Al-4V | $150 – $300 | Higher cost due to alloying elements. |
Inconel 718 | $200 – $350 | Premium pricing for high-performance use. |
CoCrMo | $180 – $300 | Used for critical medical applications. |
316L Stainless Steel | $50 – $100 | Relatively lower cost, widely available. |
AlSi10Mg | $80 – $120 | Cost-effective for automotive applications. |
Hastelloy X | $250 – $400 | Expensive due to high-performance features. |
CuCrZr | $120 – $200 | Good balance of cost and performance. |
NiTi | $300 – $500 | High cost due to unique properties. |
17-4 PH Stainless Steel | $70 – $150 | Popular in various high-strength applications. |
Maraging Steel | $150 – $250 | Cost is reflective of its high-strength properties. |
Pros and Cons of Plasma Atomization
When evaluating plasma atomization, it’s important to weigh its advantages against potential limitations. Here’s a breakdown:
Advantages of Plasma Atomization
Advantage | Explanation |
---|---|
High Purity | The controlled environment minimizes contamination. |
Uniform Particle Shape | Spherical particles enhance flowability and packing density. |
Versatility | Compatible with a wide range of metals and alloys. |
Customizable Sizes | Ability to tailor particle sizes to specific requirements. |
Enhanced Performance | Produces powders with consistent quality for high-performance applications. |
Limitations of Plasma Atomization
Limitation | Explanation |
---|---|
Cost | Can be more expensive compared to other atomization methods. |
Complex Equipment | Requires sophisticated and expensive plasma torch systems. |
Not Suitable for All Metals | Some metals may not be ideal for plasma atomization due to their properties. |
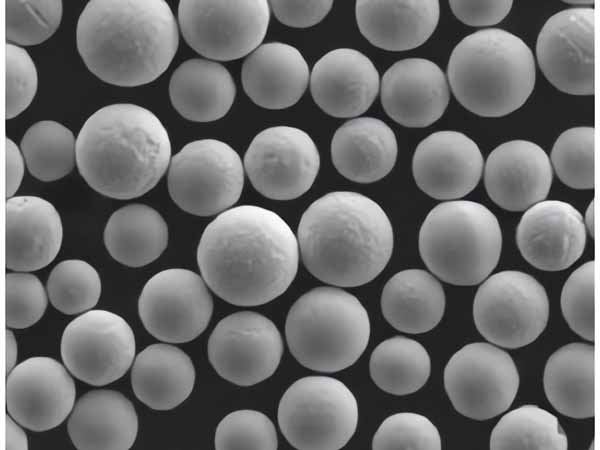
FAQ
Here’s a compilation of common questions about plasma atomization, along with their answers:
Question | Answer |
---|---|
What is plasma atomization used for? | Plasma atomization is used to produce fine, uniform metal powders for applications in aerospace, medical, automotive, and other high-precision industries. |
How does plasma atomization differ from other methods? | Plasma atomization produces spherical particles with high uniformity and purity, which is superior to other methods like gas or water atomization in terms of particle shape and size consistency. |
What metals can be atomized using plasma? | Plasma atomization can process a variety of metals including titanium, nickel, cobalt, stainless steel, aluminum, and specialty alloys like Inconel and Hastelloy. |
What are the typical particle sizes produced? | The particle sizes range from 5 microns to 150 microns, depending on the application and specific requirements. |
Is plasma atomization cost-effective? | While plasma atomization offers high quality and performance, it can be more expensive compared to other methods due to the sophisticated equipment and process control required. |
What are the main benefits of using plasma-atomized powders in 3D printing? | Plasma-atomized powders provide excellent flowability, packing density, and uniform particle size, which are crucial for producing high-quality 3D printed parts with consistent results. |
Can plasma-atomized powders be used for high-temperature applications? | Yes, many plasma-atomized powders, such as those made from Inconel or Hastelloy, are designed to withstand extreme temperatures and are ideal for high-temperature applications like aerospace and power generation. |