Metal powders are the unsung heroes behind many of the technologies we use every day, from 3D printing to high-performance alloys. But how do we get these powders in the first place? Enter the plasma gas atomizer—a cutting-edge technology that’s revolutionizing the production of metal powders. Whether you’re new to the world of metal powders or a seasoned pro, this comprehensive guide will take you on a deep dive into plasma gas atomizers, exploring their composition, characteristics, applications, and more.
Overview of Plasma Gas Atomizer Technology
The plasma gas atomizer is a state-of-the-art device used to produce ultra-fine, highly spherical metal powders. These powders are critical in industries like aerospace, automotive, and additive manufacturing, where precision and material quality are paramount. The process involves melting a metal feedstock with a plasma torch and then atomizing it into fine droplets using a high-pressure inert gas. These droplets cool and solidify in a controlled environment, resulting in a fine powder with consistent particle size and shape.
This technology offers several advantages over traditional atomization methods, including better control over particle size distribution, reduced oxidation of the metal powders, and the ability to process high-melting-point metals. Let’s explore the key aspects of this technology in detail.
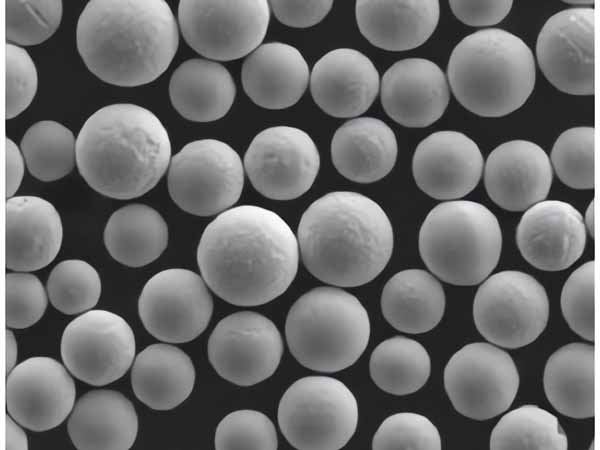
Composition of Plasma Gas Atomizers
Understanding the composition of a plasma gas atomizer is crucial for appreciating its capabilities and the quality of metal powders it produces. Here’s a breakdown of the primary components:
Component | Description | Function |
---|---|---|
Plasma Torch | A high-temperature device that generates a plasma jet using an inert gas like argon or nitrogen. | Melts the metal feedstock to create a molten stream. |
Atomization Chamber | A sealed chamber where the molten metal is atomized into fine droplets. | Provides a controlled environment for the atomization process. |
Inert Gas Supply | High-pressure argon, nitrogen, or helium gas. | Atomizes the molten metal into fine droplets and prevents oxidation. |
Metal Feedstock | Typically a metal ingot or wire, which is fed into the plasma torch. | The raw material that is melted and atomized. |
Cooling System | A system to rapidly cool the atomized droplets. | Ensures uniform solidification of the metal droplets into powder. |
Powder Collection System | A mechanism to collect the fine metal powders post-atomization. | Gathers the final product while minimizing contamination. |
Types of Metal Powders Produced by Plasma Gas Atomization
Plasma gas atomizers can produce a wide range of metal powders, each with unique properties and applications. Below, we’ve listed 10 specific metal powders, along with their descriptions and typical uses:
Metal Powder | Description | Applications |
---|---|---|
Titanium (Ti) Powder | Lightweight, high-strength powder with excellent corrosion resistance. | Aerospace, medical implants, 3D printing. |
Nickel (Ni) Powder | High melting point, excellent resistance to oxidation and corrosion. | Turbine blades, superalloys, battery electrodes. |
Cobalt-Chrome (Co-Cr) Powder | Biocompatible, wear-resistant powder with high-temperature strength. | Medical implants, dental restorations, high-temperature applications. |
Stainless Steel (316L) Powder | Corrosion-resistant, durable powder with good mechanical properties. | Additive manufacturing, automotive, medical devices. |
Aluminum (Al) Powder | Lightweight, conductive powder with good corrosion resistance. | Aerospace, automotive, electronics. |
Copper (Cu) Powder | Excellent electrical and thermal conductivity. | Electronics, conductive inks, 3D printing. |
Inconel (IN718) Powder | Nickel-chromium superalloy with high strength and oxidation resistance. | Aerospace, gas turbines, extreme environment components. |
Tool Steel (H13) Powder | High toughness, good wear resistance, and heat resistance. | Injection molds, cutting tools, die casting. |
Tantalum (Ta) Powder | Highly corrosion-resistant and biocompatible. | Medical devices, electronics, superalloys. |
Zirconium (Zr) Powder | High resistance to corrosion, especially in aggressive environments. | Nuclear reactors, chemical processing, medical implants. |
Characteristics of Plasma Gas Atomizer Metal Powders
The properties of metal powders produced via plasma gas atomization are what make them so valuable in advanced manufacturing processes. Here’s a detailed look at their characteristics:
Characteristic | Description | Impact on Applications |
---|---|---|
Particle Size Distribution | Typically ranges from 10 to 100 microns, with a narrow distribution. | Ensures uniformity in additive manufacturing and consistent material properties. |
Particle Shape | Highly spherical, with smooth surfaces. | Improves flowability and packing density in powder bed fusion processes. |
Purity | High purity, with minimal oxide contamination. | Crucial for high-performance applications in aerospace and medical fields. |
Density | High bulk and tap density due to the spherical shape. | Enhances mechanical properties in finished products. |
Flowability | Excellent due to the uniform spherical shape and consistent particle size. | Ensures consistent layering in additive manufacturing. |
Oxidation Resistance | Low oxidation levels due to the inert gas environment. | Critical for maintaining material integrity in reactive metals like titanium and aluminum. |
Applications of Plasma Gas Atomized Metal Powders
The versatility of plasma gas atomized metal powders makes them suitable for a wide array of applications. Here’s a closer look at where these powders are most commonly used:
Application | Description | Common Metal Powders Used |
---|---|---|
Additive Manufacturing (3D Printing) | Layer-by-layer construction of components using metal powders. | Titanium, Stainless Steel, Inconel, Aluminum. |
Aerospace Components | High-performance parts requiring excellent strength-to-weight ratios and resistance to extreme conditions. | Titanium, Nickel, Inconel, Cobalt-Chrome. |
Medical Implants | Biocompatible components like orthopedic implants and dental restorations. | Titanium, Cobalt-Chrome, Tantalum. |
Electronics | Conductive components and solder pastes for electronic devices. | Copper, Aluminum, Silver. |
Tooling and Molds | High-strength, wear-resistant tools and dies for manufacturing. | Tool Steel, Stainless Steel, Nickel. |
Energy Sector | Components for gas turbines, nuclear reactors, and fuel cells. | Inconel, Zirconium, Nickel, Cobalt. |
Advantages of Plasma Gas Atomization
The plasma gas atomization process offers several advantages over traditional methods like water atomization or gas atomization with non-plasma technologies. These benefits make it the preferred choice for producing high-quality metal powders:
Advantage | Description | Benefit to Users |
---|---|---|
Superior Particle Sphericity | Produces highly spherical particles with minimal satellites. | Improves flowability and packing density, leading to better end-product quality. |
Controlled Particle Size Distribution | Ability to fine-tune particle size distribution for specific applications. | Provides customization options for different manufacturing processes. |
High Purity | Minimal contamination due to the use of inert gases and controlled environments. | Ensures material integrity, especially for reactive metals like titanium. |
Versatility | Can process a wide range of metals, including high-melting-point alloys. | Expands the range of applications and materials available for advanced manufacturing. |
Reduced Oxidation | Low oxidation levels due to the use of inert gas atmospheres. | Enhances the material properties and longevity of the final product. |
Scalability | Suitable for both small-scale and large-scale production. | Flexible production options to meet varying market demands. |
Specifications and Standards for Metal Powders
When it comes to metal powders, especially those used in critical applications, adherence to specific standards and specifications is crucial. Here’s a table outlining common specifications, sizes, and grades for metal powders produced by plasma gas atomization:
Metal Powder | Common Grades | Particle Size (Microns) | Standards |
---|---|---|---|
Titanium (Ti) | Grade 1, Grade 2, Ti6Al4V | 15-45, 45-106 | ASTM B348, ASTM F2924 |
Nickel (Ni) | Ni201, Ni200 | 15-53, 45-150 | ASTM B809, AMS 5382 |
Cobalt-Chrome (Co-Cr) | CoCrMo, CoCrW | 15-45, 45-106 | ASTM F75, ISO 5832-4 |
Stainless Steel (316L) | 316L, 304L | 15-45, 45-106 | ASTM A276, ISO 5832-1 |
Aluminum (Al) | 6061, 7075 | 15-63, 45-150 | ASTM B211, AMS 4037 |
Copper (Cu) | C11000, C12000 | 10-45, 45-90 | ASTM B170, ASTM B124 |
Inconel (IN718) | IN718, IN625 | 15-53, 45-106 | ASTM B637, AMS 5662 |
Tool Steel (H13) | H13, D2 | 15-45, 45-90 | ASTM A681, ISO 4957 |
Tantalum (Ta) | TaW, Ta10W | 10-45, 45-90 | ASTM B708, ISO 13782 |
Zirconium (Zr) | Zr702, Zr705 | 15-63, 45-150 | ASTM B551, ASTM B493 |
Suppliers and Pricing Details
Knowing where to source high-quality metal powders and understanding the pricing can make or break a manufacturing project. Here’s a table featuring prominent suppliers and approximate pricing details for plasma gas atomized metal powders:
Supplier | Metal Powders Offered | Pricing (USD/Kg) | Contact Information |
---|---|---|---|
AP&C (GE Additive) | Titanium, Stainless Steel, Aluminum | $100 – $500 | www.ge.com/additive/apc |
LPW Technology (Carpenter Technology) | Nickel, Inconel, Cobalt-Chrome | $150 – $700 | www.lpwtechnology.com |
Höganäs AB | Tool Steel, Stainless Steel, Copper | $50 – $300 | www.hoganas.com |
Praxair Surface Technologies | Titanium, Nickel, Inconel | $120 – $600 | www.praxairsurfacetechnologies.com |
TLS Technik | Stainless Steel, Aluminum, Titanium | $80 – $400 | www.tls-technik.com |
Aubert & Duval | Inconel, Tool Steel, Cobalt-Chrome | $150 – $750 | www.aubertduval.com |
Sandvik Osprey | Titanium, Stainless Steel, Nickel | $100 – $550 | www.metalpowder.sandvik |
Tekna Plasma Systems | Aluminum, Titanium, Zirconium | $90 – $450 | www.tekna.com |
GKN Hoeganaes | Stainless Steel, Tool Steel, Aluminum | $70 – $350 | www.gknpm.com |
Arcam AB (a GE Additive company) | Titanium, Inconel, Cobalt-Chrome | $130 – $650 | www.arcam.com |
Comparing Plasma Gas Atomization with Other Atomization Techniques
To truly understand the advantages of plasma gas atomization, it’s essential to compare it with other atomization methods. Here’s how it stacks up against the competition:
Atomization Technique | Plasma Gas Atomization | Gas Atomization | Water Atomization |
---|---|---|---|
Particle Shape | Highly spherical | Mostly spherical, with some irregularities | Irregular, angular |
Oxidation Levels | Low (due to inert gas) | Moderate | High (due to water exposure) |
Particle Size Distribution | Narrow and controllable | Broader distribution | Broader distribution |
Material Purity | High | Moderate to high | Lower (due to water contamination) |
Metal Types | Wide range, including high-melting-point metals | Wide range | Limited (not suitable for reactive metals) |
Cost | Higher (due to complex setup) | Moderate | Lower (due to simpler setup) |
Applications | High-performance, critical applications | General manufacturing, less critical applications | Lower-cost applications, non-critical parts |
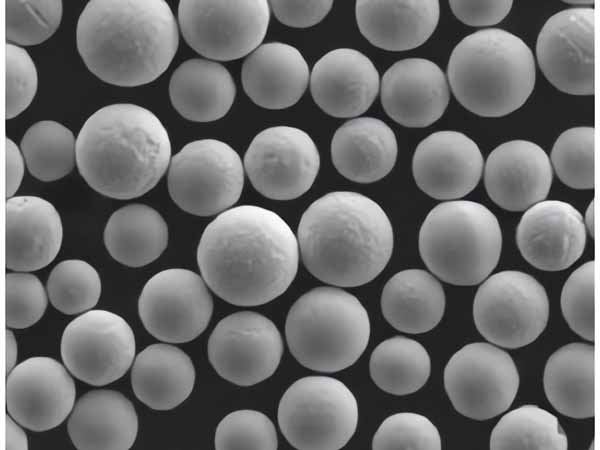
FAQs
Q: What is a plasma gas atomizer?
A: A plasma gas atomizer is a device used to produce fine, spherical metal powders by melting a metal feedstock with a plasma torch and then atomizing it using a high-pressure inert gas.
Q: What are the advantages of using plasma gas atomized powders?
A: The main advantages include superior particle sphericity, controlled particle size distribution, high purity, and reduced oxidation levels, making these powders ideal for high-performance applications.
Q: Which metals can be processed using plasma gas atomization?
A: A wide range of metals can be processed, including titanium, nickel, cobalt-chrome, stainless steel, aluminum, copper, Inconel, tool steel, tantalum, and zirconium.
Q: How does plasma gas atomization compare to other atomization methods?
A: Plasma gas atomization produces more spherical particles with lower oxidation levels and higher purity, but it is generally more expensive than gas or water atomization.
Q: What industries use plasma gas atomized metal powders?
A: These powders are used in aerospace, medical, automotive, electronics, energy, and additive manufacturing industries.
Q: Where can I purchase plasma gas atomized metal powders?
A: Many suppliers offer these powders, including AP&C, LPW Technology, Höganäs AB, and Praxair Surface Technologies.
Q: What are the typical particle sizes for plasma gas atomized powders?
A: Particle sizes typically range from 10 to 150 microns, depending on the specific application and metal type.
Q: Are plasma gas atomized powders expensive?
A: The cost varies depending on the metal and supplier, with prices typically ranging from $50 to $750 per kilogram.
Q: Can plasma gas atomized powders be used in 3D printing?
A: Yes, these powders are highly suitable for additive manufacturing due to their consistent quality, flowability, and material properties.
Q: What is the typical purity level of plasma gas atomized powders?
A: These powders typically have high purity levels, with minimal oxide contamination, making them suitable for critical applications.
Conclusion
The plasma gas atomizer is a game-changer in the world of metal powder production. Its ability to produce ultra-fine, highly spherical metal powders with consistent quality makes it indispensable for industries like aerospace, medical, and additive manufacturing. Whether you’re looking to source high-quality powders or just want to understand the technology better, this guide provides all the information you need.
Plasma gas atomization may come at a higher cost, but its benefits far outweigh the investment, especially for critical applications where material quality cannot be compromised. As industries continue to push the boundaries of what’s possible with advanced manufacturing techniques, plasma gas atomization will undoubtedly play a central role in shaping the future of materials science.