When it comes to the world of advanced manufacturing, especially in the creation of metal powders, the Plasma-Rotating Electrode Process (PREP) stands out. This fascinating technique offers unparalleled precision and quality. But what exactly is PREP, and why is it so significant? Let’s dive deep into this topic, exploring its intricacies, applications, advantages, and much more.
Overview of the Plasma-Rotating Electrode Process
The Plasma-Rotating Electrode Process is a method used to produce high-quality, spherical metal powders. It involves melting the tip of a rotating metal bar using a plasma torch, causing droplets to form and solidify into fine, uniform powder particles as they cool down. This technique is especially prized for its ability to produce powders with excellent flowability and high purity, essential for various industrial applications.
Key Features and Benefits of Plasma-Rotating Electrode Process
- High Purity: The process minimizes contamination, producing extremely pure metal powders.
- Spherical Particles: Resulting powders are spherical, enhancing flowability and packing density.
- Wide Range of Metals: Capable of processing a variety of metals and alloys.
- Consistent Quality: Produces uniform particles with consistent size distribution.
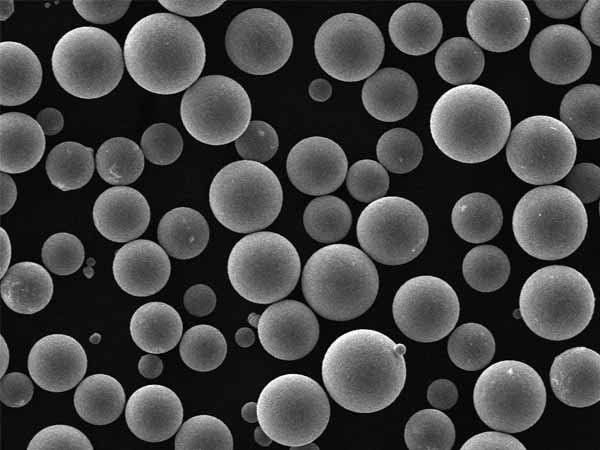
Types of Metal Powders Produced by Plasma-Rotating Electrode Process
Here, we explore specific metal powders created using PREP, detailing their composition, properties, and uses.
Metal Powder | Composition | Properties | Applications |
---|---|---|---|
Titanium (Ti) | Pure Titanium | High strength, low density, corrosion-resistant | Aerospace, medical implants |
Stainless Steel 316L | Fe-Cr-Ni-Mo | High corrosion resistance, good mechanical properties | Biomedical devices, marine environments |
Nickel-based Superalloys | Ni-Cr-Co-Mo | High temperature and corrosion resistance | Turbine blades, jet engines |
Aluminum (Al) | Pure Aluminum | Lightweight, good electrical conductivity | Automotive, electronics |
Cobalt-Chrome (CoCr) | Co-Cr-Mo | High wear resistance, biocompatibility | Dental implants, orthopedic implants |
Inconel 718 | Ni-Cr-Fe | Excellent mechanical properties at high temperatures | Aerospace, gas turbines |
Copper (Cu) | Pure Copper | High thermal and electrical conductivity | Electronics, heat exchangers |
Titanium-Aluminum-Vanadium (Ti-6Al-4V) | Ti-6%Al-4%V | High strength-to-weight ratio, corrosion-resistant | Aerospace, medical implants |
Tantalum (Ta) | Pure Tantalum | High melting point, corrosion-resistant | Medical devices, electronics |
Tungsten (W) | Pure Tungsten | High density, high melting point | Radiation shielding, electrical contacts |
Applications of Plasma-Rotating Electrode Process
The versatility of the Plasma-Rotating Electrode Process is reflected in its wide range of applications. Here’s a detailed look at where these high-quality metal powders are used:
Application | Details |
---|---|
Aerospace | Used in the manufacturing of high-strength, lightweight components for aircraft and spacecraft. |
Medical Implants | Provides biocompatible materials for orthopedic and dental implants. |
Electronics | Essential for producing components with high thermal and electrical conductivity. |
Automotive | Utilized in creating lightweight, durable parts for better fuel efficiency and performance. |
Energy | Applied in making parts for gas turbines and other high-temperature environments. |
Additive Manufacturing | Crucial for 3D printing of complex, high-precision parts. |
Marine | Suitable for parts exposed to harsh marine environments due to high corrosion resistance. |
Specifications, Sizes, Grades, and Standards of Metal Powders
Understanding the specifications, sizes, grades, and standards of metal powders is crucial for their application in different industries.
Metal Powder | Specifications | Sizes | Grades | Standards |
---|---|---|---|---|
Titanium (Ti) | ASTM B348 | 15-150 µm | Grade 1, 2, 5 | ASTM F67, F136 |
Stainless Steel 316L | ASTM A276 | 20-100 µm | 316L | ASTM F138 |
Nickel-based Superalloys | AMS 5662 | 10-75 µm | Inconel 718 | AMS 5663 |
Aluminum (Al) | ASTM B221 | 15-120 µm | 6061, 7075 | ASTM F3318 |
Cobalt-Chrome (CoCr) | ASTM F75 | 20-100 µm | F75, F799 | ASTM F1537 |
Inconel 718 | ASTM B637 | 10-80 µm | Inconel 718 | AMS 5662 |
Copper (Cu) | ASTM B124 | 15-150 µm | C11000 | ASTM F68 |
Titanium-Aluminum-Vanadium (Ti-6Al-4V) | ASTM B348 | 20-100 µm | Grade 5 | ASTM F1472 |
Tantalum (Ta) | ASTM B708 | 20-80 µm | TaW | ASTM F560 |
Tungsten (W) | ASTM B760 | 10-75 µm | W1, W2 | ASTM F288 |
Suppliers and Pricing Details for Metal Powders
Knowing where to source these metal powders and understanding their pricing can significantly impact your manufacturing decisions.
Supplier | Metal Powder | Price (per kg) | Details |
---|---|---|---|
AP&C | Titanium (Ti) | $250 – $400 | High-quality spherical powders |
Carpenter Technology | Stainless Steel 316L | $50 – $100 | Various grades available |
Höganäs AB | Nickel-based Superalloys | $200 – $350 | Premium superalloys |
Valimet | Aluminum (Al) | $30 – $60 | High purity powders |
Sandvik | Cobalt-Chrome (CoCr) | $300 – $500 | Medical-grade powders |
ATI Metals | Inconel 718 | $200 – $400 | Aerospace grade |
GKN Hoeganaes | Copper (Cu) | $20 – $50 | High conductivity powders |
Praxair | Titanium-Aluminum-Vanadium (Ti-6Al-4V) | $250 – $400 | Aerospace and medical applications |
H.C. Starck | Tantalum (Ta) | $500 – $700 | Ultra-high purity |
Plansee | Tungsten (W) | $100 – $200 | High-density applications |
Advantages and Limitations of Plasma-Rotating Electrode Process
Every manufacturing process has its strengths and weaknesses. Let’s compare the advantages and limitations of PREP to give you a balanced perspective.
Aspect | Advantages | Limitations |
---|---|---|
Purity | High purity due to reduced contamination | High energy consumption |
Particle Shape | Spherical particles improve flowability | Initial setup cost is high |
Consistency | Uniform particle size distribution | Limited to specific metals |
Versatility | Can process various metals and alloys | Requires skilled operation |
Efficiency | Efficient for high-quality powder production | May not be suitable for large-scale production |
Technical Parameters and Process Control in Plasma-Rotating Electrode Process
The effectiveness of the Plasma-Rotating Electrode Process hinges on precise control of several technical parameters.
Parameter | Description | Optimal Range |
---|---|---|
Rotation Speed | Speed of the rotating electrode | 10,000 – 30,000 RPM |
Plasma Power | Power of the plasma torch | 50 – 150 kW |
Gas Flow Rate | Rate of inert gas flow | 10 – 50 L/min |
Electrode Material | Type of metal used as electrode | Various metals/alloys |
Particle Size Control | Mechanisms to control particle size | Adjustable by process parameters |
Cooling Rate | Rate at which droplets cool and solidify | High cooling rates preferred |
Comparing Plasma-Rotating Electrode Process with Other Powder Production Methods
To better appreciate the Plasma-Rotating Electrode Process, it’s helpful to compare it against other common powder production methods.
Process | PREP | Gas Atomization | Water Atomization | Mechanical Alloying |
---|---|---|---|---|
Purity | High | Medium to High | Medium | Variable |
Particle Shape | Spherical | Spherical/irregular | Irregular | Irregular |
Size Control | Excellent | Good | Fair | Fair |
Cost | High | Medium | Low | Medium |
Production Rate | Medium | High | High | Low |
Material Range | Broad | Broad | Limited | Broad |
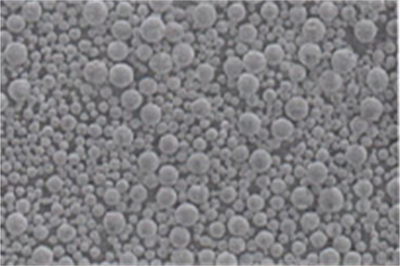
FAQ
1. What is the Plasma-Rotating Electrode Process (PREP)?
PREP is a method for producing high-quality metal powders, particularly for use in additive manufacturing and powder metallurgy. The process involves melting the end of a rotating electrode using a plasma torch, which leads to the formation of droplets that solidify into fine spherical particles.
2. What are the key components of the PREP system?
- Rotating Electrode: The metal rod or bar that acts as the feedstock.
- Plasma Torch: Provides the heat necessary to melt the electrode.
- Chamber: An enclosed environment where the melting and solidification occur, often under an inert atmosphere.
- Collection System: Where the solidified metal powder is collected.
3. How does the PREP process work?
- The metal electrode rotates at high speed.
- A plasma torch melts the tip of the electrode.
- Centrifugal force causes the molten metal to eject from the electrode surface.
- The ejected droplets solidify into spherical particles as they travel away from the electrode.
- These particles are collected as metal powder.
4. What types of materials can be processed using PREP?
PREP is suitable for a wide range of materials, including:
- Titanium and its alloys
- Nickel-based superalloys
- Stainless steels
- Cobalt-chromium alloys
- Aluminum alloys
5. What are the advantages of the PREP method?
- High Purity: Minimal contamination due to the inert atmosphere.
- Spherical Particles: Produces powders with excellent flowability and packing density.
- Control over Particle Size: Adjustments in process parameters can tailor the size distribution.
- Minimal Waste: Efficient use of material, with little to no waste.
6. What are the applications of PREP-produced powders?
- Additive Manufacturing: 3D printing of metal parts.
- Powder Metallurgy: Making parts by compacting and sintering metal powders.
- Thermal Spraying: Coating surfaces with metal powders.
- Metal Injection Molding (MIM): Producing complex shapes with high precision.