In the rapidly evolving world of additive manufacturing, PREP-prepared powders have emerged as a key player, offering unparalleled quality and consistency for industrial applications. Whether you are an engineer, researcher, or simply curious about the latest advancements in metal powders, this comprehensive guide will walk you through everything you need to know about PREP-prepared powders.
Overview of PREP-Prepared Powders
PREP, which stands for Plasma Rotating Electrode Process, is a method used to produce spherical metal powders with high purity, excellent flowability, and superior density. These powders are crucial for various applications, particularly in additive manufacturing, where they ensure the precision and quality of the final products.
PREP-prepared powders are distinct because of their unique manufacturing process. In the PREP method, a rotating electrode (made of the metal being processed) is subjected to a plasma arc, which melts the metal. The centrifugal force generated by the rotating electrode causes the molten metal to disperse and solidify into fine, spherical particles. These particles, or powders, exhibit characteristics that make them ideal for advanced manufacturing techniques, such as 3D printing.
Why PREP-Prepared Powders?
The growing demand for high-performance metal parts in industries like aerospace, automotive, and biomedical engineering has fueled the need for powders that can meet stringent quality requirements. PREP-prepared powders stand out because they offer:
- High sphericity: This ensures better flowability, crucial for additive manufacturing.
- Low oxygen content: Reduced oxidation enhances the quality of the final product.
- Uniform particle size distribution: This leads to consistent layering and better surface finish in printed parts.
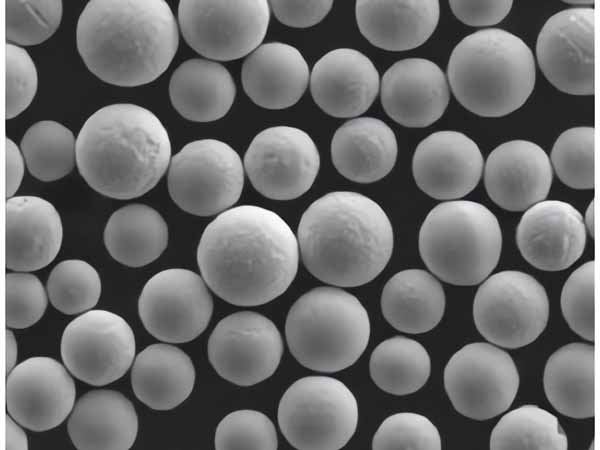
Types and Composition of PREP-Prepared Powders
PREP-prepared powders come in various compositions, each tailored to specific industrial applications. Below is a detailed table highlighting some of the most common types of PREP-prepared powders, their compositions, and key characteristics.
Powder Type | Composition | Key Characteristics | Typical Applications |
---|---|---|---|
Ti-6Al-4V | Titanium, Aluminum, Vanadium | High strength, corrosion resistance, biocompatibility | Aerospace, Medical implants |
316L Stainless Steel | Iron, Chromium, Nickel, Molybdenum | Excellent corrosion resistance, good mechanical properties | Medical devices, Food processing equipment |
Inconel 718 | Nickel, Chromium, Iron, Niobium | High temperature resistance, oxidation resistance | Turbine blades, Jet engines |
AlSi10Mg | Aluminum, Silicon, Magnesium | Lightweight, good strength-to-weight ratio | Automotive parts, Aerospace components |
CoCrMo | Cobalt, Chromium, Molybdenum | Wear resistance, biocompatibility | Dental implants, Joint replacements |
Hastelloy X | Nickel, Chromium, Molybdenum, Iron | High temperature strength, oxidation resistance | Gas turbines, Chemical processing |
CuCr1Zr | Copper, Chromium, Zirconium | High conductivity, wear resistance | Electrical components, Heat exchangers |
Maraging Steel | Iron, Nickel, Molybdenum, Cobalt | High strength, toughness, good weldability | Tooling, Aerospace, Military applications |
NiTi (Nitinol) | Nickel, Titanium | Shape memory effect, superelasticity | Medical devices, Actuators |
Al7075 | Aluminum, Zinc, Magnesium, Copper | High strength, lightweight | Aircraft structures, High-stress components |
Characteristics of PREP-Prepared Powders
Understanding the characteristics of PREP-prepared powders is essential to appreciating their advantages and applications in modern manufacturing. Let’s delve into some of the critical characteristics that set these powders apart.
1. High Sphericity
The plasma rotating electrode process produces powders with near-perfect sphericity. This is crucial in additive manufacturing, particularly in processes like Selective Laser Melting (SLM) and Electron Beam Melting (EBM), where powder flowability and packing density significantly affect the final product’s quality.
2. Uniform Particle Size Distribution
PREP-prepared powders typically exhibit a narrow particle size distribution. This uniformity ensures consistent layering during 3D printing, resulting in parts with smooth surfaces and fine details.
3. Low Oxygen Content
Oxygen contamination in metal powders can lead to oxidation, which degrades the mechanical properties of the final product. The PREP method minimizes oxygen content, enhancing the purity and performance of the powders.
4. High Purity
The absence of contamination is a hallmark of PREP-prepared powders. This high purity is particularly important in industries like aerospace and medical, where material integrity is paramount.
Advantages of PREP-Prepared Powders
So, why choose PREP-prepared powders over other types of metal powders? Here’s a detailed comparison highlighting the advantages:
Feature | PREP-Prepared Powders | Gas Atomized Powders | Water Atomized Powders |
---|---|---|---|
Sphericity | High | Medium | Low |
Flowability | Excellent | Good | Poor |
Purity | High | Medium | Low |
Particle Size Distribution | Narrow | Wider | Wide |
Oxygen Content | Low | Medium | High |
Cost | Higher | Medium | Lower |
1. Superior Flowability
Thanks to their high sphericity, PREP-prepared powders flow more easily, which is crucial for processes like 3D printing and cold spraying, where consistent powder delivery is essential.
2. Enhanced Mechanical Properties
The low oxygen content and high purity of PREP-prepared powders result in superior mechanical properties, such as tensile strength and fatigue resistance, in the final products.
3. Better Surface Finish
The uniform particle size distribution of PREP-prepared powders leads to smoother surface finishes, reducing the need for post-processing and improving the overall aesthetic and functional quality of the parts.
-
CM247LC Powder | Nickel Alloy Powder
-
0# Pure Nickel powder
-
NiCoCrAlY alloys powders
-
Rene 142 alloy-Rene Powder
-
Haynes 25 Haynes Powder
-
Best Hastelloy C-22 Powder-High temperature alloy Powder for 3D Printing
-
Best Hastelloy C-276 Powder-High temperature alloy Powder for 3D Printing
-
Best Hastelloy N Powder-High temperature alloy Powder for 3D Printing
-
Best Hastelloy B Powder丨High temperature alloy Powder for 3D Printing
Applications of PREP-Prepared Powders
PREP-prepared powders are used across a wide range of industries, thanks to their unique properties. Here’s a breakdown of some of the most common applications:
Industry | Applications | Powder Types Commonly Used |
---|---|---|
Aerospace | Turbine blades, structural components, engine parts | Ti-6Al-4V, Inconel 718 |
Medical | Implants, surgical instruments, dental devices | Ti-6Al-4V, CoCrMo |
Automotive | Lightweight components, high-performance parts | AlSi10Mg, Al7075 |
Energy | Turbine components, heat exchangers, fuel cells | Hastelloy X, Inconel 718 |
Electronics | Heat sinks, conductive components | CuCr1Zr, AlSi10Mg |
Defense | High-strength components, lightweight armor | Maraging Steel, Al7075 |
Tooling | Molds, dies, and fixtures for high-performance applications | Maraging Steel, Inconel 718 |
Specifications, Sizes, Grades, and Standards
When selecting PREP-prepared powders for specific applications, it’s crucial to consider various specifications, including particle size, purity, and applicable industry standards. The table below provides a detailed look at the specifications of some commonly used PREP-prepared powders:
Powder Type | Particle Size (µm) | Purity (%) | Standards | Grades Available |
---|---|---|---|---|
Ti-6Al-4V | 15-45 | 99.5 | ASTM F2924, AMS 4998 | Grade 23 (ELI), Grade 5 |
316L Stainless Steel | 10-53 | 99.9 | ASTM A240, ISO 5832-1 | 316L |
Inconel 718 | 15-45 | 99.0 | AMS 5662, AMS 5596 | NA |
AlSi10Mg | 20-63 | 99.5 | ISO 3522 | NA |
CoCrMo | 10-45 | 99.8 | ASTM F75, ISO 5832-4 | CoCrMo ASTM F75 |
Hastelloy X | 15-53 | 99.0 | AMS 5754 | NA |
CuCr1Zr | 20-63 | 99.9 | EN 12163, ASTM B379 | CuCr1Zr |
Maraging Steel | 10-45 | 99.5 | AMS 6514 | 18Ni (300), 18Ni (250) |
NiTi (Nitinol) | 15-45 | 99.5 | ASTM F2063 | NA |
Al7075 | 20-63 | 99.5 | ASTM B211 | NA |
Comparing Advantages and Limitations
Understanding the strengths and weaknesses of PREP-prepared powders compared to other powder production methods is key to making informed decisions. Below is a comparison table that highlights the advantages and limitations:
Comparison Factor | PREP-Prepared Powders | Gas Atomized Powders | Water Atomized Powders |
---|---|---|---|
Sphericity | Excellent | Good | Poor |
Flowability | Superior | Adequate | Limited |
Purity | High | Moderate | Low |
Cost | Higher | Medium | Lower |
Particle Size Control | Excellent | Good | Variable |
Applications in High-Tech Sectors | Widely used | Common | Limited |
Availability of Exotic Alloys | Wide range | Moderate | Limited |
Suppliers and Pricing Details
When sourcing PREP-prepared powders, it’s essential to consider not only the quality but also the cost and supplier reliability. Below is a table listing some of the top suppliers of PREP-prepared powders, along with pricing details.
Supplier | Powder Types Offered | Price Range (USD/kg) | Minimum Order Quantity | Lead Time |
---|---|---|---|---|
Carpenter Additive | Ti-6Al-4V, 316L, Inconel 718 | $250 – $500 | 5 kg | 2-4 weeks |
Praxair Surface Technologies | Ti-6Al-4V, CoCrMo, Hastelloy X | $300 – $600 | 10 kg | 3-5 weeks |
AP&C (GE Additive) | Ti-6Al-4V, AlSi10Mg, Inconel 718 | $200 – $450 | 5 kg | 4-6 weeks |
Sandvik Osprey | Maraging Steel, NiTi, CuCr1Zr | $350 – $700 | 5 kg | 3-4 weeks |
Höganäs AB | 316L, Al7075, Inconel 718 | $220 – $480 | 10 kg | 4-6 weeks |
Tekna | AlSi10Mg, Ti-6Al-4V, CoCrMo | $250 – $500 | 5 kg | 2-4 weeks |
LPW Technology | Ti-6Al-4V, Inconel 718, AlSi10Mg | $200 – $500 | 5 kg | 3-5 weeks |
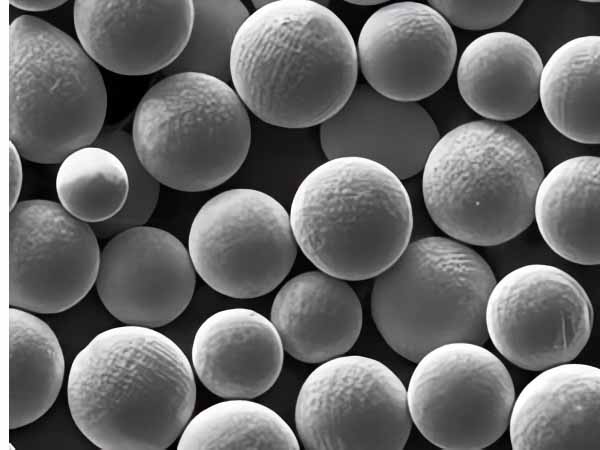
FAQs
Understanding PREP-prepared powders can be complex, so here are some frequently asked questions to help clarify key points:
Question | Answer |
---|---|
What makes PREP-prepared powders different from other metal powders? | PREP-prepared powders are distinguished by their high sphericity, low oxygen content, and uniform particle size distribution, making them ideal for additive manufacturing. |
Why are PREP-prepared powders more expensive? | The higher cost is due to the advanced production process that ensures superior quality, purity, and performance. |
Can PREP-prepared powders be used in all 3D printing technologies? | Yes, they are suitable for a range of technologies, including SLM, EBM, and Direct Metal Laser Sintering (DMLS). |
How do I choose the right PREP-prepared powder for my application? | Consider factors like the required material properties, application environment, and the specific additive manufacturing technology being used. |
Are there any limitations to using PREP-prepared powders? | While they offer many advantages, they are more expensive and may not be necessary for applications where lower-cost powders suffice. |