Aluminum 2024 powder is an extremely versatile aluminum alloy powder used in various powder metallurgy applications. This guide provides a detailed overview of Al 2024 powder covering its properties, production methods, applications, suppliers, costs, and more.
Overview of Al 2024 Powder
Al 2024 is a wrought alloy that contains copper as the major alloying element. It is known for its high strength, good machinability and ductility compared to other 2xxx series aluminum alloys.
Some key properties and characteristics of Al 2024 powder include:
Properties of Al 2024 Powder
Properties | Details |
---|---|
Composition | Aluminum (90.7-94.7%), Copper (3.8-4.9%), Magnesium (1.2-1.8%), Manganese (0.3-0.9%) |
Density | 2.79 g/cm3 |
Melting Point | 507°C |
Color | Silver-grey metallic |
Particle Shape | Spherical, irregular |
Typical Size | 15-45 microns |
Flowability | Good |
Compressibility | Good |
Some of the major advantages of using Al 2024 powder include:
- High strength and hardness – Al 2024 powder enables production of high strength parts due to precipitation hardening by copper and magnesium. Density and mechanical properties of sintered parts can reach up to 98% of fully dense Al 2024.
- Corrosion resistance – Forms protective oxide layer providing good corrosion resistance especially in marine environments. Provides better corrosion protection than 2xxx series alloys with higher copper content.
- Good dimensional stability – Controlled oxide formation gives excellent dimensional control.
- Weldable and machinable – Can be welded and machined using conventional methods. Powder metallurgy Al 2024 parts can be heat treated to T3, T4 and T6 tempers.
- Cost effectiveness – Al 2024 powder can be mass produced via atomisation processes in a cost effective manner. The near net shaping capability minimises wastage.
Some limitations of Al 2024 powder include:
- Lower strength than steels and titanium alloys – Al 2024 has moderate strength compared to other competing high performance alloys. Strength levels are also lower compared to Al alloys with higher Cu content.
- Susceptibility to stress corrosion cracking – Al 2024 is susceptible to SCC in certain environments limiting usage for some critical structural parts.
- Difficulty in achieving complex geometries – Limitations in achievable part geometries and feature details compared to cast and wrought Al products.
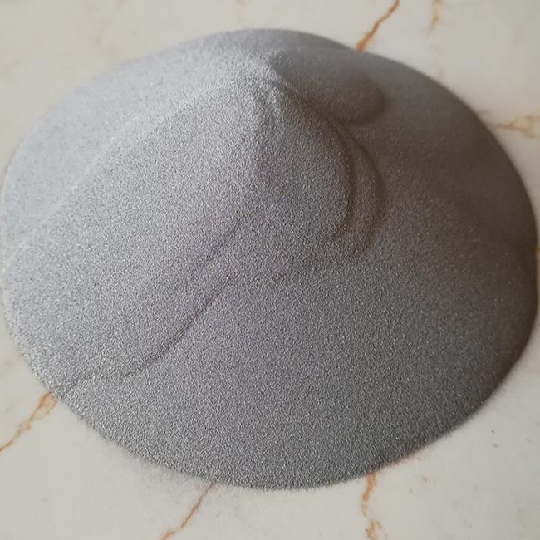
Production Methods for Al 2024 Powder
Al 2024 powder can be produced via various methods including:
Production Methods for Al 2024 Powder
Method | Typical Size | Cost | Advantages | Limitations |
---|---|---|---|---|
Gas Atomisation | 15-150 μm | Low | High purity, spherical morphology, controlled particle size distribution | Limited to small batches |
Water Atomisation | 20-400 μm | Low | Economic production of medium to large batches | Irregular morphology, wider particle distribution |
Mechanical Milling | 1-100 μm | Medium | Small batches with controlled particle sizes | Contamination issues, irregular shape |
Plasma Rotating Electrode Process (PREP) | 45-150 μm | High | Controlled microstructure and morphology | Small batches, expensive |
The particle shape and size distribution influences the flowability, packing density and sintering response. Gas atomised and PREP powders with spherical morphology provide excellent flowability and packing density.
Water atomised powder is widely used for commercial Al 2024 powder production owing to its cost-effectiveness and capability for large volume production. The typical size range for water atomised Al 2024 powder is 20-400 μm.
Mechanical milling provides the ability to produce small batches of powder with precise control of particle sizes. However, the powder can get contaminated from milling media requiring careful process control.
Applications of Al 2024 Powder
Some of the major applications of Al 2024 powder include:
Applications of Al 2024 Powder
Application | Benefits | Examples |
---|---|---|
Aerospace Components | High strength, corrosion resistance | Aircraft fittings, helicopter transmission housings |
Automotive Parts | Strength, weldability, machinability | Powertrain parts like connecting rods, pistons, gears |
Industrial Components | Good dimensional stability, machinability | Hydraulic manifolds, valves, tooling jigs and fixtures |
Consumer Products | Corrosion resistance, attractive finish | Luggage parts, sporting goods, marine hardware |
Al 2024’s excellent strength, corrosion resistance and dimensional stability make it suitable for structural parts across aviation, automotive and industrial sectors.
The good machinability and weldability of Al 2024 powder parts allows additional fabrication for enhanced complexity. The material is ideal for producing lightweight, high performance metal components via powder metallurgy technique.
Specifications for Al 2024 Powder
Al 2024 powder is widely available in compositions conforming to established specifications:
Specifications for Al 2024 Powder
Specification | Cu | Mg | Mn | Fe | Si | Zn | Ti | Other |
---|---|---|---|---|---|---|---|---|
AA2024 | 3.8-4.9% | 1.2-1.8% | 0.3-0.9% | 0.5% max | 0.5% max | 0.25% max | 0.15% max | 0.05% each; 0.15% total max |
AMS 4127 | 3.8-4.9% | 1.2-1.8% | 0.3-0.9% | 0.5% max | 0.5% max | 0.25% max | 0.15% max | – |
UNS A92024 | – | – | – | – | – | – | – | – |
Other standardized mechanical and physical properties for Al 2024 powder include:
- Density – 2.79 g/cm3
- Melting Point – 507°C
- Thermal Conductivity – 121 W/m-K
- Electrical Resistivity – 0.041 ohms-cm
- Modulus of Elasticity – 73 GPa
- Poisson’s Ratio – 0.33
- Elongation at Break – 20%
Maintaining the chemical composition within specified ranges is crucial for achieving target material performance. Rigorous quality control is implemented by suppliers during manufacturing.
Al 2024 Powder Size Distribution
The particle size distribution (PSD) influences compaction and sintering response:
Typical Size Distribution of Al 2024 Powder
Mesh | Micrometers | Distribution |
---|---|---|
+100 | +149 | 0-10% |
-100/+170 | 105-149 | 25-45% |
-170/+325 | 44-105 | 35-55% |
-325 | -44 | 0-10% |
- Size range generally between 10-170 microns
- Median particle size typically in 60-110 micron range
- Narrow distribution provides optimal packing density
- Well controlled PSD ensures repeatable compaction and sintering
- Gas atomised powder has narrowest distribution of 15-45 microns
Controlling particle size distribution within an optimal range ensures dense and uniform compaction when consolidated into a green part. It allows predictable sintering response for achieving consistent properties.
Al 2024 Powder Apparent Density
Apparent density gives a measure of how densely the powder packs:
Typical Apparent Density of Al 2024 Powder
Production Method | Apparent Density |
---|---|
Gas Atomised | 2.2-2.6 g/cc |
Water Atomised | 1.6-2.2 g/cc |
- Higher apparent density improves green density after compaction
- Gas atomised powder provides maximized density due to spherical particles
- Apparent density can be increased through techniques like annealing
- Dense packing of powder particles reduces porosity in sintered parts
Powder with high apparent density leads to higher green density and lower shrinkage after sintering. Gas atomised Al 2024 powder provides the highest apparent density.
Al 2024 Powder Flow Rate
Flow rate determines how easily the powder flows during loading and compaction:
Typical Flow Rates for Al 2024 Powder
Production Method | Flow Rate | Flow Character |
---|---|---|
Gas Atomised | 25-35 s/50g | Excellent |
Water Atomised | 35-45 s/50g | Moderate |
- Flow rate measured in sec/50g using Hall flowmeter
- Lower flow time indicates excellent flowability
- Gas atomised powder exhibits superior flow vs water atomised
- Smooth spherical morphology improves flow characteristics
- Good flow is essential for uniform die filling during compaction
Gas atomised Al 2024 powder possesses excellent flowability suitable for automated production processes. Irregular shaped water atomised powder has moderate flow rates.
Suppliers of Al 2024 Powder
Some leading global suppliers of Al 2024 powder include:
Suppliers of Al 2024 Powder
Company | Location |
---|---|
H.C. Starck Solutions | Germany, US |
Pometon SpA | Italy |
Makin Metal Powders | UK |
Valimet Inc | US |
SLM Solutions | Germany |
Sandvik Osprey | UK |
These companies can manufacture Al 2024 to various specifications tailored to customer requirements. Typical lead times range from 2-8 weeks for bulk orders depending on quantity.
Small trial batches may be supplied from inventory on shorter lead times by some distributors. High purity grades for special applications are also available from certain suppliers.
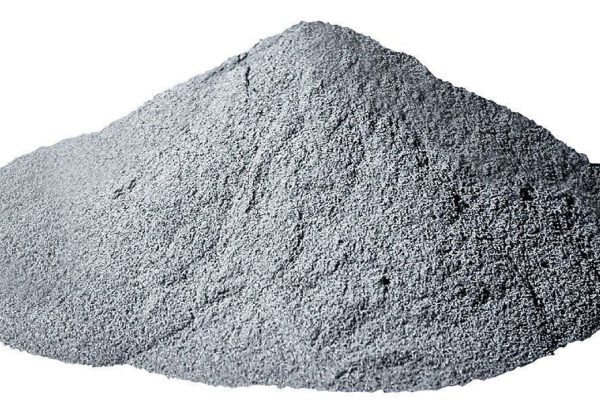
Cost of Al 2024 Powder
The average cost range for Al 2024 powder based on particle size:
Cost Range of Al 2024 Powder
Particle Size | Cost per kg |
---|---|
15-53 μm | $55-65 |
53-105 μm | $45-55 |
105-250 μm | $35-45 |
- Fine gas atomised powder is higher cost
- Water atomised powder is lower cost
- Costs vary with quantity, source, purity level
- Packaging adds cost – e.g. sealed bags in drums
- Lead time also depends on quantity ordered
Gas atomised Al 2024 powder with fine particle size distribution commands a premium price over coarse water atomised powder. Costs decrease significantly with order quantity due to economy of scale.
Installing Al 2024 Powder Systems
Key considerations for installing Al 2024 powder handling systems:
Installation Guide for Al 2024 Powder Systems
Parameter | Details |
---|---|
Powder Delivery | Delivered in drums or vacuum sealed bags, store in dry area |
Unloading | Use drum tipper or vacuum transfer to feed hopper |
Transfer Lines | Stainless steel tubing with smooth bends to prevent clogging |
Hoppers | Conical hoppers with min 60° angle to ensure flow, aeration pads |
Filters | 10-20 μm filters for hopper venting |
Surface Finish | Smooth surface finish for powder contact parts |
Sealing | Avoid powder leaks from connections using gaskets/seals |
Grounding | Ground equipment to prevent static discharge |
Safety Systems | Install explosion vents, argon inerting as required |
Proper techniques and equipment for unloading, transfer and storage prevent issues like segregation, caking, corrosion etc. Aeration and filters prevent pressure buildup in hoppers. Grounding eliminates fire hazards due to electrical static discharge.
Operation and Maintenance of Al 2024 Powder Equipment
Operation and Maintenance Guide for Al 2024 Powder Systems
Activity | Instructions | Frequency |
---|---|---|
Leak checks | Check for powder leaks at joints and seals | Monthly |
Hopper inspection | Inspect hopper walls and cone surfaces | 6 months |
Sieve analysis | Take samples and analyse for particle size distribution | Per supplier batch |
Powder quality | Test samples for composition, density, flow rate | Per supplier batch |
Discharge verification | Ensure first-in first-out flow pattern | Monthly |
Aeration pads | Inspect for clogs, clean filter elements | Monthly |
Grounding | Check electrical ground connections | Monthly |
Line clearing | Clear transfer lines using brushes or compressed air | As needed |
Equipment cleaning | Dismantle equipment and clean using solvents | Annual |
Monitoring critical parameters like particle size distribution, apparent density and flow rate ensures consistent powder quality. Regular inspections and maintenance prevent operational issues.
Choosing an Al 2024 Powder Supplier
Key factors in selecting an Al 2024 powder supplier:
Guide to Choosing Al 2024 Powder Supplier
Parameter | Details |
---|---|
Powder specification | Ability to meet required chemical composition, particle size distribution, apparent density |
Quality certifications | ISO 9001, AS9100, ISO 13485 etc. |
Sampling | Provide samples for evaluation; 5-10 kg typical |
Lead time | Ability to deliver required quantity within acceptable lead time |
Technical support | Knowledgeable technical staff for material selection advice |
Customization | Flexibility to tailor powder characteristics or alloy composition |
Testing capabilities | Internal lab for quality checks and certification |
Pricing | Reasonable pricing on volume and trial orders |
Payment terms | Flexible payment terms, especially for new customers |
Logistics | Capable of shipping to buyer location with minimal lead time |
Parameters like consistent quality, reliable delivery, technical expertise and value pricing are vital factors for powder metallurgy users. Sampling enables qualification and testing of powder.
Pros and Cons of Al 2024 Powder
Pros and Cons of Using Al 2024 Powder
Pros | Cons |
---|---|
High strength | Lower strength than steels |
Good corrosion resistance | Susceptible to SCC |
Excellent dimensional stability | Limited complexity of parts |
Good machinability and weldability | Porosity in sintered parts |
Cost effective production | Multiple process steps |
Wide range of applications | Shape limitations vs casting |
Al 2024 powder enables small, complex and net-shape parts but has limitations in achievable strength levels compared to steel. Cost benefits are counterbalanced by multiple steps of compaction, sintering and finishing.
Proper design and processing is needed to minimize porosity. The excellent dimensional stability compensates for inability to produce intricate shapes possible with castings.
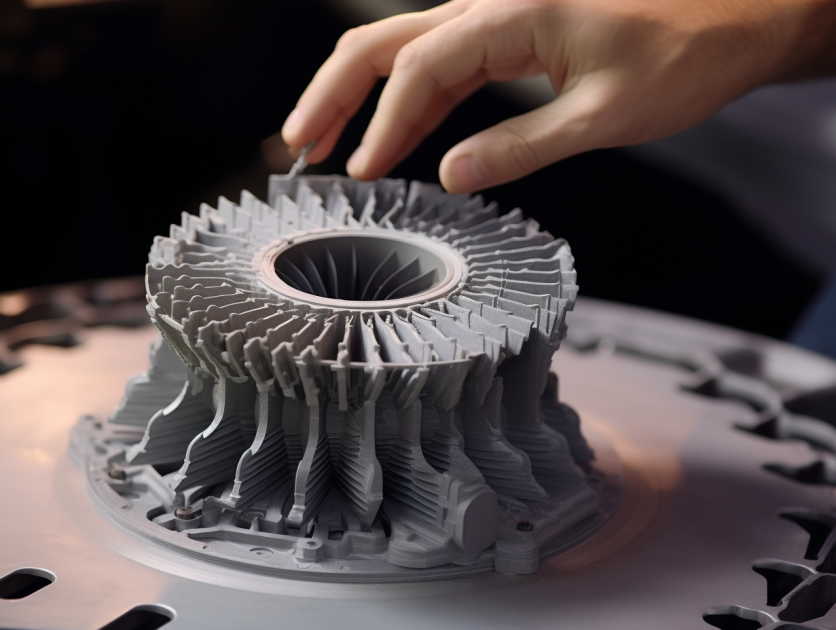
FAQs
FAQs about Al 2024 Powder
Q: What is the typical size range of Al 2024 powder?
A: The typical size range for Al 2024 powder is 10 to 170 microns, with a median size between 60-110 microns for optimal packing and sintering response.
Q: What are the different production methods for Al 2024 powder?
A: Common production methods include gas atomisation, water atomisation, mechanical milling and plasma rotating electrode process. Each has advantages and limitations.
Q: What is the effect of powder particle size on properties?
A: Finer powder size distribution improves flowability and green density after compaction. However, too fine powder can be difficult to handle and compact uniformly.
Q: What are the typical applications of Al 2024 powder?
A: Major applications are in aerospace, automotive, and industrial sectors for high performance structural parts requiring properties like strength, corrosion resistance and dimensional stability.
Q: What is the typical cost range for Al 2024 powder?
A: Cost per kg is approximately $55-65 for 15-53 micron size powder and $35-45 for 105-250 micron size, varying between suppliers.
Q: What quality checks are recommended for Al 2024 powder?
A: Conducting sieve analysis, apparent density, flow rate, and composition testing per powder lot is advisable to ensure consistent properties.
Q: What safety precautions are needed for handling Al 2024 powder?
A: Grounding equipment, using argon inerting, installing explosion vents, and proper protective gear is recommended to prevent accidents during powder handling.
Q: What are the major advantages of using Al 2024 powder?
A: Key advantages include high strength, corrosion resistance, dimensional stability, weldability/machinability, and cost-effective production of small, complex net-shape parts.
Conclusion
Al 2024 alloy powder provides an optimal balance of properties like strength, corrosion resistance, weldability and machinability for fabricating high performance lightweight structural parts via powder metallurgy technique.
Controlled processing and stringent quality procedures are critical when working with Al 2024 powder in order to achieve repeatable material performance in the final sintered components.
With in-depth understanding of the powder metallurgy production process, designers can exploit the near-net-shape capability and complex geometries attainable through press-and-sinter fabrication.