Overview
Pure tungsten powder is a fine powder form of elemental tungsten that is often processed into different materials for a variety of commercial and industrial applications. Key details of pure tungsten powder include:
Chemical formula | W |
CAS Number | 7440-33-7 |
Melting point | 3,422°C (6,192°F) |
Density | 19.3 g/cm3 |
Tungsten powder is valued for possessing the highest melting point of all metals as well as high density, strength, and corrosion resistance. It is commonly used in applications requiring hardness, wear resistance, durability and heat resistance properties.
Some key uses of pure tungsten powder include manufacturing tungsten carbide, tungsten heavy alloys, tungsten mill products, lighting filaments, heating elements, radiation shielding and specialty alloys. The powder can be further processed via sintering, hot isostatic pressing, thermal spray coatings and additive manufacturing.
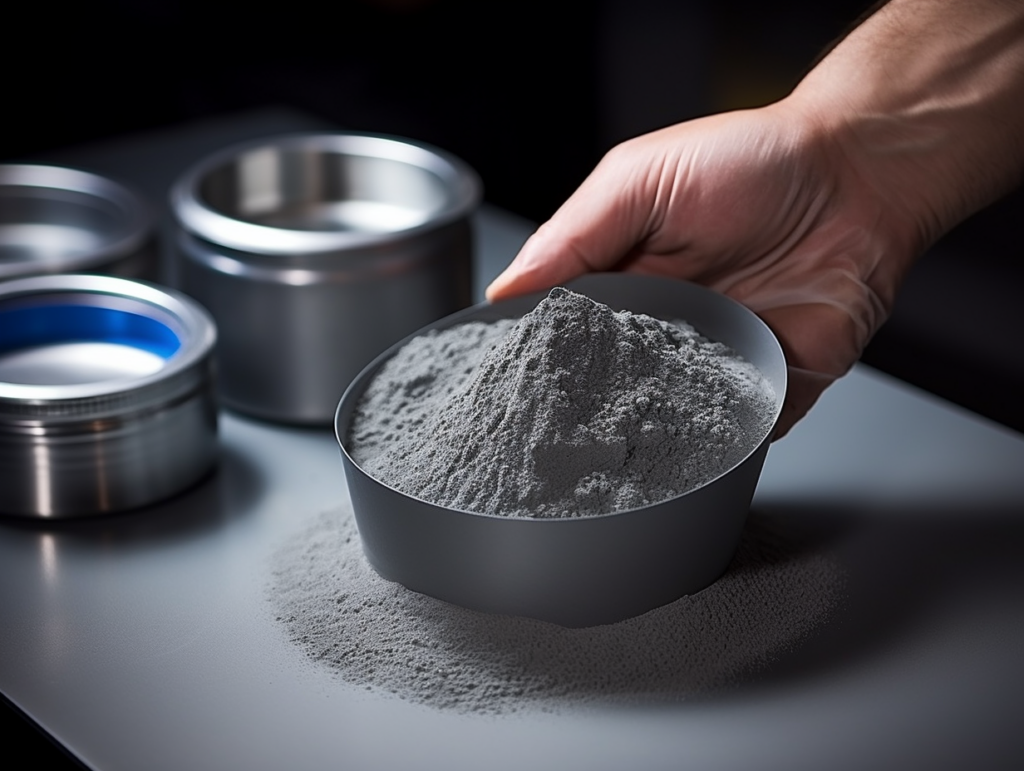
Types of Pure Tungsten Powder
There are several classifications and grades of pure tungsten powder defined by parameters like particle size, morphology, apparent density, and impurity levels:
Type | Description |
Ultrafine powder | High surface area powder with average particle size under 0.5 microns |
Fine powder | Average particle size ranging from 0.5 – 10 microns |
Coarse powder | Particle size above 10 microns |
Nano powder | At least one dimension less than 0.1 micron |
Spherical powder | Rounded particle shape and morphology |
These powders are tailored in size and morphology for specific fabrication processes and to achieve unique material properties in the final part.
Composition of Pure Tungsten Powder
High purity tungsten powders contain over 99.9% elemental tungsten by weight. Impurities may include low levels of carbon, oxygen, nitrogen and other trace elements.
Constituent | Weight % |
Tungsten (W) | 99.9% min |
Carbon (C) | 0.06% max |
Oxygen (O) | 0.03 – 0.1% |
Nitrogen (N) | 0.02% max |
Other trace elements | 0.01% max |
Maintaining high purity levels in the starting powder is critical to achieve final material properties like density, strength and ductility in tungsten products. Specific impurity limits may be defined by various tungsten powder grades and specifications.
Properties of Pure Tungsten Powder
In its pure powder form, tungsten possesses several unique physical and chemical properties:
Property | Value |
Melting point | 3,422°C (6,192°F) |
Boiling point | 5,930°C (10,706°F) |
Density | 19.3 g/cm3 |
Electrical resistivity | 5.5 x 10-6 Ωcm |
Young’s modulus | 411 GPa (59,700 ksi) |
Poisson’s ratio | 0.28 |
Coefficient of thermal expansion | 4.5 x 10-6/K |
Oxidation resistance | Resists oxidation in air up to 600-800°C |
These intrinsic properties are maintained as the powder is converted into other tungsten materials like heavy alloys, mill products, or composites using various powder metallurgy techniques.
Characteristics of Pure Tungsten Powder
In addition to composition and properties, pure tungsten powder is defined by physical characteristics like:
Characteristic | Typical Values |
Particle shape | Irregular, angular |
Particle size distribution | 0.5 – 10 microns |
Apparent density | 2 – 5 g/cm3 |
Specific surface area | 0.5 – 5 m2/g |
Flow properties | Fair flowability and packing density |
These characteristics along with purity influence the quality and consistency of finished tungsten mill products. Powder morphology and size distribution can be customized depending on application requirements.
Applications and Uses of Pure Tungsten Powder
Thanks to its specialized properties, pure tungsten powder has diverse commercial and industrial applications across many sectors:
Application | Uses |
Tungsten carbide (WC) | Cutting tools, mining/drilling equipment, dies, abrasives |
Tungsten heavy alloys | Radiation shielding, counterweights, penetrators |
Filaments | Incandescent, halogen and discharge lamps |
Heating elements | High temperature furnaces, reactors, medical devices |
Mill products | Rods, wires, sheet, foil |
Specialty alloys | Rocket nozzles, radiation shielding, thermocouples |
Additive manufacturing | 3D printed tungsten components |
These examples cover some of the major uses but by no means encompass all applications of this unique metal powder. As materials science and manufacturing technologies advance, the applications of tungsten powder will continue to expand for extreme conditions.
Specifications and Grades of Pure Tungsten Powder
There are several industry standard specifications that define grades and quality parameters for high purity tungsten powder:
Standard | Grades |
ASTM B777 | 99.9% pure (D), 99.95% pure (XD), 99.99% pure (UHP) |
ISO 18118 | APT10, APT20, APT50 |
GB/T 30111 | 99.9%, 99.95%, 99.99% purity grades |
JIS H 3201 | JP1, JP2, JP3, grades |
These define permissible levels of impurities, particle size distribution, apparent density ranges and typical applications suited for each powder grade depending on required material performance. Custom specifications tailored to end-use requirements are also common.
Manufacturers and Suppliers of Pure Tungsten Powder
Some of the major global suppliers manufacturing and distributing high purity tungsten powder include:
Company | Location |
Xiamen Tungsten Co., Ltd. | China |
Midwest Tungsten Service | USA |
Wolfram Company | Austria |
HC Stark | Germany |
Luoyang Tongrun Nano Technology Co. Ltd. | China |
Many additional regional players also offer tungsten powder sourcing, manufacturing and supply chain services to global customers. Both standardized grades as well as customized powder is available.
Pricing for Pure Tungsten Powder
Price ranges for pure tungsten powder depend on factors like:
Type | Price Range |
Ultrafine powder | $150 – $500 per kg |
Fine powder | $80 – $150 per kg |
Coarse powder | $50 – $100 per kg |
Research/custom grades | $300+ per kg |
Prices depend heavily on purity levels, production volumes, regional markets and other customization requirements. High performance ultrafine and nanopowders attract premium pricing.
Pros and Cons of Pure Tungsten Powder
There are several advantages and a few limitations to using pure tungsten powder as a material:
Advantages
- Extremely high melting point
- High density for excellent radiation blocking
- Withstands heat, corrosion, wear and abrasion
- Biocompatible – used in medical devices
- Environmentally responsible manufacturing
Disadvantages
- Expensive base material
- Brittle if not alloyed
- Challenging to machine
- Requires advanced processing for shaping
For applications where heat and radiation resistance coupled with strength and environmental stability are critical, pure tungsten outperforms most other metals and alloys hands down. Its limitations can often be overcome through use of powder metallurgy techniques.
Comparison Between Tungsten Powder Types
Key differences between the various tungsten powder classifications include:
Ultrafine | Fine | Coarse | |
Particle size | Less than 0.5 micron | 0.5 to 10 microns | Over 10 microns |
Surface area | High | Moderate | Low |
Density | Low | Moderate | Higher |
Price | Highest | Mid range | Low |
Ultrafine powders enable unique nanoscale properties but can be challenging to handle. Coarse variants offer easier processing albeit with less specialization. Particle engineering provides customized performance.
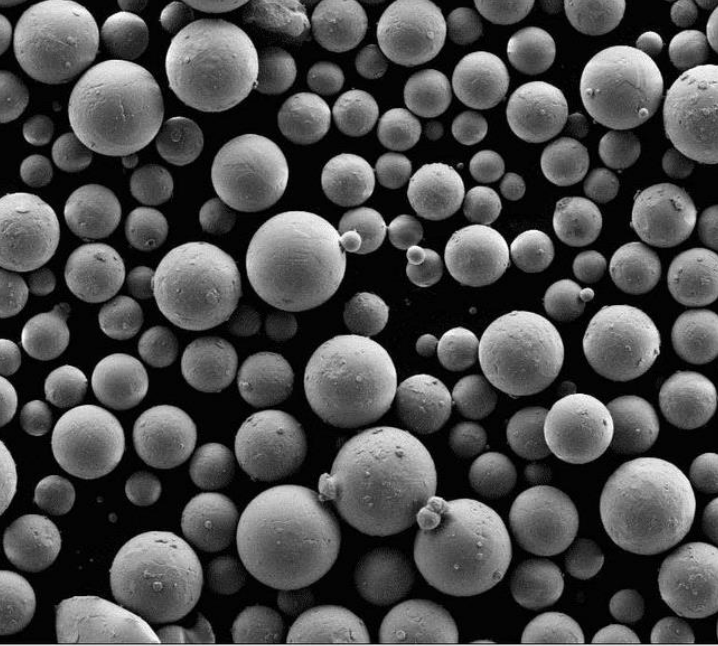
FAQs
Q: Does pure tungsten powder need to go through additional processing before use in applications?
A: Yes, tungsten powder typically requires sintering, hot isostatic pressing, densification, or additive manufacturing before achieving final material properties necessary for end use. Powder metallurgy is critical for producing functional parts.
Q: How is tungsten powder produced?
A: It is commonly produced by hydrogen reduction of tungsten oxides under controlled conditions to generate the high purity elemental powder form. Additional steps like milling, annealing and surface treatment may tailor powder characteristics.
Q: What alloying elements can be added to pure tungsten powder?
A: Small amounts of nickel, iron or copper can be blended with tungsten to produce heavy alloys for various applications requiring different property enhancements. Specific formulations are application-dependent.
Q: Does tungsten powder require special handling during manufacturing or storage?
A: Yes, exposure to air during high temperature processing can induce oxidation so an inert atmosphere is used. Storage under vacuum or inert gas prevents contamination which would degrade performance.
Q: What particle size range is best suited for additive manufacturing with tungsten?
A: Fine powders in the 10-45 micron size range possess good flowability and packing density for uniform layer printing. However nano-powders are being investigated for better densification and properties.
Conclusion
In summary, pure tungsten powder offers exceptional performance across high temperature, radiation-sensitive, and rugged applications spanning many industries. Advancements in powder metallurgy now enable broader implementation of tungsten’s unique material strengths. With expanded manufacturing infrastructure and dropping costs, we can expect purer forms of this crucial technology mineral to find widespread global adoption for pushing performance barriers even in highly demanding use cases. Its unparalleled capabilities make tungsten almost indispensable.