Metal powders are the unsung heroes of modern manufacturing, powering industries from aerospace to medicine. If you’ve ever wondered how your smartphone’s components got so precisely made or how airplanes achieve such incredible strength-to-weight ratios, the answer lies in the world of quality metal powders. Let’s dive into the fascinating universe of these fine, metallic grains and explore their types, properties, and applications in depth.
Overview
Metal powders are finely divided metals that can be used in various manufacturing processes, such as additive manufacturing (3D printing), metal injection molding, and powder metallurgy. These powders come in various forms, compositions, and grades, each tailored to specific applications. The quality of metal powders is determined by their particle size, shape, purity, and distribution, which influence their performance in end-use applications.
Types of Quality Metal Powders
Understanding the types of metal powders available can help in selecting the right material for your specific needs. Below is a detailed look at some common types of metal powders:
Metal Powder | Composition | Properties | Characteristics |
---|---|---|---|
Aluminum Powder | Pure Al or Al alloys | Lightweight, corrosion-resistant | High thermal conductivity, non-toxic |
Titanium Powder | Pure Ti or Ti alloys | High strength-to-weight ratio, biocompatible | Low density, excellent corrosion resistance |
Stainless Steel Powder | Iron with Cr, Ni, Mo | Corrosion-resistant, durable | High strength, weldability |
Copper Powder | Pure Cu or Cu alloys | High electrical and thermal conductivity | Ductile, antibacterial properties |
Nickel Powder | Pure Ni or Ni alloys | Heat and corrosion-resistant | High melting point, magnetic properties |
Cobalt Powder | Pure Co or Co alloys | Hard, wear-resistant | Magnetic properties, high temperature stability |
Iron Powder | Pure Fe or Fe alloys | Magnetic, high strength | Affordable, versatile |
Tungsten Powder | Pure W or W alloys | Very high melting point, dense | Extremely hard, excellent thermal conductivity |
Magnesium Powder | Pure Mg or Mg alloys | Very light, high strength | Highly reactive, used in pyrotechnics |
Zinc Powder | Pure Zn or Zn alloys | Corrosion-resistant, easily castable | Low melting point, used in galvanizing |
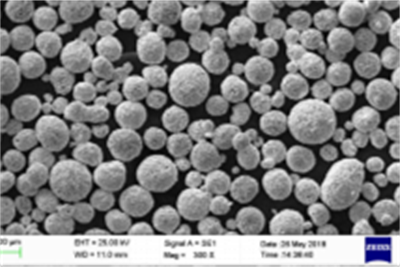
Applications of Quality Metal Powder
Metal powders find use in various industries and applications. Here’s a look at where these powders shine:
Application | Metal Powder Used | Description |
---|---|---|
Aerospace | Titanium, Aluminum | Lightweight components, high strength |
Automotive | Iron, Stainless Steel, Aluminum | Engine parts, structural components |
Medical | Titanium, Cobalt-Chromium | Implants, surgical tools |
Electronics | Copper, Silver, Gold | Conductive inks, components |
Energy | Nickel, Cobalt, Copper | Batteries, fuel cells |
Construction | Iron, Zinc | Structural parts, galvanization |
Jewelry | Gold, Silver, Platinum | High-value adornments, intricate designs |
Manufacturing | Iron, Stainless Steel, Aluminum | Metal Injection Molding, 3D Printing |
Defense | Tungsten, Aluminum | Armor, munitions |
Consumer Goods | Aluminum, Stainless Steel | Appliances, hardware |
Composition of Quality Metal Powder
The composition of metal powders is critical to their performance. This section breaks down the elemental make-up of various metal powders:
Metal Powder | Main Elements | Alloying Elements |
---|---|---|
Aluminum Powder | Al | Mg, Si, Cu, Zn |
Titanium Powder | Ti | Al, V, Sn |
Stainless Steel Powder | Fe, Cr | Ni, Mo, C |
Copper Powder | Cu | Zn, Sn, Ni |
Nickel Powder | Ni | Cr, Fe, Mo |
Cobalt Powder | Co | Cr, Ni, Mo |
Iron Powder | Fe | C, Mn, Si |
Tungsten Powder | W | Co, Ni, Fe |
Magnesium Powder | Mg | Al, Zn, Mn |
Zinc Powder | Zn | Al, Cu |
Characteristics of Quality Metal Powder
Understanding the characteristics of metal powders can help in choosing the right material for specific applications. Here’s an overview of key characteristics:
Characteristic | Description |
---|---|
Particle Size | Affects flowability, packing density, and sintering behavior |
Particle Shape | Spherical, irregular, or flake-like shapes influence packing and processing |
Purity | Higher purity often means better performance and fewer defects |
Density | Affects weight and strength of the final product |
Surface Area | Larger surface area can enhance reactivity and bonding in composites |
Flowability | Important for processes like 3D printing and powder metallurgy |
Packing Density | Influences the mechanical properties of the sintered part |
Grades of Quality Metal Powder
Different grades of metal powders are available to meet various industrial standards and specifications. Here’s a look at the grades for common metal powders:
Metal Powder | Grades | Description |
---|---|---|
Aluminum Powder | 1100, 2024, 6061 | Varying levels of alloying elements for strength and machinability |
Titanium Powder | Grade 1, Grade 2, Grade 5 | Pure titanium to high-strength alloys |
Stainless Steel Powder | 304, 316, 17-4 PH | Corrosion resistance and mechanical properties |
Copper Powder | C11000, C22000, C36000 | Electrical conductivity and machinability |
Nickel Powder | Nickel 200, Inconel 625, Hastelloy X | Heat and corrosion resistance |
Cobalt Powder | CoCr, MP35N | High strength and wear resistance |
Iron Powder | A1000, Distaloy AE, Acrawax C | Magnetic properties and sintering performance |
Tungsten Powder | W1, W2, WCu | High density and thermal conductivity |
Magnesium Powder | AZ31, AZ91 | Lightweight and high strength |
Zinc Powder | Zamak 3, Zamak 5 | Corrosion resistance and ease of casting |
Specifications, Sizes, Grades, and Standards
It’s crucial to understand the specifications, sizes, grades, and standards for metal powders to ensure the right fit for your application. Here’s a detailed table to guide you:
Metal Powder | Specification | Sizes | Grades | Standards |
---|---|---|---|---|
Aluminum Powder | ASTM B928 | 10-200 µm | 1100, 2024, 6061 | ASTM, SAE, ISO |
Titanium Powder | ASTM B348 | 15-150 µm | Grade 1, Grade 2, Grade 5 | ASTM, AMS, ISO |
Stainless Steel Powder | ASTM A276 | 20-250 µm | 304, 316, 17-4 PH | ASTM, SAE, ISO |
Copper Powder | ASTM B5 | 10-200 µm | C11000, C22000, C36000 | ASTM, SAE, ISO |
Nickel Powder | ASTM B446 | 15-200 µm | Nickel 200, Inconel 625 | ASTM, AMS, ISO |
Cobalt Powder | ASTM F75 | 20-250 µm | CoCr, MP35N | ASTM, SAE, ISO |
Iron Powder | ASTM B213 | 20-250 µm | A1000, Distaloy AE | ASTM, SAE, ISO |
Tungsten Powder | ASTM B777 | 15-150 µm | W1, W2, WCu | ASTM, ISO |
Magnesium Powder | ASTM B92 | 10-200 µm | AZ31, AZ91 | ASTM, SAE, ISO |
Zinc Powder | ASTM B6 | 10-200 µm | Zamak 3, Zamak 5 | ASTM, SAE, ISO |
Suppliers and Pricing Details
To make informed purchasing decisions, knowing the suppliers and pricing details is essential. Here’s a look at some major suppliers and their pricing:
Supplier | Metal Powder | Price (per kg) | Notes |
---|---|---|---|
Höganäs AB | Iron, Stainless Steel | $10 – $50 | Wide range of metal powders |
Carpenter Technology | Titanium, Nickel | $50 – $200 | High-performance alloys |
Sandvik | Stainless Steel, Nickel | $20 – $100 | Advanced manufacturing |
GKN Hoeganaes | Iron, Aluminum | $10 – $60 | Automotive and industrial |
LPW Technology | Aluminum, Titanium | $40 – $150 | Additive manufacturing focus |
Vale | Nickel, Cobalt | $50 – $200 | High-purity powders |
AMETEK | Copper, Zinc | $15 – $70 | Specialty metal powders |
Rio Tinto Metal Powders | Iron, Stainless Steel | $10 – $60 | Industrial applications |
Kennametal | Tungsten, Cobalt | $100 – $500 | High-temperature applications |
Advanced Powder Products | Various | Varies | Custom powder solutions |
Pros and Cons: Comparing Quality Metal Powders
When selecting a metal powder, it’s important to weigh the pros and cons. Here’s a comparison:
Metal Powder | Advantages | Disadvantages |
---|---|---|
Aluminum Powder | Lightweight, corrosion-resistant, high conductivity | Lower strength compared to some other metals |
Titanium Powder | High strength-to-weight ratio, biocompatible | Expensive, challenging to process |
Stainless Steel Powder | Corrosion-resistant, durable, versatile | Higher density, expensive compared to plain iron |
Copper Powder | Excellent electrical and thermal conductivity, ductile | Heavier than aluminum, can tarnish |
Nickel Powder | Heat and corrosion-resistant, high strength | Expensive, limited availability in some regions |
Cobalt Powder | Hard, wear-resistant, magnetic properties | Expensive, health risks with dust exposure |
Iron Powder | Affordable, magnetic, versatile | Prone to rust if not alloyed or protected |
Tungsten Powder | Very high melting point, extremely hard | Very dense, difficult to work with |
Magnesium Powder | Extremely lightweight, good strength | Highly reactive, flammable in powder form |
Zinc Powder | Corrosion-resistant, easily castable | Lower strength, low melting point |
Composition, Characteristics, and Properties: Detailed Insights
Composition of Quality Metal Powder
The composition of metal powders determines their properties and suitability for various applications. Let’s delve deeper:
Metal Powder | Primary Element | Alloying Elements | Typical Applications |
---|---|---|---|
Aluminum Powder | Al | Mg (magnesium), Si (silicon), Cu (copper) | Aerospace, automotive, electronics |
Titanium Powder | Ti | Al (aluminum), V (vanadium), Sn (tin) | Medical implants, aerospace, defense |
Stainless Steel Powder | Fe | Cr (chromium), Ni (nickel), Mo (molybdenum) | Construction, medical devices, consumer goods |
Copper Powder | Cu | Zn (zinc), Sn (tin), Ni (nickel) | Electrical components, plumbing, electronics |
Nickel Powder | Ni | Cr (chromium), Fe (iron), Mo (molybdenum) | High-temperature applications, batteries |
Cobalt Powder | Co | Cr (chromium), Ni (nickel), Mo (molybdenum) | Medical devices, superalloys, batteries |
Iron Powder | Fe | C (carbon), Mn (manganese), Si (silicon) | Automotive parts, construction, electronics |
Tungsten Powder | W | Co (cobalt), Ni (nickel), Fe (iron) | Cutting tools, electronics, defense |
Magnesium Powder | Mg | Al (aluminum), Zn (zinc), Mn (manganese) | Automotive parts, electronics, pyrotechnics |
Zinc Powder | Zn | Al (aluminum), Cu (copper) | Galvanizing, die-casting, batteries |
Characteristics of Quality Metal Powder
The characteristics of metal powders influence their processing and performance in applications:
Characteristic | Description |
---|---|
Particle Size | Smaller particles enhance surface area and reactivity; larger particles improve flowability |
Particle Shape | Spherical particles improve flowability and packing; irregular shapes may enhance bonding |
Purity | Higher purity reduces contamination and improves material properties |
Density | Determines the weight and mechanical strength of the final product |
Surface Area | Higher surface area can improve bonding and sintering properties |
Flowability | Crucial for powder-based manufacturing processes |
Packing Density | Affects the porosity and mechanical properties of the final part |
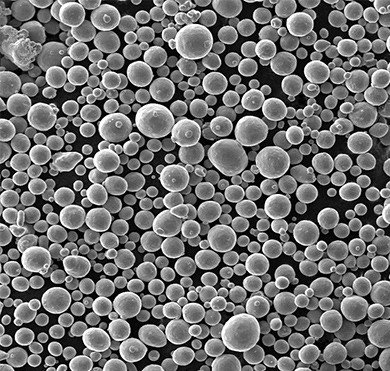
FAQ
To wrap things up, let’s address some frequently asked questions about quality metal powder.
Question | Answer |
---|---|
What are metal powders used for? | Metal powders are used in 3D printing, metal injection molding, powder metallurgy, and various coating processes. |
How are metal powders made? | Metal powders can be produced through atomization, chemical reduction, electrolysis, and mechanical comminution. |
Why is particle size important? | Particle size affects the flowability, packing density, and sintering behavior of the powder. |
What is the difference between pure and alloyed metal powders? | Pure metal powders consist of a single metal, while alloyed powders contain a mixture of metals to enhance specific properties. |
Can metal powders be recycled? | Yes, metal powders can often be recycled and reused, depending on the process and material. |
What safety precautions are necessary when handling metal powders? | Proper ventilation, protective equipment, and handling procedures are essential to prevent inhalation and combustion risks. |
How does the shape of metal powder particles affect their use? | Spherical particles generally flow better and pack more efficiently, while irregular shapes may enhance bonding in composites. |
What industries benefit most from metal powders? | Aerospace, automotive, medical, electronics, energy, and construction industries all benefit significantly from metal powders. |
How does purity affect metal powder performance? | Higher purity reduces contamination, improves material properties, and enhances the performance of the final product. |
Are there standards for metal powders? | Yes, there are industry standards such as ASTM, SAE, and ISO that specify the requirements for various metal powders. |
Conclusion
Quality metal powders are indispensable in modern manufacturing, providing the foundation for a wide array of products across diverse industries. From the lightweight, high-strength components in aerospace to the intricate medical implants saving lives, metal powders are at the core of innovation. Understanding their types, compositions, characteristics, and applications ensures that manufacturers can select the best materials for their needs, optimizing performance and efficiency.
By considering the detailed insights into various metal powders, their grades, and the associated pros and cons, you can make informed decisions that align with your specific requirements. Whether you’re in aerospace, automotive, medical, or any other industry, quality metal powders offer a world of possibilities, driving advancements and enhancing the quality of products we rely on every day.