Introduction to REP Powders
In the ever-evolving world of materials science, REP powders have carved out a niche as a go-to resource for a range of industrial applications. But what makes these powders so special? Whether you’re new to REP powders or a seasoned professional looking to deepen your understanding, this guide has got you covered.
We’ll dive deep into the world of REP powders, exploring their composition, characteristics, and the specific models that stand out in the market today. But first, let’s start with the basics.
Understanding REP Powders: What Are They?
If you’ve stumbled upon the term “REP powders” and wondered what exactly it entails, you’re in the right place. REP stands for Rapidly Evaporated Powder—a category of metal powders created through a process known as rapid solidification.
The Science Behind REP Powders
REP powders are produced by atomizing molten metal into fine droplets that solidify rapidly as they cool. This rapid cooling process results in powders with unique microstructures and properties, such as high purity, uniformity, and fine grain size, which make them ideal for various advanced manufacturing processes.
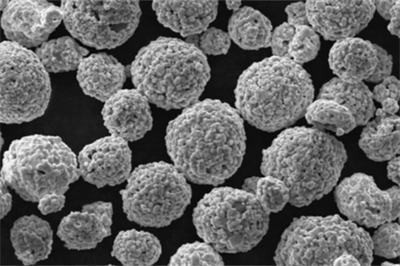
Key Applications of REP Powders
REP powders are used in an array of applications across industries due to their versatile properties. Below is a detailed overview of where these powders are most commonly applied:
Application | Description |
---|---|
Additive Manufacturing | REP powders are widely used in 3D printing technologies like SLM (Selective Laser Melting) and DMLS (Direct Metal Laser Sintering) for creating complex parts. |
Metal Injection Molding (MIM) | The fine particle size and high purity of REP powders make them perfect for MIM, where precise control over material properties is crucial. |
Surface Coating | These powders are often used in thermal spraying and other coating processes to enhance the surface properties of industrial components. |
Powder Metallurgy | In powder metallurgy, REP powders are pressed and sintered to create high-performance components with excellent mechanical properties. |
Electronics | Due to their fine microstructure, REP powders are used in the production of high-density interconnects and other electronic components. |
Composition and Characteristics of REP Powders
When it comes to understanding REP powders, delving into their composition and characteristics is crucial. Here’s what makes these powders unique:
Composition of REP Powders
REP powders can be composed of a variety of metals and alloys, each tailored to specific applications. Common materials include:
- Aluminum Alloys: Lightweight, corrosion-resistant, used in aerospace and automotive industries.
- Titanium Alloys: High strength-to-weight ratio, excellent corrosion resistance, often used in biomedical implants.
- Nickel Alloys: Superior heat and corrosion resistance, ideal for high-temperature applications in the aerospace sector.
- Stainless Steels: Known for their corrosion resistance and mechanical properties, widely used in medical and food processing industries.
- Copper Alloys: Excellent electrical conductivity, used in electronics and electrical components.
Characteristics of REP Powders
The unique characteristics of REP powders stem from their rapid solidification process. These include:
- Fine Grain Structure: The rapid cooling leads to a fine and uniform grain structure, which enhances mechanical properties.
- High Purity: The controlled atomization process minimizes contamination, resulting in powders of high chemical purity.
- Spherical Shape: REP powders often have a spherical shape, improving flowability and packing density—key factors in additive manufacturing and powder metallurgy.
- High Surface Area: The fine particle size increases the surface area, which can be beneficial for sintering and chemical reactions.
Top 10 REP Powder Models
Choosing the right REP powder depends on your specific application needs. Here’s a list of the top 10 REP powder models, each with its unique properties and applications:
1. AlSi10Mg (Aluminum-Silicon-Magnesium Alloy)
- Composition: Al-10%Si-0.5%Mg
- Properties: Lightweight, good thermal conductivity, excellent strength-to-weight ratio.
- Applications: Aerospace components, automotive parts, and lightweight structural elements.
2. Ti6Al4V (Titanium Alloy)
- Composition: Ti-6%Al-4%V
- Properties: High strength, low density, excellent biocompatibility.
- Applications: Biomedical implants, aerospace components, and high-performance sports equipment.
3. Inconel 718 (Nickel-Chromium Alloy)
- Composition: Ni-52.5%, Cr-19%, Fe, Nb, Mo
- Properties: Excellent high-temperature strength, oxidation resistance, and corrosion resistance.
- Applications: Jet engine components, gas turbines, and high-stress parts.
4. 316L Stainless Steel
- Composition: Fe-17%Cr-12%Ni-2%Mo
- Properties: Corrosion-resistant, non-magnetic, high ductility.
- Applications: Medical devices, food processing equipment, and marine components.
5. CuCrZr (Copper-Chromium-Zirconium Alloy)
- Composition: Cu-0.5%Cr-0.1%Zr
- Properties: High electrical conductivity, good strength, and thermal stability.
- Applications: Electrical contacts, heat sinks, and welding electrodes.
6. Maraging Steel (1.2709)
- Composition: Fe-18%Ni-8%Co-5%Mo
- Properties: Ultra-high strength, good toughness, and excellent dimensional stability.
- Applications: Tooling, high-performance gears, and aerospace components.
7. Hastelloy X (Nickel-Molybdenum-Chromium Alloy)
- Composition: Ni-22%Cr-9%Mo-18%Fe
- Properties: Outstanding high-temperature strength and oxidation resistance.
- Applications: Gas turbines, chemical processing, and furnace components.
8. CoCrMo (Cobalt-Chromium-Molybdenum Alloy)
- Composition: Co-28%Cr-6%Mo
- Properties: High wear resistance, excellent biocompatibility.
- Applications: Orthopedic implants, dental prosthetics, and high-wear components.
9. NiCr (Nickel-Chromium Alloy)
- Composition: Ni-80%Cr-20%
- Properties: Exceptional high-temperature strength and oxidation resistance.
- Applications: Heating elements, thermocouples, and high-temperature components.
10. AlSi12 (Aluminum-Silicon Alloy)
- Composition: Al-12%Si
- Properties: Excellent castability, good corrosion resistance, and high thermal conductivity.
- Applications: Automotive engine components, heat exchangers, and lightweight structural parts.
Comparing REP Powders: Properties and Applications
Understanding the differences between REP powders can help you select the right material for your specific application. Let’s dive into a comparative analysis:
REP Powder | Key Properties | Ideal Applications |
---|---|---|
AlSi10Mg | Lightweight, high thermal conductivity, good mechanical properties | Aerospace, automotive, lightweight structures |
Ti6Al4V | High strength, biocompatible, corrosion-resistant | Biomedical implants, aerospace, sports equipment |
Inconel 718 | High-temperature strength, oxidation and corrosion-resistant | Jet engines, gas turbines, high-stress environments |
316L Stainless Steel | Corrosion-resistant, non-magnetic, high ductility | Medical devices, food processing, marine applications |
CuCrZr | High electrical conductivity, good thermal stability | Electrical components, heat sinks, welding electrodes |
Maraging Steel | Ultra-high strength, excellent dimensional stability | Tooling, aerospace, high-performance components |
Hastelloy X | Outstanding high-temperature strength, oxidation resistance | Gas turbines, chemical processing, furnace components |
CoCrMo | High wear resistance, biocompatible | Orthopedic implants, dental prosthetics |
NiCr | Exceptional high-temperature strength, oxidation resistance | Heating elements, thermocouples |
AlSi12 |
Excellent castability, good corrosion resistance | Automotive engines, heat exchangers |
Advantages and Disadvantages of REP Powders
No material is perfect, and REP powders are no exception. Let’s explore the pros and cons of using REP powders in various applications.
Advantages of REP Powders
- High Purity and Consistency: The rapid solidification process ensures that REP powders have minimal impurities, which is crucial for high-performance applications.
- Fine Grain Structure: The unique microstructure of REP powders offers improved mechanical properties, such as strength and toughness, compared to conventional powders.
- Spherical Shape: The spherical particles improve flowability, which is particularly beneficial in additive manufacturing processes.
- Versatility: REP powders can be tailored to meet specific requirements, making them suitable for a wide range of applications from aerospace to electronics.
Disadvantages of REP Powders
- Cost: The advanced production process of REP powders can make them more expensive than traditional powders.
- Availability: Due to the specialized nature of REP powders, they may not be as readily available as other types of metal powders.
- Processing Requirements: The fine particle size and unique properties of REP powders may require specialized equipment and processes, adding complexity to their use.
Key Specifications, Sizes, and Standards of REP Powders
When selecting REP powders for your project, understanding the specifications, sizes, and standards is crucial. Below is an overview of the key parameters to consider:
Specification | Description |
---|---|
Particle Size Distribution | Typically ranges from 10 to 100 microns, depending on the application. |
Purity | REP powders are often 99.9% pure or higher, with minimal impurities. |
Density | Varies depending on the material, but typically ranges from 2.7 g/cm³ (Aluminum alloys) to 8.9 g/cm³ (Nickel alloys). |
Flowability | Spherical shape improves flowability, measured in seconds/50g flow rate. |
Standards | Conforms to international standards such as ASTM B214 for particle size distribution and ISO 4499 for microstructure. |
Top Suppliers and Pricing Details
Sourcing REP powders from reputable suppliers is key to ensuring quality and consistency. Below is a list of some top suppliers and an overview of their pricing:
Supplier | Notable Products | Pricing (per kg) |
---|---|---|
Höganäs AB | AlSi10Mg, Ti6Al4V | $150 – $300 |
Carpenter Technology | Inconel 718, Hastelloy X | $200 – $400 |
Sandvik Osprey | 316L Stainless Steel, Maraging Steel | $100 – $250 |
LPW Technology | CoCrMo, NiCr | $180 – $350 |
Arcam AB (GE Additive) | AlSi12, Ti6Al4V | $150 – $280 |
AP&C (Advanced Powders & Coatings) | Titanium alloys, Nickel alloys | $220 – $400 |
GKN Additive | Copper alloys, Stainless steels | $130 – $270 |
EOS GmbH | AlSi10Mg, Maraging Steel | $140 – $320 |
Aubert & Duval | Nickel alloys, Cobalt alloys | $210 – $420 |
Praxair Surface Technologies | Hastelloy X, Inconel 718 | $190 – $380 |
How to Choose the Right REP Powder for Your Application
Selecting the right REP powder for your specific needs can be a daunting task, given the wide array of options available. Here’s a step-by-step guide to help you make the right choice:
Step 1: Define Your Application Requirements
Start by clearly defining what you need from the material. Are you looking for something that offers high strength at elevated temperatures, or do you need a powder with excellent corrosion resistance? The end-use application will dictate your choice of material.
Step 2: Consider Material Properties
Based on your application, narrow down the materials that offer the properties you need. For example, if you require a lightweight material with good thermal conductivity, an aluminum alloy like AlSi10Mg might be the best choice.
Step 3: Evaluate Manufacturing Process Compatibility
Ensure that the REP powder you choose is compatible with your manufacturing process. For instance, some powders are better suited for additive manufacturing, while others are ideal for powder metallurgy or metal injection molding.
Step 4: Compare Suppliers and Pricing
Once you’ve identified the right material, compare suppliers to find the best quality and pricing. Consider factors like supplier reputation, delivery times, and customer support.
Step 5: Test and Validate
Before committing to a large purchase, it’s wise to test the powder in small quantities to validate its performance in your specific application.
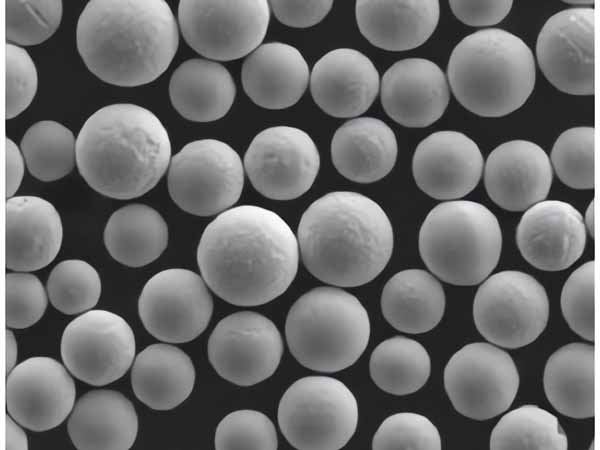
FAQs
Q: What are REP powders used for?
A: REP powders are used in various applications, including additive manufacturing, powder metallurgy, metal injection molding, and surface coating. Their fine grain structure and high purity make them ideal for high-performance parts.
Q: How are REP powders made?
A: REP powders are produced by rapidly solidifying molten metal droplets, resulting in fine, uniform powders with unique microstructures.
Q: Are REP powders expensive?
A: Yes, REP powders can be more expensive than traditional metal powders due to their advanced production process and high purity.
Q: What materials can be made into REP powders?
A: REP powders can be made from a variety of metals and alloys, including aluminum, titanium, nickel, stainless steel, cobalt, and copper.
Q: How do I choose the right REP powder for my application?
A: To choose the right REP powder, consider your application requirements, material properties, manufacturing process compatibility, supplier options, and budget.
Q: Can REP powders be used in 3D printing?
A: Yes, REP powders are widely used in 3D printing technologies like SLM and DMLS, thanks to their fine grain structure and excellent flowability.
Conclusion
REP powders represent a cutting-edge advancement in materials science, offering unparalleled properties for a wide range of applications. Whether you’re working in aerospace, medical, or electronics, these powders provide the performance and versatility you need. By understanding their unique characteristics, comparing different models, and knowing how to choose the right material, you can make informed decisions that will enhance your projects.
This guide aimed to cover every aspect of REP powders, from their composition to their applications, to help you navigate the complex world of materials with confidence. If you have more questions or need further guidance, don’t hesitate to reach out to suppliers or industry experts who can provide tailored advice for your specific needs.