The rotating electrode process (REP) is a fascinating and versatile method for producing metal powders, particularly those used in additive manufacturing, thermal spraying, and high-performance materials. This process is renowned for its ability to produce spherical powders with controlled particle sizes, which are essential in various industrial applications. In this article, we’ll dive deep into the intricacies of the rotating electrode process, exploring its composition, characteristics, advantages, and the specific types of metal powders it can produce.
We’ll also discuss its applications, provide comparisons with other methods, and guide you through selecting the right materials and suppliers for your needs.
Overview of the Rotating Electrode Process
The rotating electrode process is a specialized powder production method used in industries where precision and material properties are critical. The process involves melting a metal electrode while it rotates at high speed, causing molten droplets to be flung off and solidified into fine, spherical particles. This technique is particularly favored for producing metal powders with tight control over size distribution and purity.
Key Components and Steps in the Rotating Electrode Process
- Electrode Preparation: A metal rod, or electrode, is selected based on the desired powder composition.
- Rotation and Heating: The electrode is rotated at high speeds while an energy source (usually an electric arc or plasma) melts its surface.
- Powder Formation: Centrifugal forces propel molten metal droplets from the electrode, which solidify into fine spherical powders as they cool.
- Collection: The resulting powders are collected, sorted by size, and processed for further use.
This process is used to produce powders from a variety of metals and alloys, which are then used in industries ranging from aerospace to biomedical engineering.
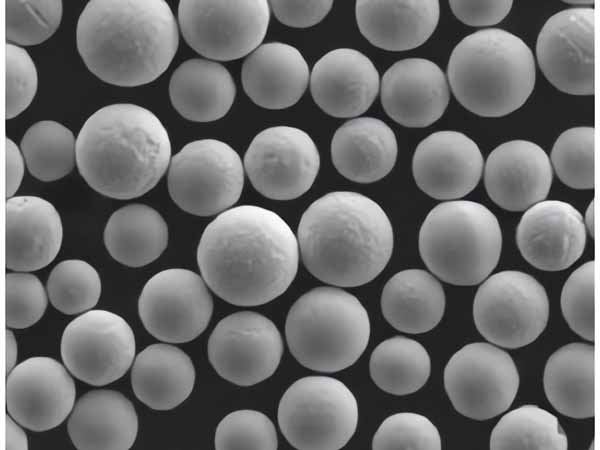
Composition and Characteristics of Metals in the Rotating Electrode Process
Metal Type | Composition | Characteristics | Typical Applications |
---|---|---|---|
Titanium (Ti) | Pure Ti or Ti alloys (e.g., Ti-6Al-4V) | High strength, lightweight, corrosion-resistant | Aerospace, biomedical implants |
Nickel (Ni) | Pure Ni or Ni-based superalloys (e.g., Inconel) | High temperature resistance, corrosion-resistant | Turbine blades, aerospace, chemical processing |
Stainless Steel | Fe-Cr-Ni alloys (e.g., 316L) | Corrosion-resistant, durable | Medical devices, automotive, construction |
Cobalt-Chromium | Co-Cr alloys (e.g., CoCrMo) | Wear-resistant, biocompatible | Dental implants, orthopedic devices |
Aluminum (Al) | Pure Al or Al alloys (e.g., Al6061) | Lightweight, high conductivity | Automotive, aerospace, electronics |
Copper (Cu) | Pure Cu or Cu alloys (e.g., CuCrZr) | High electrical and thermal conductivity | Electrical components, heat exchangers |
Tantalum (Ta) | Pure Ta or Ta alloys | High melting point, corrosion-resistant | Electronics, medical implants |
Zirconium (Zr) | Pure Zr or Zr alloys | High corrosion resistance, biocompatible | Nuclear reactors, medical devices |
Magnesium (Mg) | Pure Mg or Mg alloys (e.g., AZ91) | Lightweight, good machinability | Aerospace, automotive, electronics |
Tungsten (W) | Pure W or W alloys | Very high melting point, density, hardness | Cutting tools, radiation shielding, aerospace |
Applications of Metal Powders Produced by the Rotating Electrode Process
Metal powders produced by the rotating electrode process are critical in several high-tech industries. Their controlled particle size and spherical shape make them ideal for applications where precision and performance are paramount.
Applications of Metal Powders Produced by the Rotating Electrode Process
Industry | Application | Benefits of REP Powders |
---|---|---|
Aerospace | Additive manufacturing of engine components | High strength-to-weight ratio, temperature resistance |
Biomedical Engineering | 3D printing of implants and prosthetics | Biocompatibility, precise control over geometry |
Automotive | Powder metallurgy for lightweight components | Weight reduction, enhanced performance |
Electronics | Sintering for conductive pathways | High conductivity, reliability |
Energy | Thermal spraying for turbine blades | Wear resistance, efficiency improvement |
Defense | Armor and shielding materials | High density, protective properties |
Tooling and Machining | Production of cutting tools | Hardness, wear resistance |
Nuclear | Fuel cladding and structural components | Corrosion resistance, durability |
Specifications, Sizes, Grades, and Standards in the Rotating Electrode Process
Selecting the right metal powder involves understanding the specifications, sizes, grades, and standards that apply to your industry. Below, we outline some of the critical parameters you need to consider.
Specifications and Grades of Metal Powders in the Rotating Electrode Process
Metal Type | Particle Size Range (µm) | Grade | Standards | Applications |
---|---|---|---|---|
Titanium (Ti) | 15-45 | ASTM F67 | ASTM F67, ISO 5832-2 | Biomedical implants, aerospace |
Nickel (Ni) | 10-53 | AMS 5662 | AMS 5662, ASTM B243 | High-temp alloys, aerospace |
Stainless Steel | 20-90 | 316L | ASTM A276, ISO 5832-1 | Medical devices, construction |
Cobalt-Chromium | 15-45 | CoCrMo | ASTM F75, ISO 5832-4 | Dental implants, orthopedic devices |
Aluminum (Al) | 15-63 | 6061 | ASTM B209, AMS 4027 | Automotive, aerospace |
Copper (Cu) | 10-45 | C11000 | ASTM B170, UNS C11000 | Electrical components, heat exchangers |
Tantalum (Ta) | 20-80 | R05200 | ASTM F560, UNS R05200 | Medical implants, electronics |
Zirconium (Zr) | 15-60 | Zr702 | ASTM B551, UNS R60702 | Nuclear reactors, medical devices |
Magnesium (Mg) | 10-45 | AZ91D | ASTM B93, AMS 4377 | Aerospace, automotive |
Tungsten (W) | 5-20 | W1 | ASTM B777, UNS W73120 | Cutting tools, radiation shielding |
Key Standards for Rotating Electrode Process Powders
- ASTM International: Provides standards for various metal powders, ensuring they meet the necessary specifications for specific applications.
- ISO (International Organization for Standardization): Establishes international standards that facilitate global trade and quality assurance.
- AMS (Aerospace Material Specifications): Essential for aerospace applications, ensuring materials meet the rigorous demands of the industry.
-
CM247LC Powder | Nickel Alloy Powder
-
0# Pure Nickel powder
-
NiCoCrAlY alloys powders
-
Rene 142 alloy-Rene Powder
-
Haynes 25 Haynes Powder
-
Best Hastelloy C-22 Powder-High temperature alloy Powder for 3D Printing
-
Best Hastelloy C-276 Powder-High temperature alloy Powder for 3D Printing
-
Best Hastelloy N Powder-High temperature alloy Powder for 3D Printing
-
Best Hastelloy B Powder丨High temperature alloy Powder for 3D Printing
Pros and Cons of the Rotating Electrode Process Compared to Other Powder Production Methods
Like any manufacturing process, the rotating electrode process has its advantages and limitations. Understanding these can help you determine if it’s the right method for your application.
Table: Advantages and Disadvantages of the Rotating Electrode Process
Factor | Rotating Electrode Process | Other Methods |
---|---|---|
Powder Quality | High sphericity, low contamination | Variable sphericity, potential contamination |
Particle Size Control | Excellent control over particle size distribution | Less control, broader size distribution |
Material Loss | Minimal material waste due to efficient process | Higher waste, particularly in atomization processes |
Cost | Generally higher due to specialized equipment | Lower, but may result in inferior powder quality |
Process Complexity | Requires precise control of rotation and melting | Simpler processes available, like gas atomization |
Versatility | Suitable for a wide range of metals and alloys | Some methods are material-specific |
Comparing Rotating Electrode Process with Gas Atomization
Gas atomization is another popular method for producing metal powders, often compared to the rotating electrode process.
- Quality vs. Cost: The rotating electrode process typically produces higher-quality powders with better sphericity and size control, but it can be more expensive. Gas atomization is less costly but may not achieve the same level of powder uniformity.
- Efficiency: While gas atomization is more straightforward and can be less costly, the rotating electrode process minimizes waste and can produce powders with fewer impurities.
Key Suppliers and Pricing for Rotating Electrode Process Powders
Sourcing high-quality metal powders is crucial for ensuring the success of your projects. Below, we list some reputable suppliers and provide indicative pricing for various metal powders produced using the rotating electrode process.
Suppliers and Pricing of Metal Powders from the Rotating Electrode Process
Supplier | Metal Type | Pricing (per kg) | Available Grades | Location |
---|---|---|---|---|
Carpenter Technology | Titanium, Nickel | $500 – $800 | ASTM F67, AMS 5662 | USA |
LPW Technology | Stainless Steel, CoCr | $150 – $400 | 316L, CoCrMo | UK, USA |
Höganäs | Aluminum, Copper | $100 – $300 | 6061, C11000 | Sweden, Global |
Praxair Surface Technologies | Nickel, Titanium | $600 – $900 | Inconel 718, Ti-6Al-4V | USA, Global |
Sandvik Osprey | Stainless Steel, Ni | $200 – $450 | 316L, Inconel 625 | Sweden, UK, Global |
Tekna | Aluminum, Magnesium | $250 – $600 | AZ91D, AlSi10Mg | Canada, Global |
AP&C (GE Additive) | Titanium, Tantalum | $700 – $1000 | Ti-6Al-4V, R05200 | Canada, USA |
Arcam EBM (GE Additive) | Titanium, Zirconium | $750 – $1200 | ASTM F67, Zr702 | Sweden, USA, Global |
EOS GmbH | Stainless Steel, Ti | $300 – $700 | 316L, Ti-6Al-4V | Germany, Global |
Aubert & Duval | Nickel, CoCr | $400 – $800 | Inconel 718, CoCrMo | France, Global |
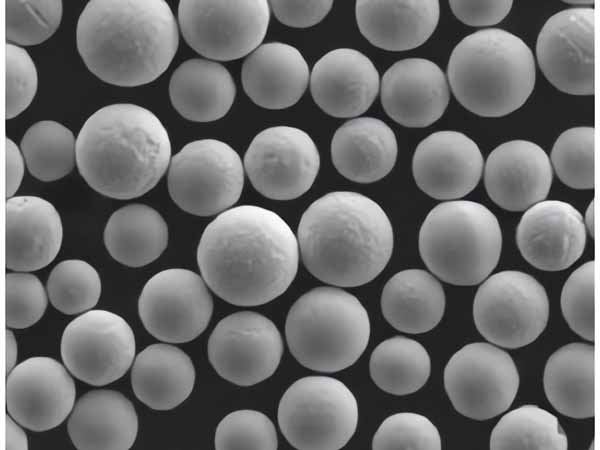
FAQs
Question | Answer |
---|---|
What metals can be used in REP? | A wide range of metals including Titanium, Nickel, Stainless Steel, Aluminum, Copper, Tantalum, and more. |
What industries benefit from REP? | Aerospace, biomedical, automotive, electronics, and energy sectors among others. |
How does REP compare to other methods? | REP generally offers better control over particle size and shape, resulting in higher quality powders, but it can be more costly. |
Are there any limitations? | The process can be complex and expensive, particularly for large-scale production, but the quality of the powders often justifies the cost. |
Conclusion
The rotating electrode process is a cutting-edge technology that plays a pivotal role in producing high-quality metal powders for a variety of industries. From aerospace to biomedical applications, the powders created through this process are renowned for their precision, purity, and performance. By understanding the intricacies of REP, including its advantages, limitations, and applications, you can make informed decisions that will benefit your projects.
Whether you’re an engineer looking to source the best materials, a manufacturer seeking to improve your production processes, or simply someone curious about the latest in material science, the rotating electrode process is a fascinating area of study that continues to evolve and influence modern technology.
Remember, choosing the right powder and supplier can make all the difference in the success of your application. Consider the specifications, weigh the pros and cons, and always look for reputable suppliers to ensure you get the best materials available.