Overview of Spherical Gas Atomized Alloy Powder
Spherical gas atomized alloy powders are an essential component in many advanced manufacturing processes. Their unique properties make them ideal for various applications, including additive manufacturing, metal injection molding (MIM), and thermal spraying. But what exactly makes these powders so special? How do they compare to other types of metal powders? And why should you consider using them in your next project?
In this article, we’ll dive deep into the world of spherical gas atomized alloy powders, exploring their composition, characteristics, and the specific models available. We’ll also look at their applications, specifications, suppliers, and prices. Whether you’re new to this topic or looking for detailed insights, this guide will provide you with everything you need to know.
What is Spherical Gas Atomized Alloy Powder?
Spherical gas atomized alloy powder is produced through a process known as gas atomization, where molten metal is dispersed into fine droplets using high-pressure gas streams. As these droplets cool and solidify, they form spherical particles. This method is favored for producing powders with uniform size distribution, high purity, and excellent flowability.
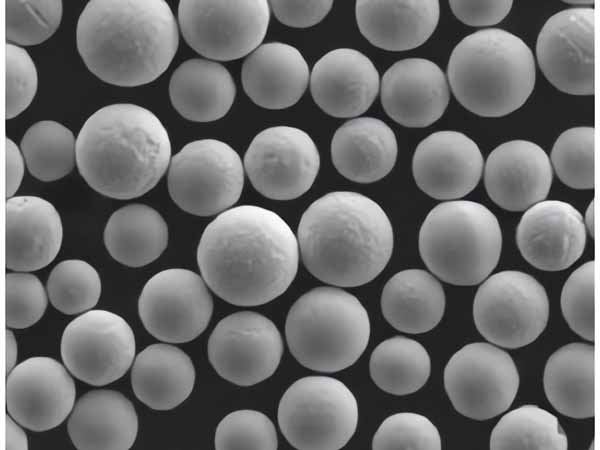
Key Characteristics of Spherical Gas Atomized Alloy Powder
Property | Description |
---|---|
Shape | Spherical |
Size Distribution | Uniform, typically within a narrow range |
Purity | High, with minimal contamination |
Flowability | Excellent, ideal for powder-based manufacturing processes |
Density | High relative density due to the spherical shape |
Surface Area | Lower surface area compared to irregularly shaped powders |
Oxidation Resistance | Enhanced due to reduced surface area and controlled environment production |
Application Flexibility | Suitable for a wide range of manufacturing techniques |
Why Choose Spherical Gas Atomized Alloy Powders?
When it comes to selecting metal powders for manufacturing, the decision can be daunting. The market offers a plethora of options, each with its own set of characteristics and advantages. However, spherical gas atomized alloy powders stand out for several reasons:
- Uniformity: The spherical shape ensures consistent flow and packing density, which is crucial for applications like 3D printing and MIM.
- Purity: The gas atomization process minimizes the risk of contamination, leading to powders with higher purity levels.
- Versatility: These powders can be used across various industries, including aerospace, automotive, and medical fields.
But it’s not just about the basics. Let’s dive into the specifics.
Composition of Spherical Gas Atomized Alloy Powder
The composition of spherical gas atomized alloy powders can vary depending on the intended application. Some common alloy powders include:
1. Ni-Based Alloys (Inconel 625)
- Composition: Nickel, Chromium, Molybdenum, Iron
- Description: Known for its excellent corrosion and oxidation resistance, Inconel 625 is often used in aerospace and marine applications.
- Characteristics: High-temperature strength, good weldability, and superb fatigue resistance.
2. Co-Cr-Mo Alloys
- Composition: Cobalt, Chromium, Molybdenum
- Description: These alloys are commonly used in medical implants due to their biocompatibility and wear resistance.
- Characteristics: High strength, corrosion resistance, and biocompatibility.
3. Ti-6Al-4V
- Composition: Titanium, Aluminum, Vanadium
- Description: Widely used in the aerospace industry, this alloy is known for its high strength-to-weight ratio.
- Characteristics: Excellent corrosion resistance, high strength, and low density.
4. Stainless Steel 316L
- Composition: Iron, Chromium, Nickel, Molybdenum
- Description: A popular choice for medical devices and food processing equipment due to its corrosion resistance and durability.
- Characteristics: High corrosion resistance, good mechanical properties, and weldability.
5. Al-Si10Mg
- Composition: Aluminum, Silicon, Magnesium
- Description: Commonly used in the automotive and aerospace industries, this alloy offers a good balance of strength and weight.
- Characteristics: Lightweight, good thermal conductivity, and excellent castability.
6. Maraging Steel
- Composition: Nickel, Cobalt, Molybdenum, Titanium
- Description: Known for its ultra-high strength and toughness, maraging steel is used in tooling and high-performance applications.
- Characteristics: High tensile strength, excellent toughness, and minimal distortion during heat treatment.
7. Bronze Alloys (Cu-Sn)
- Composition: Copper, Tin
- Description: Used in electrical contacts and bearings, bronze alloys offer good wear resistance and conductivity.
- Characteristics: Good machinability, wear resistance, and corrosion resistance.
8. Tool Steel (H13)
- Composition: Iron, Chromium, Molybdenum, Vanadium
- Description: This alloy is widely used in die casting and extrusion processes.
- Characteristics: High toughness, heat resistance, and wear resistance.
9. Nickel-Copper Alloys (Monel 400)
- Composition: Nickel, Copper
- Description: Monel 400 is highly resistant to corrosion, making it suitable for marine and chemical processing applications.
- Characteristics: Excellent corrosion resistance, good mechanical properties at elevated temperatures.
10. Aluminum Alloys (6061)
- Composition: Aluminum, Magnesium, Silicon
- Description: A versatile alloy used in automotive and aerospace industries for its combination of strength and corrosion resistance.
- Characteristics: Lightweight, good mechanical properties, and excellent corrosion resistance.
Common Spherical Gas Atomized Alloy Powders
Alloy Type | Composition | Applications | Key Characteristics |
---|---|---|---|
Inconel 625 | Ni, Cr, Mo, Fe | Aerospace, Marine | High corrosion resistance, high-temperature strength |
Co-Cr-Mo | Co, Cr, Mo | Medical Implants | Biocompatibility, wear resistance |
Ti-6Al-4V | Ti, Al, V | Aerospace | High strength-to-weight ratio, corrosion resistance |
Stainless Steel 316L | Fe, Cr, Ni, Mo | Medical Devices, Food Processing | Corrosion resistance, good mechanical properties |
Al-Si10Mg | Al, Si, Mg | Automotive, Aerospace | Lightweight, good thermal conductivity |
Maraging Steel | Ni, Co, Mo, Ti | Tooling, High-Performance Applications | Ultra-high strength, toughness |
Bronze (Cu-Sn) | Cu, Sn | Electrical Contacts, Bearings | Wear resistance, good conductivity |
Tool Steel (H13) | Fe, Cr, Mo, V | Die Casting, Extrusion | High toughness, heat resistance |
Monel 400 | Ni, Cu | Marine, Chemical Processing | Corrosion resistance, good at high temperatures |
Aluminum Alloy (6061) | Al, Mg, Si | Automotive, Aerospace | Lightweight, good mechanical properties |
-
CM247LC Powder | Nickel Alloy Powder
-
0# Pure Nickel powder
-
NiCoCrAlY alloys powders
-
Rene 142 alloy-Rene Powder
-
Haynes 25 Haynes Powder
-
Best Hastelloy C-22 Powder-High temperature alloy Powder for 3D Printing
-
Best Hastelloy C-276 Powder-High temperature alloy Powder for 3D Printing
-
Best Hastelloy N Powder-High temperature alloy Powder for 3D Printing
-
Best Hastelloy B Powder丨High temperature alloy Powder for 3D Printing
Characteristics of Spherical Gas Atomized Alloy Powder
When we talk about the characteristics of spherical gas atomized alloy powder, it’s essential to understand that these are not just ordinary metal powders. The process of gas atomization imparts several unique properties that make them stand out:
1. Particle Shape and Size Distribution
- Spherical Shape: The spherical shape of the particles results in better flowability and packing density. This is crucial for processes like additive manufacturing, where consistent layering is necessary.
- Uniform Size Distribution: These powders typically have a narrow size distribution, which ensures consistent performance in various applications.
2. Purity and Contamination Resistance
- High Purity: The gas atomization process occurs in a controlled environment, reducing the chances of contamination from external sources.
- Minimal Oxidation: Due to the reduced surface area compared to irregularly shaped powders, spherical gas atomized powders exhibit less oxidation, which can be a critical factor in high-performance applications.
3. Flowability
- Enhanced Flowability: The smooth, spherical shape of these powders allows them to flow more easily through equipment, making them ideal for processes like 3D printing, where consistent powder distribution is essential.
4. High Packing Density
- Improved Packing Density: Spherical powders pack more efficiently, leading to denser and stronger final products. This is particularly beneficial in metal injection molding and other powder metallurgy processes
.
5. Versatility Across Applications
- Wide Application Range: Due to their excellent properties, these powders can be used in various industries, from aerospace and automotive to medical and dental fields.
Characteristics of Spherical Gas Atomized Alloy Powders
Characteristic | Benefit |
---|---|
Spherical Shape | Improved flowability, better packing density |
Uniform Size Distribution | Consistent performance in manufacturing processes |
High Purity | Reduced contamination, better material properties |
Minimal Oxidation | Enhanced durability and performance in high-temperature applications |
Enhanced Flowability | Suitable for 3D printing and other powder-based processes |
High Packing Density | Stronger and denser final products |
Versatility | Applicable across various industries |
Applications of Spherical Gas Atomized Alloy Powder
The unique properties of spherical gas atomized alloy powders open up a wide range of applications. Let’s explore some of the most common uses:
1. Additive Manufacturing (3D Printing)
- Why It Works: The consistent size distribution and excellent flowability of spherical powders make them perfect for additive manufacturing. Whether you’re printing intricate aerospace components or custom medical implants, these powders deliver the precision and reliability needed for high-performance parts.
- Common Alloys: Ti-6Al-4V, Inconel 625, Stainless Steel 316L.
2. Metal Injection Molding (MIM)
- Why It Works: MIM requires powders that can be packed densely and uniformly into molds. The high packing density of spherical gas atomized powders ensures that the final product is strong and defect-free.
- Common Alloys: Maraging Steel, Stainless Steel 316L, Tool Steel (H13).
3. Thermal Spraying
- Why It Works: For coating applications, powders need to have excellent flowability and minimal oxidation. Spherical gas atomized powders meet these requirements, providing high-quality coatings for wear resistance and thermal barriers.
- Common Alloys: Ni-Based Alloys, Co-Cr-Mo Alloys.
4. Hot Isostatic Pressing (HIP)
- Why It Works: HIP involves compressing powders at high temperatures and pressures to create dense, fully dense materials. The uniform shape and size distribution of spherical powders ensure consistent compaction and sintering, leading to superior material properties.
- Common Alloys: Inconel 625, Ti-6Al-4V.
5. Brazing
- Why It Works: Spherical powders are ideal for brazing applications due to their excellent flowability and high purity. They allow for precise control over the brazing process, resulting in strong, reliable joints.
- Common Alloys: Bronze, Nickel-Copper Alloys.
Applications of Spherical Gas Atomized Alloy Powders
Application | Why It’s Suitable | Common Alloys |
---|---|---|
Additive Manufacturing | Consistent size, excellent flowability | Ti-6Al-4V, Inconel 625, Stainless Steel 316L |
Metal Injection Molding | High packing density, uniform shape | Maraging Steel, Stainless Steel 316L, Tool Steel |
Thermal Spraying | Good flowability, minimal oxidation | Ni-Based Alloys, Co-Cr-Mo Alloys |
Hot Isostatic Pressing | Uniform compaction, superior material properties | Inconel 625, Ti-6Al-4V |
Brazing | Precise control, strong joints | Bronze, Nickel-Copper Alloys |
Specifications, Sizes, Grades, and Standards
When selecting spherical gas atomized alloy powders, it’s essential to consider the specifications, sizes, and grades that meet your application needs. Here’s a detailed look at what you should be aware of:
1. Particle Size Distribution
- Range: Spherical gas atomized powders are available in various particle size distributions, typically ranging from 10 to 150 microns, depending on the application.
- Selection: Smaller particle sizes (10-45 microns) are ideal for additive manufacturing, while larger sizes (45-150 microns) are often used in thermal spraying and MIM.
2. Purity Levels
- Range: Purity levels can vary, with most powders boasting purity levels of 99.9% or higher. Some applications may require lower impurity levels, particularly for medical and aerospace applications.
- Selection: Choose powders with the appropriate purity level based on the criticality of the application.
3. Grades and Standards
- Grades: Spherical gas atomized powders are available in various grades, such as aerospace-grade, medical-grade, and industrial-grade. Each grade is tailored to meet specific industry standards.
- Standards: Compliance with international standards like ASTM, ISO, and AMS ensures the reliability and consistency of the powders.
Specifications, Sizes, Grades, and Standards of Spherical Gas Atomized Alloy Powders
Specification | Description |
---|---|
Particle Size Distribution | 10-150 microns, depending on the application |
Purity Levels | 99.9% or higher, with low impurity levels |
Grades | Aerospace-grade, medical-grade, industrial-grade |
Standards | ASTM, ISO, AMS, ensuring quality and consistency |
Suppliers and Pricing Details
When sourcing spherical gas atomized alloy powders, it’s crucial to consider the supplier’s reputation, product quality, and pricing. Here’s a look at some key suppliers and their offerings:
1. Carpenter Technology
- Products: Specializes in high-performance alloys like Ti-6Al-4V, Inconel 625, and Maraging Steel.
- Pricing: Prices vary based on the alloy and quantity, typically ranging from $50 to $200 per kilogram.
2. Praxair Surface Technologies
- Products: Offers a wide range of spherical powders, including Ni-based alloys, stainless steels, and aluminum alloys.
- Pricing: Competitive pricing, generally between $40 and $150 per kilogram, depending on the alloy.
3. Sandvik Osprey
- Products: Known for high-quality powders, including Co-Cr-Mo alloys, tool steels, and bronze alloys.
- Pricing: Premium pricing, often in the range of $60 to $250 per kilogram, reflecting the high quality and precision of their products.
4. Höganäs AB
- Products: Offers a diverse portfolio of powders, including iron-based alloys, aluminum alloys, and nickel-copper alloys.
- Pricing: Prices range from $30 to $180 per kilogram, depending on the alloy and application.
Suppliers and Pricing of Spherical Gas Atomized Alloy Powders
Supplier | Product Range | Pricing (per kg) |
---|---|---|
Carpenter Technology | Ti-6Al-4V, Inconel 625, Maraging Steel | $50 – $200 |
Praxair Surface Technologies | Ni-Based Alloys, Stainless Steels, Aluminum Alloys | $40 – $150 |
Sandvik Osprey | Co-Cr-Mo Alloys, Tool Steels, Bronze Alloys | $60 – $250 |
Höganäs AB | Iron-Based Alloys, Aluminum Alloys, Nickel-Copper Alloys | $30 – $180 |
Comparing Pros and Cons: Advantages and Limitations
While spherical gas atomized alloy powders offer numerous benefits, it’s essential to weigh these against their limitations to determine if they’re the right fit for your application.
Advantages
- High Purity: The controlled gas atomization process ensures minimal contamination, leading to high-purity powders.
- Excellent Flowability: The spherical shape of the particles allows for better flowability, which is crucial for processes like 3D printing and MIM.
- Uniform Size Distribution: This leads to consistent performance across various applications, reducing the risk of defects.
Limitations
- Cost: Spherical gas atomized powders can be more expensive than other types of metal powders due to the complexity of the production process.
- Availability: While these powders are widely available, some specialized alloys may have longer lead times or limited suppliers.
- Oxidation Sensitivity: Despite their reduced surface area, these powders can still be sensitive to oxidation, particularly in high-temperature environments.
Advantages and Limitations of Spherical Gas Atomized Alloy Powders
Advantages | Limitations |
---|---|
High Purity | Higher cost due to production complexity |
Excellent Flowability | Availability of specialized alloys may be limited |
Uniform Size Distribution | Oxidation sensitivity in high-temperature environments |
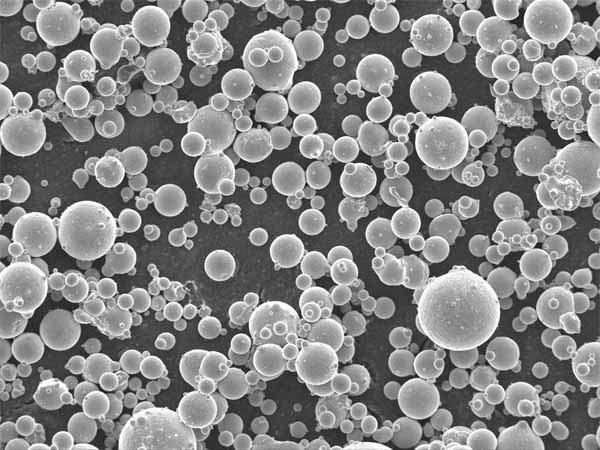
FAQs
What are spherical gas atomized alloy powders used for?
Spherical gas atomized alloy powders are used in various applications, including additive manufacturing, metal injection molding, thermal spraying, hot isostatic pressing, and brazing. Their unique properties make them ideal for high-performance applications in industries like aerospace, automotive, and medical.
What are the advantages of using spherical gas atomized powders over other metal powders?
The primary advantages include high purity, excellent flowability, and uniform size distribution. These factors contribute to better performance in manufacturing processes, resulting in stronger and more reliable final products.
How do I choose the right spherical gas atomized alloy powder for my application?
Consider factors such as particle size distribution, purity levels, and the specific alloy composition that best suits your application. Additionally, ensure that the powder complies with relevant industry standards and is sourced from a reputable supplier.
What is the typical cost of spherical gas atomized alloy powders?
Prices can vary widely depending on the alloy, supplier, and quantity. Typically, these powders range from $30 to $250 per kilogram.
How do spherical gas atomized powders compare to water atomized powders?
Spherical gas atomized powders generally offer better flowability and higher purity than water atomized powders. However, they can be more expensive due to the complexity of the gas atomization process.
Conclusion
Spherical gas atomized alloy powders represent a pinnacle of precision and performance in the world of metal powders. Their unique characteristics make them indispensable for a wide range of advanced manufacturing processes, from additive manufacturing to brazing. While they come at a higher cost, the benefits in terms of purity, flowability, and consistency often justify the investment.
Whether you’re in aerospace, automotive, or any industry requiring high-performance materials, understanding the ins and outs of these powders will help you make informed decisions for your projects. Remember, selecting the right powder isn’t just about picking an alloy—it’s about choosing a product that aligns with your specific needs, ensuring the best possible outcome for your application.
Feel free to reach out to suppliers, compare options, and explore the possibilities that spherical gas atomized alloy powders can offer. The future of manufacturing is precise, powerful, and powder-based—make sure you’re a part of it.