Overview of Spheroidising Powder
Spheroidising powder, a crucial element in metalworking and additive manufacturing, refers to metal powders processed to have a spherical shape. These powders are utilized extensively in industries like aerospace, automotive, and medical devices due to their excellent flowability, packing density, and uniformity. The process of spheroidisation enhances the physical and mechanical properties of the powder, making it highly suitable for precision applications.
In this comprehensive guide, we’ll dive into the details of spheroidising powder, exploring its types, composition, properties, applications, specifications, suppliers, and more. Whether you’re an engineer, a researcher, or just curious about this fascinating material, this guide will provide you with valuable insights.
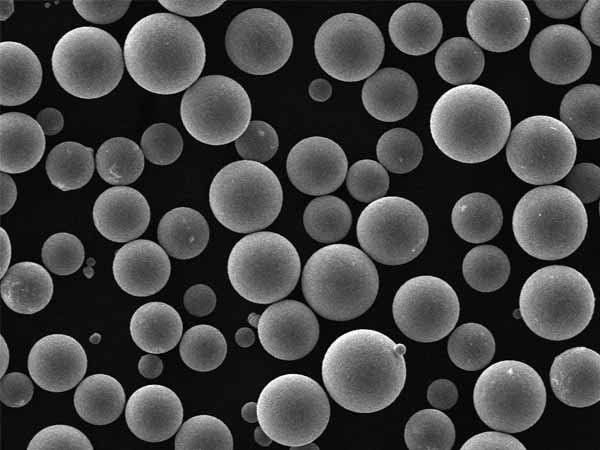
Types of Spheroidising Powder
Let’s start by looking at various types of spheroidising powders. Different metals and alloys are used for creating spheroidised powders, each with unique properties and applications.
Type | Composition | Properties | Applications |
---|---|---|---|
Titanium Alloy Powder | Ti-6Al-4V | High strength, corrosion resistance | Aerospace, medical implants |
Stainless Steel Powder | 316L | Excellent corrosion resistance, strength | Biomedical, food processing equipment |
Aluminum Alloy Powder | AlSi10Mg | Lightweight, good thermal properties | Automotive, aerospace |
Nickel Alloy Powder | Inconel 718 | High temperature resistance, strength | Aerospace, power generation |
Copper Powder | Pure Cu | Excellent conductivity | Electronics, heat exchangers |
Cobalt-Chrome Alloy Powder | CoCrMo | Wear resistance, biocompatibility | Medical implants, dental devices |
Tungsten Carbide Powder | WC-Co | High hardness, wear resistance | Cutting tools, mining |
Iron Powder | Fe | Good mechanical properties, cost-effective | Automotive parts, powder metallurgy |
Bronze Powder | Cu-Sn | Good corrosion resistance, machinability | Bearings, bushings |
Magnesium Alloy Powder | AZ91D | Lightweight, good strength-to-weight ratio | Automotive, aerospace |
Detailed Descriptions of Metal Powder Models
- Titanium Alloy Powder (Ti-6Al-4V)
- Composition: 90% Titanium, 6% Aluminum, 4% Vanadium
- Properties: High strength-to-weight ratio, excellent corrosion resistance, biocompatibility.
- Applications: Primarily used in aerospace for structural components and medical implants like hip joints and dental implants due to its excellent biocompatibility and strength.
- Stainless Steel Powder (316L)
- Composition: Iron with 16-18% Chromium, 10-14% Nickel, 2-3% Molybdenum
- Properties: Superior corrosion resistance, high strength, excellent formability.
- Applications: Widely used in biomedical devices, food processing equipment, and marine applications.
- Aluminum Alloy Powder (AlSi10Mg)
- Composition: 90% Aluminum, 10% Silicon, 0.1% Magnesium
- Properties: Lightweight, good thermal and electrical conductivity, excellent machinability.
- Applications: Ideal for lightweight structures in automotive and aerospace industries, as well as for complex geometries in 3D printing.
- Nickel Alloy Powder (Inconel 718)
- Composition: 50-55% Nickel, 17-21% Chromium, 4.75-5.5% Niobium, 2.8-3.3% Molybdenum
- Properties: Exceptional high-temperature strength, corrosion and oxidation resistance.
- Applications: Used in high-stress applications such as turbine blades, rocket engines, and nuclear reactors.
- Copper Powder (Pure Cu)
- Composition: 99.9% Copper
- Properties: Excellent electrical and thermal conductivity, good ductility.
- Applications: Used in electrical and electronic components, heat exchangers, and as a conductive material in various applications.
- Cobalt-Chrome Alloy Powder (CoCrMo)
- Composition: 60-65% Cobalt, 26-30% Chromium, 5-7% Molybdenum
- Properties: High wear resistance, biocompatibility, good mechanical properties.
- Applications: Predominantly used in medical implants such as knee and hip replacements, and dental prosthetics due to its excellent wear resistance and biocompatibility.
- Tungsten Carbide Powder (WC-Co)
- Composition: Tungsten carbide particles bonded with Cobalt
- Properties: Extremely hard, high wear resistance, high melting point.
- Applications: Ideal for cutting tools, mining equipment, and wear-resistant applications.
- Iron Powder (Fe)
- Composition: Pure Iron or iron with small amounts of carbon or other elements.
- Properties: Good mechanical properties, cost-effective.
- Applications: Widely used in automotive parts, magnetic materials, and powder metallurgy.
- Bronze Powder (Cu-Sn)
- Composition: Copper with 10-12% Tin
- Properties: Good corrosion resistance, excellent machinability, good wear resistance.
- Applications: Commonly used for bearings, bushings, and other components requiring good frictional properties.
- Magnesium Alloy Powder (AZ91D)
- Composition: 90% Magnesium, 9% Aluminum, 1% Zinc
- Properties: Extremely lightweight, good strength-to-weight ratio, good corrosion resistance.
- Applications: Ideal for lightweight structural components in automotive and aerospace industries.
Composition of Spheroidising Powder
The composition of spheroidising powder varies depending on the metal or alloy used. Here’s a table summarizing the typical composition of different spheroidising powders:
Metal Powder | Composition |
---|---|
Titanium Alloy (Ti-6Al-4V) | Ti (90%), Al (6%), V (4%) |
Stainless Steel (316L) | Fe, Cr (16-18%), Ni (10-14%), Mo (2-3%) |
Aluminum Alloy (AlSi10Mg) | Al (90%), Si (10%), Mg (0.1%) |
Nickel Alloy (Inconel 718) | Ni (50-55%), Cr (17-21%), Nb (4.75-5.5%), Mo (2.8-3.3%) |
Copper (Pure Cu) | Cu (99.9%) |
Cobalt-Chrome Alloy (CoCrMo) | Co (60-65%), Cr (26-30%), Mo (5-7%) |
Tungsten Carbide (WC-Co) | WC, Co |
Iron (Fe) | Pure Fe or Fe with small amounts of C or other elements |
Bronze (Cu-Sn) | Cu, Sn (10-12%) |
Magnesium Alloy (AZ91D) | Mg (90%), Al (9%), Zn (1%) |
Characteristics of Spheroidising Powder
The unique characteristics of spheroidising powders make them highly desirable for various applications. Here’s a detailed look at their key properties:
Characteristic | Description |
---|---|
Flowability | Spherical powders have excellent flow properties, making them suitable for additive manufacturing and powder metallurgy. |
Packing Density | High packing density ensures uniform distribution and minimal voids in the final product. |
Purity | High purity levels are essential for achieving desired mechanical properties and preventing contamination. |
Particle Size Distribution | Consistent particle size distribution improves process reliability and product quality. |
Surface Area | Lower surface area compared to irregularly shaped powders, reducing oxidation and improving performance. |
Mechanical Properties | Enhanced mechanical properties like strength, hardness, and wear resistance. |
Thermal Conductivity | Good thermal conductivity is essential for applications requiring heat dissipation. |
Electrical Conductivity | High electrical conductivity for applications in electronics and electrical components. |
Applications of Spheroidising Powder
Spheroidising powders are used in a wide range of industries due to their superior properties. Here are some common applications:
Industry | Applications |
---|---|
Aerospace | Structural components, turbine blades, rocket engines |
Automotive | Lightweight components, engine parts, gears |
Medical | Implants (hip, knee, dental), surgical instruments |
Electronics | Conductive materials, connectors, heat sinks |
Manufacturing | Additive manufacturing, powder metallurgy, coating applications |
Mining | Cutting tools, wear-resistant parts |
Marine | Corrosion-resistant components, propellers |
Energy | Power generation, nuclear reactors, heat exchangers |
Specifications, Sizes, Grades, Standards
When selecting spheroidising powders, it’s essential to consider the specifications, sizes, grades, and standards to ensure compatibility with your application. Here’s a table summarizing these parameters:
Metal Powder | Specifications | Sizes | Grades | Standards |
---|---|---|---|---|
Titanium Alloy (Ti-6Al-4V) | ASTM B348, AMS 4928 | 15-45µm, 45-90µm | Grade 5 | ISO 5832-3 |
Stainless Steel (316L) | ASTM A276, AMS 5648 | 10-45µm, 45-90µm | 316L | ASTM F138 |
Aluminum Alloy (AlSi10Mg) | AMS 4026, ASTM B209 | 20-63µm, 45-90µm | AlSi10Mg | ISO 3522 |
Nickel Alloy (Inconel 718) | ASTM B637, AMS 5662 | 15-45µm, 45-90µm | Inconel 718 | ISO 6208 |
Copper (Pure Cu) | ASTM B170, AMS 4500 | 10-45µm, 45-90µm | Pure Cu | ASTM B216 |
Cobalt-Chrome Alloy (CoCrMo) | ASTM F75, ISO 5832-4 | 10-45µm, 45-90µm | CoCrMo | ISO 5832-4 |
Tungsten Carbide (WC-Co) | ASTM B777, AMS 7870 | 15-45µm, 45-90µm | WC-Co | ISO 4499 |
Iron (Fe) | ASTM B212, AMS 5508 | 20-63µm, 45-90µm | Pure Fe | ASTM A131 |
Bronze (Cu-Sn) | ASTM B427, AMS 4730 | 10-45µm, 45-90µm | Cu-Sn | ASTM B505 |
Magnesium Alloy (AZ91D) | ASTM B403, AMS 4377 | 15-45µm, 45-90µm | AZ91D | ISO 16220 |
Suppliers and Pricing Details
Finding the right supplier for spheroidising powder is crucial for ensuring quality and cost-effectiveness. Here’s a list of some prominent suppliers and their pricing details:
Supplier | Metal Powder | Price per Kg (USD) | Location |
---|---|---|---|
Höganäs AB | Stainless Steel (316L), Iron (Fe) | $50 – $100 | Sweden |
Sandvik Osprey | Titanium Alloy (Ti-6Al-4V), Nickel Alloy (Inconel 718) | $150 – $300 | UK |
LPW Technology | Aluminum Alloy (AlSi10Mg), Cobalt-Chrome Alloy (CoCrMo) | $100 – $250 | USA |
Carpenter Additive | Copper (Pure Cu), Bronze (Cu-Sn) | $75 – $200 | USA |
GKN Additive | Tungsten Carbide (WC-Co), Magnesium Alloy (AZ91D) | $200 – $400 | Germany |
Praxair Surface Technologies | Titanium Alloy (Ti-6Al-4V), Nickel Alloy (Inconel 718) | $180 – $350 | USA |
AP&C (GE Additive) | Stainless Steel (316L), Aluminum Alloy (AlSi10Mg) | $90 – $180 | Canada |
Arcam AB | Cobalt-Chrome Alloy (CoCrMo), Iron (Fe) | $120 – $220 | Sweden |
AMETEK Specialty Metal Products | Bronze (Cu-Sn), Tungsten Carbide (WC-Co) | $110 – $250 | USA |
Tekna | Copper (Pure Cu), Magnesium Alloy (AZ91D) | $80 – $180 | Canada |
Comparing Pros and Cons of Spheroidising Powder
When choosing spheroidising powder, it’s essential to weigh the pros and cons of different options. Here’s a comparative table to help you make an informed decision:
Metal Powder | Advantages | Limitations |
---|---|---|
Titanium Alloy (Ti-6Al-4V) | High strength, lightweight, corrosion-resistant, biocompatible | High cost, difficult to machine |
Stainless Steel (316L) | Excellent corrosion resistance, strength, cost-effective | Lower thermal conductivity compared to other metals |
Aluminum Alloy (AlSi10Mg) | Lightweight, good thermal properties, easily machinable | Lower strength compared to titanium alloys |
Nickel Alloy (Inconel 718) | High temperature resistance, strength, corrosion-resistant | Expensive, difficult to machine |
Copper (Pure Cu) | Excellent conductivity, good ductility | Prone to oxidation, relatively soft |
Cobalt-Chrome Alloy (CoCrMo) | Wear resistance, biocompatible, high strength | High cost, difficult to machine |
Tungsten Carbide (WC-Co) | Extremely hard, wear-resistant, high melting point | Brittle, expensive |
Iron (Fe) | Good mechanical properties, cost-effective | Prone to rust, lower corrosion resistance |
Bronze (Cu-Sn) | Good corrosion resistance, machinability | Moderate strength, heavier than aluminum |
Magnesium Alloy (AZ91D) | Extremely lightweight, good strength-to-weight ratio | Prone to corrosion, flammable |
Comparative Analysis of Spheroidising Powder Properties
Property | Titanium Alloy (Ti-6Al-4V) | Stainless Steel (316L) | Aluminum Alloy (AlSi10Mg) | Nickel Alloy (Inconel 718) |
---|---|---|---|---|
Density (g/cm³) | 4.43 | 7.99 | 2.70 | 8.19 |
Melting Point (°C) | 1660-1670 | 1371 | 660 | 1336-1346 |
Ultimate Tensile Strength (MPa) | 895-930 | 485-620 | 300-350 | 965-1035 |
Yield Strength (MPa) | 825-870 | 170-310 | 170-200 | 720-850 |
Hardness (HV) | 349-400 | 160-190 | 70-100 | 330-370 |
Thermal Conductivity (W/mK) | 6.7 | 16.2 | 167 | 11.4 |
Electrical Conductivity (% IACS) | 3 | 2-4 | 34-36 | 1.3 |
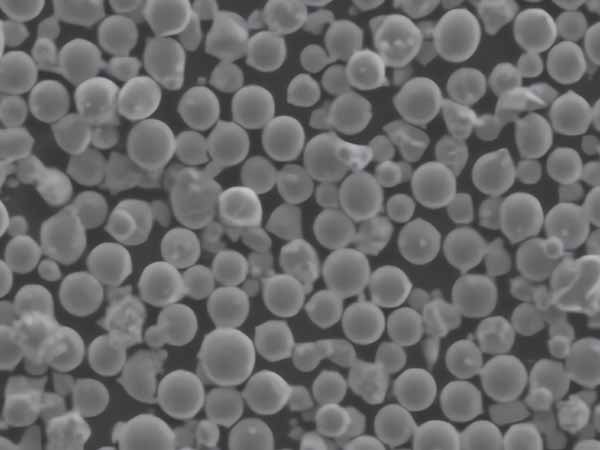
FAQ
Here are some frequently asked questions about spheroidising powder:
Question | Answer |
---|---|
What is spheroidising powder? | Spheroidising powder is metal powder processed to have a spherical shape, enhancing its flowability, packing density, and mechanical properties. |
Why is spheroidising powder important in additive manufacturing? | Its spherical shape ensures uniform layer deposition, reducing defects and improving the quality of 3D printed parts. |
What are the common applications of spheroidising powder? | Applications include aerospace components, medical implants, automotive parts, electronic devices, and cutting tools. |
How is the spheroidisation process carried out? | Common methods include gas atomization, plasma atomization, and centrifugal atomization, where molten metal is sprayed and solidified into spherical particles. |
What factors should be considered when selecting spheroidising powder? | Consider the powder’s composition, particle size distribution, flowability, purity, and compatibility with the intended application. |
Can spheroidising powders be recycled? | Yes, many spheroidising powders can be recycled, but it depends on the specific material and the extent of contamination or oxidation. |
What are the challenges in using spheroidising powder? | Challenges include high cost, difficulty in machining certain metals, and the need for precise handling to avoid contamination. |
How does particle size affect the properties of spheroidising powder? | Smaller particles provide better surface finish and detail resolution but can be more prone to oxidation, while larger particles enhance flowability but may reduce detail precision. |
Conclusion
Spheroidising powder is a cornerstone in modern manufacturing and engineering, offering unparalleled benefits in terms of mechanical properties, process efficiency, and product quality. Whether used in aerospace, medical devices, or automotive components, these powders bring significant advantages that drive innovation and performance. By understanding the types, properties, applications, and selection criteria of spheroidising powders, manufacturers can make informed decisions to optimize their production processes and achieve superior results.