Overview of Stainless Steel 316L Powder
Stainless steel 316L powder refers to fine particulate material composed of an austenitic stainless steel alloy. It exhibits high strength, excellent corrosion resistance, and ease of fabrication. 316L powder is widely used in additive manufacturing, alloy blends, and surface coatings across industries.
Key characteristics of Stainless Steel 316L powder:
- Alloy composition – Fe/Cr/Ni/Mo optimized for corrosion resistance
- Particles sizes – Ranging from microns to nanometers
- High purity and spherical morphology ideal for AM
- Melting point 1400-1450°C
- Density approximately 7.9 g/cc
- Manufactured via gas atomization or other specialty processes
- Conforms to ASTM and other global material specifications
Let’s explore the composition, properties, applications and supply details of 316L powder.
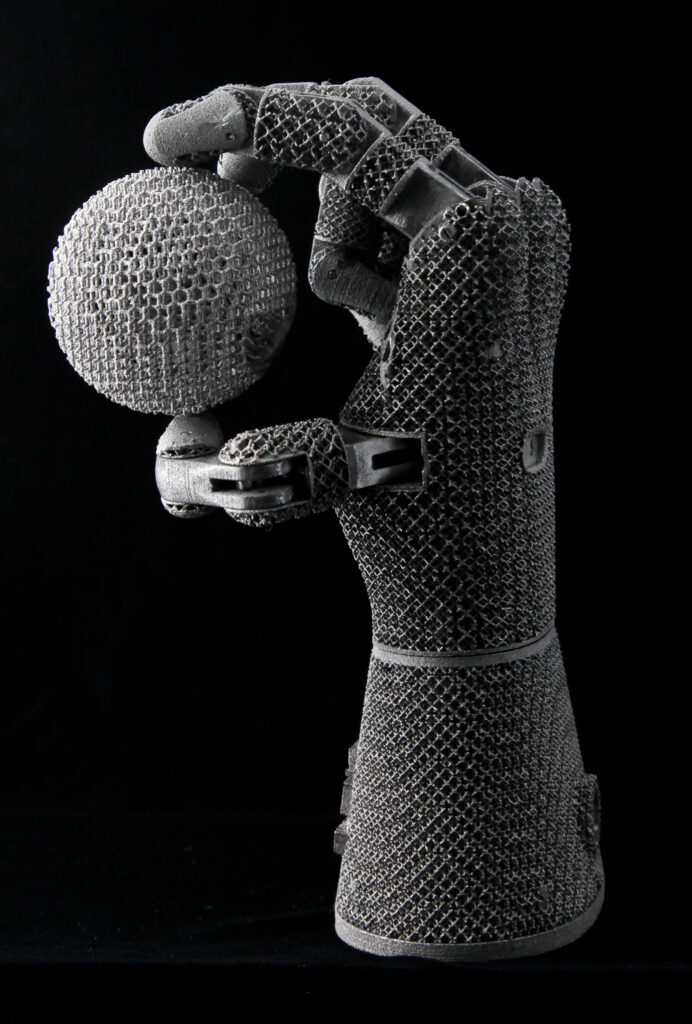
Composition
The composition of stainless steel 316L powder is:
Element | Weight % | Role |
---|---|---|
Iron (Fe) | Balance | Base metal |
Chromium (Cr) | 16-18% | Corrosion resistance |
Nickel (Ni) | 10-14% | Austenite stabilizer |
Molybdenum (Mo) | 2-3% | Pitting/crevice corrosion resistance |
Manganese (Mn) | <2% | Deoxidizer |
Silicon (Si) | <1% | Deoxidizer |
Carbon (C) | <0.03% | Austenite stabilizer |
Nitrogen (N) | 0.1% | Austenite stabilizer |
Phosphorus (P) | <0.045% | Impurity |
Sulfur (S) | <0.03% | Impurity |
Table 1: 316L stainless steel powder composition
The low carbon variant 316L powder achieves optimal corrosion resistance and ductility. The nickel stabilizes the desired austenite microstructure. These alloys conform to national and international specifications for composition and powder quality.
Properties of Stainless Steel 316L Powder
Stainless steel 316L powder offers an exceptional combination of high strength and corrosion resistance:
Property | Description |
---|---|
Strength | Yield strength > 300 MPa, tensile strength > 550 MPa, can be significantly increased with finer grain sizes |
Hardness | Typical Vickers hardness approximately 190 HV |
Corrosion Resistance | Excellent due to Cr-Ni-Mo composition, suitable for harsh environments |
Wear Resistance | Very high erosion-corrosion resistance |
High Temperature Resistance | Can perform up to approx. 800°C for continuous use in air |
Cryogenic Performance | Retains ductility and fracture toughness at -196°C |
Table 2: Overview of mechanical and physical properties exhibited by stainless steel 316L powders
These properties make 316L highly valued for demanding applications across energy, transportation, chemical processing, food manufacturing and more.
Powder Characteristics
Stainless steel 316L powder is commercially available with different particle characteristics:
Parameter | Range |
---|---|
Particle size | 1 micron to 150 microns |
Particle shape | Spherical, irregular |
Size distribution | Tight distributions or broad |
Production method | Gas atomized, water atomized, plasma atomized |
Purity | From 98% to 99.9% |
Surface chemistry | Bare alloy, with flow agents etc. |
Table 3: Variability in 316L powder morphology, dimensions and composition
Gas atomized powders show the most ideal properties for additive manufacturing with spherical particles, tight size distribution, and very high purity. Other forms serve for conventional powder processing.
Applications
Common applications taking advantage of stainless steel 316L powder’s strengths:
Industry | Application | Benefits |
---|---|---|
Aerospace | Thrust chambers, turbine blades | High strength-to-weight ratio |
Automotive | Valve components | Corrosion resistance, high hardness |
Chemical | Process equipment | Withstand corrosion |
Oil and gas | Downhole tools, wellheads | Strength and wear resistance |
Medical | Implants, surgical instruments | Biocompatibility |
Marine | Propellers, pumps | Resist seawater corrosion |
Food processing | Components, vessels | Avoid contamination |
Table 4: Overview of industries using 316L powder for additive and powder metallurgy applications
In additive manufacturing, 316L facilitates complex, high-performance metal parts serving highly demanding environments. The flexibility of AM enables custom food-grade components and biomedical devices.
-
CM247LC Powder | Nickel Alloy Powder
-
0# Pure Nickel powder
-
NiCoCrAlY alloys powders
-
Rene 142 alloy-Rene Powder
-
Haynes 25 Haynes Powder
-
Best Hastelloy C-22 Powder-High temperature alloy Powder for 3D Printing
-
Best Hastelloy C-276 Powder-High temperature alloy Powder for 3D Printing
-
Best Hastelloy N Powder-High temperature alloy Powder for 3D Printing
-
Best Hastelloy B Powder丨High temperature alloy Powder for 3D Printing
Specifications of Stainless Steel 316L Powder
Stainles steel 316L powder compositions and quality adhere to various standard specifications:
Standard | Description |
---|---|
ASTM A240 | Standard specification for chromium and chromium-nickel stainless steel plate, sheet, and strip for pressure vessels and general applications |
ASTM B817 | Standard specification for powder metallurgy (PM) stainless steel processes |
AMS 5643 | Composition requirements for additive manufacturing of 316L powder |
ISO 9001 | Quality management for production of metallic materials including atomized powders |
Table 5: Industry standards applicable to 316L stainless steel powders
Reputable manufacturers test every powder lot to guarantee compliance with chemistry, particle size distribution and other quality benchmarks.
Suppliers and Pricing
A selection of available stainless steel 316L powder suppliers and pricing:
Supplier | Pricing |
---|---|
LPW Technology | $46+ per kg |
Sandvik Osprey | $56+ per kg |
Carpenter Additive | $65+ per kg |
Praxair | $75+ per kg |
Höganäs | $60+ per kg |
AMG Analytical | $1500+ per kg |
Table 6: Sample 316L powder suppliers and indicative prices
Prices range widely from $50 to $1500+ per kg depending on purity, powder morphology, buyer volumes and additional user testing services. Research to find the ideal balance of cost and powder consistency.
Advantages vs. Solid 316L
Parameter | Powder | Solid |
---|---|---|
Manufacturability | More complex geometries viable through AM vs subtractive machining | Limited by tool accessibility constraints |
Mechanical Properties | Finer microstructures boost yield and tensile strength | Depends on primary mill/melt processes |
Grain Structure | Very fine, directional grains from rapid solidification | Comparatively coarser grains |
Surface Finish | Smoother as-printed surface in some AM processes requiring less post-processing | Secondary machining required to improve surface roughness |
Buy-to-fly ratio | Near 100% utilisation of purchased material | Significant scrap losses from machining |
Supply Chain | Reduced lead time with digital distribution of printable files vs metal product shipping | Extended global supply chains for solid forms like bar, plate etc. |
Table 7: Comparison of 316L powder vs. wrought stainless steel
Additive manufacturing using 316L powder facilitates complex, high-performance parts otherwise unmakeable through conventional subtractive techniques. Lead times, buy-to-fly ratios and mechanicals often favor powder approaches.
Limitations vs. Alternatives
Parameter | 316L Powder | Alternatives (17-4PH, Inconel 718 etc.) |
---|---|---|
Max Service Temperature | Approx. 800°C | Over 1000°C possible |
Hardness | Up to ~340 HV | 500 HV achievable |
Corrosion Resistance | Excellent overall | Application-specific alloys offer better resistance in some chemical exposures |
Cost | $50 to $100 per kg | Certain alloys 2X-5X times more expensive |
Table 8: 316L powder limitations against high-performance aerospace/energy alternatives
For the most extreme environments, alternatives like precipitation-hardening or nickel alloys hold performance advantages despite steeply higher costs. 316L makes an affordable, versatile choice balancing capabilities and budget constraints across industries.
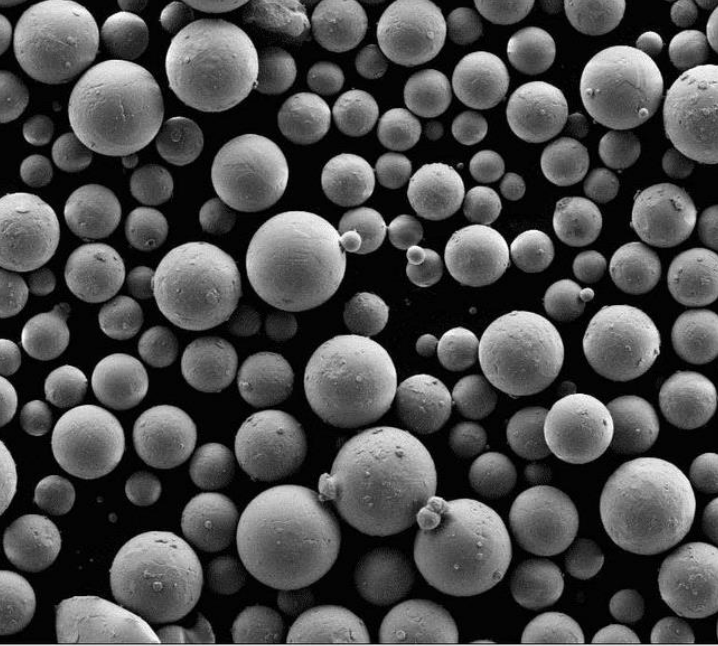
FAQ
Q: What particle size 316L powder is optimal for additive manufacturing?
A: 10-45 microns exhibits easiest flow and highest packing density suited to AM requirements. Finer particles improve finished part density and mechanicals but have more difficult handling characteristics. Evaluate based on printer capabilities and application needs.
Q: Does 316L powder require special storage precautions?
A: Inert gas sealing and climate-controlled humidity below 30% RH helps preserve flowability and minimize oxidation. Periodic rejuvenation cycles may help powders used over extended durations.
Q: What post-processing steps are recommended on 316L AM parts?
A: Hot isostatic pressing (HIP) helps eliminate internal voids and further improves material properties. Stress relieving, machining, surface finishing, coating, or other secondary operations may also apply depending on service conditions and design intent.
Q: Is stainless steel 316L suitable for food/medical applications?
A: Yes, 316L conforms to ASTM A240 for high temperature and general corrosive environments making it an economical choice for food, medical, pharmaceutical and other critical process applications needing stainless. Validate cleaning and sterilization processes for regulatory compliance.
Q: Does 316L powder contain known carcinogens or hazardous substances?
A: No, 316L does not contain reportable levels of Nickel, Chromium VI or Cadmium compounds above regulated thresholds for commercial, medical or food products. Ensure an up-to-date Safety Data Sheet from the manufacturer is available. Handle any fine metallic powders using dust collection, PPE protocols etc. to mitigate risks.