Stainless steel OP431 is a precipitation hardening martensitic grade providing a unique combination of high strength, toughness and corrosion resistance. OP431 powder is used primarily for additive manufacturing, surface engineering applications and spray and fuse coatings across demanding industries.
Overview of Stainless Steel OP431 Powder
Key properties that make stainless steel OP431 suitable for laser powder bed fusion include:
- Exceptional tensile strength from a tempered martensitic structure
- High hardness level up to 50 HRC when peak aged
- Excellent corrosion resistance comparable to 304/316 grades
- Good dimensional stability across operating temperature range
- Low magnetism facilitates post-processing and inspection
- Flowability and spreadability optimized for AM build consistency
OP431 delivers both high mechanical performance as well as corrosion resistance at levels unattainable with conventional stainless steel alloys.
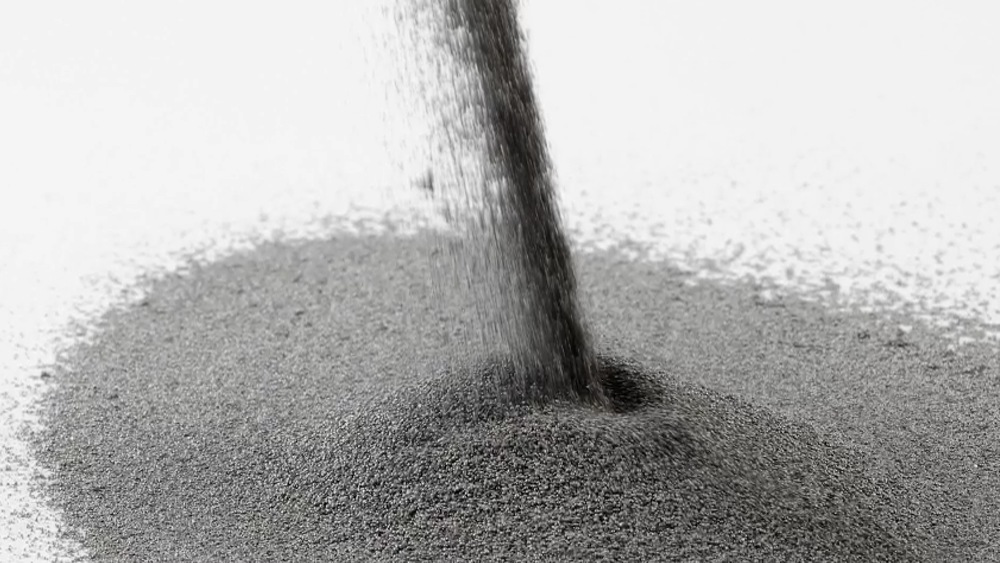
Types of Stainless Steel OP431 Powder
Composition of Stainless Steel OP431 Powder
Element | Weight % |
---|---|
Chromium | 15 – 17.5 |
Nickel | 3.5 – 5.5 |
Manganese | 1 max |
Silicon | 1 max |
Carbon | 0.04 max |
Sulfur | 0.03 max |
Phosphorus | 0.04 max |
Copper | 3 – 5 |
Niobium | 0.2 – 0.6 |
Source: Sandvik Osprey
Small Niobium additions give OP431 unique precipitation hardening response. Copper provides internal passivation against corrosion.
Popular Variants of OP431 Powder
OP431
Standard grade with good balance of properties, weldability and cost. Used for majority of applications.
OP431L
Low carbon variant with carbon limited to 0.03% max for improved weldability. Intergranular corrosion resistance also increased.
OP431LSi
Extra low carbon + silicon variant with carbon below 0.02% and silicon 0.8% min specifically for welding. Preferred when welding required.
OP431N
Nitrogen-alloyed grade with nitrogen 0.15% min for increased strength. Used when high hardness important.
Specifications of OP431 Powder
Critical parameters that dictate quality and performance of printed or sprayed OP431 parts include:
Size Distribution Specifications
Mesh Size | Micrometre Range |
---|---|
-100 Mesh | 105 – 150 μm |
100 – 325 Mesh | 44 – 105 μm |
150 – 325 Mesh | 32 – 75 μm |
Chemistry Conformance per AMS Standard
Element | Weight % |
---|---|
Carbon | 0.03/0.04 max |
Silicon | 1.00 max |
Manganese | 1.00 max |
Phosphorus | 0.03 max |
Sulfur | 0.02 max |
Nickel | 3.50/5.50 |
Chromium | 15.00/17.50 |
Niobium | 0.15/0.45 |
Source: AMS 5922 Standard
Applications of OP431 Powder
Thanks to its high strength-to-weight ratio and corrosion resistance, stainless steel OP431 sees diverse applications when fabricated using AM powder bed techniques.
OP431 Powder Applications by Industry
Industry | Typical Applications |
---|---|
Aerospace | Airframe & engine bolts, landing gear parts, actuators |
Automotive | Rocker arms, connecting rods, valves |
Chemical Processing | Pump shafts & impellors, valve bodies |
Oil & Gas | Downhole/subsea fasteners, wellhead parts |
Medical & Dental | Orthopedic implants, surgical instruments |
Ability to 3D print intricate, lightweight geometries expands possible applications across markets.
How OP431 Compares to Commonly Used Steel Powders
Alloy | Relative Corrosion Resistance | As-Fabricated Hardness | Post-Treatment Hardness |
---|---|---|---|
OP431 | Excellent, similar to 316 stainless | Up to 35 HRC | Peak 50 HRC |
17-4PH | Moderate, less than 316 | 35-40 HRC | Peak 50 HRC |
316L | Better than OP431 | ~25 HRC | – |
H13 | Low, requires coating | Up to 45 HRC | – |
OP431 delivers best all-around properties after full precipitation hardening post-treatment.
-
0# Pure Nickel powder
-
NiCoCrAlY alloys powders
-
Rene 142 alloy-Rene Powder
-
Haynes 25 Haynes Powder
-
FGH95 Ni-base Alloy Powder | Nickel Alloy Powder
-
CMSX-4 Nickel Alloy Powder | Nickel Alloy Powder
-
Ni-Fe-Mo Soft Magnetic Powder | Nickel Alloy Powder
-
Ni-Cr-Mo Alloy Powder | Nickel Alloy Powder
-
Nickel Titanium Alloy Powder | Nickel Alloy Powder
Suppliers of OP431 Stainless Steel Powder
Leading manufacturers providing OP431 steel powders for AM include:
OP431 Powder Manufacturers & Common Pricing
Company | Typical Pricing/Kg | Powder Variants |
---|---|---|
Sandvik Osprey | $50 – $120 | OP431, OP431LSi, OP431N |
Hoganas | $45 – $100 | OP431, OP431L |
Rio Tinto Metal Powders | $60 – $140 | OP431, OP431N |
Praxair | $70 – $130 | OP431, OP431N |
Costs range based on size distribution, lot quantity, certifications required, etc. Grades with extra low impurities command higher prices.
FAQ
What particle size distribution is recommended for OP431 in laser PBF AM?
A size range of 20-75 microns, with median size ~45 microns and Gaussian distribution is ideal. This ensures optimal packing density and even melting needed for high quality powder bed fusion processing.
What post-treatments can increase OP431 part properties?
Solution annealing followed by double aging heat treatments can increase hardness up to 700 Vickers/50 HRC maximum. Stress relieving, Hot Isostatic Pressing (HIP) and Hot Isostatic Heat Treatment (HIPHT) also further enhance material performance.
Is OP431 harder or stronger than 316L stainless steel?
OP431 has significantly higher strength and hardness capabilities – exceeding 1900 MPa tensile strength and 700 Vickers when precipitation hardened, almost 2X stronger than 316L on key metrics.
What industries use OP431 most for metal AM applications?
Aerospace and space, oil & gas equipment like valves and pumps, automotive turbochargers and high performance components have been early adopters of OP431 for service-critical applications needing extreme environmental resistance.
Are OP431 parts weldable using conventional or laser welding methods?
Yes, with proper joint preparation and process controls, OP431 can be welded successfully in both conventional GTAW/GMAW or laser/electron beam welding. Extra low carbon OP431L variant recommended for the best weldability results.