Overview
Stainless steel powder refers to fine stainless steel particles used as feedstock for manufacturing techniques like metal injection molding (MIM), additive manufacturing (AM), and conventional press and sinter powder metallurgy. Controlling stainless steel powder characteristics like composition, particle size distribution, morphology, and microstructure is critical to properties of finished components.
Common stainless steel grades available in powder form include:
- Austenitic grades – 304L, 316L, 303L, 17-4PH
- Martensitic grades – 420, 440C
- Duplex/ferritic – Custom alloys
atomization and the Hoganas process of reducing stainless steel oxides are the predominant production routes.
Stainless Steel Powder Production Methods
Method | Key Characteristics | Main Applications |
---|---|---|
Gas Atomization | Spherical powders for AM | Aerospace components |
Water Atomization | Irregular shapes, lower cost | Automotive parts |
Hoganas Process | Reduces oxides into alloy powders | High purity requirements |
Carbonyl Process | Ultra-fine spherical powders | MIM components |
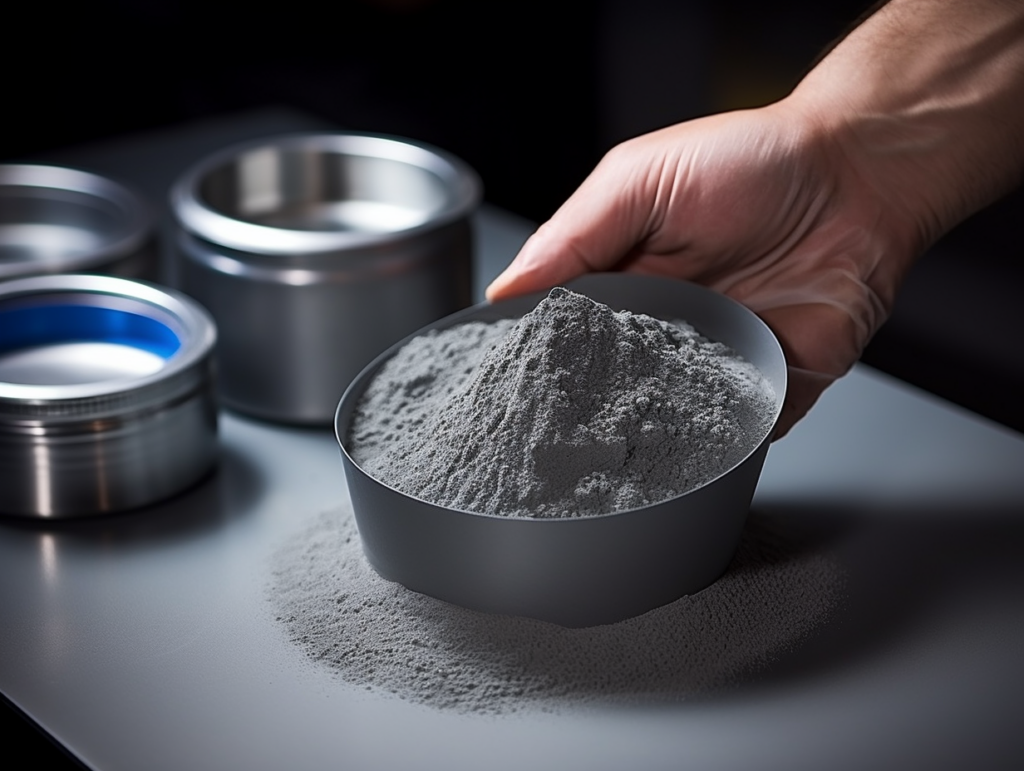
Alloy Grades and Compositions
Stainless steel powders contain iron alloyed with chromium, nickel, molybdenum, manganese in varying compositions:
Austenitic Stainless Steel Powder
Austenitic stainless steel powder like 316L and 304L are non-magnetic with an austenitic FCC crystal structure. Common compositions are:
Alloying Element | Role | Weight % Range |
---|---|---|
Chromium | Corrosion resistance | 16-18% |
Nickel | Austenite stabilizer | 10-14% |
Molybdenum | Resists pitting and crevice corrosion | 2-3% |
Manganese | Substitute for nickel | Up to 2% |
Nitrogen | Increases strength | 0.1-0.25% |
Benefits: Excellent corrosion resistance, good weldability and formability. Most widely used grade.
Martensitic Stainless Steel Powder
Martensitic stainless steel powder like 420, 440C achieve high strength and moderate corrosion resistance with compositions like:
Alloying Element | Role | Weight % Range |
---|---|---|
Chromium | Corrosion resistance | 12-18% |
Carbon | Hardenability | 0.2-1.0% |
Molybdenum | Increases corrosion resistance | 0.2-1% |
Vanadium | Carbide former | Up to 1% |
Benefits: Very high hardness capability up to 60 HRC after heat treatment.
Duplex Stainless Steel Powder
Duplex stainless steel powder combines both ferritic and austenitic structures to provide a balance of high strength and good ductility and toughness.
Alloying Element | Role | Weight % Range |
---|---|---|
Chromium | Corrosion resistance | 21-26% |
Nickel | Austenite stabilizer | 5-8% |
Molybdenum | Pitting/crevice resistance | 2-4% |
Nitrogen | Strengthens ferrite | 0.2-0.3% |
Benefits: Twice the strength of austenitic grades. Good resistance to stress corrosion cracking.
Production Methods
Various techniques are utilized to produce stainless steel powders:
Gas Atomization
In gas atomization process, molten stainless steel stream breaks into fine droplets by an inert gas blast which rapidly solidify into spherical powders ideal for metal AM and MIM.
Parameter | Description |
---|---|
Particle shape | Highly spherical |
Particle size | 15–45 μm typical |
Oxygen content | <0.5% |
Production scale | Medium–high |
Water Atomization
In water atomization, compressed air or water breaks up a stainless steel melt into fine irregular powders containing higher oxygen suitable for press and sinter process.
Parameter | Description |
---|---|
Particle shape | Irregular |
Particle size | 20-150 μm |
Oxygen content | 0.8-1.5% |
Production scale | Very high |
Carbonyl Iron Process
Metal carbonyls are decomposed to produce very fine stainless steel particles containing chromium alloying additions suitable for micro powder injection molding.
Parameter | Description |
---|---|
Particle shape | Spherical |
Particle size | 2-5 μm |
Oxygen content | <0.2% |
Production scale | Lower |
Oxide Reduction (Hoganas) Process
Stainless steel scrap oxides are reduced at high temperature producing irregular shaped powders with optimized oxygen/nitrogen levels.
Parameter | Description |
---|---|
Particle shape | Irregular |
Particle size | 45-150 μm |
Oxygen content | <0.6% |
Production scale | High |
Powder Characteristics
Critical stainless steel powder characteristics include:
Particle Size Distribution
Laser diffraction analyzers determine full range size distribution from nanometers to millimeters. Matching particle sizes to production method capabilities allows maximizing density.
Key parameters | Description |
---|---|
D10, D50, D90 | Size below which 10%, 50%, 90% particles by volume exist |
Mean size | Measure of central tendency |
Span = (D90-D10)/D50 | Width of distribution |
Particle Morphology
Scanning electron microscopy reveals fine particle shape details influencing powder behavior. Smooth, spherical particles improve flow and packing density.
Apparent and Tap Density
Flowmeter funnels determine how easily powders consolidate indicating ease of handling and compression into fine mold sections or intricate 3D geometries.
Parameter | Typical range |
---|---|
Apparent density | 2 – 3 g/cc |
Tap density | 3 – 4 g/cc |
Flow Characteristics
Hall flowmeter rates correlate well with layer filling performance in binder jet AM methods through optimized stainless steel powder flowability matching equipment needs.
Applications of Stainless Steel Powder
Unique properties of stainless steel powders make them critical for:
Metal Additive Manufacturing
Powder bed fusion techniques like selective laser melting and electron beam melting use fine stainless steel powders to directly fabricate complex three-dimensional components like impellers and reactive vessels.
Metal Injection Molding (MIM)
Mixing fine stainless steel powders with binders, then injection molding and sintering produces high volume small precision parts like gears, valves and nozzles.
Press and Sinter Powder Metallurgy
Compacting and sintering stainless steel powders produce porous structures like filters or self-lubricated bearings.
Surface Coatings
Atmospheric plasma spraying stainless steel powders creates durable protective coatings resisting wear, abrasion and corrosion.
Standards and Specifications
Stringent chemistry limits and powder characteristics are mandated to satisfy critical application needs:
Chemistry Control
Standards like ASTM A743, AMS 5604, 5743 regulate:
- Alloy ratios of Fe, Cr, Ni, Mn to provide specific microstructures and corrosion resistance
- Impurity limits on S, P, Si, N, O defining contamination thresholds
- Minor trace elements like Mo, Cu, Co enhancing performance
Powder Properties
Key quality metrics include:
Parameter | Typical Specification | Test Method |
---|---|---|
Mean particle size | 15-45 μm for AM | Laser diffraction |
Apparent density | > 2.5 g/cc | Hall flowmetry |
Tap density | > 3 g/cc | Scott volumeter |
Flow rate | >23 sec/50g | Hall flowmetry |
Loss on ignition | <1% | Thermogravimetric analysis |
Standards evolve continuously, mandating stricter chemistry and powder attribute controls to satisfy expanding application needs and safety in high performance sectors.
Suppliers and Pricing
Leading stainless steel powder producers globally include:
Supplier | Headquarters | Production Capabilities |
---|---|---|
Sandvik Osprey | UK | Gas atomization |
Hoganas | Sweden | Water atomization, oxide reduction |
CNPC Powder | China | Gas, water atomization |
Carpenter | USA | Gas, water atomization |
Cost varies based on:
- Base composition – higher alloy grades are pricier
- Production method purity
- Processing to tailor particle characteristics
- Purchase volumes – contracts enable lower pricing
Grade | Price Estimate |
---|---|
304L | $15 – $30 per kg |
17-4PH | $30 – $60 per kg |
Custom duplex/maraging | $60 – $150 per kg |
Pros and Cons
Benefits
- Corrosion resistance
- Thermal/electrical properties
- Fabrication flexibility – weldable
Tradeoffs
- More expensive than carbon steels
- Lower ductility than austenitic alloys
- Difficult machining driving costs
Comparing stainless steel powders to alternatives:
Parameter | Stainless Steel | Tool Steel | Maraging Steel |
---|---|---|---|
Corrosion Resistance | Excellent | Lower | Medium |
Thermal Conductivity | Lower | Higher | Highest |
Strength | Medium | Higher | Highest |
Cost | Medium | Low | Highest |
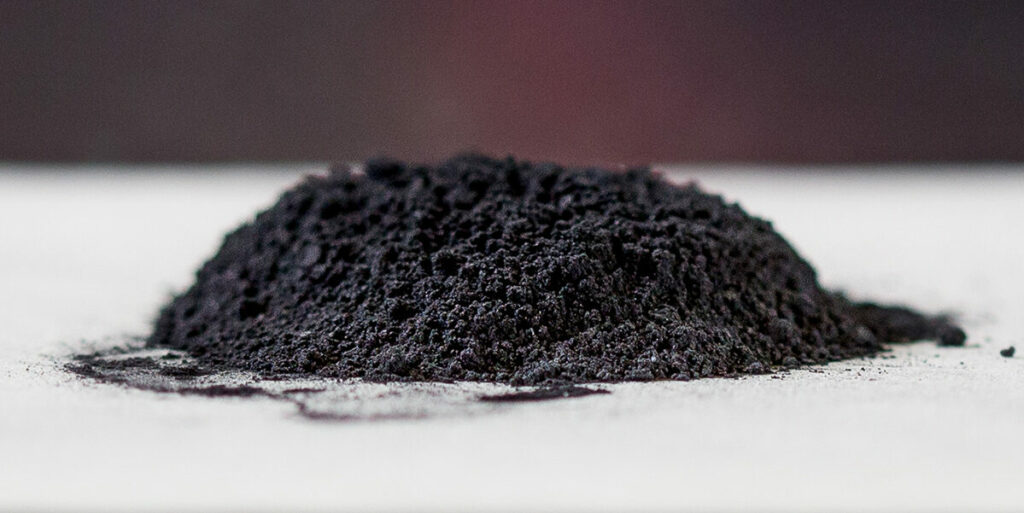
FAQs
Q: What is the most common stainless steel powder used in metal AM?
A: Gas-atomized 316L stainless steel powder is widely used in powder bed fusion AM techniques like SLM and EBM thanks to its excellent corrosion resistance combined with availability and reasonable pricing.
Q: How does stainless steel powder cost compare to tool steels or nickel alloys?
A: Stainless generally costs more than tool steels but less than precious metal alloys like nickel superalloys widely used in aerospace applications. Unique compositions can vary prices drastically.
Q: What affects stainless steel powder reuse rates in binder jet printing?
A: Maintaining strict layer thickness uniformity and accountability for ratio of fresh to recycled powder per build helps limit effects of work hardening and contamination enabling reuse up to 20 times before full replenishment.
Q: Why is high apparent density preferred for stainless steel powders in MIM feedstock?
A: Higher apparent density improves powder-binder mixing homogeneity allowing easier mold filling without binder richness issues that generate internal voids and sinks degrading mechanical performance.
Q: Which grades offer the best combination of corrosion resistance and high strength?
A: Duplex stainless steel powders like 2304 provide double the strength of 304 and 316 while still maintaining pitting and crevice resistance equivalent to 316 through high chromium and molybdenum contents.