stainless steels powders are fine metal particles made from various grades of stainless steel. They exhibit high strength, corrosion resistance, and versatility which makes them suitable for many applications. This article provides an overview of stainless steel powders, their composition, properties, manufacturing process, grades, sizes, applications, suppliers, standards, and more.
Overview of stainless steels powder
Stainless steel powders are metallic powders produced from alloys of iron, chromium, nickel, molybdenum, copper, titanium, aluminum, and other elements. The chromium content typically ranges from 10-30% which gives the steel its corrosion resistant properties.
They are made by processes like gas atomization, water atomization, and electrolytic deposition to yield fine spherical powder particles usually 5 – 150 microns in size. The powder shape, size distribution, density, and composition can be controlled to customize properties for different applications.
Their unique properties like high strength, good ductility, corrosion/oxidation resistance, durability, and diversity of grades makes these powders suitable for uses like 3D printing, injection molding, pressing and sintering, brazing, surfacing, welding, and thermal spraying.
Benefits of using stainless steel powders include:
- High strength and hardness
- Good ductility and toughness
- Excellent corrosion and wear resistance
- High temperature resistance
- Non-magnetic capabilities
- Controlled powder size and morphology
- Alloy flexibility with different compositions
- Cost-effectiveness
- Suitability for additive manufacturing
Limitations include:
- Higher cost than carbon steel powders
- Lower thermal/electrical conductivity
- More difficult to machine than wrought forms
- Susceptibility to pitting and crevice corrosion
- Processing challenges with certain grades
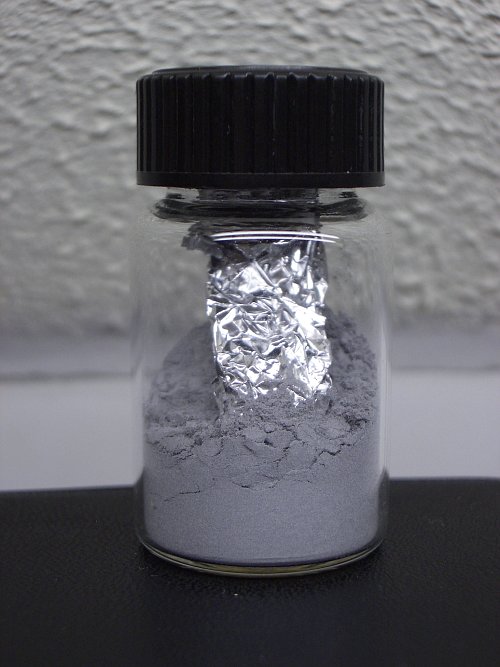
Composition of stainless steels powder
Stainless steel is defined as a steel alloy with a minimum of 10.5% chromium content. This chromium addition is what gives stainless steel its notable corrosion resistance, hardness, and strength.
The base is iron complemented by varying amounts of elements like nickel, molybdenum, manganese, titanium, copper, niobium, aluminum, silicon, nitrogen, sulfur, phosphorus, and carbon. The presence and percentages of these alloying elements is what determines the grade and distinguishes the properties of the different stainless steel powder types.
Typical composition ranges:
Element | Composition (%) |
---|---|
Iron (Fe) | Balance |
Chromium (Cr) | 10.5-30% |
Nickel (Ni) | 0-20% |
Molybdenum (Mo) | 0-6% |
Manganese (Mn) | 0-2% |
Copper (Cu) | 0-4% |
Titanium (Ti) | 0-0.7% |
Niobium (Nb) | 0-1% |
Silicon (Si) | 0-1% |
Nitrogen (N) | 0-0.25% |
Carbon (C) | 0-1.2% |
Sulfur (S) | 0-0.03% |
Phosphorus (P) | 0-0.04% |
Comparison between 316L and 17-4PH grades:
Element | 316L SS | 17-4PH SS |
---|---|---|
Chromium | 16-18% | 15-17.5% |
Nickel | 10-14% | 3-5% |
Molybdenum | 2-3% | 0-1% |
Copper | 0.5% max | 3-5% |
Niobium | – | 0-1% |
Nitrogen | 0.1% max | – |
Effects of key elements:
- Chromium – Core alloying element that enables corrosion resistance and hardness
- Nickel – Adds toughness, ductility, and high temperature strength
- Molybdenum – Increases corrosion resistance particularly to chlorides/acids
- Copper – Further enhances corrosion performance in acidic environments
- Niobium/Titanium – Used as stabilizers to negate properties reduction from intermetallics
- Nitrogen – Solid solution strengthener which also boosts yield strength
- Manganese – Deoxidizer improving sulfur resistance during processing
- Carbon/Sulfur/Phosphorus – Impurities controlled at low levels (often <0.03%)
Properties of stainless steels powder
Stainless steel powders exhibit an attractive combination of properties that bridge the gap between standard carbon steels and the more exotic alloys. The chromium and nickel alloying elements primarily enable their defining corrosion resistant capabilities but also augment their high strength-to-weight performance.
Mechanical properties
- Good strength (yield strength 100-350 MPa range)
- Excellent hardness (Brinell 160-240)
- Moderate ductility (10-50% elongation)
- High fracture toughness (20-200 MPa-m^1/2^)
- Good impact resistance
- Non-magnetic grades available
Corrosion properties
- Pitting resistance – Can withstand localized attacks in aggressive media
- Crevice resistance – Resilient versus stagnant micro-environments
- Stress cracking resistance – Durable against damaging tensile stresses
- Wear/erosion resistance – Suitable for high wear applications
- Oxidation resistance – Can operate in oxidizing conditions up to 900°C
Other properties
- Density – Around 8 g/cm3
- Thermal conductivity – 12-30 W/m-K
- Electrical resistivity – 0.75 μΩ-m
- Curie temperature – Ranges from -150°C to 315°C
- Melting point – 1300-1500°C
stainless steels powder Manufacturing Process
Stainless steel powders can be produced through different techniques depending on required characteristics like particle size range, shape, microstructure, cost, and alloying precision. The most common methods in use are gas atomization, water atomization, and electrolytic powder manufacturing.
Gas Atomization
Molten stainless steel is disintegrated into fine droplets by high velocity inert gas jets (argon or nitrogen). The droplets rapidly solidify into spherical powders with tightly controlled particle size distributions. Advantages include good powder flowability and compressed density. Downsides are satellite formation and higher gas consumption.
Water Atomization
Similar to gas atomization but water is used instead for quenching the molten metal stream. Rapid solidification yields irregular shaped powders with a wide particle size range and porous internal structure. Low cost but limited alloy options and lower powder densities relative to gas atomization.
Electrolytic Powder Production
Uniform and porous spherical powders are deposited onto a cathode through electro-winning from aqueous electrolytes containing stainless steel ions. Tight control over shape and size distribution but limited to simple alloys like 316L grade.
Other methods – Rotating electrode process, rotary atomization, plasma rotating electrode process, thermal plasma synthesis
In addition to primary manufacturing, the powders may undergo secondary treatment like annealing, fragmentation, classifying, mixing, sieving, and coating to achieve target specifications.
stainless steels powder Grades and Sizes
Stainless steel powders are available in a variety of standardized alloys/grades to suit different applications and conditions. The grade denotes specific composition which gives rise to certain physical, mechanical, corrosion, and fabrication characteristics.
Common grades include:
- 304 – General purpose Austenitic SS with 18-20% Cr and 8-10.5% Ni
- 316/316L – Austenitic SS with 16-18% Cr, 10-14% Ni and 2-3% Mo for superior corrosion resistance
- 410 – Martensitic grade with 11.5-13.5% Cr offering high strength and hardness
- 420 – Similar to 410 grade but with increased carbon content for greater wear resistance
- 17-4PH – Precipitation hardening martensitic SS with good corrosion resistance after aging
- 15-5PH – Precipitation hardening grade with high strength capability
- Custom alloys – Special grades tailored for niche applications
The powders cover a wide range of sizes (particle diameters) generally in the range of 5 μm to 150 μm:
- Ultrafine = less than 15 μm
- Fine = 15 μm to 45 μm
- Medium = 45 μm to 105 μm
- Coarse = 105 μm to 150 μm
Average size, distribution, sphericity, tap density, pycnometer density, flow rate, and chemical assays are usually provided by the manufacturer according to application needs.
Size distribution example – gas atomized 316L stainless steel powder
Sieve Size | Weight Percent Retained (%) |
---|---|
+140 mesh | 2% |
-140/+200 mesh | 13% |
-200 mesh | 7% |
Pan | 78% |
stainless steels powder Applications
Key applications of stainless steel powders leverage attributes like high temperature performance, hardness, strength, corrosion resistance, wear resistance, manufacturability, and range of available alloys.
Additive manufacturing
- Binder jet printing
- Directed energy deposition
- Laser powder bed fusion
- Electron beam melting
Used across industries like aerospace, medical, energy, and automotive to print complex, lightweight, or custom stainless parts.
Metal injection molding (MIM)
Sintering of fine powders enables high volume production of small, intricate shapes with tight tolerances like surgical tools, gears, nozzles, and manifolds.
Press and sinter components
Compacting and heating powders to produce high density parts like bushings, seals, ball bearings and structural components needing controlled porosity.
Joining / surfacing applications
Stainless steel powders are a common raw material for methods like cold/thermal spraying, laser cladding, and brazing used for wear resistant coatings and corrosion protection.
Other niche uses
Investment casting, centrifugal casting, friction materials fabrication, spark plasma sintering, powder forging, surface texturing, pyrotechnic compositions, etc.
Global stainless steels powder and Pricing
Stainless steel powder is commercially produced by a range of leading specialty metals manufacturers around the world. Prices vary based on grade, size distribution, quantity, and geographical region. Some top producers include:
Company | Location |
---|---|
Sandvik | Sweden |
Höganäs | Sweden |
Rio Tinto Metal Powders | Canada |
Pometon Powder | Italy |
Ametek SMP | US |
CNPC | China |
JFE Steel | Japan |
Carpenter Powder Products | US |
Aubert & Duval | France |
Price estimates:
Powder Grade | Cost Per Kg |
---|---|
304, 316, 316L, 410, 420 | $12-60 |
17-4PH, 15-5PH | $30-100 |
Custom alloys | $50-200 |
Prices vary based on:
- Purity / trace elements
- Particle size range
- Consistency / sphericity
- Purchase volume
- Level of post-processing
- Location
Higher performance alloys with controlled characteristics and smaller batches command premium pricing. Large OEM contracts benefit from economies of scale.
stainless steels powder Specifications and Standards
Stainless steel powders must meet exacting industry standards that cover critical chemical, physical, and mechanical parameters to ensure fitness-for-use across various demanding applications.
Standard | Organization | Region |
---|---|---|
ASTM B963 | ASTM International | Global |
EN 10088 | European Committee for Standardization (CEN) | Europe |
JIS G 4305 | Japanese Industrial Standards (JIS) | Japan |
GB/T 20878 | Standardization Administration of China (SAC) | China |
These specifications help define proper:
- Nominal composition – Analysis and % of alloying elements like Fe, Cr, Ni, Mo etc. that constitute the grade
- Impurity limits – Maximum permissible trace elements like C, P, S, Si etc.
- Particle size distribution – Micron range fractions from sieving
- Particle shape – Scanning Electron Microscope (SEM) imaging
- Tap density – Assessed via hall flowmeter method
- Flow rate – Weight flow per minute through an orifice
along with recommended sampling, testing, inspection, packaging, marking, and certification procedures.
Customers often request compliance reports from reputable testing agencies to validate procurement lots satisfy designated grade and property requirements.
Comparison of Atomization Methods
Gas vs Water Atomization
Water atomization is more cost effective but gas atomization provides superior powder quality.
Parameter | Gas Atomization | Water Atomization |
---|---|---|
Particle shape | Highly spherical | Irregular, satellite particles common |
Particle size distribution | Narrow distribution | Wide distribution |
Tap density | Up to 4.5 g/cc | 2-3 g/cc |
Internal porosity | Lower | Higher |
Alloy options | Most alloys feasible | Limited alloys |
Cost | Higher capital and operating cost | Lower cost process |
Gas alone provides sufficient cooling rates for consistent small particles suited for additive manufacturing and metal injection molding.
Pros and Cons of Stainless Steel Powders
Advantages | Disadvantages |
---|---|
– Excellent corrosion resistance | – Relatively expensive |
– High hardness and wear performance | – Lower thermal conductivity than carbon steels |
– High ductility and fracture toughness | – More difficult to cut and machine |
– Temperature resistance up to 900°C | – Certain grades susceptible to pitting and crevice corrosion |
– Non-magnetic capabilities available | – Limited formability relative to carbon steels |
– Range of alloys/grades to choose from | – Contains allergenic elements like Ni and Cr |
– Compositional flexibility from wide alloy choices | – Some fractions pose combustion and explosion risks |
– Suitable for metal injection molding and additive manufacturing | – Powder reuse can be limited for some applications |
– Cost effective relative to other high alloy options (titanium, super alloys etc.) |
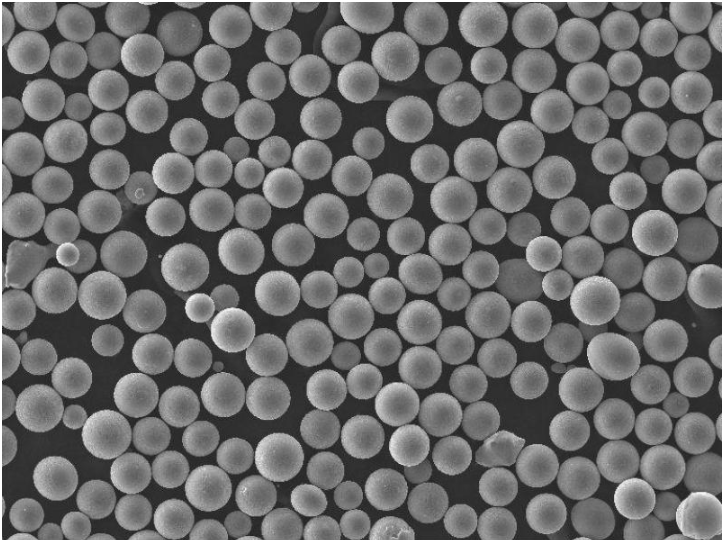
FAQ
Q: What is the main difference between 304 and 316 stainless steel powders?
A: 316 SS powders contain 2-3% molybdenum allowing improved pitting and crevice corrosion resistance over 304, especially for chlorine or saltwater exposure. 316 SS is better for medical implants and marine applications.
Q: Why use stainless steel powders instead of wrought products?
A: Powder-based manufacturing techniques enable intricate, lightweight parts with enhanced mechanical properties and alloy combinations unattainable via conventional practices. Powders are vital for additive and powder metallurgy methods.
Q: How big is the global stainless steel powders market?
A: Around 80 kilotons per year valued at over $850 million and growing above 5% annually. Use is rising across 3D printing, automotive fuel cells, food processing, chemical plants, biomedical, aerospace, and energy applications.
Q: What safety precautions should be taken when handling stainless steel powders?
A: Exposure mitigation measures like masks, gloves, ventilation and hygiene to limit skin/lung contact and sensitization risks. Plus fire and explosion prevention given combustion potential of fine metallic particles. Proper storage away from sparks, ignition sources, oxidizers and acids also crucial.
Q: What is the recycling potential for stainless steel powders?
A: Depends on contamination levels and acceptable property degradation for the specific application. Can often melt and reuse powders multiple times for prototyping work before mechanical performance deteriorates too far. More process controls needed for secondary reuse targeting final part production.