Introduction to Stellite 3 Powder
When it comes to materials that can withstand extreme wear, high temperatures, and intense friction, Stellite 3 Powder stands out as a preferred choice in a range of industrial applications. If you’ve ever wondered why aerospace, oil & gas, and heavy manufacturing rely heavily on certain metal alloys, the answer often lies in their unique compositions—and Stellite alloys are a prime example. The Stellite family of alloys, initially developed in the early 20th century, has earned a solid reputation in high-wear applications, thanks to its remarkable resistance to corrosion, wear, and even galling (a form of material transfer under friction).
Stellite 3 Powder, part of this robust alloy family, is especially prized for its use in hard-facing and coating processes. It is composed primarily of cobalt, chromium, tungsten, and carbon, each of which contributes specific properties that make it incredibly durable under stress. But what exactly makes Stellite 3 Powder so unique, and how does it stack up against other metal powders? Let’s dig into the details.
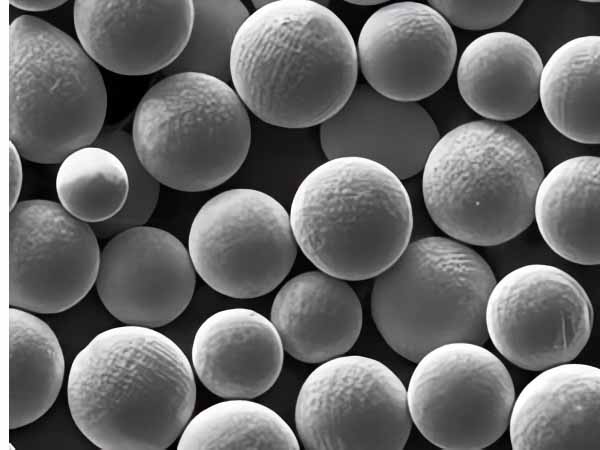
Composition of Stellite 3 Powder
The strength and durability of Stellite 3 Powder lie in its carefully engineered composition. Here’s a breakdown of its primary elements and why each one is essential:
Element | Percentage Range | Role in Stellite 3 Powder |
---|---|---|
Cobalt (Co) | 50-60% | Base metal providing corrosion resistance and thermal stability. |
Chromium (Cr) | 25-35% | Adds oxidation resistance, especially at high temperatures. |
Tungsten (W) | 4-7% | Increases hardness and wear resistance. |
Carbon (C) | 1.8-2.5% | Enhances the hardness by forming carbides, which resist abrasion. |
Silicon (Si) | <1% | Helps with the alloy’s fluidity and anti-galling properties. |
These elements work together to form a highly durable and wear-resistant alloy that performs exceptionally well in challenging conditions. Unlike other alloys, Stellite 3 maintains its hardness at high temperatures, which makes it ideal for coatings in environments where intense heat and friction are common.
Characteristics of Stellite 3 Powder
What sets Stellite 3 Powder apart are its unique characteristics, resulting from its composition and metallurgical structure. It is incredibly hard and resistant to both abrasion and corrosion, a combination that few other materials can match. Let’s take a closer look at the specific characteristics of Stellite 3 Powder:
Property | Value | Description |
---|---|---|
Hardness | 45-50 HRC | Provides exceptional wear resistance. |
Melting Point | 1,350°C | Withstands high temperatures without losing structure. |
Density | ~8.6 g/cm³ | Dense, which contributes to its durability. |
Corrosion Resistance | High | Resistant to oxidation and corrosion in harsh environments. |
Thermal Stability | High | Retains strength and hardness even when exposed to extreme temperatures. |
These characteristics make Stellite 3 Powder a top choice in thermal spraying, plasma transferred arc welding (PTA), and laser cladding applications. When compared to other Stellite alloys, Stellite 3 has a slightly lower hardness but higher wear resistance, making it versatile for industries that require both robustness and durability.
Applications and Use Cases for Stellite 3 Powder
Due to its unique composition and properties, Stellite 3 Powder finds widespread applications across numerous industries. From oil and gas to aerospace and medical manufacturing, its ability to withstand harsh conditions makes it invaluable. Here’s where Stellite 3 Powder truly shines:
Industry | Application | Benefits |
---|---|---|
Oil & Gas | Valve coatings, drill bit reinforcements | High wear resistance, long-lasting performance under friction. |
Aerospace | Engine parts, turbine coatings | Thermal stability and oxidation resistance. |
Medical | Surgical tools, dental implants | Biocompatible, corrosion-resistant. |
Automotive | Wear parts, bearings | Reduces friction and extends part life. |
Mining | Excavator and loader components | Hard surface reduces material wear from abrasive environments. |
The specific properties of Stellite 3, such as its resistance to corrosion and high melting point, make it ideal for applications where other materials would wear out prematurely. In particular, hard-facing tools and components in the oil and gas industry are primary beneficiaries of this metal powder’s durability.
-
CM247LC Powder | Nickel Alloy Powder
-
0# Pure Nickel powder
-
NiCoCrAlY alloys powders
-
Rene 142 alloy-Rene Powder
-
Haynes 25 Haynes Powder
-
Best Hastelloy C-22 Powder-High temperature alloy Powder for 3D Printing
-
Best Hastelloy C-276 Powder-High temperature alloy Powder for 3D Printing
-
Best Hastelloy N Powder-High temperature alloy Powder for 3D Printing
-
Best Hastelloy B Powder丨High temperature alloy Powder for 3D Printing
Grades and Standards of Stellite 3 Powder
Understanding the available grades and standards of Stellite 3 Powder helps users select the right variant for specific applications. While Stellite alloys are governed by different international standards, the following table highlights some key standards and grades associated with Stellite 3 Powder.
Grade | Standard | Application Suitability |
---|---|---|
Stellite 3C | AMS 5894 | High-hardness applications, best for abrasive environments. |
Stellite 3F | ASTM B818 | Fine powder for precise coating applications. |
Stellite 3P | AWS A5.13 | Suitable for PTA welding and laser cladding. |
Suppliers and Pricing for Stellite 3 Powder
Finding a reliable supplier for Stellite 3 Powder is crucial due to the specific requirements in quality and composition for industrial use. Pricing can vary depending on supplier, quantity, purity levels, and the specific grade required. Here’s a breakdown of major suppliers and estimated pricing trends to help guide purchasing decisions.
Supplier | Location | Available Grades | Average Price (USD/kg) | Key Features |
---|---|---|---|---|
Kennametal | Global | Stellite 3C, 3P, 3F | $50 – $150 | Leading supplier with a range of customization options. |
Höganäs | Sweden, Global | Stellite 3 Powder | $45 – $140 | Known for high-quality powders in various grain sizes. |
Oerlikon Metco | Switzerland, Global | Stellite 3, Stellite 12 | $60 – $160 | High-grade powders suitable for thermal spraying. |
Carpenter Technology | USA | Stellite 3F, 3P | $55 – $145 | Custom powder sizes and wide distribution network. |
Wall Colmonoy | USA, UK | Stellite 3 | $65 – $150 | Specialized in wear-resistant metal alloys. |
Pricing Factors to Consider
The cost of Stellite 3 Powder varies based on several factors:
- Grade Specificity: Fine powders for precise applications may be priced higher.
- Quantity Ordered: Bulk purchases often come with discounts, ideal for industrial-scale use.
- Supplier Reputation: Reliable suppliers may charge a premium, but this often ensures consistent quality.
- Customization Requirements: Custom particle sizes or compositions can also impact pricing.
Typically, industrial buyers choose to prioritize quality over cost due to the essential role that Stellite 3 Powder plays in high-stakes applications. For example, if you’re coating turbine parts or heavy equipment, the expense of premature wear from using inferior powders could far outweigh the initial cost savings.
Advantages and Disadvantages of Stellite 3 Powder
When choosing Stellite 3 Powder for your application, it’s helpful to weigh its pros and cons against other alloys. Here’s a comparative view of the benefits and limitations associated with Stellite 3 Powder, so you can make an informed choice.
Advantages | Limitations |
---|---|
Exceptional Wear Resistance | Relatively high cost compared to basic alloys. |
High-Temperature Stability | Challenging to machine once coated on surfaces. |
Corrosion and Oxidation Resistant | Limited to specific industrial applications. |
Biocompatible (suitable for medical use) | May require specialized equipment for application. |
Versatile Application Options (thermal spraying, PTA, cladding) | Less ductile, which can make it brittle under extreme pressure. |
Advantages Explained
Stellite 3 Powder shines in applications where wear resistance and durability are paramount. In the oil and gas industry, where high-friction environments demand parts that won’t degrade quickly, Stellite 3 provides a robust solution. Additionally, its corrosion resistance makes it invaluable for coating components that are exposed to the elements or harsh chemicals.
Limitations to Consider
While Stellite 3 is undoubtedly robust, its high cost can be a limiting factor for small operations. Machining Stellite coatings can also be challenging because of its hardness, meaning additional investments in specialized equipment might be necessary. Moreover, due to its brittleness in certain conditions, it’s not ideal for every application, especially those that require a degree of flexibility.
Technical Specifications of Stellite 3 Powder
Each grade and type of Stellite 3 Powder has specific technical specifications that cater to different applications. From particle size to hardness, here’s a look at the technical details that matter.
Specification | Details |
---|---|
Particle Size | 20-150 µm (Microns), customizable based on need. |
Hardness | 45-50 HRC |
Thermal Conductivity | Low – enhances performance under high temperatures. |
Melting Point | Approx. 1,350°C |
Bulk Density | 8.6 g/cm³ |
Flowability | Excellent for spray applications, less clogging. |
Key Technical Insights
- Particle Size Variability: The range from 20 to 150 microns allows for versatility in application methods. Smaller particles are preferred for precision coating applications, whereas larger particles might be used in bulk surface coverage or hard-facing.
- Hardness: With a hardness between 45 and 50 HRC, Stellite 3 Powder is exceptionally tough, suitable for high-wear applications. This hardness level is ideal for equipment facing extreme stress, such as mining tools and cutting equipment.
- Thermal Stability: Stellite 3 Powder’s low thermal conductivity ensures it retains its structure in high-heat environments. This makes it invaluable for industries like aerospace and oil and gas, where parts are often subjected to intense temperatures.
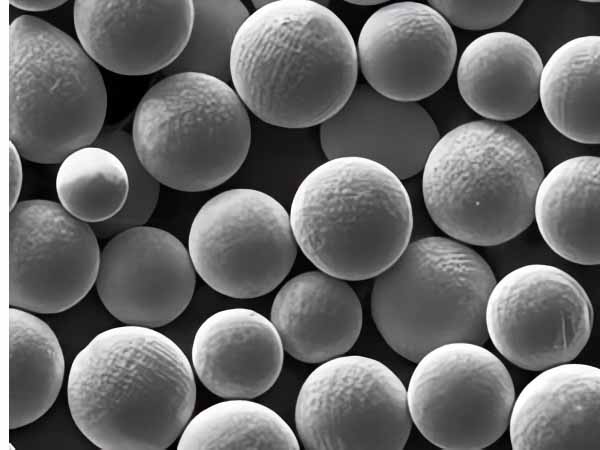
FAQ
Understanding the unique properties and applications of Stellite 3 Powder can sometimes raise questions, especially for new buyers or users. Below is a detailed FAQ section to clarify common inquiries.
Question | Answer |
---|---|
What is Stellite 3 Powder used for? | It is mainly used in hard-facing and coating applications for high-wear and high-temperature environments. |
Can Stellite 3 Powder be applied to any metal? | Typically, it is applied to alloys compatible with high-temperature processes like thermal spraying. |
Is Stellite 3 Powder expensive? | Yes, it’s generally more expensive than standard metal powders due to its unique properties. |
How does it compare to other Stellite powders? | Stellite 3 offers better wear resistance but may be harder to machine compared to softer grades. |
What application methods work best with Stellite 3 Powder? | Thermal spraying, plasma transferred arc (PTA) welding, and laser cladding are commonly used methods. |
How is the particle size determined? | Particle size is often tailored to application needs, ranging from fine powder to coarser grains. |
Are there environmental limitations for its use? | Stellite 3 is excellent for harsh environments, though it may become brittle in extreme cold. |
Is Stellite 3 Powder biocompatible? | Yes, it is used in medical tools and implants due to its corrosion resistance and durability. |
What is the typical shelf life of Stellite 3 Powder? | If stored properly, Stellite 3 Powder can last several years without degradation. |
Does it require special storage? | It should be stored in a dry environment to avoid any moisture contamination |