In the realm of advanced materials, titanium alloys reign supreme for their exceptional blend of strength, weightlessness, and resilience. But within this metallic kingdom, TA15 titanium alloy powder stands out as a champion, boasting a unique composition and a remarkable set of properties that have revolutionized the world of additive manufacturing (3D printing).
This article delves into the fascinating world of TA15 titanium alloy powder, unraveling its secrets and exploring its potential. We’ll embark on a journey that explores its characteristics, applications, advantages and considerations, and even answer some burning questions you might have. So, buckle up and get ready to be amazed by the power packed within these tiny metallic particles.
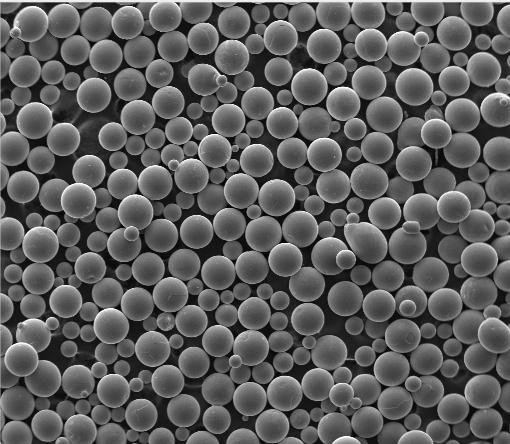
Characteristics of TA15 Titanium Alloy Powder
Imagine a metal powder so fine it could dance on the tip of your finger, yet so potent it holds the key to crafting high-performance components. That’s the essence of TA15 titanium alloy powder. But what makes it special? Let’s dissect its composition:
- Chemical Makeup: TA15 boasts a specific chemical composition of Ti-6Al-2Zr-1Mo-1V. This translates to a precise blend of titanium (Ti) as the base element, fortified with aluminum (Al) for strength, zirconium (Zr) for high-temperature stability, molybdenum (Mo) for creep resistance, and vanadium (V) for improved toughness.
- Microstructure: Under a powerful microscope, TA15 powder reveals itself as a collection of tiny, near-spherical particles. This spherical shape is crucial for a smooth and efficient 3D printing process, ensuring optimal flow and packing during printing. Particle size also plays a vital role, with finer powders typically leading to smoother surface finishes on printed parts.
- Mechanical Properties: The magic lies in the synergy between its elements. TA15 offers an impressive combination of high strength, exceeding 950 MPa (137,000 psi) in the tensile test, excellent ductility (ability to deform without breaking), and remarkable fatigue resistance, meaning it can withstand repeated stresses without succumbing to failure.
Think of it this way: Imagine a bridge. You want it to be strong enough to support heavy loads (high strength), yet flexible enough to sway slightly in the wind without cracking (ductility). TA15 titanium alloy powder offers the perfect balance for such demanding applications.
Applications of TA1 Alloy Powder
TA15’s exceptional properties make it a highly sought-after material in various industries, particularly those pushing the boundaries of design and performance:
- Aerospace: In the relentless pursuit of lightweight yet robust aircraft components, TA15 shines. It’s used to create parts like landing gear components, airframe structures, and engine mounts, where weight reduction translates to improved fuel efficiency and overall performance.
- Medical Implants: The human body deserves the best. TA15’s biocompatibility makes it an ideal candidate for medical implants like knee and hip replacements. Its remarkable strength ensures these implants can withstand the rigors of daily life, while its corrosion resistance minimizes the risk of rejection.
- Automotive: The quest for lighter, faster, and more fuel-efficient vehicles is a constant battle cry in the automotive industry. TA15 steps up to the challenge, enabling the creation of high-performance components like suspension parts, connecting rods, and even intricate engine components.
- Consumer Goods: From high-end sporting equipment like bicycle frames and golf clubs to luxury consumer electronics, TA15 is finding its way into an increasing number of applications. Its unique combination of strength, weight, and aesthetics makes it a compelling choice for manufacturers seeking to create premium products.
Consider this analogy: Think of a high-end sports car. It needs to be light and agile for superior handling (low weight), yet strong enough to maintain structural integrity during high-speed maneuvers (high strength). TA15 allows engineers to achieve this delicate balance.
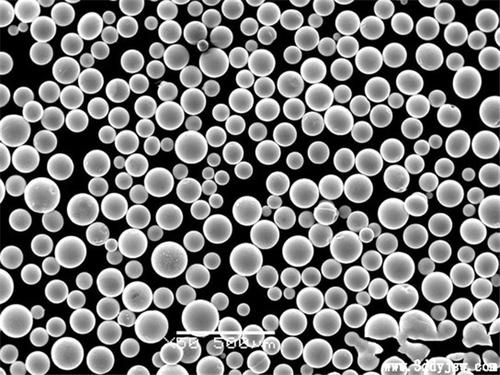
Advantages of TA15 Titanium Alloy Powder
When compared to other titanium alloy powders or even traditional manufacturing techniques, TA15 offers a distinct set of advantages:
- Superior Mechanical Properties: As discussed earlier, TA15 boasts exceptional strength, ductility, and fatigue resistance, making it ideal for applications demanding peak performance.
- Design Freedom: Additive manufacturing unlocks a world of design possibilities. TA15, perfectly suited for 3D printing, allows engineers to create complex, lightweight structures that would be impossible with conventional techniques.
- Reduced Waste: Traditional manufacturing often results in significant material waste. With 3D printing and TA15 powder, material usage is optimized, minimizing waste and promoting a more sustainable approach.
- Lightweighting: In applications where weight reduction is paramount, TA15 shines.
- Fast Prototyping: The ability to create complex prototypes rapidly is a game-changer in product development. TA15 powder facilitates swift iteration and testing cycles, accelerating the path from concept to finished product.
- Cost-Effectiveness: While the initial cost of TA15 powder might seem high, its efficiency in material usage and the design freedom it offers can translate to significant cost savings in the long run, particularly for complex parts.
Imagine this scenario: A company is developing a revolutionary new prosthetic limb. With TA15, they can create intricate, lightweight designs that perfectly mimic natural movement, while minimizing production waste and accelerating the testing and refinement process.
Considerations for Using TA15 Titanium Alloy Powder
While TA15 boasts a remarkable set of properties, there are a few factors to consider before incorporating it into your project:
- Cost: Compared to some other metal powders, TA15 can be more expensive. However, as discussed earlier, the potential cost savings in material usage and design optimization can offset the initial investment.
- Processing Requirements: 3D printing with TA15 powder necessitates specialized equipment and expertise. The printing process itself can be more complex compared to some other materials.
- Surface Finish: While TA15 can produce parts with good surface finishes, achieving an ultra-smooth finish might require additional post-processing techniques.
Think of it like this: Imagine a high-performance sports car. It offers incredible speed and handling, but it also requires specialized fuel and a skilled driver to operate at its peak. Similarly, TA15 offers exceptional properties, but it necessitates the right equipment and expertise to unlock its full potential.
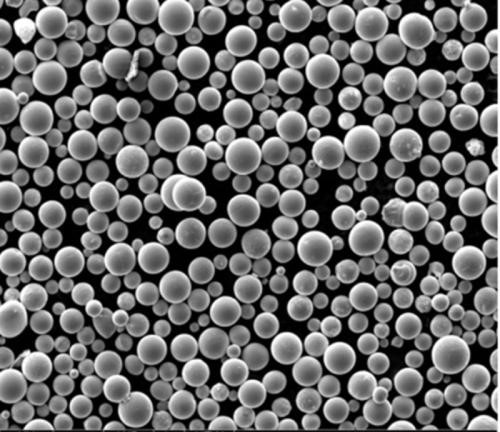
FAQ
Q: What are the typical particle sizes of TA15 powder?
A: TA15 powder is available in a range of particle sizes, typically between 15-50 micrometers. The optimal size depends on the specific application and desired surface finish. Finer powders generally result in smoother finishes but might require more specialized printing equipment.
Q: How does TA15 compare to other titanium alloy powders like Ti6Al4V?
A: Both TA15 and Ti6Al4V (grade 5) are popular titanium alloy powders. Here’s a quick comparison:
Feature | TA15 | Ti6Al4V (Grade 5) |
---|---|---|
Strength | Slightly higher | High |
Ductility | Slightly lower | Higher |
Fatigue Resistance | Excellent | Good |
High-Temperature Stability | Better | Good |
Cost | More expensive | Less expensive |
Q: Is TA15 a good choice for bioprinting applications?
A: TA15’s biocompatibility makes it a promising candidate for some bioprinting applications. However, other biocompatible titanium alloys specifically designed for bioprinting might be better suited depending on the specific needs of the implant.
Q: Where can I buy TA15 titanium alloy powder?
A: Several reputable suppliers offer TA15 powder. It’s crucial to choose a supplier with a proven track record of quality and consistency.
Conclusion
TA15 titanium alloy powder stands as a testament to the power of innovation in materials science. Its unique blend of properties and its compatibility with 3D printing technology have opened doors to a new era of design and manufacturing possibilities. From lightening the skies with aerospace components to revolutionizing medical implants, TA15 is poised to play a significant role in shaping the future across various industries. As advancements in 3D printing technology continue, and the cost of TA15 powder becomes more competitive, we can expect to see even wider adoption of this remarkable material.