TC11 powder is an important material used in various manufacturing and production applications. This guide provides a detailed overview of TC11 powder, its key characteristics, applications, specifications, suppliers, installation, operation and maintenance procedures.
What is TC11 Powder?
TC11 powder is a specialty titanium alloy powder designed for additive manufacturing applications like laser powder bed fusion. The “TC” refers to the titanium alloy system containing chromium, while “11” indicates the specific alloy composition.
Some key properties of TC11 alloy and powder include:
- High strength and hardness while maintaining ductility
- Excellent corrosion resistance
- Good oxidation resistance up to 700°C
- Low density compared to steel alloys
- Biocompatibility and non-toxicity
TC11 parts can achieve strengths over 1300 MPa and elongation over 10% when processed correctly. The material offers an excellent combination of strength, toughness and corrosion resistance.
TC11 is considered an α+β titanium alloy, containing both alpha and beta phases. The α phase provides good ductility and fracture toughness, while the beta phase contributes to high strength.
Composition of TC11
The nominal composition of TC11 alloy is:
Element | Weight % |
---|---|
Titanium | Balance |
Chromium | 7.5-8.5 |
Molybdenum | 1.5-2.5 |
Aluminum | 3.5-4.5 |
Zirconium | 3.5-4.5 |
Tin | 1.5-2.5 |
Trace elements like carbon, oxygen and nitrogen are minimized since they negatively affect mechanical properties and corrosion resistance. The chromium content provides excellent oxidation and corrosion resistance.
Production of TC11 Powder
TC11 alloy powder can be produced using various methods:
- Gas Atomization: High pressure inert gas is used to turn molten alloy into fine droplets that solidify into spherical powder particles. This produces powder with good flowability and packing density.
- Plasma Rotating Electrode Process (PREP): Electrode rotation and plasma arc melting produces highly spherical powders with controlled microstructure and composition.
- Hydride-Dehydride (HDH): The alloy is hydrogenated into brittle chunks that are crushed into powder and then de-hydrogenated. This produces irregular, angular powder particles.
Gas atomized and PREP powders have higher quality, but HDH powder can be cheaper. Particle size distribution, morphology and purity are controlled carefully during production to optimize properties.
Applications of TC11 Powder
TC11 parts fabricated from the alloy powder have diverse applications in industries like aerospace, oil & gas, automotive, medical, chemical processing and more.
Some major applications include:
- Aerospace: Structural components like airframes, ribs, bulkheads, fasteners, brackets, valves etc. where high strength-to-weight ratio is critical.
- Automotive: Valvetrain components, connecting rods, drive shafts, turbocharger parts subjected to high temps and stresses.
- Medical: Orthopedic and dental implants like joint replacements, screws, plates that require biocompatibility, corrosion resistance and high strength.
- Chemical processing: Heat exchangers, tanks, pipes, pumps, valves used in corrosive environments at elevated temperatures.
- Power generation: Components for steam and gas turbines, heat exchangers and pipes in nuclear power plants.
- Marine: Propellers, shafts, pumps, valves, pipelines where seawater corrosion resistance is crucial.
TC11 combines high specific strength with oxidation and corrosion resistance to perform reliably in critical components under demanding conditions.
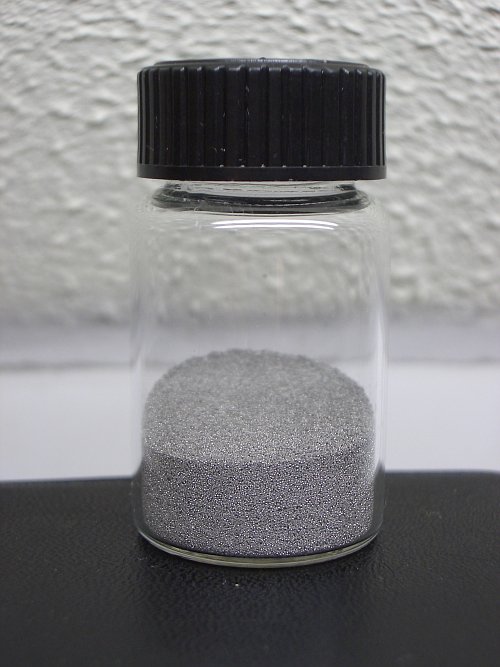
Benefits of Using TC11 Powder
Some of the main advantages of using TC11 over other alloy options:
High strength: 1300 MPa or higher tensile strength can be achieved in additively manufactured TC11 components. This is significantly stronger than stainless steel or aluminum alloys.
Toughness: Elongation over 10% ensures good damage tolerance even at high strength levels. This allows reliable performance in dynamic loads.
Lightweight: With a density around 4.7 g/cm3, TC11 parts are much lighter than steel, leading to significant weight savings.
Corrosion resistance: The high chromium content imparts excellent resistance to pitting, crevice and stress corrosion cracking in harsh environments.
High temperature stability: Can withstand temperatures up to 700°C without losing strength or corrosion resistance due to oxidation.
Biocompatibility: Non-toxicity and high corrosion resistance allows use for medical implants and devices.
Processability: TC11 can be laser powder bed fused, metal injected molded and wrought processed into various component shapes.
With its versatile properties, TC11 powder enables lighter, stronger and more reliable parts critical in demanding applications across sectors.
TC11 Powder Specifications
TC11 powder for AM processes needs to conform to strict specifications related to composition, particle size distribution, morphology, microstructure and impurity levels.
Chemical Composition
The powder composition must match standard TC11 grade limits for critical alloying elements:
Element | Weight % |
---|---|
Aluminum | 3.5-4.5% |
Chromium | 7.5-8.5% |
Molybdenum | 1.5-2.5% |
Zirconium | 3.5-4.5% |
Tin | 1.5-2.5% |
Oxygen, nitrogen and carbon are limited to ≤ 0.20% each. Hydrogen content should be less than 100 ppm. The balance is titanium. Meeting the chemistry specs ensures achieving required properties in the final part.
Particle Size Distribution
Most laser powder bed fusion machines work best with powder in the size range of 15-45 microns. Common size distributions include:
- D10: 10 μm
- D50: 25-35 μm
- D90: 40-55 μm
Finer powders can improve resolution but reduce flowability. Coarser powders may not pack well during spreading and produce poorer surfaces.
Powder Morphology
- Spherical, smooth powder particles with minimal satellites are preferred.
- Irregular, angular powder can negatively affect powder bed density, flowability and part quality.
- Satellite particles attached to main particles also disrupt powder spreading and density.
Microstructure
- Gas atomized and PREP powders have refined, homogeneous microstructures ideal for AM.
- HDH powders can contain coarser, inhomogeneous microstructures.
Impurities
Impurities like surface oxide layers, adsorbed gases and contaminants can impair powder properties. Rigorous analysis and checks are needed to control impurity levels.
Meeting all specification requirements for TC11 powder is critical for AM process stability, part quality and mechanical performance.
Suppliers of TC11 Powder
Some of the major global suppliers offering TC11 titanium alloy powder for additive manufacturing include:
Supplier | Production Method | Particle Sizes | Additional Services |
---|---|---|---|
AP&C | Gas atomization | 15-45 μm | Custom alloys, R&D |
Tekna | Plasma atomization | 15-45 μm | Toll processing |
Carpenter Additive | Gas atomization | 15-106 μm | Part qualification, HIP |
Praxair | Gas atomization | 15-53 μm | Process development |
LPW Technology | Gas atomization, HDH | Up to 106 μm | Material testing |
Sandvik Osprey | Gas atomization | Up to 150 μm | Spherical analyzers |
Pricing: Price can vary from $100-500 per kg based on order volume, powder grade, particle size distribution, production method etc.
Lead Times: Stock inventory is limited. Typical delivery times are 3-6 months for gas atomized powder and 6-12 months for plasma atomized powder.
Minimum Orders: Trial orders under 10 kg are possible but large orders over 100 kg get better pricing.
Quality Checks: Powder should come with composition and particle size distribution data, MSDS, SEM images and other test reports.

Installation and Operation of TC11 Powder-Based AM Machines
Installing and operating metal AM equipment that utilizes TC11 powder requires attention to safety, procedures and parameters for quality outcomes.
Facility Requirements
- Stable temperature, humidity and ventilation
- Fire safety and explosion prevention systems
- Protection from metallic powder hazards
- Dust management and powder storage protocols
Machine Installation
- Install machine as per OEM guidelines securing all modules
- Calibrate sensors, optics, mechanisms and controllers
- Test safety systems like emergency stops, alarms, fire safety
- Establish power, inert gas and cooling water connections
Workflow
- Parameter selection guided by PBF model, TC11 properties and part geometry
- Sieving and mixing powder batches to meet particle specifications
- Spreading uniform powder layers with recoating system
- Laser scanning strategy optimized for desired microstructure
- Minimizing thermal stresses and distortion during build
- Part detachment from plate, powder evacuation and cleanup
Personnel Training
- Operating procedures, safety protocols and maintenance basics
- Quality management using design rules, parameters, metallography, testing
- Powder handling, machine setup, build optimization, post-processing
With trained staff and robust operating practices, TC11 AM systems can deliver high productivity and process consistency.
Maintenance of TC11 Powder AM Machines
Consistent preventive maintenance along with proper machine operations is key to maximizing uptime and performance consistency for TC11 AM systems.
Daily/Weekly Checks
- Inspect major modules like lasers, optics, scanners for damage
- Monitor powder levels and other consumables
- Clean build chamber and platforms to avoid contamination
- Test recoater blade and sensors to identify wear
- Check leakages in cooling, hydraulic and inert gas lines
- Confirm electrical grounding and calibration of instrumentation
Periodic Maintenance
- Replace filters according to schedule
- Lubricate and replace worn components like bearings, pistons
- Inspect chain and gear mechanisms, realign/replace if needed
- Test emergency stop, safety doors, alarms and interlocks
- Validate process monitoring sensors and calibration
- Inspect laser optics and windows, replace if deteriorated
Annual Overhaul
- Disassemble critical modules for internal inspection
- Preventive replacement of components prone to wear/failure
- Hardware and software upgrades to latest version
- Full testing and recalibration of instrumentation
- Test builds to verify performance after maintenance
Proactive maintenance paired with sound operating practices ensures maximum powder bed fusion system availability and performance for TC11 parts.
How to Select a TC11 Powder Supplier
Choosing a TC11 powder supplier for additive manufacturing requires evaluating several factors to find one that reliably meets quality and performance needs.
Product Quality
- Powder composition within specified TC11 limits
- Consistent particle size distribution in ideal range
- Spherical morphology with minimal satellites
- Low levels of oxide and other impurities
- Test data for critical powder characteristics
Technical Capability
- Staff expertise in titanium alloy powder production
- Stringent quality control during manufacturing
- Range of in-house characterization equipment
Manufacturing Process
- Gas atomization or plasma process for optimal quality
- Batch-to-batch consistency and reproducibility
Testing and Certification
- ISO 9001 compliant quality management system
- Powder batches supported by test reports
- Certifications demonstrating product quality
Order Fulfillment
- Ability to meet requested delivery times and quantities
- Willingness to accept small trial orders
- Order tracking and status updates
Customer Service
- Technical assistance for application requirements
- Responsiveness to requests and issues
- Ability to customize particle size or composition
Evaluating powder suppliers on above parameters minimizes risks and helps ensure high, reliable TC11 powder quality.
Pros and Cons of TC11 Powder for Additive Manufacturing
TC11 has many benefits but also some limitations to factor while considering it for AM applications.
Advantages
- Increased strength and hardness versus Ti6Al4V
- Excellent corrosion and oxidation resistance
- Higher service temperatures up to 700°C
- Lower density than steel for lightweight parts
- Proven biocompatibility for medical uses
- Available from multiple reputable suppliers
Disadvantages
- More expensive than Ti6Al4V powder
- Lower tensile ductility than Ti6Al4V
- Requires hot isostatic pressing (HIP) post-processing
- High reactivity of titanium powders presents safety issues
- Limited data available compared to more established alloys
Ideal Applications
- Aerospace and automotive components needing high strength
- Critical static parts able to undergo HIP treatment
- Biomedical implants with complex geometries
- Chemical/petrochemical hardware exposed to corrosion
Less Suitable Applications
- Highly dynamic components requiring ultra-high ductility
- Very large parts limited by AM build chamber size
- Components difficult to HIP due to sealed internal cavities
- Cost-sensitive applications where Ti6Al4V can suffice
Overall, TC11 offers higher performance than Ti6Al4V in many aspects, justifying its use where design requirements are challenging.
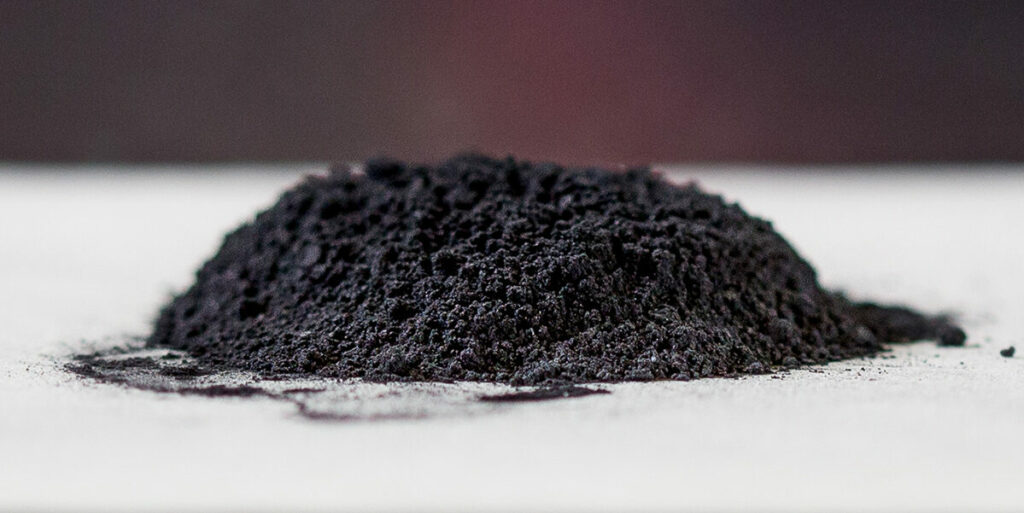
FAQ
Q: What particle size range of TC11 powder is optimal for laser powder bed fusion?
A: 15-45 microns is recommended, with a D50 of 25-35 microns ideal for most printer models. Finer powders can cause issues with spreading and flowability.
Q: Does TC11 alloy require stress relieving post-processing?
A: Yes, stress relieving at 700°C for 2 hours followed by air cooling is usually necessary to minimize cracking and distortion. Hot isostatic pressing also further enhances properties.
Q: What is the typical surface roughness as-built from TC11 powder?
A: With optimized AM process parameters, surface roughness under 10 microns Ra is achievable. Some finishing like abrasive flow machining may still be required.
Q: What is the recommended layer thickness for printing TC11 powder?
A: 20-50 microns is suggested, with 30 microns being a common choice. Thinner layers improve resolution but substantially increase build time.
Q: Are there composition variants of TC11 alloy with higher strength or ductility?
A: TC18 (Ti-5Al-5Mo-5V-3Cr) offers higher tensile strength while TC17 (Ti-5Al-2Sn-2Zr-4Mo-4Cr) offers higher ductility versus TC11.
Q: Does unused TC11 powder from AM machines retain its properties?
A: With proper storage in an inert environment, TC11 powder can typically be reused up to 10-20 times before significant property degradation occurs.
Q: What is the typical as-built density achieved with TC11 parts?
A: Density above 99.5% is readily achievable. Hot isostatic pressing can further eliminate internal voids and pores to maximize density.
Q: What are some recommended post-processing steps for TC11 AM parts besides stress relieving?
A: Machining, abrasive flow machining, shot peening, laser polishing, and coating deposition are often used depending on application requirements.