Imagine a material that’s incredibly strong yet surprisingly lightweight, shrugging off corrosion like a seasoned warrior. That’s the magic of Ti-6Al-4V powder, a game-changer in the world of advanced manufacturing. But what exactly is this wonder material, and how is it revolutionizing countless industries? Buckle up, because we’re about to embark on a journey into the fascinating world of Ti-6Al-4V powder.
Production Methods of Ti-6Al-4V Powder
Ti-6Al-4V powder isn’t your average sprinkle on a cupcake. It’s a meticulously crafted material derived from titanium, a naturally occurring element known for its impressive strength-to-weight ratio. Here’s a peek behind the curtain of the production process:
- The Plasma Atomization Process: Picture a molten stream of titanium alloy being blasted with a high-velocity plasma torch. This intense heat breaks the liquid down into tiny, rapidly solidifying droplets. These droplets then cool and solidify into spherical particles – the magic of Ti-6Al-4V powder!
- Gas Atomization: Similar to plasma atomization, but instead of a plasma torch, an inert gas like argon is used to break down the molten metal. This method offers good control over powder size and morphology.
- Hydride-Dehydride (HDH) Processing: This multi-step process involves converting titanium sponge into a metal hydride, crushing it into a powder, and then removing the hydrogen through a high-temperature vacuum process. While less common, HDH offers excellent powder purity.
Each method has its own advantages and disadvantages. Plasma atomization is ideal for high production volumes, while gas atomization provides finer control over particle size. HDH processing offers the highest purity but is a more complex and expensive method.
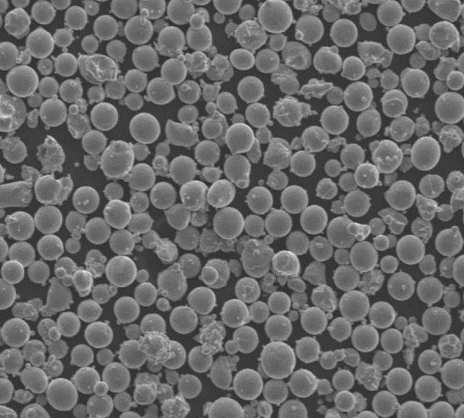
Applications of Ti-6Al-4V Powder
Ti-6Al-4V powder isn’t just sitting on a shelf waiting for its moment to shine. It’s actively transforming industries thanks to its unique properties:
- Aerospace: Ever wondered why those sleek airplanes seem to defy gravity? Ti-6Al-4V powder plays a crucial role. Its exceptional strength-to-weight ratio allows for lighter aircraft structures, translating to increased fuel efficiency and longer flight ranges. Imagine a fighter jet that can stay airborne for hours longer, or a commercial airliner that uses less fuel, making both environmental and economic sense.
- Medical Implants: For those requiring life-saving implants, Ti-6Al-4V powder offers a biocompatible solution. Its excellent corrosion resistance ensures the implant lasts for years, minimizing the need for revision surgeries. Think of a hip replacement that feels natural and functions flawlessly, allowing patients to regain their mobility and quality of life.
- Automotive: The quest for lighter, more fuel-efficient vehicles is a constant battle. Ti-6Al-4V powder is emerging as a champion in this fight. By replacing heavier components with lighter, stronger titanium parts, car manufacturers can shave off precious pounds, leading to better fuel economy and a more enjoyable driving experience.
- Consumer Goods: From high-end bicycles to sporting goods, Ti-6Al-4V powder is finding its way into everyday products. Imagine a bike frame that’s incredibly strong yet light enough to conquer any climb, or a baseball bat with explosive power packed in a manageable weight. The possibilities are endless!
These are just a few examples of how Ti-6Al-4V powder is revolutionizing various fields. As additive manufacturing techniques continue to evolve, we can expect even more innovative applications for this remarkable material.
Performance Characteristics of Ti-6Al-4V Powder
So, what exactly makes Ti-6Al-4V powder such a powerhouse? Let’s delve into its key performance characteristics:
- High Strength-to-Weight Ratio: Remember that analogy about airplanes defying gravity? It all boils down to this property. Ti-6Al-4V powder boasts exceptional strength for its weight, making it ideal for applications where both robustness and lightness are crucial.
- Excellent Corrosion Resistance: Imagine leaving a metal object outside for years and it still looking pristine. That’s the beauty of Ti-6Al-4V powder’s corrosion resistance. This makes it perfect for applications like medical implants and marine equipment, where exposure to harsh environments is inevitable.
- Biocompatibility: For those who rely on medical implants, biocompatibility is paramount. Ti-6Al-4V powder’s biocompatible nature ensures the body readily accepts the implant, minimizing the risk of rejection.
- Formability: Imagine sculpting a complex shape out of metal. That’s the magic of formability. Ti-6Al-4V powder exhibits good formability, making it suitable for intricate designs in additive manufacturing processes like 3D printing. This allows for the creation of lightweight yet strong components with complex geometries, pushing the boundaries of design and functionality.
- Machinability: Not all heroes wear capes – some wear drill bits! When it comes to machining finished parts from Ti-6Al-4V powder, machinability is key. While it’s a robust material, advancements in machining techniques and tooling allow for efficient and precise shaping of the final product.
It’s important to note that these properties aren’t created equal. There can be trade-offs depending on the specific production method and post-processing techniques used. For instance, plasma atomized powder might offer higher strength due to its slightly coarser morphology, while gas atomized powder could provide better ductility due to its finer particle size.
Understanding these nuances is crucial for manufacturers to select the optimal Ti-6Al-4V powder for their specific application requirements.
Advantages and Considerations of Ti-6Al-4V Powder
While Ti-6Al-4V powder boasts an impressive list of advantages, it’s essential to consider all aspects before diving headfirst.
Advantages:
- Lightweight: Compared to traditional materials like steel, Ti-6Al-4V powder offers significant weight savings. This translates to numerous benefits depending on the application. In aerospace, lighter aircraft structures mean increased fuel efficiency and longer flight ranges. In automotive, weight reduction leads to better fuel economy and improved performance.
- High Strength: Don’t be fooled by its lightness. Ti-6Al-4V powder packs a serious punch in terms of strength. This makes it ideal for applications demanding high structural integrity, such as medical implants and aerospace components.
- Corrosion Resistance: Imagine a material that laughs in the face of rust and corrosion. That’s Ti-6Al-4V powder for you! Its exceptional resistance to corrosion ensures components last longer and perform reliably in harsh environments, making it perfect for marine equipment and chemical processing applications.
- Biocompatibility: As mentioned earlier, Ti-6Al-4V powder plays a vital role in medical implants due to its biocompatible nature. The human body readily accepts this material, minimizing the risk of rejection and ensuring a smooth recovery process for patients.
- Design Freedom: Additive manufacturing techniques like 3D printing unlock a world of design possibilities with Ti-6Al-4V powder. Complex geometries and lightweight structures become a reality, pushing the boundaries of innovation in various industries.
Considerations:
- Cost: There’s no denying that Ti-6Al-4V powder is a premium material. The production process and the inherent value of titanium itself contribute to a higher cost compared to some traditional materials. However, the long-term benefits like increased lifespan, improved performance, and weight savings can often outweigh the initial investment.
- Processing Complexity: Working with Ti-6Al-4V powder requires specialized equipment and expertise in additive manufacturing techniques. Compared to traditional manufacturing methods, the process can be more complex, demanding a higher level of technical know-how.
- Post-Processing: The magic doesn’t stop after printing with Ti-6Al-4V powder. Additional post-processing steps like hot isostatic pressing (HIP) are often necessary to achieve the desired mechanical properties and eliminate any potential internal defects.
The key takeaway? While Ti-6Al-4V powder offers a plethora of advantages, it’s crucial to weigh the cost considerations and processing complexities against the specific application needs.
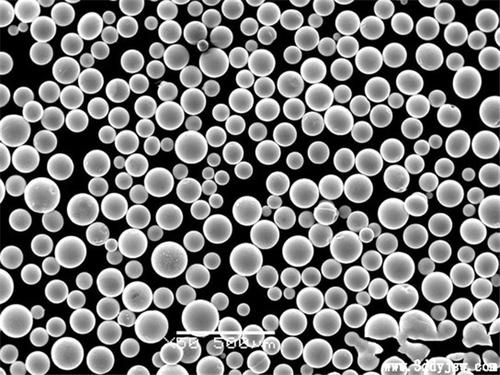
FAQ
Q: What are the different types of Ti-6Al-4V powder available?
A: Ti-6Al-4V powder can be categorized based on the production method used. Plasma atomized, gas atomized, and HDH processed powders are the most common types, each offering slight variations in particle size, morphology, and properties.
Production Method | Advantages | Considerations |
---|---|---|
Plasma Atomization | High production volume, Cost-effective | Coarser particle size, May require additional processing |
Gas Atomization | Finer particle size, Improved ductility | Lower production volume, Slightly higher cost |
HDH Processing | Highest purity | Complex and expensive process |
Q: How strong is Ti-6Al-4V powder compared to other materials?
A: Ti-6Al-4V powder exhibits impressive strength for its weight. Here’s a comparison to some common materials:
- Steel: While steel offers superior raw strength, Ti-6Al-4V powder can achieve comparable strength at a significantly lower weight. This makes it a compelling choice for applications where weight reduction is crucial.
- Aluminum: Aluminum is known for its lightness, but it falls short of Ti-6Al-4V powder in terms of strength. For applications demanding both light weight and high structural integrity, Ti-6Al-4V powder takes the lead.
- Polymers: While polymers offer good weight savings, they generally can’t compete with the strength of Ti-6Al-4V powder. This makes titanium the preferred choice for components requiring high mechanical loads.
It’s important to remember that strength can vary depending on the specific processing techniques used. For instance, hot isostatic pressing (HIP) can further enhance the strength of Ti-6Al-4V powder by eliminating internal voids and improving overall material integrity.
Q: Is Ti-6Al-4V powder safe for human implants?
A: Yes, Ti-6Al-4V powder is considered a biocompatible material, meaning the human body generally tolerates it well. This makes it a leading choice for various medical implants, such as hip replacements, knee joints, and dental implants. The biocompatibility minimizes the risk of rejection and ensures a smooth integration with the body’s tissues.
Q: How is Ti-6Al-4V powder used in additive manufacturing?
A: Additive manufacturing techniques like 3D printing unlock the true potential of Ti-6Al-4V powder. The powder is fed into the 3D printer layer by layer, allowing for the creation of complex, lightweight structures that would be impossible with traditional manufacturing methods. This opens doors for innovative designs in aerospace, medical, and automotive industries.
Q: What is the future outlook for Ti-6Al-4V powder?
A: The future of Ti-6Al-4V powder is bright! As additive manufacturing technology continues to evolve, we can expect even wider adoption of this remarkable material. Advancements in powder production methods and post-processing techniques are likely to further improve its properties and cost-effectiveness. This will pave the way for even more innovative applications across various industries, pushing the boundaries of design and functionality.
In conclusion, Ti-6Al-4V powder is a game-changer in the world of advanced materials. Its unique combination of strength, lightness, corrosion resistance, and biocompatibility makes it a valuable asset for countless applications. As technology advances and costs become more competitive, we can expect to see Ti-6Al-4V powder play an even greater role in shaping the future of manufacturing and design.