Overview of Titanium Alloy Powders
Titanium alloys are widely used in aerospace, medical, marine and other demanding applications due to their high strength-to-weight ratio, corrosion resistance, biocompatibility and ability to withstand extreme environments.
In powder metallurgy and additive manufacturing, titanium alloy powders can be selectively melted or sintered layer-by-layer to fabricate complex, lightweight components with superior mechanical properties matching or exceeding traditionally processed wrought alloys.
Common titanium alloys available in powder form include:
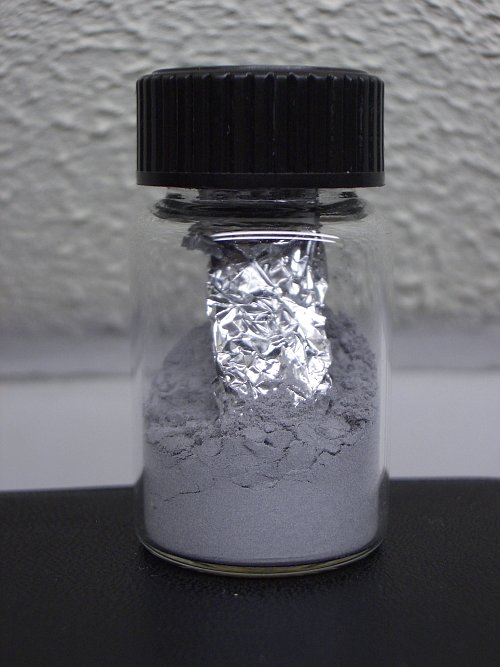
Titanium Alloy Powder Composition
Titanium alloys used in powder metallurgy contain mainly titanium, with alloying elements like aluminum, vanadium, iron, molybdenum and others:
Alloy | Composition |
---|---|
Ti-6Al-4V (Grade 5) | 6% aluminum, 4% vanadium, 0.25% (max) iron, 0.2% (max oxygen), balance titanium |
Ti-6Al-7Nb | 6% aluminum, 7% niobium, balance titanium |
Ti-555 (Ti-5Al-5Mo-5V-3Cr-0.5Fe) | 5% aluminum, 5% molybdenum, 5% vanadium, 3% chromium, 0.5% iron, balance titanium |
Ti-1023 (Ti-10V-2Fe-3Al) | 10% vanadium, 2% iron, 3% aluminum, balance titanium |
Titanium Alloy Powder Properties
Key characteristics of titanium alloy powders include:
Property | Significance |
---|---|
Particle size distribution | 30-150 μm for most additive processes; influences density, precision, surface finish |
Sphericity and shape | Highly spherical morphology improves flowability, packing density |
Purity | >99.5%, low oxygen important to achieve mechanical properties |
Flow rate | >25 s/50 g; affects recoating and layer uniformity |
Apparent density | >2.5 g/cc; relates to final part density |
Hausner ratio | <1.25; indicates powder flowability |
Applications of Titanium Alloy Powder
Additive manufacturing with titanium alloy powders spans diverse industries:
Industry | Applications |
---|---|
Aerospace | Structural airframe components, engine parts subjected to high temperatures |
Medical | Orthopedic and dental implants, prosthetics, surgical instruments |
Automotive | Connecting rods, turbocharger wheels, valves and valve springs |
Chemical | Heat exchangers, valves, pipes and reaction vessels |
Petroleum | Downhole tools for corrosive, high pressure environments |
Specifications for Titanium Alloy Powder
Key standards for composition, impurities and contamination in titanium alloy powders:
Standard | Powder Grades Covered |
---|---|
ASTM B348 | Grade 1 to Grade 48 wrought titanium alloys |
ASTM F67 | Unalloyed, alpha-beta and beta titanium for surgical implants |
ASTM F2924 | Ti-6Al-4V for additive manufacturing |
ASTM F3001 | Ti-6Al-4V ELI (extra low interstitial) for AM |
Suppliers of Titanium Alloy Powders
Many established companies manufacture titanium alloy powders for additive manufacturing globally:
Company | Grades Offered | Pricing |
---|---|---|
AP&C | Ti-6Al-4V, Ti-6Al-4V ELI | $350-$500 per kg |
TLS Technik | Ti-6Al-4V, Ti-6Al-7Nb, Ti-5Al-5Mo-5V-3Cr | $250-$450 per kg |
Tekna | Ti-6Al-4V ELI, Ti-6Al-7Nb, Custom alloys | $400-$600 per kg |
Metalysis | Ti-6Al-4V, Ti-6Al-4V ELI, Ti-64, Custom alloys | $300-$450 per kg |
Comparison Between Titanium Alloy Powders
Key differences between the most common titanium alloys Ti-64 and Ti-64 ELI:
Parameter | Ti-6Al-4V (Ti-64) | Ti-6Al-4V ELI |
---|---|---|
Oxygen level | Up to 0.20 wt% | Below 0.13 wt% |
Iron level | Up to 0.30 wt% | Below 0.25 wt% |
Mechanical strength | High | Medium |
Ductility | Medium | Very high |
Fatigue resistance | Medium | Very high |
Fracture toughness | Medium | High |
Cost per kg | Lower | Higher |
Benefits of Additive Manufacturing With Titanium Alloy Powder
Key advantages offered by AM processes using titanium alloy powder feedstock:
- Ability to produce lightweight, customized topology-optimized geometries
- Significant reduction in raw material waste compared to subtractive techniques
- Does not require expensive tooling, dies or machining setups
- Parts show equivalent or better fatigue resistance and fracture toughness over cast and wrought
- High strength-to-weight ratio ideal for aerospace component design
- Graded compositions and advanced alloy blends can tailored easily
- Just-in-time manufacturing possible with low minimum order quantities
Challenges Associated With Additive Manufacturing Using Titanium Alloy Powders
Some limitations need consideration for adopting titanium AM across industries:
- High material cost due to energy-intensive extraction and powder processing
- Removal of residual stresses to prevent distortion and cracking post-build
- Additional HIP and finish machining often necessary to achieve critical tolerances
- Reactive powder handling needs protective atmospheres and procedures
- Since shrinkage is difficult to predict accurately, design compensation is essential
- Optimization of thermal parameters and scan strategies needed to limit anisotropy
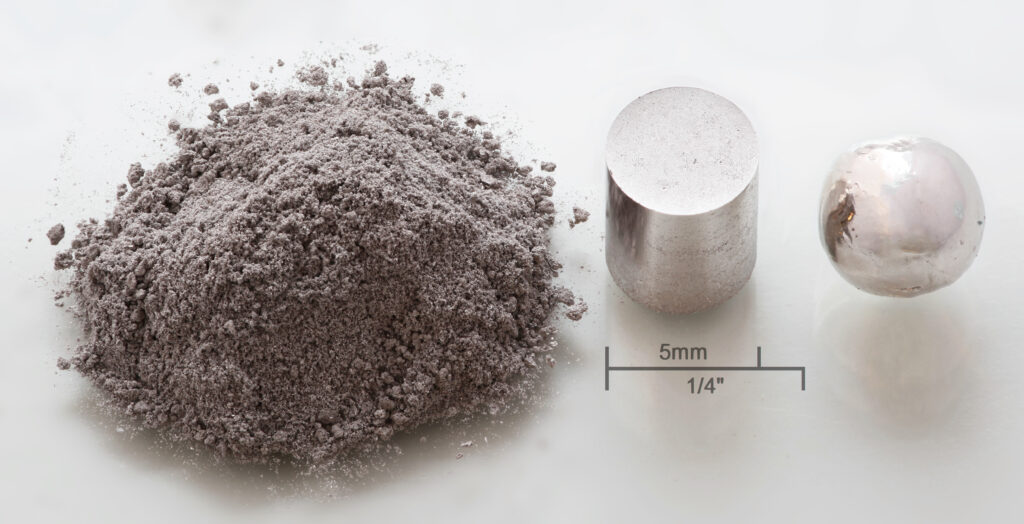
FAQ
Q: Which titanium alloy powder is most widely used in AM?
A: Ti-6Al-4V (Grade 5) accounts for over 50% of all titanium additive manufacturing, owing to its excellent mechanical properties like tensile strength, fatigue life and corrosion resistance. Ti-6Al-4V ELI is also popular for its superior ductility and fracture toughness.
Q: Does additive manufacturing with titanium alloys give porous or dense parts?
A: Both are achievable based on processing parameters. While high density above 99% giving properties equivalent to bulk alloys is preferred for structural applications, controlled porosity between 30-70% allows orthopedic implants to promote tissue in-growth leading to better osseointegration over solid metal.
Q: What particle size distribution is optimal for titanium alloy powders in AM?
A: Around 20-63 microns is commonly used, with the ideal minimum particle size over 15 microns to limit pyrophoricity risks. Though finer powders below 30 microns allow better resolution and surface finish, extremely fine particles can compromise powder flow leading to poor recoating and density issues during printing.
Q: How are unused titanium alloy powders reused after additive manufacturing?
A: They are passed through classifiers to sieve out usable fractions meeting size and shape specifications. These are then mixed with some fresh powder in controlled ratios maintaining bulk chemistry. Such recycling after multiple reuses lets titanium powder attain an optimal spherical shape and flowability that gives superior layer uniformity during builds.
Q: Why does the build chamber need an inert argon atmosphere while printing titanium alloys?
A: Titanium is highly reactive at elevated temperatures, readily absorbing gases like oxygen, nitrogen and hydrogen leading to embrittlement and mechanical property degradation. Keeping an oxygen level below 25 ppm is recommended. An inert gas environment prevents contamination of high purity titanium alloys during additive printing.
Q: What post-processing methods are used on additively manufactured titanium components?
A: Support removal using NaOH or HCl baths, stress-relieving heat treatment, HIP and finish-machining are routinely employed. Other advanced techniques include surface texturing, collagen micro-patterning of implants, hardening via shot peening, surface anodization and applying bioactive coatings using thermal spray or laser cladding.
Q: What are some best practice guidelines for handling titanium alloy powders safely?
A: Using intrinsically safe electrical equipment, minimizing static charge buildup via grounding, storage in original inert containers and avoiding atmosphere exposure are vital. Face masks and protective apparel are needed when handling. Firefighting gear must be worn with special media like graphite powder ready for reactive powder fires.