Overview of titanium aluminide powder
Titanium aluminide powder is an advanced engineering material made from titanium and aluminum. It has gained significant interest in recent years due to its excellent combination of high strength, low density, and ability to withstand high temperatures.
Some key details about titanium aluminide powder:
- Composition: Titanium combined with aluminum, as well as other alloying elements like niobium or molybdenum
- Production methods: Gas atomization, plasma rotating electrode process (PREP), mechanical alloying
- Particle sizes: From 10 microns to 150 microns typically
- Common phases: Gamma (γ) and alpha-2 (α2) titanium aluminide intermetallic phases
- Density: 3.7 – 4.25 g/cm3, much lower than titanium or steel alloys
- Melting point: Over 1,250°C
Titanium aluminide offers properties superior to conventional titanium alloys for lightweight, high-temperature applications such as aerospace components. However, it also has challenges like low room-temperature ductility and fracture toughness. Ongoing research aims to optimize processing methods and alloy additions to expand commercial usage.
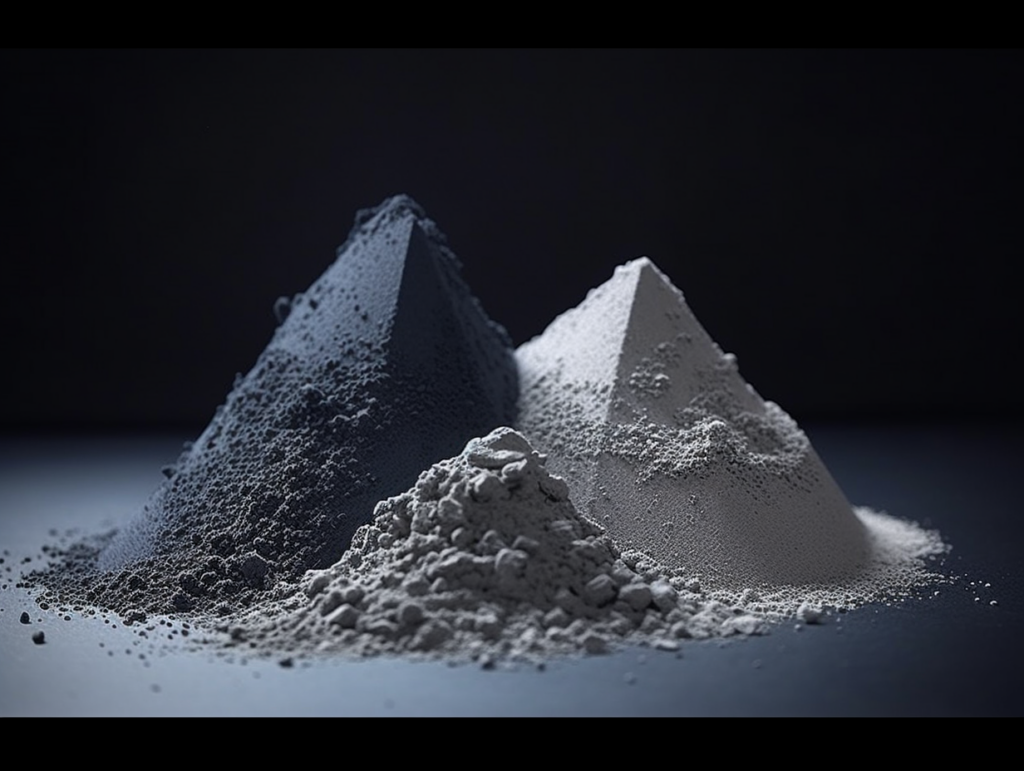
Composition
The main constituents of titanium aluminide alloys are titanium, aluminum, and other alloying elements:
Element | Weight % |
---|---|
Titanium (Ti) | 50 – 80% |
Aluminum (Al) | 10 – 25% |
Niobium (Nb) | 0 – 10% |
Molybdenum (Mo) | 0 – 5% |
Chromium (Cr), Vanadium (V) | 1% each max |
The main intermetallic phases present are:
- Gamma titanium aluminide (γ-TiAl): Face centered tetragonal crystal structure, ordered phase combination of titanium and aluminum. Primary interest for high temperature applications.
- Alpha-2 titanium aluminide (α<sub>2</sub>-Ti<sub>3</sub>Al): Hexagonal crystal structure, ordered phase of titanium and aluminum. Confers room temperature ductility but has lower high-temperature strength.
By optimizing the ratios between γ-TiAl, α<sub>2</sub>-Ti<sub>3</sub>Al, and other phases, properties can be tailored for specific needs.
Production Methods
Titanium aluminide powder can be produced using advanced powder metallurgy processes:
Method | Description | Particle sizes | Advantages |
---|---|---|---|
Gas atomization | Molten alloy stream breakup using gas jets | 10 – 150 μm | High powder yields, range of sizes |
Plasma rotating electrode process (PREP) | Centrifugal disintegration of rotating molten electrode | 45 – 150 μm | Control over powder sizes and quality |
Mechanical Alloying | Repeated cold welding and fracturing of powder particles | 10 – 100 μm | Alloying flexibility, composite powders |
Gas atomization uses pressurized gas jets directed at a melt stream to produce rapidly solidified spherical powders. Plasma PREP utilizes an electrode being melted by plasma torches, disintegrating by centrifugal forces. Mechanical alloying does not melt but creates composite particles by mechanochemistry. Each has unique advantages in titanium aluminide production.
Properties
Titanium aluminides offer a rare balance of useful mechanical and physical properties:
Property | Details | |
---|---|---|
Strength | Tensile strength | 500 – 1100 MPa |
0.2% Yield strength | 400 – 900 MPa | |
Density | Specific gravity | 3.7 – 4.25 g/cm3 |
Thermal | Melting point | Over 1250°C |
Coefficient of thermal expansion | 11 – 13 x 10-6 K-1 | |
Ductility | Room temperature elongation | 0.5 – 2% |
The combination of high strength, low density, and retention of strength at over 600°C makes titanium aluminides very attractive to replace nickel alloys and steels. However, issues like low ductility, fracture resistance, and fatigue strength need addressing.
-
CM247LC Powder | Nickel Alloy Powder
-
0# Pure Nickel powder
-
NiCoCrAlY alloys powders
-
Rene 142 alloy-Rene Powder
-
Haynes 25 Haynes Powder
-
Best Hastelloy C-22 Powder-High temperature alloy Powder for 3D Printing
-
Best Hastelloy C-276 Powder-High temperature alloy Powder for 3D Printing
-
Best Hastelloy N Powder-High temperature alloy Powder for 3D Printing
-
Best Hastelloy B Powder丨High temperature alloy Powder for 3D Printing
Applications
The excellent strength-to-weight ratio and heat resistance enables several potential applications:
Industry | Components | Benefits |
---|---|---|
Aerospace | Turbine blades, disks, shafts | Weight savings, thrust increase |
Automotive | Turbocharger wheels, valves | Higher power, fuel efficiency |
Industrial | Radial compressor wheels, blades | Weight savings, longer life |
Titanium aluminide delivers substantial weight savings over nickel superalloys in rotating high-temperature components like turbine blades or compressor wheels while providing equal or greater component life.
Automotive turbocharger wheels made with this material can reach higher rotational speeds and boost pressure thanks to reduced weight. It also finds increasing usage in industrial radial flow compressors and turbines in the oil and gas industry.
Specifications
Titanium aluminide products for commercial usage need to meet established standards:
Attribute | Details |
---|---|
Powder sizes | 10 μm to 150 μm |
Particle size distribution | D10: 20 μm, D50: 45 μm, D90: 105 μm (typical) |
Powder grades | Grade 5 (Ti-47Al-2W-0.5Si), Grade 23 (Ti-47Al-3.5(Nb,Mn,Cr)-0.2Si) |
Standards | ASTM B863, AMS 4999 |
Finished part standards | AMS 4928, 4967, 4979 |
Having standardized test methods allows reliable evaluation and comparison between powder lots and finished components made from various titanium aluminide alloys. Parts can achieve aerospace-level qualification through established AMS grades to be used in flight hardware.
Suppliers and Pricing
A number of specialist powder producers offer titanium aluminide for Additive Manufacturing or alloy development:
Brand | Manufacturer | Powder cost (USD/kg) |
---|---|---|
CronalTM TiAl | GfE Metalle und Materialien GmbH | 500 |
AMP 48-2-2 | ATI Powder Metals | 460 |
Ti-48Al-2Nb-2Cr | Carpenter Technology | 510 |
Ti-47Al-2W-0.5Si | Praxair | 450 |
Ti-Al6-Nb7 | TLS Technik GmbH | 600 |
Cost per kilogram is still very high compared to traditional titanium alloys due to low powder volumes. However specialty grades optimized for Additive Manufacturing are driving increased commercial adoption.
Comparison
Titanium aluminides demonstrate substantial benefits but also some downsides relative to competing high-temperature alloys:
Ti Aluminides | Nickel Alloys | Ti Alloys | |
---|---|---|---|
Density | Lower | Higher | Comparable |
Strength at >600°C | Higher | Lower | Lower |
Room temperature ductility | Lower | Higher | Higher |
Cost | Higher | Lower | Comparable |
Nickel superalloys retain decent ambient properties but become much weaker at high temperatures. Conventional titanium alloys are limited below 600°C. Titanium aluminides uniquely don’t lose strength even up to 800°C. Optimizing the mix of downsides and benefits leads to targeted applications in aerospace.
Pros and Cons
There are compelling advantages with titanium aluminide along with certain enduring limitations:
Advantages
- Up to 35% lower density than nickel alloys
- Strength and modulus retention at over 600°C
- High temperature creep resistance
- Compatibility with titanium manufacturing
- Adds less weight than composites
Disadvantages
- Brittle behavior and low ductility
- Poor fracture toughness
- Susceptibility to fatigue cracking
- Joining difficulties
- Rapid air oxidation over 750°C
- Higher cost than titanium alloys
Steady materials development has begun expanding the temperature range of acceptable properties while improving environmental resistance. Costs are also gradually declining with expanded usage in commercial aerospace engines.
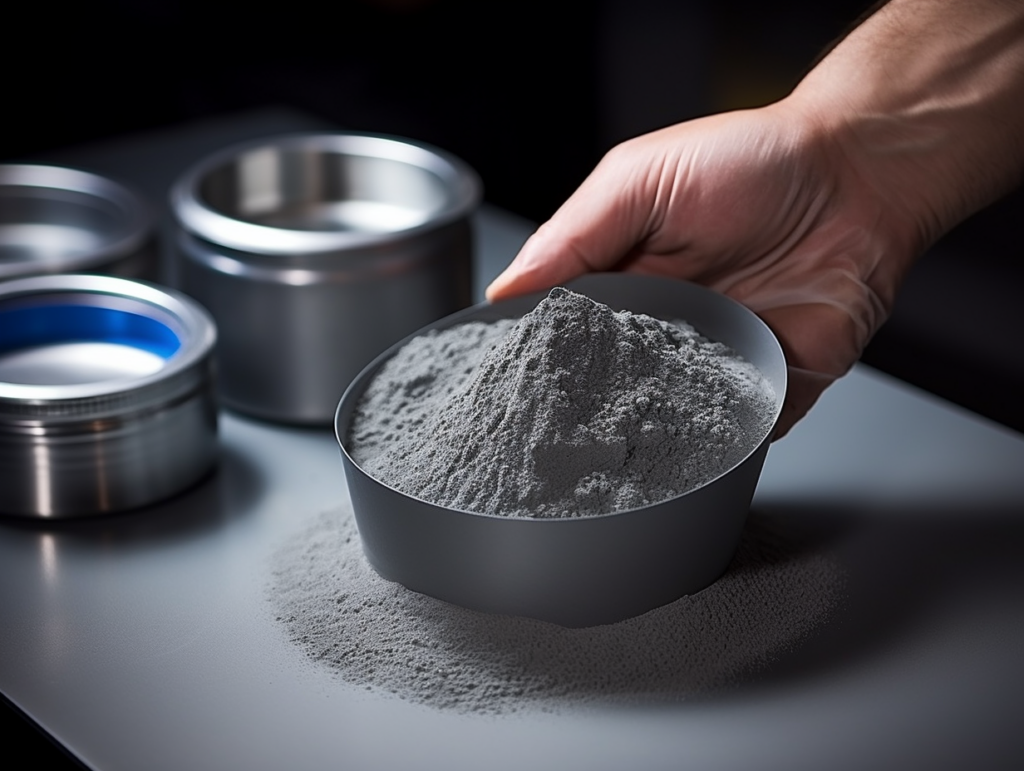
FAQs
Question | Answer |
---|---|
How heavy is titanium aluminide compared to steel or titanium? | With a density of 3.7 – 4.25 g/cm3, titanium aluminide is 35% lighter than nickel alloys and over 40% lighter than steels while having comparable or higher strengths. |
Can you 3D print with titanium aluminide powder? | Yes, titanium aluminide alloys are very suited to powder bed fusion or directed energy deposition additive manufacturing methods offering expanded property optimization flexibility over cast and wrought products. |
What is titanium aluminide used for? | The excellent elevated temperature capabilities coupled with lower density versus nickel alloys makes titanium aluminide suitable for replacing components like turbine blades, turbocharger wheels and compressor components in aerospace, automotive and industrial applications. |
Is titanium aluminide brittle? | Unlike other lightweight alloys, titanium aluminides suffer from intrinsic brittleness due to their intermetallic nature, necessitating careful design and usage consideration to avoid premature cracking or fracture, especially under fatigue loads. |
How strong is titanium aluminide? | In optimum processed conditions, titanium aluminides can achieve tensile strengths over 1,100 MPa and yield strengths approaching 1,000 MPa at both room and high operating temperatures, making them the strongest lightweight metallic material option. |
Conclusion
With its rare blend of low density, retention of high-temperature strength and modulus, elevated temperature creep resistance, fatigue behavior, and oxidation resistance, γ-TiAl based titanium aluminides fulfill a unique materials technology niche.
Despite ongoing efforts to expand ductility and ambient temperature fracture toughness, the intrinsic brittleness of the intermetallic continues to limit more widespread adoption. Applications have focused on replacing heavier nickel alloys whenever the environmental resistance limitations can be addressed.
Powder metallurgy production paired with precise consolidate like Additive Manufacturing has expanded the envelope of usable mechanical properties like strength, damage tolerance and high-cycle fatigue behavior. This helps overcome prior barriers in commercialization.
Research into alloying additions, novel processing methods like additive manufacturing, and thermo-mechanical treatments aims to unlock the full potential of this advanced lightweight alloy family. Targeted gas turbine and automotive engine component substitution is driving early adoption today.