Overview of Titanium Based Alloy Powder
Titanium based alloy powder is a metal powder made from titanium mixed with other alloying elements like aluminum, vanadium, iron, and molybdenum. It offers exceptional strength, low density, high corrosion resistance, and biocompatibility. Titanium powders are widely used in aerospace, medical implants, automotive parts, sports equipment, and other applications needing lightweight, durable components.
The unique properties of titanium alloy powder stem from its crystalline structure. Alloying elements are added to pure titanium powder to enhance specific characteristics for different applications. The particle shape, size distribution, flowability, and microstructure of the powder can be tailored to optimize performance in additive manufacturing or powder metallurgy processes.
This guide provides a detailed overview of different types of titanium alloy powder, their properties, applications, suppliers, costs, standards, and more. It aims to help buyers select the right titanium powder for their manufacturing needs.
Titanium Alloy Powder Types
There are four main categories of titanium alloy powder:
Alloy Type | Key Alloying Elements | Characteristics |
---|---|---|
Alpha alloys | Aluminum, oxygen | Excellent corrosion resistance, stable at high temperatures |
Alpha-beta alloys | Aluminum, vanadium, molybdenum | High strength, moderate ductility |
Metastable beta alloys | Molybdenum, vanadium, iron, chromium | Heat treatable, high strength, good ductility |
Near-beta/beta alloys | Molybdenum, vanadium, niobium | Highest strength, moderate ductility |
The microstructure and resulting properties depend on the type and amount of alloying elements:
Aluminum increases strength and creep resistance at elevated temperatures in alpha and alpha-beta alloys.
Vanadium provides strength through solid solution strengthening and precipitation hardening. It stabilizes the beta phase in beta and near-beta alloys.
Iron is added to stabilize the alpha phase but can decrease ductility.
Molybdenum strengthens beta phase titanium alloys and improves creep resistance.
Chromium increases strength and high temperature properties.
Niobium stabilizes the beta phase at room temperature and enables precipitation hardening.
Applications of Titanium Alloy Powder
Titanium alloy powder is suitable for a wide range of applications:
Industry | Applications |
---|---|
Aerospace | Engine components, airframes, landing gear, fasteners |
Medical | Implants, surgical instruments, prostheses |
Automotive | Connecting rods, valves, springs, turbocharger wheels |
Chemical | Heat exchangers, reaction vessels, pipes and tubes |
Power generation | Steam and gas turbine blades, heat exchanger tubes |
Sporting goods | Golf clubs, tennis rackets, bicycles, hockey sticks |
Petrochemical | Seawater desalination plants, oil and gas drilling equipment |
The combination of high strength, low density, corrosion resistance, and biocompatibility makes titanium alloy powder ideal for critical structural parts needing reliability and performance.
Specifications and Standards
Titanium alloy powders are produced according to ASTM International standards that define the chemistry, particle size distribution, flow rate, and other quality parameters. Common specifications include:
- ASTM B348: Standard Specification for Titanium and Titanium Alloy Powders
- ASTM B939: Standard Specification for Titanium Alloy Powders for Coatings
- ASTM F1580: Standard Specification for Titanium and Titanium-6 Aluminum -4 Vanadium Alloy Powders for Coatings
- ASTM F3049: Standard Guide for Characterizing Properties of Metal Powders Used for Additive Manufacturing Processes
International standards organizations like ISO also provide titanium powder specifications:
- ISO 22068: Titanium powders for thermal spraying
- ISO 23304: Titanium alloy powders for additive manufacturing
Powder producers must continuously test their material and processes to ensure compliance with chemistry, particle size, morphology, flow rate, and contamination requirements in the standards.
Titanium Alloy Powder Characteristics
The composition, particle size distribution, morphology, microstructure, flowability, and contamination levels determine the quality and performance of titanium alloy powder:
Particle size: Influences density, quality, and accuracy in additive manufacturing. Fine powders below 100 microns are commonly used.
Morphology: Spherical, irregular, or mixed particle shapes affect powder flow and packing density. Satellite particles can cause defects.
Flowability: Measured by factors like angle of repose, Hausner ratio, and Hall flowmeter funnel tests. Critical for feeding during processing.
Microstructure: Alloy composition and production method determines the alpha, alpha-beta, or beta microstructures. Affects mechanical properties.
Oxygen/nitrogen content: Higher levels increase brittleness and porosity. Pyrophoric grades have very low oxygen content for reactivity and safety.
Metal impurities: Iron, chromium, nickel and other contaminants alter alloy characteristics. Tight control is needed.
Titanium Powder Production Methods
The four main production routes for titanium alloy powder are:
- Plasma atomization – A high energy inert gas plasma melts and atomizes the liquid metal into fine spherical powders with a controlled size distribution. Common for reactive alloys.
- Gas atomization – An inert gas disintegrates the liquid metal stream into powder. Less energy than plasma process. Irregular morphology.
- Rotating electrode process – An electric arc melts the wire feedstock and centrifugal forces disperse the molten droplets into powder. Cost-effective method.
- Hydride-dehydride process – Titanium hydride powder is first produced and then dehydrided to create brittle irregular titanium powder. Simple process used for low cost applications.
Atomization techniques allow close control over powder characteristics critical for high performance components.
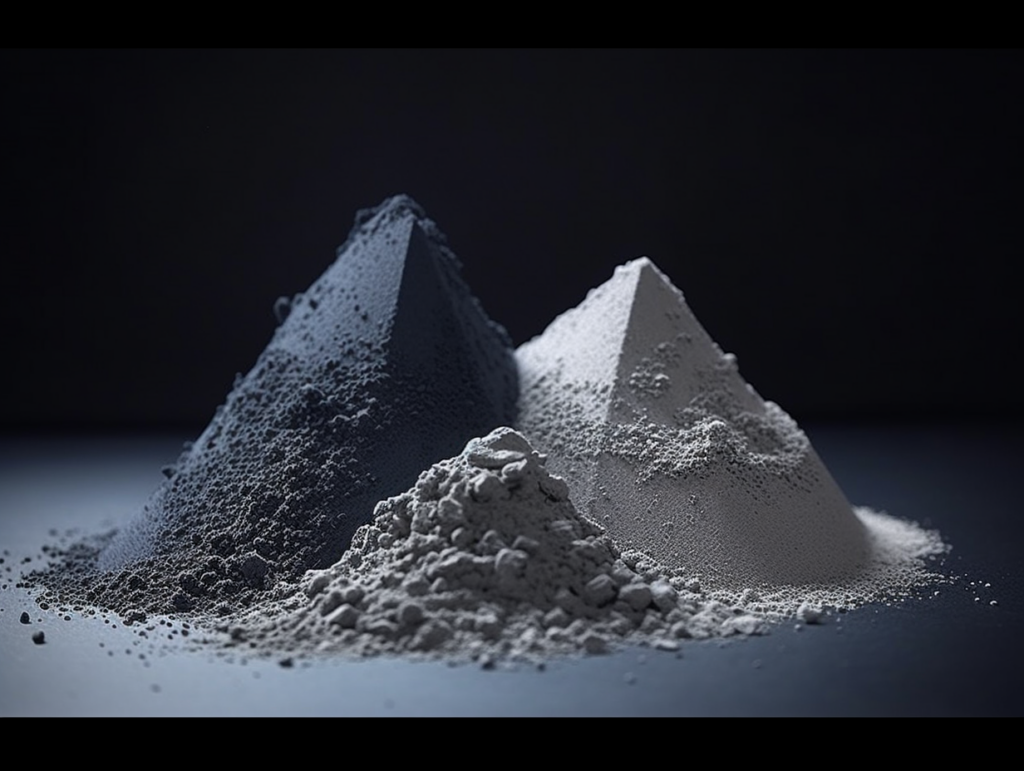
Titanium Alloy Powder Suppliers
Many companies supply titanium alloy powders for different applications and processing methods:
Supplier | Grades Offered | Production Method |
---|---|---|
AP&C | Ti-6Al-4V, Ti-6Al-4V ELI, Ti-6Al-4V Grade 23, Ti-6Al-4V Grade 5 | Plasma atomization |
Arcam AB | Ti-6Al-4V, Ti-6Al-4V ELI, Ti-64 Grade 5 | Plasma atomization |
Carpenter Additive | Ti-6Al-4V, Ti-6Al-4V ELI | Gas atomization |
CNPC POWDER | Ti-6Al-4V, Ti-6Al-4V ELI, Ti Grade 2, Ti Grade 5 | Plasma atomization |
GKN Powder Metallurgy | Ti-6Al-4V, Ti-6Al-4V ELI | Gas atomization |
LPW Technology | Ti-6Al-4V, Ti-6Al-4V ELI, Ti Grade 2, Ti Grade 5 | Plasma atomization |
Praxair | Ti-6Al-4V, Ti-6Al-4V ELI | Plasma atomization |
Sandvik Osprey | Ti-6Al-4V, Ti Grade 2, Ti Grade 5 | Gas atomization |
Tekna | Ti-6Al-4V, Ti-6Al-4V ELI | Plasma atomization |
Leading medical and aerospace brands use high quality powders from these producers for critical applications needing consistent properties and ultra-fine size control.
Titanium Powder Prices
Titanium alloy powder is more expensive than steels due to the complex extraction and processing:
Grade | Price Range |
---|---|
Ti-6Al-4V | $100-$500 per kg |
Ti-6Al-4V ELI | $150-$600 per kg |
Ti Grade 5 | $250-$1000 per kg |
Ti Grade 23 | $300-$1200 per kg |
Prices vary based on:
- Chemistry – Grades with tighter chemistry specifications for critical applications demand higher prices.
- Production method – Gas atomized and plasma atomized powders cost more than HDH powders.
- Particle size – Finer powders below 45 microns are more expensive than coarser sizes.
- Order volume – Large quantity orders over 1000 kg offer better discounts from suppliers.
- Processing – Prices are higher for spherical, flowable powders used in additive manufacturing versus irregular powders for press and sinter applications.
- Certifications – Aerospace grades with full traceability and QA as per AS9100 and ISO 9001 standards carry premium pricing.
- Exotic alloys – More complex proprietary titanium alloys developed for specialized applications are very expensive.
How to Select Titanium Powder Suppliers
Choosing a reliable titanium alloy powder supplier is critical. Here are key factors to consider:
- Experience – Look for manufacturers with decades of experience in titanium powder production technologies. This ensures process mastery.
- Quality systems – Suppliers should have ISO 9001, ISO 13485, AS9100 or other certifications to guarantee stringent quality control and testing.
- Production capacity – Partner with suppliers that can reliably meet your volume needs, now and in the future as your operations grow.
- Technical expertise – Powder producers should have in-house technical teams to collaborate on custom alloy development and advise you on suitable grades for your application.
- Industry reputation – Reputable suppliers are trusted by leading aerospace, medical, and industrial brands for their capabilities and performance track record.
- Safety – Assess their safety programs, material handling protocols, and compliance with hazardous material transportation regulations.
- Value-added services – Some suppliers offer additional benefits like inventory management, expedited shipping, and application prototyping support.
Prioritize titanium powder manufacturers with advanced production technologies, a broad product range, competitive pricing, and strong track record in your target industry.
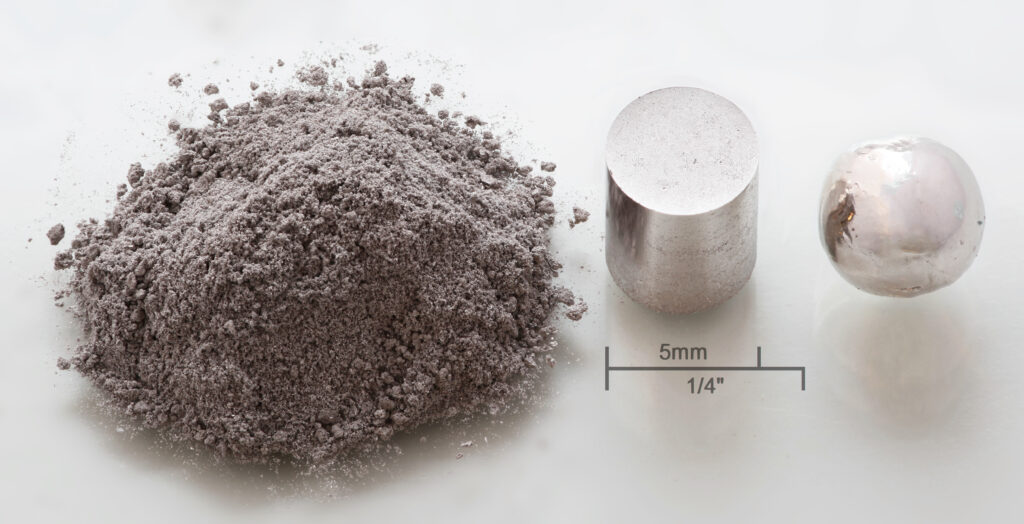
How to Choose Titanium Powder for Additive Manufacturing
Selecting the optimum titanium alloy powder is crucial for defect-free, high quality 3D printed parts. Follow these guidelines:
1. Match alloy to application
- Use Ti-6Al-4V for the best combination of strength, ductility and corrosion resistance.
- Choose Ti-6Al-4V ELI for higher ductility or Grade 5 for better strength and heat treatability.
- Specify ASTM standards like F2924 or F3001 to define chemistry and properties.
2. Spherical morphology for flowability
- Spherical powders spread evenly, pack densely, and flow smoothly. Gas or plasma atomization gives the best sphericity and flow.
3. Tight particle size distribution
- Distribution between 15-45 microns allows dense packing and good flow. Too wide a range causes segregation issues.
4. Low oxygen content
- Higher oxygen increases brittleness and porosity. Specify maximum levels below 0.20%.
5. Minimize fine satellites
- Satellites under 10 microns get trapped in powders, clog filters, and create defects.
6. Smooth surface texture
- Rough, porous powder particles trap gas and cause porosity during printing.
7. Match powder to printer requirements
- Consult printer manufacturer’s guidelines on compatible alloys, size range, shape and chemistry.
Choosing the right titanium alloy powder optimizes the printing process, part properties, performance, and production economics.
Installing and Operating Titanium Powder 3D Printers
Additive manufacturing with titanium alloy powder requires careful installation and operation for safe, high-quality prints. Follow these best practices:
Installation
- Install printer on a stable, vibration-free surface
- Ensure room temperature between 20-25°C for consistency
- Provide inert argon gas supply and ventilation as specified
- Install cooling water supply and chiller system
- Set up recycling systems for used powder
- Get humidity sensors to monitor levels below 50%
- Use antistatic flooring, grounding wires and ionizers
Operation
- Run initial test builds to optimize parameters
- Store and handle powder properly to prevent contamination
- Sieve powder before each build and discard satellites
- Follow OEM guidelines for build plate set up
- Monitor and control oxygen levels below 0.12%
- Clean and maintain all system components regularly
- Automate processes with MES and MOM software systems
- Analyze builds to fine-tune layer times, offsets and positions
- Adjust parameters as necessary based on quality checks
Thorough training, controlled conditions, and preventive maintenance ensure high, consistent print quality and optimize printer productivity.
Maintaining Titanium Powder Printers
Consistent maintenance is essential for peak performance, repeatable part quality, and long service life of titanium powder printers:
Component | Maintenance Activities | Frequency |
---|---|---|
Powder handling system | Inspect tubing, seals, valves, connectors | Weekly |
Powder storage containers | Check for leaks, moisture ingress | Monthly |
Sieving system | Inspect mesh, clean, replace as needed | Daily |
Build chamber | Clean optical sensors, windows, mirrors | Weekly |
Recoater | Check gap, alignment, blade wear | Daily |
Gas supply system | Leak tests, flow calibration | Quarterly |
Beam focusing optics | Clean lenses, calibration, alignment | Monthly |
Motors and drives | Lubricate bearings, inspect timing belts | Quarterly |
Beam emitting source | Tune and calibrate electron beam | Biannually |
Cooling system | Test water quality, inspect chillers | Annually |
Filtration system | Replace inert gas filters | After 200 print hrs |
Control systems | Install software and firmware updates | As released |
Safety sensors | Validate oxygen and temperature sensors | Monthly |
Preventive maintenance as per the OEM schedule is essential for maximizing printer availability, print consistency, and operational lifespan.
How to Choose Between Metal Powder Bed Fusion Printer Brands
Selecting the right powder bed fusion 3D printer for titanium alloys depends on weighing several factors:
Print quality and properties
- Part accuracy, density, surface finish, microstructure
- Mechanical properties like tensile and fatigue strength
Materials capabilities
- Range of titanium grades supported
- Compatibility with reactive and high temperature alloys
Productivity
- Build volume, speed, automation features
- Software workflow, digital tools, post-processing ease
Operating cost
- Powder use efficiency, recycling rate
- Labor, energy, and consumables cost per part printed
Reliability and uptime
- Printer robustness, longevity, serviceability
- OEM support services and responsiveness
Safety
- Powder and emissions handling
- Monitoring and control of oxygen level
Initial investment
- Printer hardware, accessories, peripherals
- Facility infrastructure and installation services
Scalability
- Production capacity growth potential
- Breadth of technology portfolio and application expertise
Leading printer brands for titanium alloys are EOS, GE Additive, Velo3D, Renishaw, Trumpf. Schedule demos, compare performance data, and calculate total cost of ownership when selecting your system.
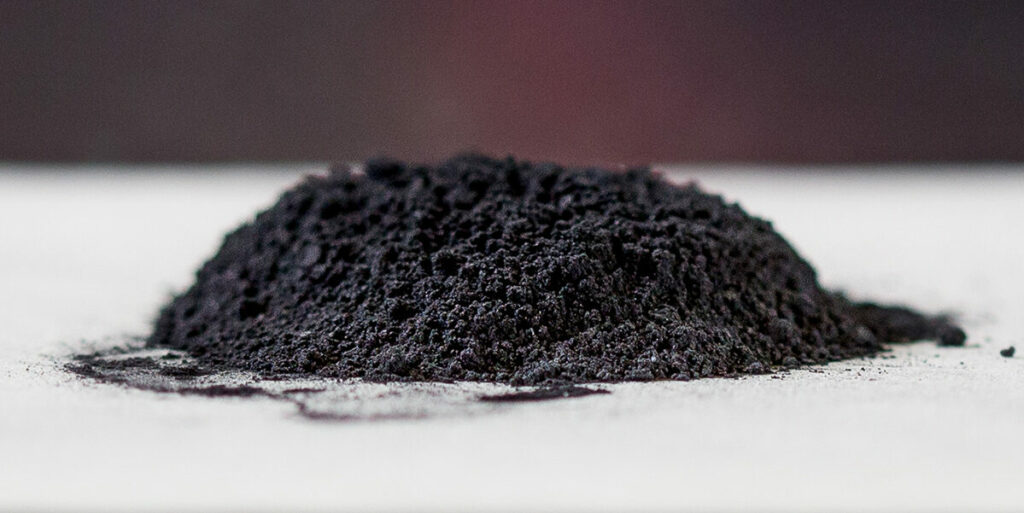
How to Design Parts for Metal Powder Bed Fusion 3D Printing
Designing parts specifically for additive manufacturing unlocks performance benefits and avoids manufacturing issues:
Benefits
- Consolidate assemblies into single complex parts
- Create lightweight organic shapes with lattices and thin walls
- Optimize material strength by aligning to load paths
- Integrate internal cooling channels and undercuts
Design Guidelines
- Use minimum wall thickness of 0.3-0.5mm to ensure fusion
- Design self-supporting geometries to avoid supports
- Include chamfers and radii for easy powder removal
- Orient part to minimize overhangs and downward facing surfaces
- Position part on base plate to minimize height and thermal stresses
- Design homogeneous wall thickness for even heating and cooling
- Allow access holes in hollow sections for unfused powder removal
- Account for shrinkage by scaling up part dimensions
Simulation and optimization tools like anisotropic lattice design, geometry analysis, thermal modeling, and machine learning algorithms enable designs only possible through AM.
Comparing Metal Injection Molding vs Metal 3D Printing
Metal injection molding (MIM) and metal 3D printing both produce complex parts from powder, but have distinct differences:
Parameter | Metal Injection Molding | Powder Bed 3D Printing |
---|---|---|
Materials | Stainless steel, tool steel, titanium alloys | Titanium, aluminum, nickel, cobalt alloys |
Part size | Up to 300mm | Up to 500mm |
Geometry | Draft angles needed, some design limits | No drafts required, more freedom |
Density | Up to 99% | Nearly 100% |
Accuracy | ±0.1% with high precision tooling | ±0.2-0.3% |
Surface finish | Smooth, high luster | Rougher finish, post-processing often needed |
Mechanical properties | Predictable, isotropic | Anisotropic, depends on build orientation |
Production method | High volume using mold tooling | Low to medium volumes, no tooling |
Lead time | Weeks for tooling before production | Hours to days for production |
Cost: MIM has high upfront costs for mold tooling but lower per-part cost at high volumes. AM has no tooling so is more economical at low to medium volumes.
Design: MIM requires draft angles while AM can produce complex shapes without drafts. AM enables lightweight lattice structures not possible with MIM.
Materials: MIM offers a wider range of materials including stainless steels and tool steels. AM is limited to reactive and high temperature alloys like titanium, nickel, and cobalt chrome.
Quality: MIM parts have excellent consistency and accuracy when using high precision tooling. AM accuracy depends on process control but can reach ±0.2% or better.
Post-processing: MIM parts need binder removal and sintering. AM parts need supports removed and may require hot isostatic pressing and machining.
Mechanical properties: MIM offers isotropic properties. AM parts are anisotropic due to layer-by-layer build with directional strengths.
Applications: MIM suits high volume automotive and consumer goods. AM is preferred for low volume complex metal parts for aerospace, medical, and industrial.
Lead time: MIM requires weeks for tooling before production. AM can build parts within hours or days without any tooling needed.
Supply chain: MIM depends on logistics of tooling, metal powder, polymer binders, and sintering capacity. AM uses only metal powder with in-situ sintering so streamlined supply chain.
Sustainability: AM has less material waste and energy use versus subtractive processes. But atomization of fine AM powder has environmental impacts.
In summary, MIM and AM both enable small complex metal parts but have intrinsic differences that make each method suitable for particular applications based on volumes, lead times, quality, and costs.
Titanium Powder Metallurgy Advantages and Limitations
Titanium powder metallurgy offers benefits but also has some limitations compared to wrought titanium:
Advantages
- Components with complex geometries can be produced
- Significantly reduces waste versus machining from solid
- Allows alloys difficult to process via ingot metallurgy
- Near-net-shape capability reduces machining
- Components can be sintered to full density and fine microstructure
- Mechanical properties exceed cast and match wrought material
- Lower energy consumption than primary extraction and processing
Limitations
- Higher material cost than aluminum and steels
- Limited to smaller part sizes than wrought processing
- Needs protective atmosphere during sintering
- Brittle hydride phase forms at low temperatures
- Residual porosity possible without hot isostatic pressing
- Reactive powders require special handling
- Distortion or growth during sintering
- Anisotropic shrinkage and properties
- Secondary machining often required
With continual improvements in powder quality and printing parameters, additive manufacturing helps overcome size, shape, and microstructure limitations of conventional powder metallurgy.
Titanium Powder Safety Precautions
Safety is critical when handling reactive titanium powders:
- Use inert gas gloves boxes to prevent air exposure during powder handling
- Worker exposure levels should adhere to OSHA Permissible Exposure Limit (PEL) of 15 mg/m3 for titanium dust
- Prevent powder ignition by controlling static discharge and maintaining below 30% oxygen
- Ground all equipment and use antistatic footwear, gloves, clothing
- Avoid accumulation of fine powder deposits to limit explosion hazards
- Provide proper ventilation and dust extraction systems
- Wear NIOSH-approved respirators to limit inhalation of fine particles
- Use particle filters in laser powder bed fusion machine chambers
- Install oxygen sensors and fire suppression systems
- Handle and store powders only in enclosed containers
- Follow regulations for transporting reactive hazardous materials
- Dispose of used powder properly as metallic waste; never discard in landfills
- Establish emergency response protocols for powder spills or fire
- Train all workers on powder flammability risks and proper handling procedures
With responsible handling and strict safety protocols, the risks of working with reactive titanium powders can be minimized.
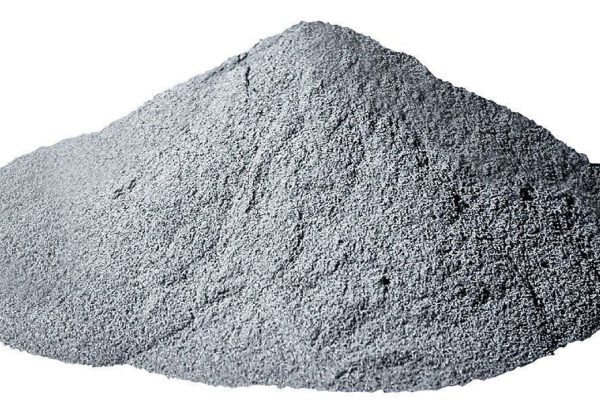
FAQs
Q: What is the main application for titanium alloy powder?
A: The aerospace industry accounts for over 60% of titanium powder consumption, using it to produce engine components, airframe parts, fasteners, and other critical lightweight structural parts needing extreme strength along with heat and corrosion resistance.
Q: Which titanium alloy grade is best for additive manufacturing?
A: Ti-6Al-4V is the most popular titanium alloy for AM due to its excellent combination of strength, ductility, fatigue resistance, and corrosion resistance. The ELI “extra low interstitial” version offers higher fracture toughness and impact strength needed for AM.
Q: What particle size range is optimal for titanium powder bed fusion?
A: A particle size range between 15-45 microns balances dense packing and smooth powder flow needed for defect-free printing. Anything below 10 microns can be problematic.
Q: How is titanium powder recycled after 3D printing?
A: After each printed layer, unfused surplus titanium powder is collected and sieved to remove large contaminants. The “used” powder can then be blended with virgin powder, thermal conditioned, and reused, reducing material costs.
Q: Why is flowability an important metric for metal printing powders?
A: Good powder flow and packing density ensures uniform, consistent layers during printing for part accuracy and quality. Measurement methods like angle of repose and Hall flowmeter funnel tests characterize flowability.
Q: How does oxygen content affect titanium powder quality?
A: Higher oxygen levels increase brittleness and lower ductility due to formation of brittle titanium oxides. For additive manufacturing, oxygen should be limited to 2000-3500 ppm for optimum mechanical performance.
Q: What causes anisotropic properties in 3D printed titanium parts?
A: Parts are stronger horizontally across each printed layer but weaker vertically between layers. This anisotropy is minimized by finer powder size, lower layer thickness, and optimizing build parameters.
Q: Why is gas atomized powder less suitable than plasma atomized powder for AM?
A: The lower energy gas atomization produces more irregular, elongated powder morphology versus highly spherical particles from plasma processes. This gives poorer powder flow and packing density.