Tungsten alloy powders refer to powder metallurgy grade tungsten metal powders blended with alloying elements like nickel, iron, copper, or cobalt. These powder mixes can be consolidated into high-density parts using pressing and sintering to yield superior mechanical properties beyond tungsten’s capabilities.
This guide details tungsten alloy powder compositions tailored for factors like hardness, toughness, erosion resistance, thermal behavior, electrical conductivity, etc. It also covers manufacturing methods, product standards, applications, global suppliers, pros and cons, and frequently asked questions about these materials.
Overview of Tungsten Alloy Powders
Tungsten alloys leverage tungsten’s intrinsic properties like high density, strength, melting point, thermal/electrical conductivity, and radiation shielding. Alloying additions then augment select characteristics to meet application needs.
Benefits of Using Tungsten Alloys Include:
- Enhanced tensile and yield strengths
- Improved elongation and impact toughness
- Better high-temperature plasticity
- Higher recrystallization temperature
- Increased corrosion/erosion resistance
- Modified thermal expansion coefficients
- Optimized for weighting or balancing
Tailored tungsten alloy powders serve as feedstock for manufacturing critical components via powder metallurgy processing:
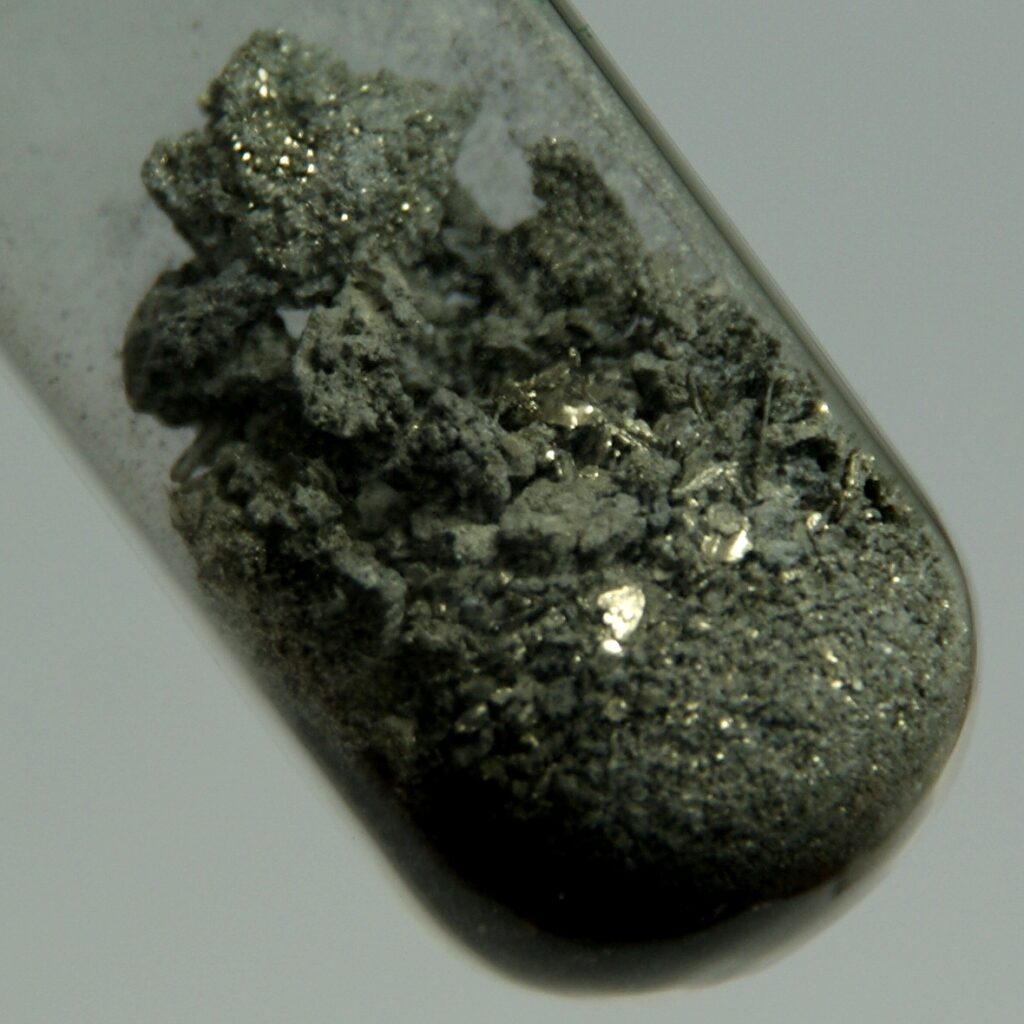
Compositions of Tungsten Alloy Powders
Tungsten alloy powders span a wide spectrum from W-Ni and W-Fe on the toughened ductile end to W-Cu offering the best erosion resistance.
Popular compositions and their notable attributes include:
Common Tungsten Alloy Powder Compositions
Alloy | Composition | Key Characteristics |
---|---|---|
Tungsten Nickel | W-Ni: 95W, 4Ni, 1Fe | Enhanced toughness & strength |
Tungsten Iron | W-Fe: 97W, 3Fe | High toughness & ductility |
Tungsten Copper | W-Cu: 97W, 3Cu | Superior erosion resistance |
Tungsten Silver | W-Ag: 97W, 3Ag | Excellent electrical conductivity |
Tungsten Cobalt | W-Co: 97W, 3Co | High-temperature strength |
These powders can also be customized with small additions of rhenium, titanium, zirconium or carbon to further augment properties like creep resistance, hardness, or grain stabilization.
Properties of Tungsten Alloy Powders
Key traits of popular tungsten alloy powder compositions consolidated into parts are contrasted below:
Properties of Tungsten Alloy Powder Parts
Property | Units | W-Ni <br> 92W, 6Ni, 2Fe | W-Cu <br> 97W, 3Cu | W-Fe <br> 94W, 6Fe |
---|---|---|---|---|
Density | g/cm<sup>3</sup> | 18.0 | 17.2 | 18.3 |
Hardness | Hv | 340 | 380 | 330 |
Strength | MPa | 1,240 | 1,100 | 1,150 |
Elongation | % | 18 | 3 | 12 |
Electrical Resistivity | μΩ·cm | 7.8 | 6.3 | 19 |
Thermal Conductivity | W/m·K | 140 | 175 | 32 |
Maximum Service Temp | °C | 800 | 1,000 | 1,150 |
This illustrates how strategic alloying enables optimizing tungsten for hardness, toughness, thermal behavior, or conductivity to suit end use conditions.
Manufacturing Process
Tungsten alloy powder preparation involves blending, consolidation into powder compacts, liquid-phase sintering, and final mechanical processing.
Key Manufacturing Steps
- Powder Blending – Measured proportions of tungsten powder and alloying elements are wet mixed in a lined ball mill using ceramic or plastic milling media. This composite powder serves as feedstock.
- Compaction – The feedstock powder undergoes cold/warm isostatic pressing or uniaxial die compaction to produce green parts near finished shape.
- Liquid Phase Sintering – Green compacts are sintered at 1400-1600°C using a partial pressure furnace with hydrogen gas. The lower melting alloying elements liquefy, infiltrating pores and consolidating a dense microstructure.
- Mechanical Processing – Final parts may undergo Hivec, hot upset forging or machine tooling to dimensional accuracy, surface finish, or other properties.
Advanced methods like metal injection molding offer greater complexity, precision, and flexibility for intricate commercial component shapes demanded today.
Applications of Tungsten Alloy Powders
Thanks to their unrivaled high-density credentials, tungsten alloys see diverse use across defense, aviation, motorsports, medical, and other major sectors:
Industry Applications of Tungsten Alloy Parts
Industry | Typical Applications |
---|---|
Defense | Radiation shielding, penetrators, ordnance |
Aviation | Turbine blades, helicopter rotors, nosecone ballast |
Automotive | Tire studs, balance weights, driveshaft weights |
Motorsports | Racing car ballast weights |
Medical | Gamma knife shielding, prostate brachytherapy seeds |
Electronics | Heat sinks, wire screens, electrical contacts |
New tungsten alloy variants and consolidation methods continue augmenting applicability across critical performance components globally.
Grades and Specifications
International standardized grades for tungsten alloy powders include:
Tungsten Alloy Powder Standards
Grade | Alloy | Specification |
---|---|---|
TP10N | 92W, 6Ni, 2Fe | WT-10Ni |
TP20N | 90W, 8Ni, 2Fe | WT-20Ni |
TFP20 | 88W, 8Ni, 4Fe | |
TC15 | 97W, 3Cu | WT-15Cu |
TFS10 | 90W, 6Fe, 4Ni | WT-10FeS |
These cover common alloy variants like W-Ni-Fe, W-Cu and W-Fe-Ni systems used across industrial, aerospace, automotive, and ordnance applications.
Global Manufacturers and Supricing
As tungsten availability has tightened recently with supply chain pressures, prices of tungsten alloy powders have correspondingly risen.
Indicative Pricing Ranges for Tungsten Alloy Powders
Grade | Price per kg |
---|---|
92W 6Ni 2Fe | $90 – $150 |
97W 3Cu | $70 – $130 |
94W 6Fe | $80 – $140 |
Leading global manufacturers of tungsten alloy powders include:
Prominent Tungsten Alloy Powder Manufacturers
Company | Headquarters |
---|---|
Wolfram Company | USA |
Buffalo Tungsten | USA |
EdgeTech Industries | USA |
HC Starck Solutions | Germany |
Xiamen Tungsten | China |
Many further toll process customer supplied tungsten materials into alloy powder forms. Get in touch with major industry suppliers for pricing particular to your annual volume and quality needs.
Pros and Cons
Advantages of Using Tungsten Alloy Powders
- Tailorable properties like hardness, strength, toughness
- Temperature resistance exceeding alloy alternatives
- Highest density among metals aids weight, balance
- Economical powder metallurgy consolidation
- Favorable machining characteristics
- Recyclable materials approach
Limitations of Tungsten Alloy Powder Usage
- Higher cost component of finished parts
- Limited supply and production scale
- Brittle behavior restricts component design
- Challenging to machine certain alloy grades
- Surface finishing requirements
Comparison with Tungsten Carbide Powder
As a sister refractory material, tungsten carbide offers much greater hardness and wear resistance thanks to tungsten forming hard carbide phases with carbon additions.
However, tungsten carbide grades lack intrinsic ductility. This necessitates cobalt binder phases compromising temperature capabilities. Tuning WC-Co composite mixes allows balancing hardness, toughness and strength.
Contrasting Key Properties of WC-Co and Tungsten Alloys
Property | Tungsten Alloy | Tungsten Carbide |
---|---|---|
Hardness | Up to 400 Hv | 1300-1600 HV |
Toughness | Ductile | Brittle |
Strength | Up to 1,500 MPa | Up to 3,400 MPa |
Max. Temp | Up to 1,250°C | 500-800°C |
Corrosion Resistance | Excellent | Carbide prone to chemical wear |
Applications | Radiation shielding, penetrators | Cutting tools, dies, bearings |
This outlines distinct selection criteria hinging on mechanical wear needs versus high temperature demands.
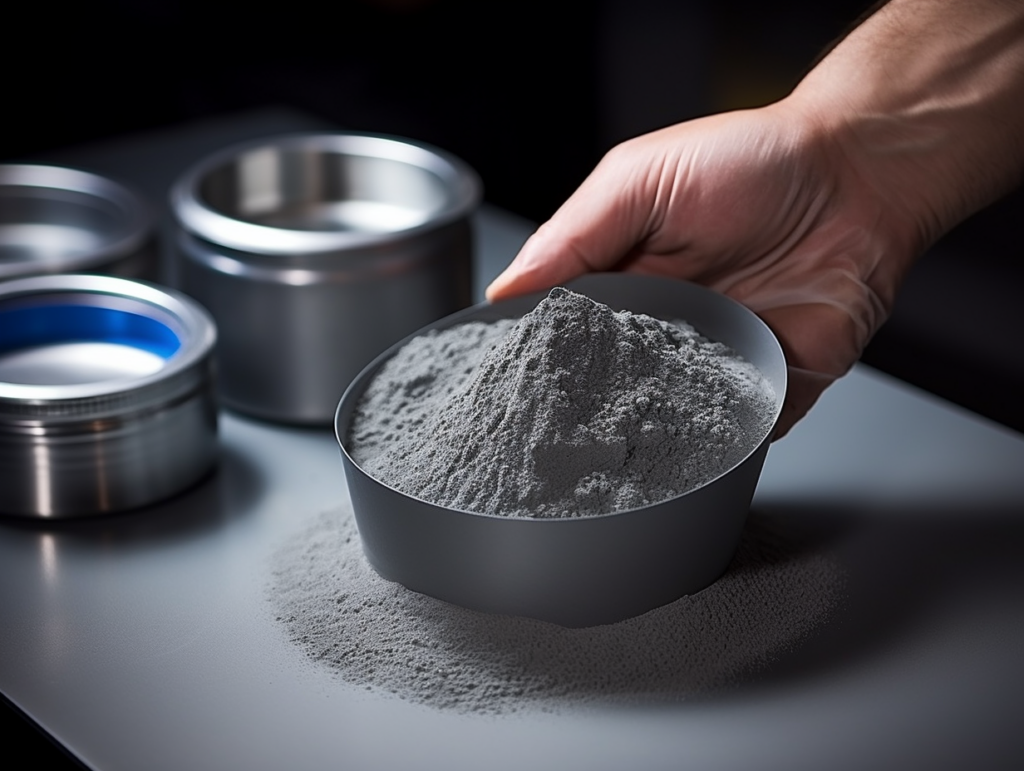
FAQ
How do tungsten alloy powders compare to tungsten metal powders?
Tungsten alloy powders leverage strategic blending with alloying elements like nickel, iron, or copper. This augments attributes like tensile ductility, high temperature plasticity, recrystallization resistance and shock toughness compared to pure tungsten.
Why are tungsten alloys used in radiation shielding?
Tungsten alloys combine the highest density among metals with strong mechanical properties. This allows for fabricating precise shielding geometries protective against dangerous gamma or neutron radiation yet structurally sound given minimal volumes to work with.
What are some examples of tungsten alloy applications?
Tungsten alloys see broad use across aviation, defense, automotive, motorsport, medical, electronics and other industries – ranging from radiation shields, aircraft rotors, wheel weights, penetrators, heat sinks, to prosthetic implants among others. Their unique density, strength and conductivity find niche roles.
Are tungsten alloys expensive materials?
Yes, being refined from scarce tungsten ores, coupled with specialized powder metallurgy processing, tungsten alloys carry higher costs per unit weight. However the unique benefits often justify applications where no alternatives meet technical performance or safety needs. Recycling routes help recover these valuable materials.
How to work with tungsten alloy powders when developing new applications?
Collaborating early with expert suppliers of tungsten alloy powders ensures you select the optimal blend to meet target properties. They can tailor these composite mixes, facilitate prototyping of powder compact samples, and scale up fabrication for testing form-fit-function before committing to high volume production.
Conclusion
Tungsten alloy powders present a versatile materials platform to appropriate tungsten’s pedigree of superior density, hardness, melting point and conductivity – augmented by strategic alloying approaches for factors like optimizing tensile ductility, high-temperature strength, creep resistance or electrical resistivity.
Ongoing R&D into specialized tungsten alloys coupled with additive manufacturing promises to further broaden adoption spanning critical aerospace components to radiation shielding across next-gen defense, space and medical applications where fail-safety remains paramount.
Powder metallurgy fabrication processes enable reliable access to affordable finished parts in volume. With supply chain pressures, recycling routes will also close the materials loop. All factors considered, tungsten alloys retain a bright future thanks to their unparalleled density-compensated mechanical properties and refractory nature.