Tungsten carbide (WC) powder refers to fine particles consisting of tungsten metal cemented with carbon atoms. Tungsten carbide exhibits extreme hardness, wear resistance, high density, and thermal/electrical conductivity. These unique properties make tungsten carbide widely used across industrial tooling, mining, aerospace, automotive, and electronic applications.
This guide covers different grades of tungsten carbide powder, their composition, manufacturing methods, applications, specifications, pricing details from suppliers, pros and cons, and answers common questions on integrating cemented tungsten carbide into components via powder metallurgy techniques.
Types of Tungsten Carbide Powder
There are several primary tungsten carbide powder classifications based on characteristics like carbon content, particle size, manufacturing method and purity levels:
Type | Description | Typical Compositions |
---|---|---|
Simple carbides | Most common formulation, contain only tungsten carbide (WC) and carbon binder matrix | Carbon types: Co, Ni, Fe |
Complex carbides | Carbides of tantalum (TaC) or titanium (TiC) added into the tungsten-carbon matrix for increased hardness and heat resistance | WC + (TaC or TiC) particles in cobalt binder |
Micrograin carbides | Ultrafine nano-scale carbide particles 20-200 nanometers (for higher hardness) cemented using cobalt | WC nano particles + 3% Co |
Cermets | Hard tungsten carbide particles dispersed throughout a softer application specific metal matrix | WC in a copper, iron or bronze binder matrix |
Additionally, powder particle size distributions like coarse, fine and ultra-fine grades mean optimizing raw material flowability, density ratios, and surface finish capabilities for different tungsten carbide product manufacturing processes.
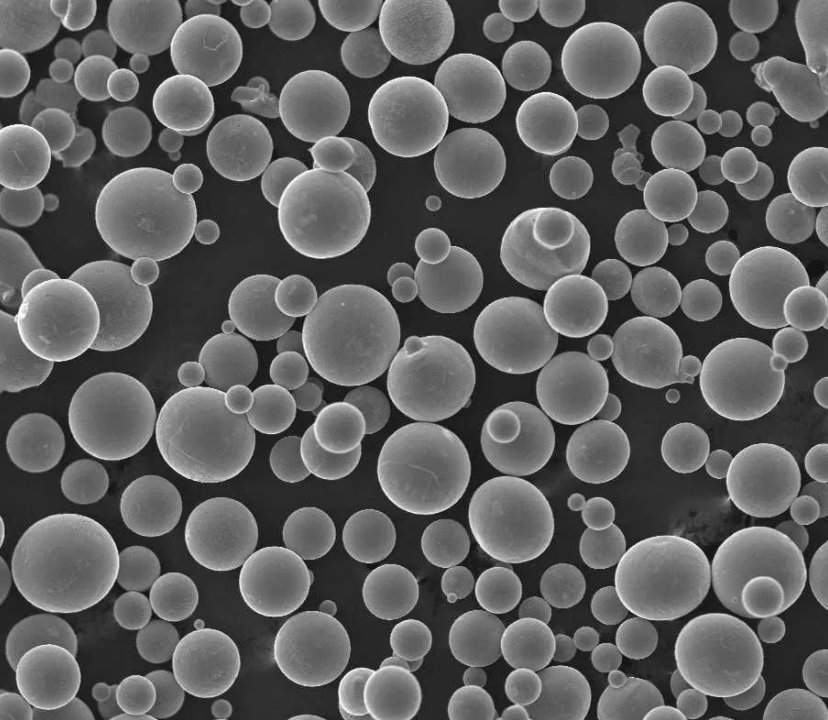
Production Methods
Common techniques to produce tungsten carbide powder on industrial scales:
Method | Description | Typical Output |
---|---|---|
Carbothermic reduction | Tungsten ore is reduced using gas mixture of carbon monoxide and hydrogen at high temperature into tungsten metal powders | Irregular flattened grains with higher oxygen levels |
Spray conversion process | Liquid tungsten compound aerosolized and reacted with carbon | Spherical agglomerated batches up to 3 tons/hour |
Fusion method | Pure tungsten metal ignited in carbon beds into WC which is crushed and milled | Blocky angular powder particles |
Sol-gel | Tungstates precipitated from aqueous mixtures form tungsten gels for calcining | Very small nano scale particles possible |
The size range, shape and purity of carbide powder required depends greatly on part manufacturing process and application performance requirements.
Properties of Tungsten Carbide Powder
Key characteristics that make tungsten carbide so versatile for fabricating extremely hard, durable tooling and components include:
Property | Characteristics | Benefits |
---|---|---|
Extreme hardness | Vickers 1300-2400 HV range, among hardest manmade materials | Withstands abrasion as cutting tools, drilling bits, wear surfaces |
Heat resistance | Retains hardness > 1500 HV at temperatures near 1,000 °C | Allows dry machining without coolants, resists deformation in high heat uses |
Corrosion resistance | Chemically inert to most mineral acids and organic compounds | Dependable long term in exposed industrial environments |
High density | Nearly double the density of steel | Maximizes mass in applications like counterweights or ballast |
Thermal/electrical conductivity | As conductive as common metals like steel | Dissipates heat rapidly during machining, ideal for electrical contacts |
These combined traits make tungsten carbide more durable at smaller sizes than other materials – contributing to miniaturization and efficiency gains in precision couplings, seals, pumps, valves and other demanding applications.
Applications of Tungsten Carbide Powder
Major industry uses of tungsten carbide components made from cemented powder include:
Segment | Common Applications | Benefits |
---|---|---|
Machining tools | Cutting tool inserts, end mills, circular saws | Hardness maintains sharp cutting edge |
Dies and tooling | Forming dies, stamping punches, rollers | Withstands repeated high pressure and abrasion |
Mining and construction | Drill bits, rock drills, excavation tools | Durability against cracks or fractures in extreme environments |
Automotive | Fuel injection nozzles, valve seat inserts | Resists wear from high velocity gas and fluid flows |
Aerospace | Aircraft gun barrel linings, radiation shielding | Density efficienctly absorbs X-ray and gamma rays |
Electronics | Electrical contacts, vacuum tube filaments | Conductive with low electronic emission rates |
The unique combination of hardness, toughness, heat tolerance and density make tungsten carbide indispensable across these critical industries – facilitating broader trends like faster CNC machining, expanded oil/gas drilling ranges and improved fuel economy.
-
CM247LC Powder | Nickel Alloy Powder
-
0# Pure Nickel powder
-
NiCoCrAlY alloys powders
-
Rene 142 alloy-Rene Powder
-
Haynes 25 Haynes Powder
-
Best Hastelloy C-22 Powder-High temperature alloy Powder for 3D Printing
-
Best Hastelloy C-276 Powder-High temperature alloy Powder for 3D Printing
-
Best Hastelloy N Powder-High temperature alloy Powder for 3D Printing
-
Best Hastelloy B Powder丨High temperature alloy Powder for 3D Printing
Specifications and Grades
International standards for consistent identification of tungsten carbide powder properties:
Standard | Common Grades | Definitions |
---|---|---|
ISO 513 K | K01, K05, K10, K20 | Mean tungsten carbide grain size in microns |
ASTM B771 | WC-6Co, WC-10Co | Percentage of cobalt binder matrix |
JIS R 1601 | FFF, FFF-F, FFF-S | Japanese code defining grain size and shape |
DIN 6580 | D25-D150 codes | German oversize grain percentage conventions |
Higher cobalt content increases part toughness but lowers hardness. Ultrafine grain powders favor wear resistance but sacrifice impact strength. Work closely with manufacturers to select grade optimized for specific loading needs.
Suppliers and Pricing
Supplier | Grades | Price Range |
---|---|---|
Buffalo Tungsten | General/Aerospace/Electronic Grades | $50-200 per pound |
Midwest Tungsten | WC-Co Grades from 1-20% binder levels | $60-220 per pound |
Global Tungsten | ISO K01 – K40 grain sizes | $90-250 per pound |
NanoBoron Prom | Nano grain WC for high hardness | $200+ per pound |
Costs range widely $50 per lb. for common general purpose unrefined grades up to $250+ per lb. for ultrafine nano-grain tightly specified powder optimized for medical or aerospace applications. Prices also fluctuate based on availability and raw tungsten market spot trends.
Remember – buy the grade specified for application, balancing hardness against toughness strength, not just by initial cost.
Pros and Cons
Pros | Cons |
---|---|
Exceptional hardness at high temperatures | Challenging/expensive to fully densify green compacts in sintering |
Resists abrasion | Brittle after sintering, prone to cracks under loads |
Biologically inert and non-toxic | Raw materials costs fluctuate based on Chinese export quotas driving market volatility |
Enables miniaturization of wear components | Specific handling precautions needed given reactivity risks at particle scale |
Combined strength + conductivity unique | Requires cobalt binders procuring issues given geopolitical supply chain risks |
While demanding production processes from powder metallurgy to finishing means tungsten carbide can cost over 20X more than steel, extraordinary hardness and thermal traits deliver unmatched longevity (measured in decades) in industrial cutting operations like stamping that recover upfront investments in tooling many times over.
Limitations and Considerations
Restrictions when working with tungsten carbide powders:
- Hard and brittle after densification – avoid sharp radius edges prone to breakage
- Proper cobalt percentage binder ratios crucial to balance strength versus hardness
- Prone to oxidizing and decomposing to WO3 above 500 °C forms in machining
- Carcinogen powder handling precautions plus requiring cobalt means managing supply chain risks
- Cannot substitute grades in formulations without adjusting production process parameters
- Purity standards continuing to rise with microchip feature tolerances measured in atoms
Engineers should work closely with powder metallurgy manufacturing experts starting in design phase to customize net shape geometries maximizing density and accounting for post-sintering 20% shrinkage while minimizing trapped internal pockets leading to cracks. Consider coatings like diamond-like-carbon to enhance surface lubrication. Leverage finite element analysis to qualify mechanical loads and fatigue limits from vibration. And work to continually qualify multiple sources of raw materials to mitigate geopolitical availability bottlenecks.
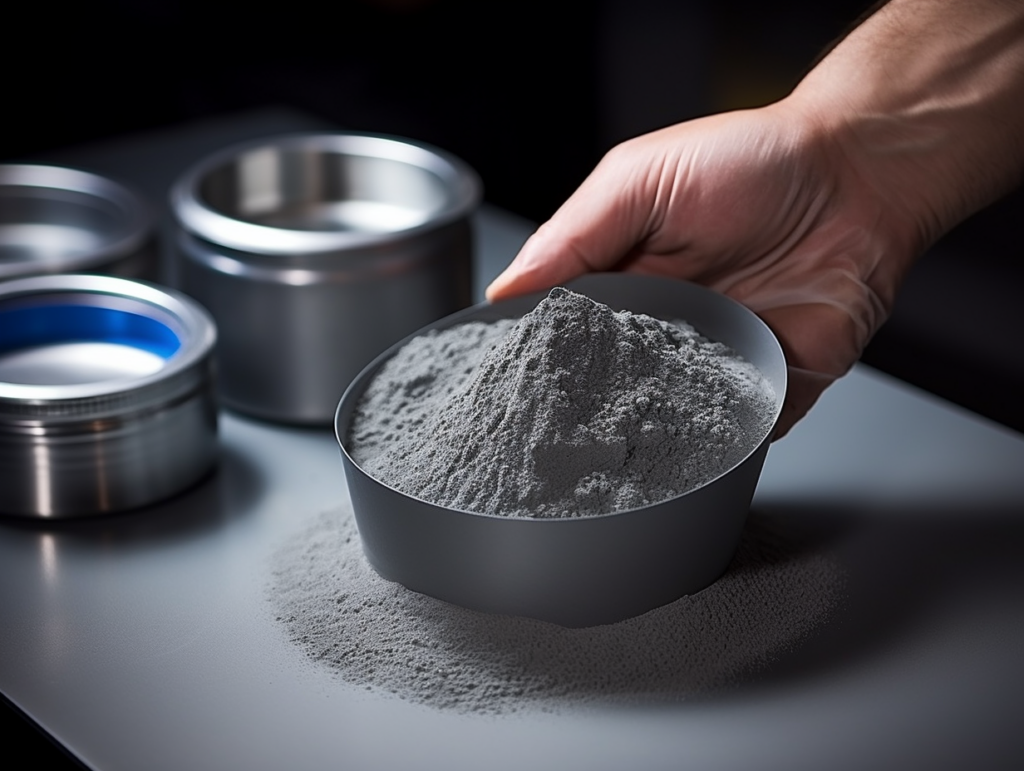
FAQ
Question | Answer |
---|---|
What is the average particle size range used as feedstock powder? | 0.5 to 10 microns typically, with nano grade emerging under 0.5 microns |
What temperature does tungsten carbide start to oxidize at? | Around 500 to 600 °C range, decomposing into WO3 which causes part degradation |
What industries consume the most tungsten carbide today? | Manufacturing tools and mining industries account for over 60% of global demand |
Does tungsten carbide powder expire or go bad? | Not generally if sealed against moisture ingress, but retest after max 3-5 years. |
Is the powder flammable or explosive? | No flammability issues but fine dust explosion risks requiring intrinsic safety handling |
What are cancer risks from tungsten carbide dust? | Lung cancers documented from cobalt particles. Strict PPE and ventilation mandatory. |
What downstream process is typically used? | Most compacts go through multi-stage sintering ovens for densification then require diamond grinding finishing. |
Which is used more – tungsten carbide or titanium carbide? | Tungsten carbide dominates by volume with over 3X consumption globally. |
Proper precautions combined with custom mechanical design enable tungsten carbide to revolutionize component durability across the most demanding applications.
Conclusion
With exceptional hardness ratings beyond other metals, the unique material properties of cemented tungsten carbide will continue spearheading innovations from longer-lasting precision surgical tools to enabling economical deep oil and gas drilling in remote regions. Combining particles as small as 200 nanometers grades emerging from leading powder manufacturers with computer-controlled densification processes allows engineers the design freedom to create net shape parts unimaginable through traditional machining means. And continuous tungsten supply chain improvements will stabilize costs while meeting purity levels measured in parts-per-million as tolerances tighten. By accounting for brittleness risks in mechanical design phases and codifying proper handling procedures both at industrial powder handling scales through to nano-scale laboratory research, durability engineers can fully utilize this material’s potential across automotive, aerospace, construction and electronics sectors to maximize efficiency and product lifetimes as application demands intensify. While historically dominant in cutting tools and mining accessories simply due to extreme hardness conveying durability, proliferating additive manufacturing methods will likely expand tungsten carbide growth opportunities across further applications like lightweight aircraft interior fittings or recoil buffer components as more sectors recognize the advantages conveyed across wear, heat and radiation shielding capabilities relative to common metal alternatives.