Tungsten powder is a fine gray powder made from tungsten metal. It has unique properties that make it useful across many industrial and commercial applications. This article provides a comprehensive overview of tungsten powder covering its composition, properties, production methods, applications, specifications, pricing, pros and cons, and leading global suppliers.
Overview of tungsten powder
Tungsten powder is composed almost entirely of elemental tungsten metal in powder form. The powder particles are very fine, ranging from 0.5 to 10 microns in size. The powder has a grayish coloration and high density due to the intrinsic properties of metallic tungsten.
Tungsten powder offers exceptional hardness, heat resistance, and density compared to most other metals and alloys. Key properties that make tungsten powder suitable for various functions include:
- High density similar to gold and almost twice that of lead
- Melting point of 3410°C – highest of all metals
- Low electrical resistivity comparable to common metals
- Excellent radiation shielding density
- Strength retention at high temperatures
- Corrosion resistance in many environments
These attributes allow tungsten powder uses in applications like radiation shielding, electrodes, heating elements, ballast weights, dyes, catalysts, and more. The powder can be pressed into shapes or sintered into end-use components with special characteristics.
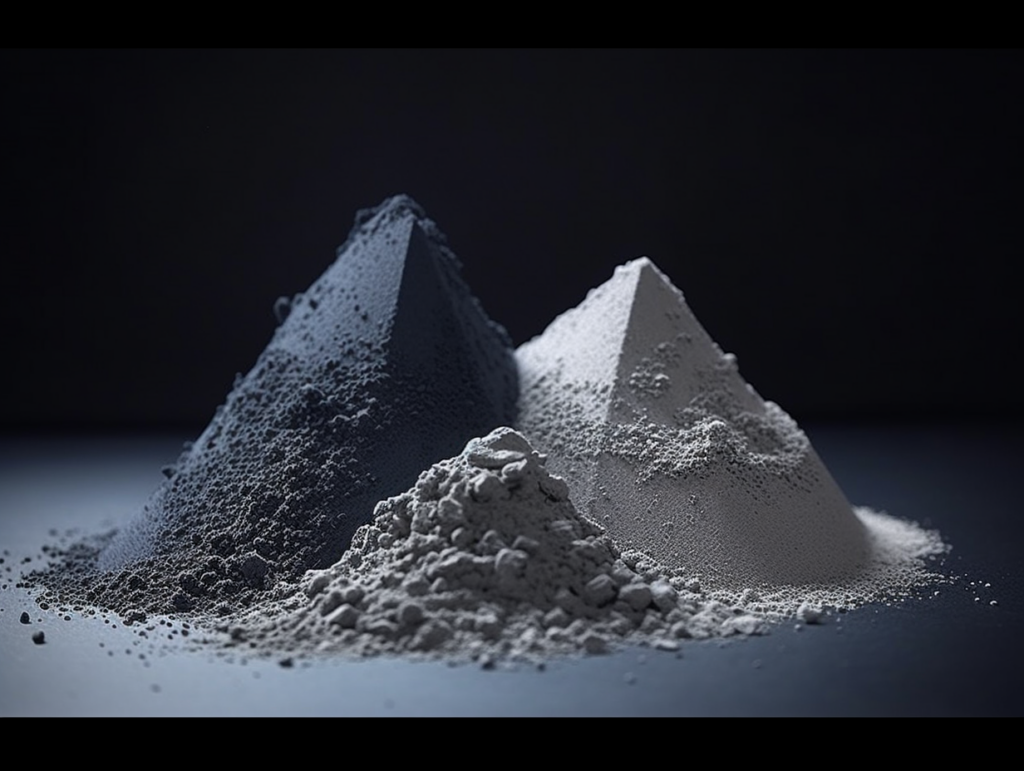
Types of Tungsten Powder
Tungsten powder is manufactured in several forms with differences in particle size distribution, shape, purity levels, and powder surface chemistry. The major types of tungsten powder include:
Type | Description |
---|---|
Fine powder | Particle size of 0.5 to 10 microns suitable for pressing into shapes |
Coarse powder | Larger spherical particles over 10 microns for improved flow and packing |
Crushed powder | Irregular jagged particles sized 1 to 44 microns from crushing ingots |
Alloy powders | Composite powders blended with carbon, cobalt, nickel, copper, silver etc. |
Chemical powders | Ultrafine nanostructure tungsten and oxide powders |
The particle shape, size distribution, flow characteristics, compaction density, and microstructure requirements determine the type of tungsten powder selected for an application.
Composition of Tungsten Powder
Tungsten powders for industrial uses typically contain over 99.95% pure tungsten metal to ensure consistent performance. Trace impurities from raw materials and manufacturing can be present up to these levels:
Element | Maximum Content | Role |
---|---|---|
Carbon (C) | 100 ppm | Grain growth inhibitor |
Oxygen (O) | 100 ppm | Surface oxide films |
Phosphorus (P) | 10 ppm | Residual impurity |
Sulfur (S) | 10 ppm | Residual impurity |
Potassium (K) | 10 ppm | Residual impurity |
Silica (Si) | 10 ppm | Residual impurity |
Higher purity grades minimize contamination issues during sintering and improve ductility. Special high-purity tungsten suitable for lighting filaments, electronics, and laboratory uses have only 10-100 ppb impurities.
Alloy tungsten powders are commonly blended with 1-5% cobalt, nickel, iron, silver, or copper to enhance sintering, machinability, or high-temperature behavior. Small amounts of inorganic additives can provide unique functional properties.
Properties of Tungsten Powder
Tungsten metal powder has intrinsic properties that stem from its elemental composition and crystalline structure. Being pure tungsten, the powder exhibits related thermal, electrical, mechanical, and chemical characteristics.
Physical Properties
Key physical properties of tungsten powder:
Property | Value |
---|---|
Density | 19.3 g/cm<sup>3</sup> |
Melting Point | 3410°C |
Thermal Conductivity | 170 W/m·K |
Vapor Pressure | Low, ~10<sup>-6</sup> bar at ~1700°C |
Specific Heat Capacity | 130 J/kg·K |
Coefficient of Thermal Expansion | 4.5 μm/m·K |
Color | Gray to black |
The ultrahigh melting point, high density, good conductivity, and excellent dimensional stability under heat make tungsten useful for extreme temperature applications.
Mechanical Properties
Tungsten powder can be compacted and sintered to obtain very high hardness and strength with moderate ductility levels:
Property | Sintered Condition |
---|---|
Hardness | Up to 550 VPN |
0.2% Yield Strength | ~800 MPa |
Ultimate Tensile Strength | ~900 MPa |
Fracture Toughness | 30-35 MPa√m |
Young’s Modulus | ~400 GPa |
Tungsten retains strength exceptionally well even at temperatures approaching 2000°C in inert atmospheres or vacuum thanks to its refractory nature.
Electrical Properties
Tungsten powder and sintered parts offer good electrical and thermal conductivity ideal for heating elements:
Property | Value |
---|---|
Electrical Resistivity | 5.5 μΩ·cm |
Temperature Coefficient of Resistance | ~4 x10<sup>-3</sup> Ω/Ω/K |
The stability, low resistivity, and positive tempco ensure excellent performance in electrical discharge machining electrodes too.
-
CM247LC Powder | Nickel Alloy Powder
-
0# Pure Nickel powder
-
NiCoCrAlY alloys powders
-
Rene 142 alloy-Rene Powder
-
Haynes 25 Haynes Powder
-
Best Hastelloy C-22 Powder-High temperature alloy Powder for 3D Printing
-
Best Hastelloy C-276 Powder-High temperature alloy Powder for 3D Printing
-
Best Hastelloy N Powder-High temperature alloy Powder for 3D Printing
-
Best Hastelloy B Powder丨High temperature alloy Powder for 3D Printing
Production of Tungsten Powder
Tungsten metal powder is primarily produced by the reduction of tungsten oxide followed by crushing and grinding stages. The manufacturing steps are:
1. Concentration of ore: Natural tungsten ores containing the mineral scheelite or wolframite are physically upgraded to higher tungsten levels by crushing and grinding, gravity, magnetic, or flotation processes.
2. Conversion to oxide: The concentrated mineral is reacted at high temperature with hydrogen, carbon, or carbon monoxide gas to yield crude tungsten oxide WO<sub>3</sub>. Lime or soda ash fluxing agents help produce a porous, easily reducible oxide.
3. Hydrogen Reduction: The oxide is reduced with dry hydrogen gas passed over it heated to about 800°C in pusher or rotary furnaces. This produces blue tungsten oxide W<sub>3</sub>O which is further reduced to yield tungsten metal powder.
4. Milling and Blending: The reduced tungsten powder goes through pulverization and size classification to obtain specific particle size distributions. Powders can be blended with dopants like potassium or grain growth inhibitors. Heat treatment and annealing provide proper powder tap density and morphology.
5. Packaging: Tungsten powder is packed into drums or bags under controlled humidity conditions for shipment to pressing and sintering facilities.
Secondary scrap recovery, recycling of tungsten hardmetals, electronic waste, and used cemented carbide tools also provide a growing source of tungsten powder feedstock.
Applications of Tungsten Powder
Key applications using tungsten powder as feed material include:
Cemented carbides
Over 60% of tungsten powder is used to manufacture hardmetal composites with cobalt or nickel binders. Grades like WC-Co are very widely used.
Mill products
Tungsten metal shapes like rods, wires, and sheets made by powder metallurgy contain pressed and sintered tungsten powder.
Lighting filaments
Tungsten wires for household incandescent bulbs are fabricated from very pure pressed and sintered tungsten.
Heating elements
The high temperature strength and electrical resistivity allow all-tungsten or doped heating elements for furnaces, heaters etc.
Electrodes
Tungsten electrodes for welding, electrical discharge machining, and plasma cutting applications derive from pressed powder preforms.
Electronics
Sintered tungsten contacts, heat sinks bases, and packages take advantage of its thermal-electrical attributes.
Radiation shielding
Tungsten alloys or composite mixtures provide shielding from gamma rays and X-rays in nuclear, medical, and space fields.
Ballast weights
Tungsten metal provides very high density in a compact form factor ideal for weighting of rotors, vibration dampening etc.
Catalysts
Tungsten oxide species dispersed on substrates give specialized catalysts for chemical processes.
Tungsten Powder Specifications
Tungsten metal powders are standardized based on metrics like particle size distribution, shape, purity levels, surface area, apparent density, and flow rates.
Grades
Common tungsten powder varieties are:
Grade | Description | Particle Size | Apparent Density |
---|---|---|---|
Extra fine | High purity, thin flake morphology | 1-5 μm | 2.2-3.5 g/cc |
Fine | General use, rounded particles | 1-10 μm | 3-8 g/cc |
Medium | Free-flowing, pressed into mill shapes | 5-25 μm | 7-9 g/cc |
Coarse | Best flowability, high green strength | 15-45 μm | 8-10 g/cc |
Specialized tungsten powder alloys have cobalt, copper, silver, nickel, or other alloying additions like W-Ni-Fe, W-Ni-Cu etc.
Standards
Tungsten powder manufacture and testing adheres to these main international specifications:
- ASTM B776 – Standard for Tungsten Powders and Tungsten Powder Products
- ISO 4492 – Metallic powders – Determination of tap density
- ISO 4497 – Metallic powders – Determination of flow rate by means of a calibrated funnel (Hall flowmeter)
- IEC 60804 – Tungsten powders and tungsten metal powders for lamps
- GB/T 33137-2016 – Tungsten powder and tungsten powder products
Based on application and regional needs, JIS, DIN, BS, and other standards may cover tungsten powder also.
Pricing
Pricing depends on tungsten powder grade, purity, particle size, quantity, and geographical market. Some indicative costs of tungsten powder (USD per metric tonne, 2023):
Region | Fine Grade | Medium Grade |
---|---|---|
China | $35,000 | $32,000 |
Europe | $52,000 | $47,000 |
USA | $57,000 | $50,000 |
Japan | $62,000 | $55,000 |
Higher density, more uniform particle distribution, special dopants, finer sizes, and smallest packing sizes command premium pricing of over $250/kg for ultrafine and nanopowders.
Pros and Cons
Tungsten demonstrates benefits and certain limitations for applications:
Advantages
- Highest melting point metal
- Best high temperature strength
- High hardness when sintered
- Excellent radiation shielding
- Dimensional stability under heat
- Resists corrosion and oxidation
Disadvantages
- Brittleity when sintered and forged
- Challenging forming and machining
- Heavy weight compared to titanium/aluminum
- Subject to surface defects if impure
- Lower electrical/thermal conductivity than silver, copper, aluminum
- Expensive compared to steel, lead
By understanding strengths and weaknesses of tungsten powder, suitable applications can employ its uniqueness optimally.
Suppliers
Leading global producers supplying tungsten metal powder include:
Company | HQ Location |
---|---|
Wolfram Company | Austria |
Buffalo Tungsten | USA |
Midwest Tungsten | USA |
Tungsten Heavy Powder | China |
Xiamen Tungsten | China |
JX Nippon Mining | Japan |
H Cross Company | Japan |
GTP Gudelsky Technical Powders | Germany |
These corporations offer reliable large volume capacity and product diversity catering to a wide range of commercial and industrial needs.
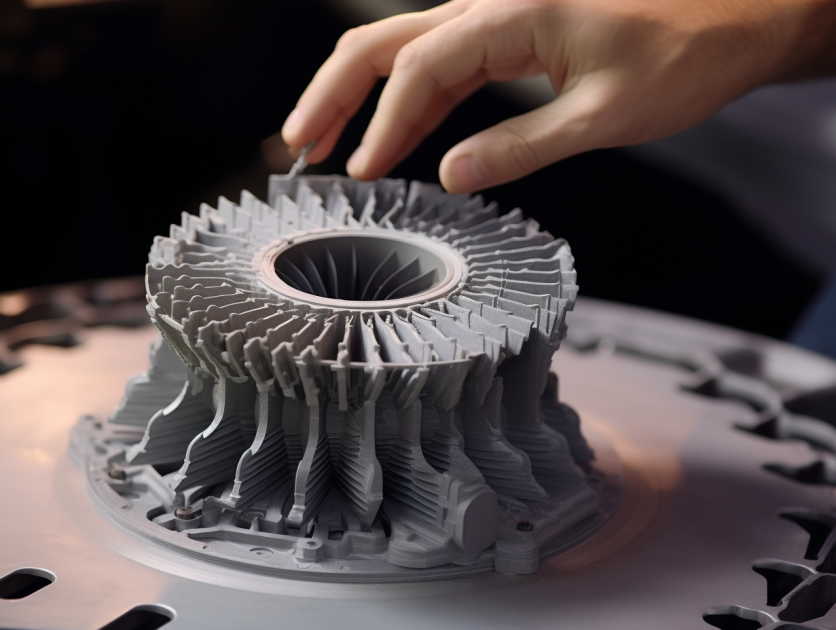
FAQs
Question | Answer |
---|---|
What is tungsten powder made of? | ≈99.95% pure elemental tungsten metal in powder form along with minor residual impurities |
What is tungsten powder used for? | Manufacturing cemented carbides, heating elements, lighting filaments, radiation shielding, electrodes, metal injection molding precursors |
What are the different varieties of tungsten powder? | Based mainly on particle size distribution – ultrafine, fine, medium and coarse grades from 0.5 to 45 microns |
What are the advantages of using fine tungsten powders? | Allow pressing of detailed, thin-walled shapes; impart strength through extensive sintering; distribute uniformly in an alloy matrix |
What are the characteristics of coarse tungsten powders? | Free-flowing spherical particles fill die cavities well; high green strength resists cracking; form skeleton structure to support alloy mix |
How is tungsten powder made? | Reduction of tungsten oxide combined with particle size diminution via milling/grinding of reduced tungsten metal |
Is tungsten powder toxic? | Elemental tungsten is relatively inert and non-toxic. However inhalation of fine powders can cause lung irritation requiring protective equipment |
Is tungsten powder flammable or explosive? | No, tungsten metal itself does not burn or explode under normal situations. But fine powders can form explosive mixtures with air |
Is tungsten environmentally friendly? | Yes, tungsten mining and metal production follows modern sustainability protocols. Powder provides green strength for creative use of tungsten properties |
Conclusions
With extraordinary refractory properties setting it apart from alternatives, tungsten in powder form enables unique high-temperature applications across industries. Pressed and sintered shapes exploit exceptional hardness, electrical/thermal conductivity, radiation shielding density, corrosion resistance, and dimensional stability under demanding environments.
Careful specification coupled with understanding of powder attributes allows reliable functionality. Blending altered alloy varieties expands possibilities while secondary scrap feeds circular economy. Future progress in powder quality through advanced atomization promises exciting material and energy efficiencies harnessing tungsten powder’s full potential.