Overview of Vacuum Inert Gas Atomisation
Vacuum Inert Gas Atomisation (VIGA) is a sophisticated process used in the production of high-quality metal powders, primarily for applications that require superior material properties like additive manufacturing, aerospace, and biomedical implants. The VIGA process involves the atomization of molten metal in a vacuum chamber filled with an inert gas, resulting in fine, spherical powders with minimal contamination. The process is crucial for manufacturing powders that maintain their purity and possess uniform particle size, which are critical factors in advanced manufacturing processes.
Imagine this process as a fine dance of physics, where metal is first melted and then shattered into tiny droplets by a high-speed inert gas stream. These droplets solidify into tiny, perfectly spherical particles as they cool down, much like how raindrops form but in a highly controlled environment. This high level of control ensures that the final product, the metal powder, is of the highest quality.
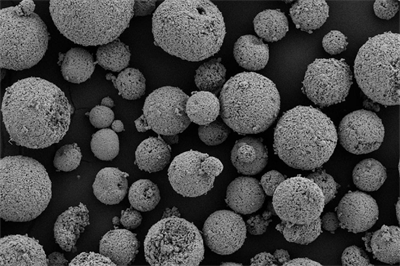
Types of Metal Powders Produced by VIGA
VIGA is capable of producing a wide range of metal powders, each with unique properties tailored to specific applications. Below is a table outlining some of the most common metal powders produced through this process, along with their specific models and characteristics:
Metal Powder | Model | Composition | Properties | Applications |
---|---|---|---|---|
Stainless Steel | SS316L | Fe-Cr-Ni-Mo | High corrosion resistance, excellent ductility | Medical implants, aerospace components |
Titanium Alloy | Ti-6Al-4V | Ti-Al-V | High strength-to-weight ratio, excellent corrosion resistance | Aerospace, biomedical implants |
Nickel-Based Superalloy | Inconel 718 | Ni-Cr-Fe-Nb-Mo-Ti | High-temperature stability, excellent oxidation resistance | Gas turbines, jet engines |
Cobalt-Chromium Alloy | CoCrMo | Co-Cr-Mo | High wear resistance, biocompatibility | Dental implants, orthopedic devices |
Aluminum Alloy | AlSi10Mg | Al-Si-Mg | Lightweight, good thermal conductivity | Automotive parts, aerospace |
Copper Alloy | CuCrZr | Cu-Cr-Zr | High electrical conductivity, good thermal properties | Electrical components, heat exchangers |
Maraging Steel | 18Ni300 | Fe-Ni-Co-Mo | High strength, good toughness | Tooling, aerospace components |
Tungsten Alloy | W-Ni-Fe | W-Ni-Fe | High density, good radiation shielding | Medical, defense applications |
Tool Steel | H13 | Fe-Cr-Mo-V | High hardness, wear resistance | Molds, dies, cutting tools |
High Entropy Alloy | AlCoCrFeNi | Al-Co-Cr-Fe-Ni | High strength, good thermal stability | Advanced engineering applications |
Each of these powders has been engineered to meet specific industry demands, and the choice of powder depends largely on the application. For instance, Titanium alloys like Ti-6Al-4V are preferred in aerospace due to their strength and lightweight properties, while Stainless Steel 316L is a go-to in the medical field for its biocompatibility.
Composition of Vacuum Inert Gas Atomisation Metal Powders
The composition of metal powders produced by VIGA is a critical factor that determines their suitability for various applications. The process allows for precise control over the alloying elements, leading to powders with uniform chemical composition and minimal impurities. Below is a detailed breakdown of the composition of some key metal powders produced by VIGA:
Metal Powder | Composition | Key Alloying Elements | Effect on Properties |
---|---|---|---|
SS316L | Fe-Cr-Ni-Mo | 17% Cr, 12% Ni, 2.5% Mo | Corrosion resistance, strength, ductility |
Ti-6Al-4V | Ti-Al-V | 6% Al, 4% V | High strength, lightweight |
Inconel 718 | Ni-Cr-Fe-Nb-Mo-Ti | 53% Ni, 19% Cr, 5% Nb | Oxidation resistance, high-temperature strength |
CoCrMo | Co-Cr-Mo | 28% Cr, 6% Mo | Wear resistance, biocompatibility |
AlSi10Mg | Al-Si-Mg | 10% Si, 0.5% Mg | Lightweight, good castability |
CuCrZr | Cu-Cr-Zr | 1% Cr, 0.15% Zr | High electrical conductivity |
18Ni300 | Fe-Ni-Co-Mo | 18% Ni, 9% Co, 5% Mo | High strength, toughness |
W-Ni-Fe | W-Ni-Fe | 90% W, 7% Ni, 3% Fe | High density, good machinability |
H13 | Fe-Cr-Mo-V | 5% Cr, 1.5% Mo, 1% V | Hardness, wear resistance |
AlCoCrFeNi | Al-Co-Cr-Fe-Ni | Equiatomic mix | High strength, thermal stability |
The ability to fine-tune these compositions gives manufacturers the flexibility to create powders that meet specific mechanical, chemical, and thermal requirements.
Characteristics of Vacuum Inert Gas Atomisation Powders
The characteristics of VIGA-produced metal powders are crucial in determining their performance in various applications. Below are some key characteristics:
Characteristic | Description | Impact on Applications |
---|---|---|
Particle Size Distribution | Uniform, fine | Improves flowability and packing density |
Sphericity | High sphericity | Enhances powder flowability, reduces porosity in final product |
Purity | Low levels of oxygen and nitrogen | Prevents defects in additive manufacturing |
Surface Area | Optimized surface area | Affects sintering behavior in powder metallurgy |
Flowability | High flowability | Essential for consistent layer deposition in additive manufacturing |
Apparent Density | Controlled density | Impacts the final part density and mechanical properties |
These characteristics are achieved through the precise control of the atomization process. For instance, the use of inert gases like Argon or Nitrogen prevents oxidation during atomization, ensuring the high purity of the powders. The spherical shape of the particles, achieved through rapid solidification, enhances the flowability and packing density, which are critical in processes like 3D printing.
Advantages of Vacuum Inert Gas Atomisation
The VIGA process offers several advantages over other atomization methods, making it the preferred choice for producing high-performance metal powders. Here are some of the key benefits:
- High Purity Powders: The vacuum environment and inert gas prevent oxidation and contamination, resulting in powders with very high purity levels. This is particularly important in industries like aerospace and medical, where material integrity is critical.
- Uniform Particle Size Distribution: VIGA produces powders with a narrow particle size distribution, which is crucial for consistent performance in additive manufacturing and other powder metallurgy applications.
- Enhanced Sphericity: The spherical shape of the particles improves flowability, packing density, and the quality of the final product. This is especially beneficial in 3D printing, where uniform layer deposition is essential.
- Scalability: VIGA is suitable for both small-scale and large-scale production, making it versatile for various manufacturing needs.
- Reduced Contamination: The closed system and controlled environment of VIGA minimize the risk of contamination, ensuring the production of high-quality powders suitable for critical applications.
In comparison to other atomization methods, such as water atomization or gas atomization in a non-vacuum environment, VIGA stands out for its ability to produce powders with superior characteristics.
Applications of Vacuum Inert Gas Atomisation Powders
The unique properties of VIGA powders make them suitable for a wide range of applications. Below is a table highlighting the primary uses of these powders in various industries:
Industry | Applications | Metal Powders Used |
---|---|---|
Additive Manufacturing | 3D printing of complex parts | SS316L, Ti-6Al-4V, Inconel 718 |
Aerospace | Turbine blades, structural components | Ti-6Al-4V, Inconel 718, H13 |
Medical | Implants, prosthetics | SS316L, CoCrMo, Ti-6Al-4V |
Automotive | Engine components, lightweight parts | AlSi10Mg, SS316L, CuCrZr |
Energy | Power generation components | Inconel 718,W-Ni-Fe |
Tooling | Molds, dies, cutting tools | H13, 18Ni300, CoCrMo |
Defense | Ammunition, armor-piercing rounds | W-Ni-Fe, Ti-6Al-4V |
Electronics | Conductive components, heat sinks | CuCrZr, AlSi10Mg |
Marine | Corrosion-resistant parts | SS316L, Ti-6Al-4V |
Dental | Crowns, bridges | CoCrMo, SS316L |
In additive manufacturing, VIGA powders are particularly valued for their uniformity and purity, which result in high-quality prints with minimal defects. Aerospace and medical industries rely on VIGA powders for their critical components due to their excellent mechanical properties and biocompatibility.
Specifications, Sizes, and Standards of VIGA Powders
When it comes to VIGA powders, specifications, sizes, and standards vary depending on the application and industry requirements. Below is a detailed table outlining the common specifications and standards:
Metal Powder | Particle Size Range | Standards | Packaging Sizes | Density (g/cm³) | Flow Rate (s/50g) |
---|---|---|---|---|---|
SS316L | 15-45 µm | ASTM F138, ISO 5832-1 | 1kg, 5kg, 25kg | 7.9 | 25 |
Ti-6Al-4V | 20-63 µm | ASTM F2924, ISO 5832-3 | 1kg, 5kg, 25kg | 4.43 | 32 |
Inconel 718 | 15-53 µm | AMS 5662, AMS 5663 | 1kg, 5kg, 25kg | 8.19 | 28 |
CoCrMo | 20-45 µm | ASTM F75, ISO 5832-4 | 1kg, 5kg, 25kg | 8.3 | 30 |
AlSi10Mg | 10-63 µm | DIN EN 1706 | 1kg, 5kg, 25kg | 2.68 | 22 |
CuCrZr | 15-45 µm | ASTM B505, EN 12163 | 1kg, 5kg, 25kg | 8.9 | 18 |
18Ni300 | 20-53 µm | AMS 6514 | 1kg, 5kg, 25kg | 8.1 | 34 |
W-Ni-Fe | 10-45 µm | ASTM B777 | 1kg, 5kg, 25kg | 17.6 | 35 |
H13 | 20-53 µm | ASTM A681 | 1kg, 5kg, 25kg | 7.8 | 29 |
AlCoCrFeNi | 15-63 µm | In-house standards | 1kg, 5kg, 25kg | 7.5 | 27 |
These specifications are essential in ensuring that the metal powders meet the requirements for specific applications. Standards like ASTM and ISO provide guidelines on particle size, purity, and mechanical properties, which manufacturers must adhere to in order to ensure product quality.
Suppliers and Pricing Details of VIGA Powders
The market for VIGA powders is diverse, with numerous suppliers offering a range of products. Below is a table providing details on some of the leading suppliers and the pricing of their VIGA powders:
Supplier | Metal Powders | Pricing (per kg) | MOQ | Lead Time | Certifications |
---|---|---|---|---|---|
Höganäs AB | SS316L, Ti-6Al-4V, Inconel 718 | $200 – $450 | 10 kg | 4-6 weeks | ISO 9001, ISO 14001 |
Carpenter Technology | Ti-6Al-4V, CoCrMo | $300 – $600 | 5 kg | 3-5 weeks | AS9100, ISO 13485 |
LPW Technology | Inconel 718, AlSi10Mg | $250 – $500 | 5 kg | 2-4 weeks | ISO 9001, AS9100 |
Arcam AB | Ti-6Al-4V, SS316L | $350 – $700 | 10 kg | 6-8 weeks | ISO 13485, ISO 9001 |
Sandvik Materials Technology | SS316L, Inconel 718 | $200 – $450 | 5 kg | 4-6 weeks | ISO 9001, ISO 14001 |
GKN Hoeganaes | H13, 18Ni300 | $150 – $400 | 10 kg | 4-6 weeks | ISO 9001 |
AP&C (GE Additive) | Ti-6Al-4V, AlSi10Mg | $300 – $650 | 5 kg | 3-5 weeks | AS9100, ISO 13485 |
Praxair Surface Technologies | SS316L, CoCrMo | $250 – $500 | 10 kg | 4-6 weeks | ISO 9001, AS9100 |
Erasteel | H13, Inconel 718 | $200 – $450 | 5 kg | 4-6 weeks | ISO 9001, ISO 14001 |
TLS Technik | W-Ni-Fe, AlCoCrFeNi | $400 – $800 | 10 kg | 6-8 weeks | ISO 9001 |
Pricing varies depending on the metal powder, order quantity, and supplier. Lead times also vary, with some suppliers offering faster delivery for urgent orders. Certifications such as ISO 9001 and AS9100 are crucial for ensuring the quality and traceability of the powders, especially in critical industries like aerospace and medical.
Advantages and Limitations of VIGA
While VIGA offers numerous advantages, it’s important to understand the potential limitations as well. Below is a comparison of the pros and cons of VIGA:
Advantages | Limitations |
---|---|
High Purity Powders | Higher Cost: VIGA equipment and processes can be more expensive compared to other methods. |
Uniform Particle Size Distribution | Complex Process: Requires precise control and expertise. |
Enhanced Sphericity | Lower Production Rates: Slower than other atomization methods due to vacuum requirements. |
Scalability | Limited Material Types: Not all materials are suitable for VIGA. |
Reduced Contamination | Energy Intensive: High energy consumption due to the need for vacuum and inert gases. |
This comparison highlights that while VIGA is an excellent choice for producing high-quality metal powders, it may not be the most cost-effective or efficient method for all applications.
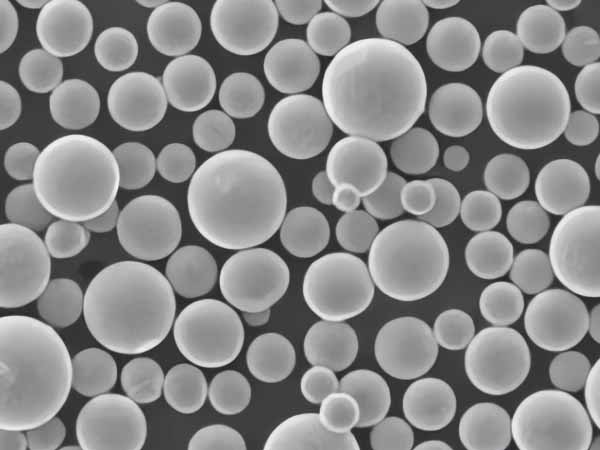
FAQs
Here’s a frequently asked questions section to address common queries about VIGA:
Question | Answer |
---|---|
What is Vacuum Inert Gas Atomisation? | VIGA is a process used to produce high-quality metal powders by atomizing molten metal in a vacuum chamber filled with inert gas. |
What are the benefits of using VIGA powders? | VIGA powders offer high purity, uniform particle size distribution, enhanced sphericity, and reduced contamination, making them ideal for advanced manufacturing. |
Which industries use VIGA powders? | VIGA powders are widely used in aerospace, medical, automotive, energy, and additive manufacturing industries. |
How does VIGA compare to other atomization methods? | VIGA produces higher quality powders but is generally more expensive and energy-intensive compared to other methods like water or air atomization. |
What are the common metal powders produced by VIGA? | Common VIGA powders include Stainless Steel 316L, Ti-6Al-4V, Inconel 718, CoCrMo, and AlSi10Mg. |
Are VIGA powders suitable for 3D printing? | Yes, VIGA powders are highly suitable for 3D printing due to their high purity, uniformity, and excellent flowability. |
What are the challenges of VIGA? | The main challenges include higher costs, complexity of the process, and lower production rates. |