Wear resistance powders are crucial materials in industries where components are subject to heavy wear and tear. They enhance the durability and lifespan of various mechanical parts, making them essential in manufacturing, automotive, aerospace, and more. This article delves into the intricacies of wear resistance powders, exploring their types, compositions, properties, applications, and more. Buckle up for a comprehensive guide that leaves no stone unturned!
Overview of Wear Resistance Powder
Wear resistance powders are specialized materials designed to reduce wear and extend the life of surfaces in high-stress environments. They are often used in coatings, surface treatments, and additive manufacturing. These powders come in various compositions, including metals, ceramics, and composites, each offering unique benefits.
Key Points
- Purpose: Enhance durability and lifespan of components
- Applications: Manufacturing, automotive, aerospace, mining, etc.
- Types: Metal powders, ceramic powders, composite powders
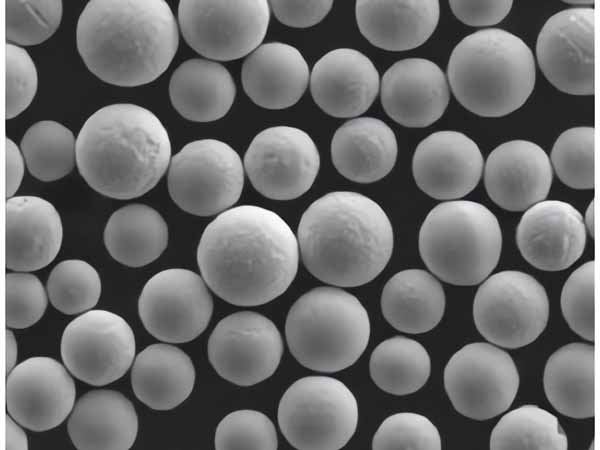
Types of Wear Resistance Powder
Metal Powders
Metal powders are widely used for their excellent mechanical properties and ease of application. Let’s explore some specific models:
- Stellite 6: A cobalt-chromium alloy known for its outstanding wear and corrosion resistance.
- Tungsten Carbide (WC): Offers high hardness and wear resistance, ideal for cutting tools.
- Nickel Alloy 625: Provides excellent fatigue and thermal resistance.
- Iron-Based Alloy: Cost-effective option with decent wear resistance.
- Chromium Carbide (CrC): High hardness and wear resistance, suitable for high-temperature applications.
Ceramic Powders
Ceramics are known for their extreme hardness and thermal stability. Here are some examples:
- Aluminum Oxide (Al2O3): High hardness and chemical resistance.
- Silicon Carbide (SiC): Excellent thermal conductivity and wear resistance.
- Zirconium Oxide (ZrO2): High fracture toughness and thermal stability.
Composite Powders
Composite powders combine the properties of metals and ceramics for enhanced performance:
- WC-Co (Tungsten Carbide-Cobalt): Combines hardness of WC with toughness of Co.
- NiCr-Cr3C2 (Nickel Chromium-Chromium Carbide): Excellent for high-temperature wear applications.
- TiC-Ni (Titanium Carbide-Nickel): Balances hardness and toughness.
Composition of Wear Resistance Powder
Understanding the composition of wear resistance powders is crucial for selecting the right material for your needs. Here’s a breakdown of common compositions:
Type | Composition | Properties |
---|---|---|
Stellite 6 | Cobalt, Chromium, Tungsten, Carbon | Wear and corrosion resistance |
Tungsten Carbide | Tungsten, Carbon | High hardness, wear resistance |
Nickel Alloy 625 | Nickel, Chromium, Molybdenum, Niobium | Fatigue, thermal, and corrosion resistance |
Iron-Based Alloy | Iron, Carbon, Chromium | Cost-effective, decent wear resistance |
Chromium Carbide | Chromium, Carbon | High hardness, wear resistance |
Aluminum Oxide | Aluminum, Oxygen | High hardness, chemical resistance |
Silicon Carbide | Silicon, Carbon | Thermal conductivity, wear resistance |
Zirconium Oxide | Zirconium, Oxygen | Fracture toughness, thermal stability |
WC-Co | Tungsten Carbide, Cobalt | Hardness of WC, toughness of Co |
NiCr-Cr3C2 | Nickel, Chromium, Chromium Carbide | High-temperature wear resistance |
TiC-Ni | Titanium Carbide, Nickel | Balanced hardness and toughness |
Characteristics of Wear Resistance Powder
The characteristics of wear resistance powders determine their suitability for various applications. Here’s what to consider:
- Hardness: Determines the material’s resistance to deformation.
- Toughness: The ability to absorb energy and resist cracking.
- Corrosion Resistance: Resistance to chemical degradation.
- Thermal Stability: Ability to maintain properties at high temperatures.
- Fatigue Resistance: Resistance to weakening under repeated stress.
Applications of Wear Resistance Powder
Wear resistance powders find applications across a wide range of industries due to their ability to enhance durability and performance.
Application | Description |
---|---|
Manufacturing | Tools and dies, molds, machine parts |
Automotive | Engine components, brake pads, transmission parts |
Aerospace | Turbine blades, structural components |
Mining | Drilling equipment, conveyor systems |
Oil and Gas | Pump components, valve seats |
Construction | Excavator teeth, crusher parts |
Medical Devices | Implants, surgical tools |
Agriculture | Plowshares, harvester blades |
Electronics | Semiconductor manufacturing tools |
Marine | Propeller shafts, rudders |
Specifications, Sizes, Grades, Standards
Specifications of wear resistance powders are crucial for ensuring compatibility with different applications. Here’s a detailed table:
Material | Grade | Particle Size | Standards |
---|---|---|---|
Stellite 6 | AMS 5894 | -45/+15 µm | ASTM B637 |
Tungsten Carbide | WC-10Co-4Cr | -53/+20 µm | ISO 14121 |
Nickel Alloy 625 | UNS N06625 | -63/+10 µm | ASTM B443 |
Iron-Based Alloy | FeCrC | -45/+15 µm | AWS A5.21 |
Chromium Carbide | Cr3C2-25NiCr | -53/+20 µm | ISO 14121 |
Aluminum Oxide | AL 99.5 | -45/+15 µm | ISO 17934 |
Silicon Carbide | SiC | -63/+10 µm | ASTM B849 |
Zirconium Oxide | Y-TZP | -45/+15 µm | ISO 13356 |
WC-Co | WC-12Co | -53/+20 µm | ISO 14121 |
NiCr-Cr3C2 | NiCr-20Cr3C2 | -63/+10 µm | ASTM B899 |
TiC-Ni | TiC-20Ni | -45/+15 µm | ISO 17934 |
Suppliers and Pricing Details
Knowing where to source these materials and understanding the pricing is essential for procurement planning. Here’s an overview:
Supplier | Material | Price (per kg) | Location |
---|---|---|---|
Carpenter Technology | Stellite 6 | $150 – $200 | USA |
Kennametal | Tungsten Carbide | $200 – $250 | USA, Europe |
Haynes International | Nickel Alloy 625 | $100 – $150 | USA |
Höganäs | Iron-Based Alloy | $50 – $80 | Sweden |
Praxair Surface Technologies | Chromium Carbide | $120 – $170 | USA |
Saint-Gobain | Aluminum Oxide | $30 – $50 | France |
Fiven | Silicon Carbide | $60 – $100 | Norway |
Tosoh Corporation | Zirconium Oxide | $100 – $150 | Japan |
Oerlikon Metco | WC-Co | $250 – $300 | Switzerland |
HC Starck | NiCr-Cr3C2 | $180 – $220 | Germany |
Kennametal | TiC-Ni | $150 – $200 | USA, Europe |
Comparing Pros and Cons
Every material has its strengths and weaknesses. Here’s a comparison to help you choose the right one for your application:
Material | Cons |
---|---|
Stellite 6 | High cost |
Tungsten Carbide | Brittle, expensive |
Nickel Alloy 625 | High cost |
Iron-Based Alloy | Lower wear resistance compared to others |
Chromium Carbide | Brittle |
Aluminum Oxide | Brittle, difficult to process |
Silicon Carbide | Brittle |
Zirconium Oxide | Expensive |
WC-Co | High cost |
NiCr-Cr3C2 | Expensive |
Composition of Wear Resistance Powder
The composition of wear resistance powder is crucial to its performance in various applications. Here’s a detailed table summarizing the composition of some common wear resistance powders:
Material | Composition | Properties |
---|---|---|
Stellite 6 | Cobalt, Chromium, Tungsten, Carbon | High wear and corrosion resistance, toughness |
Tungsten Carbide | Tungsten, Carbon | Extremely hard, high wear resistance |
Nickel Alloy 625 | Nickel, Chromium, Molybdenum, Niobium | Excellent fatigue, thermal, and corrosion resistance |
Iron-Based Alloy | Iron, Carbon, Chromium | Cost-effective, decent wear resistance |
Chromium Carbide | Chromium, Carbon | High hardness, excellent wear resistance |
Aluminum Oxide | Aluminum, Oxygen | High hardness, chemical resistance |
Silicon Carbide | Silicon, Carbon | Excellent thermal conductivity, high wear resistance |
Zirconium Oxide | Zirconium, Oxygen | High fracture toughness, thermal stability |
WC-Co | Tungsten Carbide, Cobalt | Combines hardness of WC with toughness of Co |
NiCr-Cr3C2 | Nickel, Chromium, Chromium Carbide | Excellent high-temperature wear resistance |
TiC-Ni | Titanium Carbide, Nickel | Balances hardness and toughness |
Properties of Wear Resistance Powder
The properties of wear resistance powders determine their suitability for various applications. Here’s an overview:
- Hardness: A key property that determines the ability of the powder to resist deformation and wear.
- Toughness: The ability of the powder to absorb energy and resist fracture.
- Corrosion Resistance: The powder’s resistance to chemical degradation and oxidation.
- Thermal Stability: The ability to maintain properties at high temperatures.
- Fatigue Resistance: Resistance to weakening under repeated stress.
Detailed Table of Properties
Material | Hardness (HV) | Toughness | Corrosion Resistance | Thermal Stability | Fatigue Resistance |
---|---|---|---|---|---|
Stellite 6 | 500-600 | High | Excellent | Good | High |
Tungsten Carbide | 1200-2000 | Low | Moderate | Excellent | Moderate |
Nickel Alloy 625 | 200-240 | Moderate | Excellent | Excellent | High |
Iron-Based Alloy | 400-500 | Moderate | Moderate | Good | Moderate |
Chromium Carbide | 1500-2000 | Low | Good | Excellent | Moderate |
Aluminum Oxide | 1500-2000 | Low | Excellent | Excellent | Low |
Silicon Carbide | 2400-2800 | Low | Good | Excellent | Moderate |
Zirconium Oxide | 1200-1400 | High | Excellent | Good | High |
WC-Co | 1200-1500 | Moderate | Good | Good | Moderate |
NiCr-Cr3C2 | 1500-2000 | Moderate | Excellent | Excellent | High |
TiC-Ni | 1200-1500 | Moderate | Good | Good | Moderate |
Applications of Wear Resistance Powder
Wear resistance powders are used in a wide range of applications to enhance durability and performance. Here’s an overview of their applications:
Application | Description |
---|---|
Manufacturing | Tools and dies, molds, and machine parts |
Automotive | Engine components, brake pads, transmission parts |
Aerospace | Turbine blades, structural components |
Mining | Drilling equipment, conveyor systems |
Oil and Gas | Pump components, valve seats |
Construction | Excavator teeth, crusher parts |
Medical Devices | Implants, surgical tools |
Agriculture | Plowshares, harvester blades |
Electronics | Semiconductor manufacturing tools |
Marine | Propeller shafts, rudders |
Detailed Table of Applications
Application | Material Used | Reason |
---|---|---|
Manufacturing | Stellite 6, WC-Co | High wear resistance, toughness |
Automotive | Tungsten Carbide, NiCr-Cr3C2 | Hardness, thermal stability |
Aerospace | Nickel Alloy 625, Zirconium Oxide | Thermal stability, fatigue resistance |
Mining | Iron-Based Alloy, Chromium Carbide | Cost-effective, high wear resistance |
Oil and Gas | Stellite 6, Aluminum Oxide | Corrosion resistance, thermal stability |
Construction | Tungsten Carbide, Silicon Carbide | Hardness, wear resistance |
Medical Devices | Zirconium Oxide, Aluminum Oxide | Biocompatibility, wear resistance |
Agriculture | Iron-Based Alloy, TiC-Ni | Cost-effective, balanced hardness and toughness |
Electronics | Silicon Carbide, Aluminum Oxide | High thermal conductivity, wear resistance |
Marine | Nickel Alloy 625, Stellite 6 | Corrosion resistance, toughness |
Comparing Wear Resistance Powders
Choosing the right wear resistance powder involves comparing different options based on various parameters. Here’s a comparison to help you decide:
Parameter | Stellite 6 | Tungsten Carbide | Nickel Alloy 625 | Iron-Based Alloy | Chromium Carbide |
---|---|---|---|---|---|
Hardness | Moderate | Very High | Low | Moderate | Very High |
Toughness | High | Low | Moderate | Moderate | Low |
Corrosion Resistance | High | Moderate | Very High | Moderate | Moderate |
Thermal Stability | Good | Excellent | Excellent | Good | Excellent |
Fatigue Resistance | High | Moderate | Very High | Moderate | Moderate |
Cost | High | Very High | High | Low | Moderate |
Advantages and Disadvantages
Material | Advantages | Disadvantages |
---|---|---|
Stellite 6 | Excellent wear and corrosion resistance, toughness | High cost |
Tungsten Carbide | Superior hardness and wear resistance | Brittle, expensive |
Nickel Alloy 625 | Great fatigue, thermal, and corrosion resistance | High cost |
Iron-Based Alloy | Cost-effective, decent wear resistance | Lower wear resistance compared to others |
Chromium Carbide | High hardness, excellent wear resistance | Brittle |
Aluminum Oxide | High hardness, chemical resistance | Brittle, difficult to process |
Silicon Carbide | Excellent thermal conductivity, high wear resistance | Brittle |
Zirconium Oxide | High fracture toughness, thermal stability | Expensive |
WC-Co | Combines hardness of WC with toughness of Co | High cost |
NiCr-Cr3C2 | Excellent high-temperature wear resistance | Expensive |
TiC-Ni | Balances hardness and toughness | Moderate cost |
Suppliers and Pricing Details
Finding reliable suppliers and understanding pricing is essential for sourcing wear resistance powders. Here’s a detailed table of suppliers and pricing:
Supplier | Material | Price (per kg) | Location |
---|---|---|---|
Carpenter Technology | Stellite 6 | $150 – $200 | USA |
Kennametal | Tungsten Carbide | $200 – $250 | USA, Europe |
Haynes International | Nickel Alloy 625 | $100 – $150 | USA |
Höganäs | Iron-Based Alloy | $50 – $80 | Sweden |
Praxair Surface Technologies | Chromium Carbide | $120 – $170 | USA |
Saint-Gobain | Aluminum Oxide | $30 – $50 | France |
Fiven | Silicon Carbide | $60 – $100 | Norway |
Tosoh Corporation | Zirconium Oxide | $100 – $150 | Japan |
Oerlikon Metco | WC-Co | $250 – $300 | Switzerland |
HC Starck | NiCr-Cr3C2 | $180 – $220 | Germany |
Kennametal | TiC-Ni | $150 – $200 | USA, Europe |
FAQ
What is wear resistance powder used for?
Wear resistance powder is used to enhance the durability and lifespan of components in high-stress environments, such as manufacturing tools, automotive parts, aerospace components, and more.
What are the common types of wear resistance powders?
Common types include metal powders (e.g., Stellite 6, Tungsten Carbide), ceramic powders (e.g., Aluminum Oxide, Silicon Carbide), and composite powders (e.g., WC-Co, NiCr-Cr3C2).
How do you choose the right wear resistance powder?
Choosing the right powder depends on the specific application requirements, including hardness, toughness, corrosion resistance, thermal stability, and cost considerations.
Where can I buy wear resistance powder?
You can buy wear resistance powder from suppliers like Carpenter Technology, Kennametal, Haynes International, Höganäs, Praxair Surface Technologies, and more.
What is the cost of wear resistance powder?
The cost varies depending on the material and supplier. Prices typically range from $30 to $300 per kilogram.
Can wear resistance powder be used in additive manufacturing?
Yes, wear resistance powders are often used in additive manufacturing to create components with enhanced durability and performance.
Conclusion
Wear resistance powders are indispensable in industries where durability and longevity of components are paramount. By understanding the different types, compositions, properties, and applications, you can make informed decisions about which wear resistance powder is best suited for your needs. Whether you’re looking for the toughness of Stellite 6, the hardness of Tungsten Carbide, or the balance of WC-Co, there’s a wear resistance powder that meets your requirements. So, gear up and enhance your components with the right wear resistance powder today!