Wear resistance powder is an essential material in industries where machinery and components are subjected to harsh environments and continuous friction. But what exactly is wear resistance powder, and why is it so critical in modern engineering? In this article, we dive deep into the world of wear-resistant powders, exploring their composition, properties, types, and real-world applications. We’ll compare different metal powders, highlight their pros and cons, and answer your most pressing questions. Whether you’re a seasoned engineer or just curious about advanced materials, this guide will provide valuable insights.
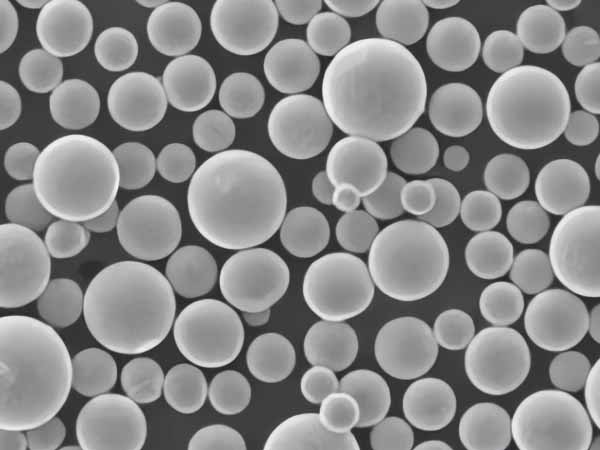
Overview of Wear Resistance Powder
Wear resistance powders are finely ground materials, typically metal-based, that are used to enhance the durability and lifespan of components exposed to high wear conditions. These powders are crucial in industries such as automotive, aerospace, mining, and manufacturing, where components like gears, bearings, and cutting tools must withstand extreme stress, abrasion, and corrosion. The right wear resistance powder can significantly reduce maintenance costs and downtime, leading to more efficient and reliable operations.
What Makes Wear Resistance Powder Special?
Think of wear resistance powder as the armor plating for your machinery. Just like how knights wore armor to protect against blows in battle, wear resistance powder shields your components from the harsh forces they encounter daily. These powders are engineered to be incredibly tough, often combining metals and ceramics to achieve superior hardness, corrosion resistance, and thermal stability.
Why Should You Care About Wear Resistance?
Imagine your car’s engine running without any lubrication or your kitchen knife made of soft metal—it wouldn’t last long, would it? The same concept applies to industrial machinery. Without the proper wear resistance, components wear out quickly, leading to frequent replacements, unexpected breakdowns, and higher costs. By using wear resistance powders, you’re not just extending the life of your equipment; you’re ensuring smoother operations and better performance.
Composition of Wear Resistance Powder
When it comes to wear resistance powders, the composition is key. These powders are typically made from a blend of metals, ceramics, and sometimes polymers, each chosen for its specific properties that contribute to wear resistance.
Metal Powder Model | Composition | Key Properties | Common Applications |
---|---|---|---|
Tungsten Carbide (WC) | WC | Extremely hard, high melting point, wear-resistant | Cutting tools, mining equipment |
Chromium Carbide (Cr3C2) | Cr, C | Excellent corrosion resistance, hardness | Aerospace components, high-temperature environments |
Titanium Carbide (TiC) | Ti, C | High hardness, lightweight, corrosion resistance | Aerospace, automotive components |
Boron Carbide (B4C) | B, C | Very high hardness, lightweight | Ballistic armor, abrasives |
Silicon Carbide (SiC) | Si, C | High thermal conductivity, low thermal expansion | Power electronics, high-temperature applications |
Alumina (Al2O3) | Al, O | High hardness, good thermal stability | Wear-resistant coatings, electrical insulators |
Molybdenum Disulfide (MoS2) | Mo, S | Low friction, high wear resistance | Lubricants, aerospace, automotive |
Nickel-Chromium Alloy | Ni, Cr | High temperature oxidation resistance | Gas turbines, power plants |
Cobalt-Chromium Alloy | Co, Cr | Excellent wear resistance, corrosion resistance | Medical implants, aerospace |
Iron-Based Alloys | Fe, Various | Cost-effective, good wear resistance | Construction, heavy machinery |
The Role of Metals in Wear Resistance Powders
Metals like tungsten, chromium, and titanium are commonly used in wear resistance powders because of their inherent hardness and ability to withstand high temperatures. These metals form carbides or oxides that are incredibly tough and resistant to wear. For instance, Tungsten Carbide (WC) is one of the hardest known materials and is frequently used in cutting tools and mining equipment where high wear resistance is critical.
Tungsten Carbide: The Gold Standard in Wear Resistance
Tungsten Carbide is often referred to as the “gold standard” in wear resistance powders. It combines tungsten with carbon to form a material that is almost as hard as diamond. This makes it perfect for applications where tools and components are subjected to intense friction and heat. For example, in the oil and gas industry, drilling tools coated with tungsten carbide can withstand the extreme conditions deep underground, significantly extending their operational life.
Ceramics and Their Contribution to Wear Resistance
Ceramics, like silicon carbide and alumina, also play a crucial role in wear resistance powders. These materials are known for their hardness and thermal stability, making them ideal for applications where high temperatures are involved. Silicon Carbide (SiC), for example, is often used in power electronics and high-temperature applications due to its excellent thermal conductivity and low thermal expansion.
Silicon Carbide: A Powerhouse in High-Temperature Applications
When it comes to handling heat, silicon carbide is unmatched. This ceramic material is used in applications where traditional metals would fail due to excessive thermal expansion. For instance, in power electronics, silicon carbide helps manage heat efficiently, ensuring that components operate reliably even in extreme conditions.
How Composites Enhance Wear Resistance
In some cases, wear resistance powders are made from composite materials that combine metals and ceramics. These composites offer the best of both worlds: the toughness and ductility of metals, combined with the hardness and thermal stability of ceramics. This synergy results in a material that can withstand even the harshest conditions.
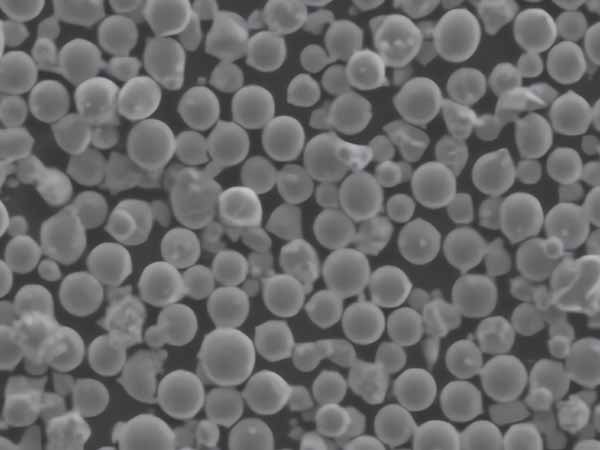
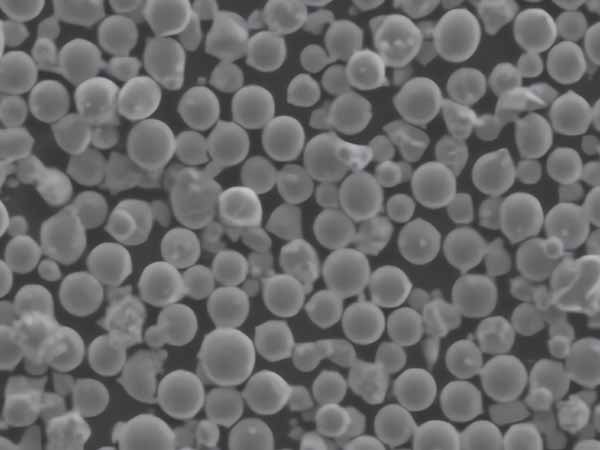
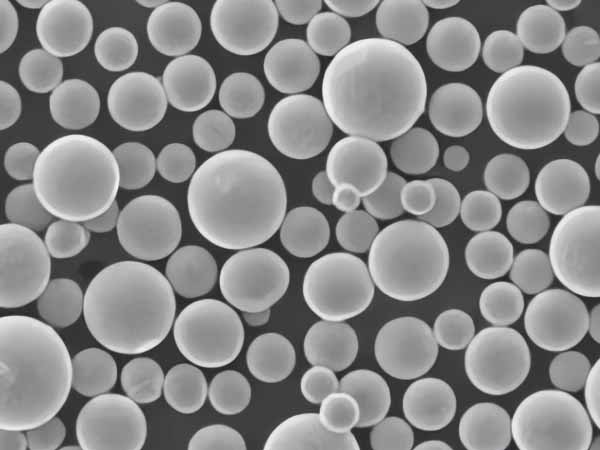
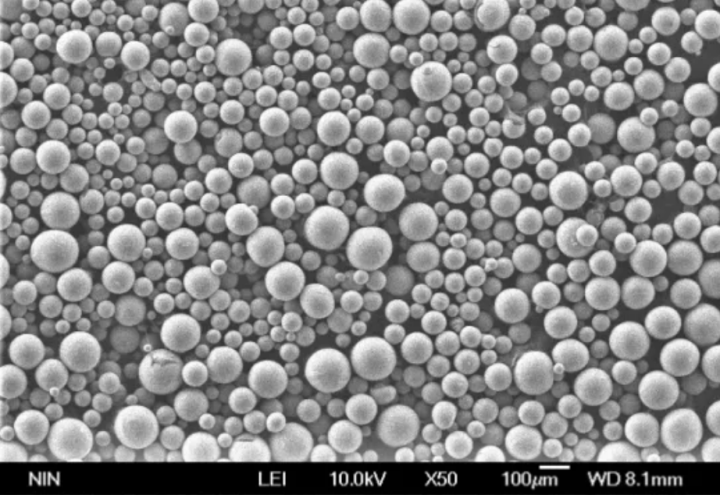
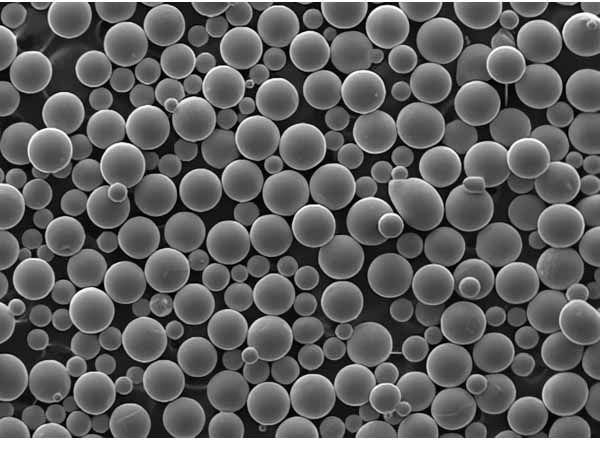
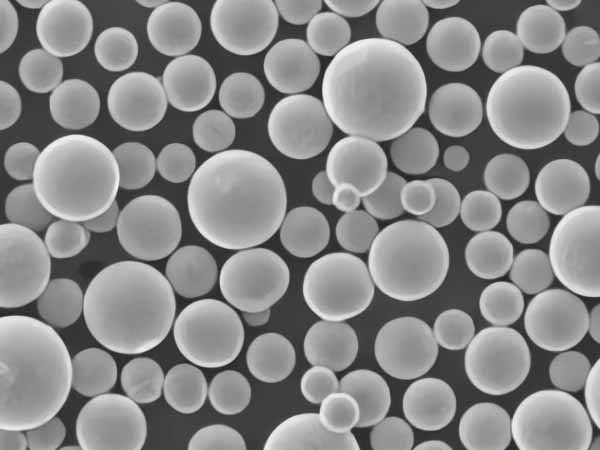
Characteristics of Wear Resistance Powder
Understanding the characteristics of wear resistance powder is essential for selecting the right material for your application. These characteristics include hardness, thermal stability, corrosion resistance, and more. Each characteristic plays a critical role in determining the performance of the powder in real-world applications.
Hardness: The Core of Wear Resistance
Hardness is perhaps the most important characteristic of wear resistance powders. It directly impacts the material’s ability to resist abrasion and wear. The harder the material, the more resistant it is to surface deformation and erosion. For instance, tungsten carbide, with its incredible hardness, is often used in tools and components that encounter high friction and wear.
Thermal Stability: Surviving the Heat
Thermal stability refers to a material’s ability to maintain its properties at high temperatures. In industries like aerospace and power generation, components are often exposed to extreme heat. Materials like silicon carbide and alumina, which maintain their hardness and strength at elevated temperatures, are crucial in these environments.
Corrosion Resistance: Withstanding the Elements
Corrosion resistance is another critical characteristic, especially in environments where the material is exposed to moisture, chemicals, or other corrosive elements. Chromium carbide and nickel-chromium alloys are known for their excellent corrosion resistance, making them ideal for use in harsh environments like marine or chemical processing industries.
Friction Coefficient: Reducing Wear through Lubrication
The friction coefficient of a material determines how much friction it will generate when in contact with another surface. A lower friction coefficient generally means less wear and tear on the material. For example, molybdenum disulfide has a very low friction coefficient, which makes it an excellent choice for lubrication applications in automotive and aerospace industries.
Table of Wear Resistance Powder Characteristics
Characteristic | Description | Example Materials |
---|---|---|
Hardness | Ability to resist surface deformation and wear. | Tungsten Carbide, Silicon Carbide |
Thermal Stability | Maintains properties at high temperatures. | Alumina, Silicon Carbide |
Corrosion Resistance | Ability to resist chemical degradation and corrosion. | Chromium Carbide, Nickel-Chromium |
Friction Coefficient | Determines the level of friction generated against other surfaces. | Molybdenum Disulfide, Cobalt-Chromium |
Toughness | Ability to absorb energy and deform without breaking. | Iron-Based Alloys, Nickel Alloys |
Density | Mass per unit volume, which impacts weight and strength. | Boron Carbide, Titanium Carbide |
Thermal Conductivity | Ability to conduct heat efficiently, reducing thermal stress. | Silicon Carbide, Tungsten Carbide |
Electrical Conductivity | Ability to conduct electricity, important for electronic applications. | Silicon Carbide, Molybdenum Disulfide |
Applications of Wear Resistance Powder
Wear resistance powders find applications across various industries, from aerospace to automotive to heavy machinery. Their ability to enhance the durability and lifespan of components makes them invaluable in environments where wear and tear are significant concerns.
Aerospace Industry: Flying High with Wear Resistance
In the aerospace industry, wear resistance powders are used to coat turbine blades, engine components, and other parts that experience extreme temperatures and
friction. For instance, nickel-chromium alloys are commonly used in gas turbines due to their excellent high-temperature oxidation resistance. These coatings help maintain the efficiency and reliability of aircraft engines, ensuring safe and smooth operations.
Automotive Industry: Driving Durability
In the automotive sector, wear resistance powders are used in various engine components, such as pistons, camshafts, and gears. Tungsten carbide and titanium carbide are often applied as coatings to these parts, reducing wear and extending their operational life. This not only improves the performance of vehicles but also reduces maintenance costs for car owners.
Mining and Drilling: Tough Enough for the Roughest Jobs
The mining and drilling industries are perhaps the most demanding environments for wear resistance powders. Drilling tools, conveyor belts, and crushers are all subjected to continuous abrasion and impact. Powders like tungsten carbide and boron carbide are essential in these applications, providing the necessary toughness and wear resistance to handle the harsh conditions underground.
Manufacturing: Ensuring Efficiency and Longevity
In manufacturing, wear resistance powders are used to coat cutting tools, molds, and other machinery components. This not only enhances the durability of the tools but also ensures consistent performance over time. For example, chromium carbide is often used in cutting tools for its excellent wear and corrosion resistance, allowing manufacturers to maintain high productivity levels.
Table of Wear Resistance Powder Applications
Industry | Applications | Common Materials Used |
---|---|---|
Aerospace | Turbine blades, engine components | Nickel-Chromium Alloy, Titanium Carbide |
Automotive | Pistons, camshafts, gears | Tungsten Carbide, Titanium Carbide |
Mining & Drilling | Drilling tools, conveyor belts, crushers | Tungsten Carbide, Boron Carbide |
Manufacturing | Cutting tools, molds, machinery components | Chromium Carbide, Silicon Carbide |
Power Generation | Gas turbines, power plant components | Nickel-Chromium Alloy, Silicon Carbide |
Medical Devices | Implants, surgical tools | Cobalt-Chromium Alloy, Titanium Carbide |
Electronics | Power electronics, heat sinks | Silicon Carbide, Alumina |
Marine | Ship hulls, underwater structures | Chromium Carbide, Nickel-Chromium Alloy |
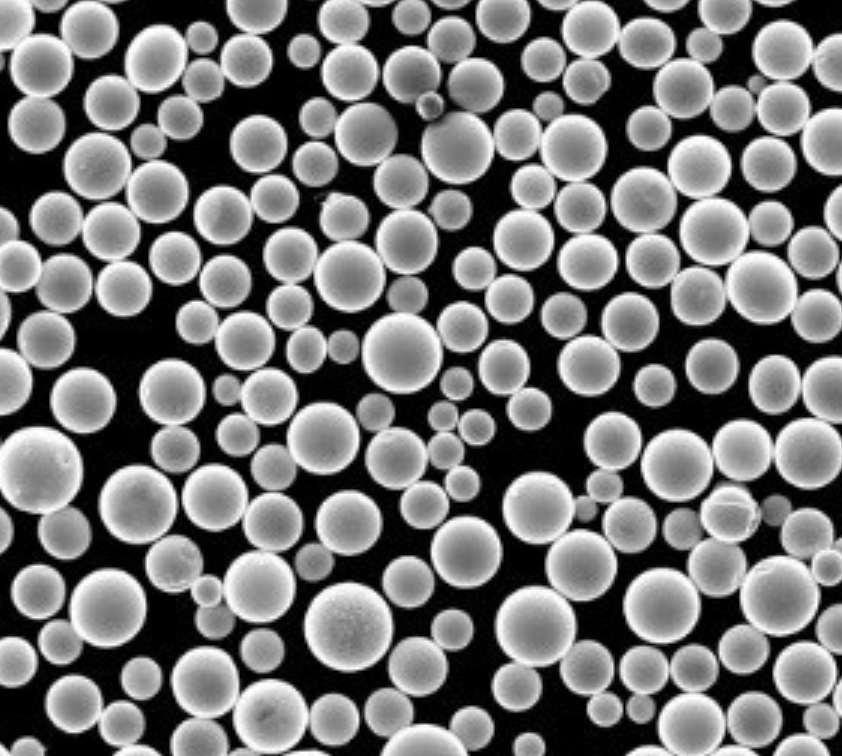
Specifications, Sizes, Grades, and Standards of Wear Resistance Powder
When selecting a wear resistance powder, it’s crucial to understand the specific grades, sizes, and standards that apply. These specifications ensure that the powder will meet the performance requirements for your application.
Understanding Grades and Sizes
Wear resistance powders come in various grades and particle sizes, each suited to different applications. For instance, a finer particle size might be required for coating applications where a smooth finish is essential, while coarser particles might be preferred for bulk applications like welding or thermal spraying.
Table of Wear Resistance Powder Specifications
Powder Type | Particle Size Range (µm) | Grade | Standard |
---|---|---|---|
Tungsten Carbide (WC) | 0.5 – 100 | A12, B20 | ASTM B777 |
Chromium Carbide (Cr3C2) | 0.5 – 120 | A40, B10 | ISO 10993 |
Titanium Carbide (TiC) | 1 – 150 | A15, B25 | ASTM F2885 |
Boron Carbide (B4C) | 0.1 – 90 | A50, B30 | MIL-STD-129 |
Silicon Carbide (SiC) | 0.2 – 150 | A16, B12 | JIS R6001 |
Alumina (Al2O3) | 0.3 – 100 | A11, B40 | ASTM C704 |
Molybdenum Disulfide (MoS2) | 0.5 – 60 | A22, B35 | AMS-M-7866 |
Nickel-Chromium Alloy | 1 – 200 | A18, B15 | AWS A5.21 |
Cobalt-Chromium Alloy | 0.3 – 150 | A32, B20 | ASTM F75 |
Iron-Based Alloys | 0.5 – 180 | A50, B10 | ASTM A681 |