Overview of AlSi7Mg Powder
AlSi7Mg powder is an aluminum alloy powder containing approximately 7% silicon and 0.3-0.45% magnesium. It is widely used for metal additive manufacturing processes like selective laser sintering (SLS) and direct metal laser sintering (DMLS) to create light-weight, high-strength aluminum parts with good thermal properties.
Some key features of AlSi7Mg alloy powder include:
- High strength-to-weight ratio
- Good corrosion resistance
- Excellent thermal conductivity
- Good dimensional stability
- Capability for complex geometries
- Surface finish similar to die casting
AlSi7Mg is considered an optimal material for aerospace, automotive, and industrial applications where light-weight and performance are critical. Parts made with AlSi7Mg powder can replace traditionally manufactured aluminum components and provide more design freedom.
AlSi7Mg Powder Types
There are a few variants of AlSi7Mg powders available for additive manufacturing:
Powder Type | Description | Characteristics |
---|---|---|
AlSi7Mg0.6 | Standard grade | Good spreadability, optimized particle size distribution |
AlSi10Mg | Higher silicon content | Improved hardness and wear resistance |
AlSi7Mg0.6 EOS | Optimized for EOS machines | Excellent flowability and spreadability |
AlSi7Mg Powder Characteristics
Here are some typical properties and characteristics of AlSi7Mg powders:
Parameter | Range |
---|---|
Particle size | 15-45 microns |
Flowability | Excellent |
Apparent density | 1.2-1.8 g/cm3 |
Tap density | 2.2-2.7 g/cm3 |
Residual oxygen content | < 0.5% |
Residual nitrogen content | < 0.3% |
Residual carbon content | < 0.1% |
Applications of AlSi7Mg Parts
AlSi7Mg is commonly used for manufacturing the following types of components:
Application | Example Components | Benefits |
---|---|---|
Aerospace | Brackets, air ducts, heat exchangers | Light-weight, corrosion resistance |
Automotive | Suspension components, transmission cases | High strength, thermal stability |
Industrial | Heat sinks, robotics parts, tooling | Dimensional accuracy, thermal conductivity |
Consumer | Drone components, sporting goods | Complex geometry, surface finish |

AlSi7Mg Powder Specifications
AlSi7Mg powder for additive manufacturing needs to meet certain chemical composition and particle morphology specifications for optimal performance.
Chemical Composition
The typical chemical composition limits of AlSi7Mg powder are:
Element | Weight % |
---|---|
Aluminum | Base |
Silicon | 6-8% |
Magnesium | 0.25-0.45% |
Iron | < 0.55% |
Copper | < 0.05% |
Manganese | < 0.45% |
Nickel | < 0.05% |
Zinc | < 0.10% |
Lead | < 0.05% |
Tin | < 0.05% |
Silicon and magnesium are intentionally added to enhance strength, hardness, weldability. The limits on impurity elements help ensure powder quality.
Particle Morphology
The particle size distribution, shape and flow characteristics dictate the powder spreading and melting behavior:
- Particle size between 15-45 microns, normally distributed
- Spherical morphology with smooth surface
- Apparent density: 1.2-1.8 g/cm3
- Tap density: 2.2-2.7 g/cm3
- Flow rate: 25-35 s/50g
- Hausner ratio: 1.25-1.5
AlSi7Mg Design and Printing Parameters
Here are some typical parameters used for designing and 3D printing components with AlSi7Mg powder:
Parameter | Typical Value |
---|---|
Layer thickness | 20-100 microns |
Laser power | 180-400 W |
Scan speed | 800-2500 mm/s |
Hatch spacing | 0.1-0.2 mm |
Supports | Required for overhangs |
Heat treatment | T6 temper |
- Complexity should be controlled to allow excess powder removal
- Minimum wall thickness of 0.3-0.4 mm is recommended
- Post-processing like powder removal, heat treatment, finishing is required
Suppliers of AlSi7Mg Powder
There are a number of reputable suppliers that provide high quality AlSi7Mg powder for additive manufacturing:
Supplier | Description |
---|---|
AP&C | Wide range of Al alloys, global presence |
Carpenter Additive | Good availability, small to large quantities |
EOS | OEM powder optimized for EOS machines |
LPW Technology | Custom alloys possible, high purity |
Sandvik Osprey | Leading supplier, global distribution network |
Typical pricing for AlSi7Mg powder is in the range of $80-100/kg for orders above 100 kg. Lower quantities can be 50-100% higher priced.
Installation, Operation, and Maintenance of Metal Printers
Installation
- Install printer on a stable, flat, and level surface
- Ensure room temperature between 20-25°C with minimal temperature fluctuations
- Keep humidify between 20-70% for powder handling
- Provide compressed air or nitrogen supply if required
- Install supplementary cooling or heating if ambient conditions vary
- Setup powder recycling system and post-processing stations
Operation
- Perform regular calibration, quality checks as per manufacturer
- Do visual inspection of parts during build
- Use recommended parameters based on part geometry, quality needs, and materials
- Monitor the build chamber temperature, oxygen levels, etc.
- Sieve and blend powder between builds to refresh material
- Ensure no moisture exposure during powder handling
Maintenance
- Follow daily, weekly, and monthly maintenance schedules
- Keep machine and build chamber clean from powder spillage
- Inspect critical components like recoater blade and filters periodically
- Monitor and log errors, anomalies in log book
- Lubricate moving parts as per maintenance manual
- Validate, calibrate sensors and lasers periodically
- Schedule preventive maintenance from OEM technicians
Proper installation, operation, and maintenance is critical to achieve consistent, high-quality 3D printed parts.
How to Select AlSi7Mg Powder Suppliers
Here are some tips on selecting a reputable AlSi7Mg powder supplier for your metal AM application needs:
- Qualifications – Supplier should have AS9100/ISO quality certifications specifically for AM powder production
- Technical Capability – Ability to customize alloys, modify particle characteristics, and conduct application testing
- Quality Control – Supplier should have strict quality control and sample testing protocols for each powder lot
- Industry Experience – Number of years supplying powder to AM industry, customer base and success stories
- R&D – Investment in ongoing R&D to enhance AM powder quality and printability
- Cost Effectiveness – Balance cost vs quality and consistency to maximize value
- Lead Time – Supplier capability to meet delivery timelines for the quantity needed
- Customer Service – Responsiveness to queries, technical support, after-sales service
It is recommended to evaluate a few potential suppliers, get reference samples, review technical data, and validate print results before large volume procurements.
Pros and Cons of AlSi7Mg Powder
AlSi7Mg is a versatile aluminum alloy powder but has some limitations too.
Pros
- High strength-to-weight ratio
- Good thermal conductivity
- Excellent dimensional accuracy
- Capable of complex geometries
- Corrosion and wear resistance
- Widely available and cost-effective
Cons
- Lower maximum temperature resistance than steels
- Susceptible to porosity defects if improperly printed
- Lower hardness than high-silicon Al alloys
- Requires post-processing and heat treatment
- Surface finish inferior to die cast parts
For most applications, the pros of light-weight, performance, and geometric freedom outweigh the cons. Parameter optimization and quality control during printing improves results.
How AlSi7Mg Powder Compares to Alternatives
AlSi7Mg is compared below to some alternative alloy powders for additive manufacturing:
Alloy | AlSi7Mg | AlSi10Mg | Aluminum 6061 | Titanium Ti6Al4V |
---|---|---|---|---|
Density | 2.7 g/cm3 | 2.7 g/cm3 | 2.7 g/cm3 | 4.4 g/cm3 |
Tensile Strength | 430 MPa | 480 MPa | 230 MPa | 850 MPa |
Elongation | 8% | 3% | 12% | 10% |
Thermal Conductivity | 150 W/m-K | 150 W/m-K | 180 W/m-K | 7 W/m-K |
Corrosion Resistance | Good | Good | Moderate | Excellent |
Max Service Temp | 200°C | 250°C | 330°C | 550°C |
Lead Time | Short | Medium | Short | Long |
Cost | Low | Medium | Low | High |
For most light-weighting applications, AlSi7Mg provides the best balance of strength, thermal properties, manufacturability, and cost. Higher silicon Al alloys improve hardness and temperature resistance but reduce ductility. Titanium alloys provide superior properties but at higher cost and lead times.
How to Choose Between AlSi7Mg Powder Suppliers
Choosing the right AlSi7Mg powder supplier depends on several factors:
Quality and consistency
- Supplier should have strict quality control standards and procedures
- Chemical assay, particle morphology, microstructure uniform between lots
- Customer reject rates and feedback on powder performance
Technical support
- Capability to customize alloys, conduct application tests
- Recommendations on printing parameters based on experience
- Quick response to technical queries and sample analysis
Availability and delivery
- Ability to supply small prototyping orders to bulk quantities
- Reasonable lead times for both standard and custom materials
Pricing
- Balance cost vs performance based on application needs
- Value added services like sieving, blending, research support
Customer service
- Responsiveness to requests, quotes, concerns
- Professionalism and technical expertise of team
Certifications
- Quality management system certification like ISO 9001
- Industry specific AM powder certifications
It is recommended to qualify at least 2-3 suppliers through testing to ensure security of supply.
Applications of AlSi7Mg in Key Industries
AlSi7Mg finds widespread use in aerospace, automotive, industrial, and consumer sectors.
Aerospace
- Structural brackets, airframe components, heat exchangers
- Engine and landing gear parts subject to high loads
- Complex geometries not possible by casting or machining
- 30-60% weight savings versus aluminum alloys
Automotive
- Powertrain parts like pistons, turbochargers, transmission cases
- High temperature resistance for engine components
- Strong and rigid suspension parts
- Customized designs for performance gains
Industrial
- Robotics components with strength, vibration resistance
- Jigs, fixtures, press tools with durability and dimensional stability
- Customized grippers, end-effectors for productivity
- Low-volume production of obsolete spare parts
Consumer
- Lightweight drones, quadcopters with high strength frames
- Athletic gear like golf clubs, bicycle parts
- High performance RC car components
- Customized orthotic and prosthetic devices
AlSi7Mg allows engineers to maximize performance, customization, and weight savings across these industries.
How Material Composition Influences AlSi7Mg Powder Properties
The unique properties of AlSi7Mg powder stem from its underlying material composition and microstructure.
Role of Aluminum
The aluminum matrix provides:
- Low density – 2.7 g/cm3 density versus 7.8 g/cm3 for steel
- Excellent thermal conductivity for heat dissipation
- High reflectivity and non-magnetic properties
Role of Silicon
The silicon alloying element:
- Increases strength through precipitation hardening
- Enhances castability and weldability
- Improves wear resistance through hard Si particles
- Reduces coefficient of thermal expansion
Role of Magnesium
Addition of magnesium:
- Strengthens the alloy through solid solution strengthening
- Improves mechanical properties like ductility
- Assists in grain structure control
Alloy Microstructure
Key phases in AlSi7Mg microstructure:
- Primary alpha-Al matrix
- Silicon particles – increases hardness
- Intermetallic phases – improves strength
- Grain refinement with uniform fine grains
This optimized composition provides a great balance of strength, ductility, thermal stability, and corrosion resistance needed for AM.
Design Principles for AlSi7Mg Parts
Here are some design guidelines to follow when designing components to be 3D printed with AlSi7Mg powder:
- Optimize wall thickness to 0.3 – 0.8mm for good mechanical properties
- Include fillets and rounds with minimum radius > 0.5mm to reduce stress concentrations
- Design fine cooling channels and lattices to improve heat transfer if needed
- Allow for post-machining by having overall stock dimensions slightly larger
- Design with support structures in mind – minimize large overhangs and angles below 45°
- Avoid huge variations in cross-sectional area along build direction
- Include holes/bores slightly undersized to allow for post-processing
- Minimize enclosed volumes to facilitate powder removal after printing
- Ensure components can be easily removed from build plate without damage
Following design-for-AM principles allows realizing the full benefits of 3D printing with AlSi7Mg powder.
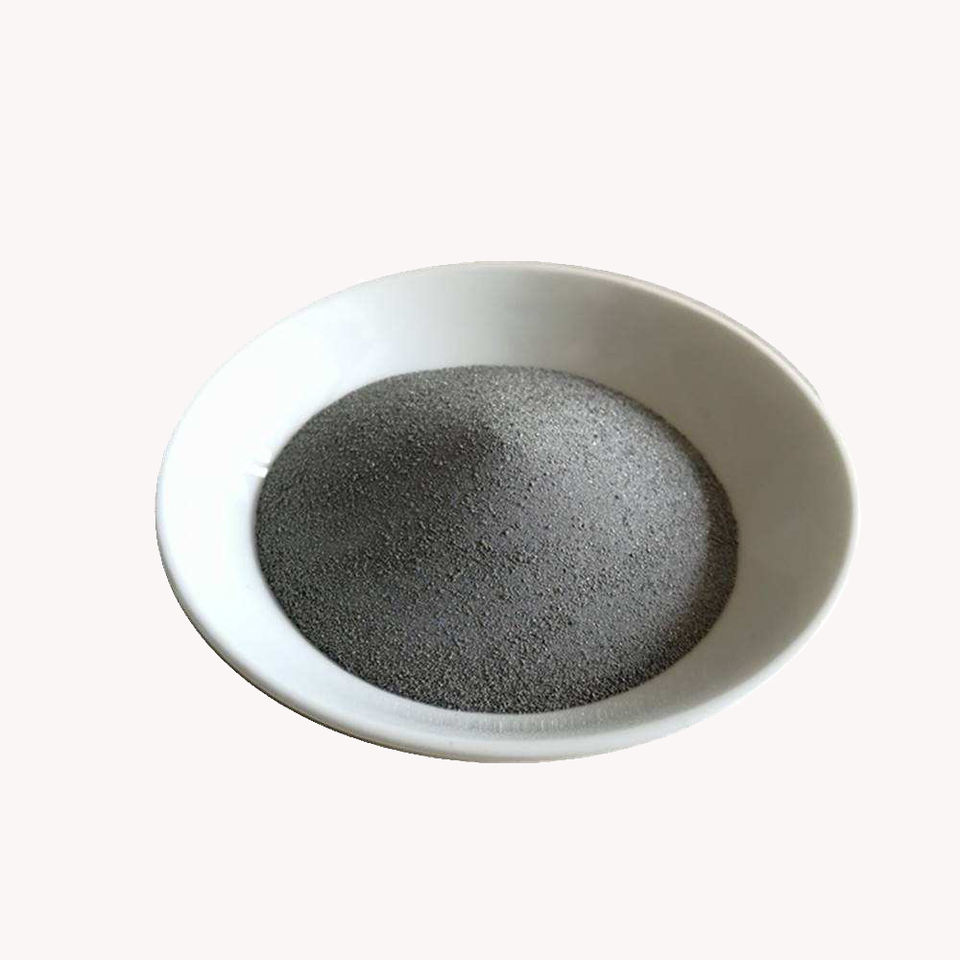
How to Optimize AlSi7Mg Printing Process
Optimizing the AlSi7Mg printing process involves finding the right combination of parameters, powder quality, and post-processing.
Printing Parameters
- Use 30-100 micron layer thickness for good surface finish and resolution
- Test different laser power, scan speeds, hatch spacing for your particular component geometry
- Optimize scan strategy – stripes vs chessboard, alternating directions between layers
- Orient part to minimize supports and avoid large overhangs
Powder
- Use high quality powder with good flowability, optimized particle size distribution
- Consider using fresh powder or sieve/blend between prints for consistency
- Pre-dry powder for 1-4 hours at 80-100°C to remove moisture
Post-Processing
- Stress relief heat treatment to relieve residual stresses
- HIP (Hot Isostatic Pressing) to eliminate internal voids
- Machining/grinding to refine surface roughness and achieve critical dimensions
- T6 heat treatment for maximum strength and hardness
- Shot peening to improve surface finish and fatigue resistance
Continual testing and process refinement is key to producing high-quality AlSi7Mg parts consistently.
AlSi7Mg Powder for Aerospace Applications
AlSi7Mg has emerged as a metal powder alloy of choice for aerospace parts due to its excellent strength-to-weight ratio.
Benefits for Aerospace
- 30% lighter than titanium alloys, 60% lighter than nickel alloys
- Resists fatigue, corrosion cracking, and creep deformation
- Stable at higher temperatures up to 300°C
- Smoother surfaces than direct metal laser sintering (DMLS)
Example Components
Typical aircraft components manufactured include:
- Structural brackets, hydraulic manifolds, fuel lines
- Wing and landing gear parts subjected to dynamic loads
- Engine mounts, housings, heat exchangers
- Conformal cooling channels for tooling
Aerospace Standards
Key standards include:
- AMS 4242 – composition limits for AlSi7Mg casting alloys
- AMS 7001 – AM aluminum powder classification system
- AMS 7016 – specifications for AlSi7Mg AM powder
- AMS 7032 – quality requirements for AM aerospace parts
Qualifications
Extensive testing is required to qualify AlSi7Mg printed parts for flight:
- Tensile, fatigue, fracture toughness, corrosion, thermal
- Conformity to CAD models – GD&T
- Non-destructive inspection – CT scans, X-ray
- Microstructure characterization
- Comparison to forged parts
AlSi7Mg enables lighter, stronger, and higher-performing aircraft designs not possible with conventional manufacturing.
AlSi7Mg for Automotive Applications
AlSi7Mg powder is advantageous for printing lightweight, high-strength automotive components.
Benefits
- Up to 50% weight reduction versus cast aluminum alloys
- Components consolidated into single 3D printed part
- Customizable designs for improved functionality
- Less material waste compared to machining
Example Components
- Pistons – optimized cooling gallery designs
- Cylinder heads – high temperatures, pressure loads
- Brake discs – resistance to wear and high temperatures
- Suspension parts – high strength and fatigue life
Automotive Standards
Relevant standards include:
- ISO 17296-3 – specifications for AM metallic parts
- ASTM F3001 – standard for AM medical/aerospace alloys
- VDA 6.1 – surface finish requirements
- Custom OEM standards – e.g. VAG 4657
Automotive Qualification
Qualification testing covers:
- Tensile, compression, fatigue, fracture, impact properties
- Corrosion resistance – salt spray, atmosphere tests
- Validation of mechanical properties over service life
- Optical and SEM microstructure characterization
- Density analysis using
Trends and Developments in AlSi7Mg Powder
The AlSi7Mg alloy system continues to evolve with new powder developments and printing innovations.
Powder Improvements
- Increased silicon content for higher strength – AlSi10Mg, AlSi12Mg alloys
- Fine powder for better resolution – 5-25 micron particle sizes
- Lower oxygen and nitrogen impurity levels
- Better powder flow and spreadability
Printer Capabilities
- Larger build volumes up to 500 x 500 x 500 mm
- Multi-laser systems for higher productivity
- Closed-loop process control for consistency
- Integrated powder handling and recycling
Post-Processing
- Automated support removal and surface finishing
- Integrated heat treatment furnaces
- Ability to hot isostatic press (HIP) parts in-situ
- Automated inspection using CT scanning
Applications
- Increased use in structural aircraft components
- High-volume automotive parts like wheel hubs
- Custom orthopedic implants with lattice structures
- Conformal cooling channels in injection molds
Advancements across the additive manufacturing workflow will expand adoption of AlSi7Mg for mission-critical applications.
Challenges and Limitations of AlSi7Mg Powder
Despite its strengths, AlSi7Mg poses some challenges that engineers should be aware of.
Metallurgical Challenges
- Solidification cracking tendency – careful solidification control needed
- Porosity due to gas entrapment – process optimization required
- Heat treatment can cause dimensional changes
Print Challenges
- High reflectivity demands higher laser power
- Hard to achieve surface finish of cast parts
- Residual stress can distort parts or cause cracking
Performance Limits
- Low hardness and wear resistance compared to steels
- Not suitable for high temperature applications above 300°C
- Lower strength than high-silicon Al alloys like AlSi12Mg
Production Challenges
- Currently limited to aerospace and automotive – high cost
- Post-processing time and cost
- Validation and qualification effort
With continual development of alloys, parameters, and technology, AlSi7Mg AM capabilities will advance significantly.
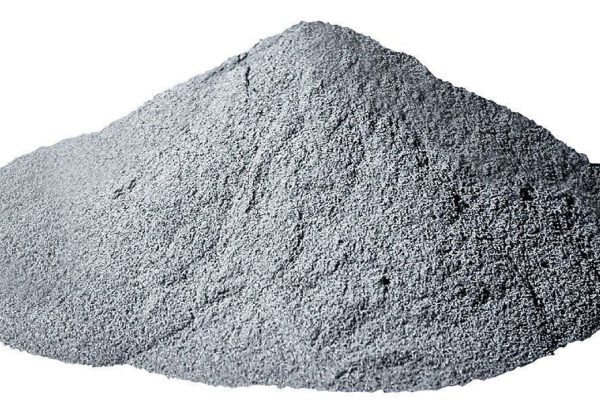
FAQs
Here are some frequently asked questions about AlSi7Mg powder for metal additive manufacturing:
What are the main advantages of AlSi7Mg?
AlSi7Mg provides an excellent strength-to-weight ratio combined with good ductility, thermal properties, and corrosion resistance. It enables light-weighting and design freedom.
What industries typically use AlSi7Mg?
Aerospace and automotive are the main industries using AlSi7Mg powder currently. But there is increasing adoption in industrial machinery, medical devices, and consumer products.
What is the typical cost of AlSi7Mg powder?
AlSi7Mg powder costs around $80-120 per kg currently, with aerospace grades at the higher end. Prices vary based on quantity and supplier.
What heat treatment is used for AlSi7Mg parts?
A T6 heat treatment is commonly used – solutionizing, quenching, and artificial aging to achieve peak strength. HIP can also be used.
Does AlSi7Mg require supports during printing?
Yes, supports are needed during printing to avoid deformation and prevent overhangs from drooping or warping.
What standards are applicable to AlSi7Mg powder?
Key standards are AMS 4242 for composition, AMS 7001 for classification, and AMS 7016 for AM powder specifications.
What post-processing is required for AlSi7Mg parts?
Post-processing steps include support removal, heat treatment, HIP, machining, grinding, polishing, and coating. This improves finish and properties.
What typical surface finish can be expected with AlSi7Mg printing?
With process optimization, a surface roughness of around 10-15 microns Ra can be achieved for AlSi7Mg printed parts.
Are there health and safety risks with AlSi7Mg powder?
Like other metal powders, it can be reactive and combustible, so precautions are needed during handling and storage. Proper PPE should be used.