Inconel 738 powder is a nickel-based superalloy powder used primarily in the aerospace industry for gas turbine engine components. This high performance alloy offers excellent mechanical properties and resistance to heat and corrosion.
Overview of Inconel 738 Powder
Inconel 738 powder is a precipitation hardened nickel chromium alloy also containing aluminum, cobalt, molybdenum, titanium, tungsten, niobium and tantalum as minor alloying elements.
Key properties and characteristics of Inconel 738 powder include:
Properties | Characteristics |
---|---|
Composition | Nickel, Chromium, Aluminum, Cobalt, Molybdenum, Titanium, Tungsten, Niobium, Tantalum |
Particle shape | Spherical |
Particle size | 15 – 45 microns |
Melting point | ~1400°C |
Density | 8.15 g/cm<sup>3</sup> |
Key attributes | High strength, Good corrosion resistance, Excellent creep resistance, Retains strength at high temperatures |
Manufacturing processes | Additive manufacturing including DMLS, LENS |
Applications | Turbine blades, Turbocharger components, Combustion cans |
Some of the key advantages of Inconel 738 powder include:
- High tensile, fatigue and creep rupture strength
- Ability to withstand operating temperatures up to 750°C
- Good oxidation and corrosion resistance
- High thermal stability
However, limitations include lower processability compared to other superalloys, as well as high material costs.
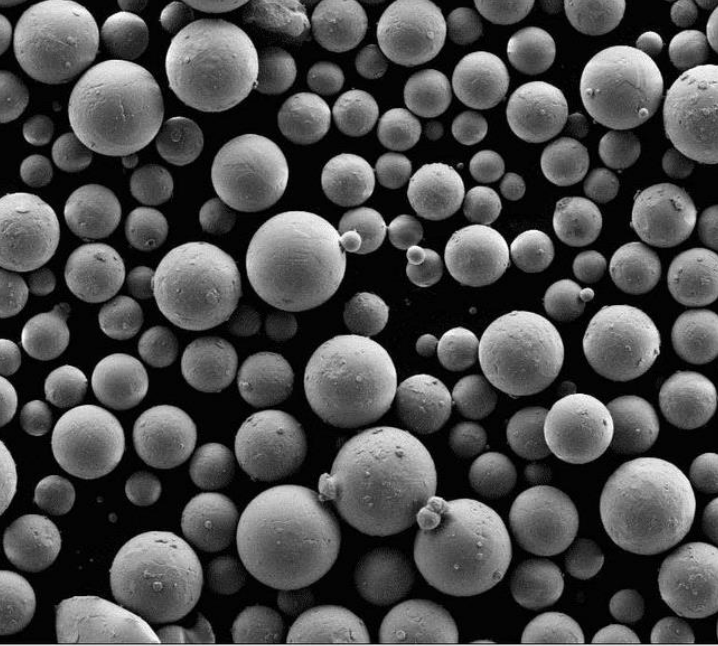
Chemical Composition
The nominal chemical composition of Inconel 738 powder is given below:
Element | Weight % |
---|---|
Nickel (Ni) | Balance |
Chromium (Cr) | 15 – 17% |
Aluminum (Al) | 3 – 4% |
Cobalt (Co) | 8 – 10% |
Molybdenum (Mo) | 1.5 – 2.5% |
Titanium (Ti) | 0.7 – 1.2% |
Tungsten (W) | 2 – 3% |
Niobium (Nb) | 0.1 – 0.6% |
Tantalum (Ta) | 0.5 – 1.5% |
The combination of nickel, chromium and aluminum imparts corrosion resistance. Elements like molybdenum and tungsten enhance high temperature strength via solid solution strengthening. Meanwhile, additions of cobalt improve hot workability.
Trace amounts of carbon, manganese, silicon, phosphorus, sulfur and boron may also be present. The composition is controlled as per ISO standard 21332 for Inconel 738 powder to ensure consistent properties during additive manufacturing or other powder metallurgy applications.
Mechanical Properties
Inconel 738 powder can achieve the following mechanical properties in heat treated condition:
Property | Value |
---|---|
Tensile strength | 1050 – 1300 MPa |
0.2% Yield strength | ≥ 900 MPa |
Elongation | ≥ 16% |
Reduction in area | ≥ 25% |
Hardness | ≥ 390 HV |
The properties vary based on exact composition within alloy spec limits, powder quality and parameters used during additive manufacturing. Heat treatments like aging after manufacturing also impact mechanical performance.
Compared to Inconel 718, Inconel 738 demonstrates nearly 15-20% higher tensile and creep rupture strength owing to minor additions like tantalum and niobium. However, fabricability is lower for 738 material systems.
Applications
Some typical applications of Inconel 738 powder include:
Industry | Applications |
---|---|
Aerospace | Turbine blades, Combustion cans/liners, Turbocharger components |
Automotive | Turbocharger wheels and housings, Exhaust valves |
Oil and gas | Downhole safety valves, Wellhead components |
Power generation | Gas turbine hot section parts |
Chemical processing | Reactor internals, Scrubbers, Cyclone components |
The primary use of Inconel 738 powder is in manufacturing hot section aeroengine components via additive manufacturing or other powder bed processes allowing complex, lightweight geometries.
Properties like high temperature tensile strength, resistance to creep deformation and fatigue make this an optimal material for turbo machinery applications seeing temperatures of 700°C or greater in service.
Specifications and Grades
Globally, Inconel 738 powder is manufactured to meet the following specifications:
Specification | Grade Designation |
---|---|
AMS 5899 | Alloy 738 |
ISO 21332 | PK-MET740Y |
UNS N07738 | – |
Equivalents include Alloy 738 LC (Low Carbon) and Cronal 738. Functionally similar superalloys include HS 188 and Mar-M 738.
Powder particle size distribution as per ISO 21332 is given below for reference:
Particle Size (μm) | Amount (%) |
---|---|
>150 | 0 |
106 – 150 | ≤ 6 |
45 – 106 | Balance |
<45 | ≤ 10 |
Finer particle size distributions resulting in better density and mechanical properties are also available. Grades optimized for additive manufacturing with high sphericity and flowability have also been developed.
-
CM247LC Powder | Nickel Alloy Powder
-
0# Pure Nickel powder
-
NiCoCrAlY alloys powders
-
Rene 142 alloy-Rene Powder
-
Haynes 25 Haynes Powder
-
Best Hastelloy C-22 Powder-High temperature alloy Powder for 3D Printing
-
Best Hastelloy C-276 Powder-High temperature alloy Powder for 3D Printing
-
Best Hastelloy N Powder-High temperature alloy Powder for 3D Printing
-
Best Hastelloy B Powder丨High temperature alloy Powder for 3D Printing
Suppliers and Pricing
Some leading global suppliers of Inconel 738 powder include:
Supplier | Product Designation | Price Range ($/kg) |
---|---|---|
Sandvik Osprey | Osprey® 738 | 450 – 750 |
Carpenter Additive | CARPENTER® Alloy 738 | 500 – 850 |
Praxair | TA1 738 | 425 – 700 |
Höganäs | Höganäs 738 | 400 – 650 |
LPW Technology | LPW 738 | 375 – 600 |
Pricing varies based on order quantity, particle size range, location and customization for AM optimization. Small lab samples tend to cost more on a per kilogram basis.
Cost Comparison With Inconel 718 Powder
Factor | Inconel 738 | Inconel 718 |
---|---|---|
Relative Price | 1.4X | 1X |
Density | Higher by 5% | – |
Despite higher alloying content, Inconel 738 powder can demonstrate cost benefits for high temperature applications owing to increased mechanical performance.
Advantages and Limitations
Advantages | Limitations |
---|---|
~15% higher tensile and creep rupture strength than Inconel 718 | More difficult to machine and weld |
Retains strength up to 750°C | Higher material costs |
Excellent oxidation and corrosion resistance | Lower fabricability than Inconel 718 |
Thermal stability in cryogenic conditions | Tendency for strain-age cracking |
Higher hardness than Inconel 625 or Waspaloy® | Sensitive to variations in heat treatment |
Cost advantage on basis of performance | – |
Key Takeaways
- Inconel 738 demonstrates strength and temperature capability improvement over 718 but with fabricability challenges
- Powder customized for additive manufacturing now available
- Qualifies as value engineering alternative for extreme environments
FAQs
Q: What is Inconel 738 powder typically used for?
A: Inconel 738 powder sees primary usage in additive manufacturing of hot section aerospace components like turbine blades, turbocharger wheels and combustor cans able to withstand 700°C plus temperatures.
Q: Does Inconel 738 require heat treatment?
A: Yes, Inconel 738 powder is precipitation hardenable via aging heat treatments. Solution treatment followed by double aging allows achieving optimal combination of ductility and high temperature strength.
Q: What particle size is best suited for AM?
A: Particle size range between 20-45 microns offers optimal powder bed density and mechanical performance. However, special grades are available with controlled sphericity and flow characteristics to improve processability.
Q: Is Inconel 738 weldable?
A: Inconel 738 shows lower weldability than 718 due to higher alloying additions. Matching filler material composition to base metal is absolutely necessary to minimize possibility of strain-age or liquidation cracking during welding.
Q: What is the difference between Inconel 738 vs 718?
A: Inconel 738 demonstrates over 15% higher tensile and creep rupture strength over 718 owing to additions like tantalum and niobium. However, 738 is more difficult to fabricate by either welding or machining processes.
Q: Does Inconel 738 require hot isostatic pressing (HIP) after AM?
A: HIP is recommended after additive manufacturing Inconel 738 components to eliminate internal porosity, impart 100% density and achieve optimal mechanical properties. HIP at 1160-1200°C under 100-150 MPa pressure is typically used.