Titanium alloy Ti6Al4V powder is an important engineering material valued for its high strength-to-weight ratio, corrosion resistance, and biocompatibility. This article provides a comprehensive technical reference on Ti6Al4V powder covering composition, properties, applications, specifications, pricing, and more.
Ti6Al4V Powder Composition
Ti6Al4V powder contains the following elemental composition by weight percentage:
Element | Weight % |
---|---|
Titanium (Ti) | Balance |
Aluminum (Al) | 5.5-6.75% |
Vanadium (V) | 3.5-4.5% |
Oxygen (O) | <0.2% |
Iron (Fe) | <0.3% |
Carbon (C) | <0.1% |
Nitrogen (N) | <0.05% |
The combination of aluminum and vanadium as the key alloying elements in a titanium matrix provides Ti6Al4V powder with its advantageous mechanical properties and performance characteristics.
Careful control of interstitial elements like oxygen, iron, carbon, and nitrogen during production is critical as higher levels negatively impact ductility and fracture toughness.
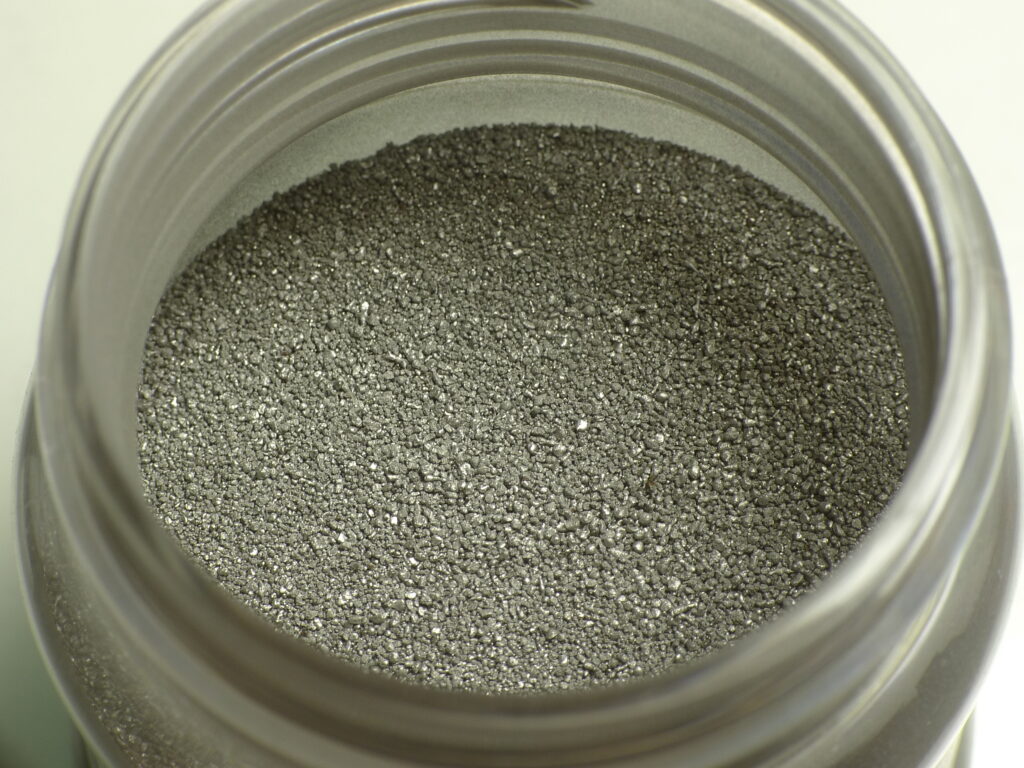
Ti6Al4V Powder Properties
Ti6Al4V powder offers the following balance of physical, mechanical, and performance properties:
Ti6Al4V Powder Properties
Property | Value |
---|---|
Density | 4.43 g/cm3 |
Melting Point | 1604-1660°C |
Thermal Conductivity | 6.7 W/m-K |
Electrical Resistivity | 1.78 microhm-cm |
Tensile Strength | 895-930 MPa |
Yield Strength | 825-869 MPa |
Elongation at Break | 10-15% |
Young’s Modulus | 110-120 GPa |
Shear Modulus | 44 GPa |
Poisson’s Ratio | 0.32-0.34 |
Fatigue Strength | 400-500 MPa |
Fracture Toughness | 55-115 MPa-m^1/2 |
Biocompatibility | Excellent |
Corrosion Resistance | Excellent |
The high strength and stiffness to weight ratio, fatigue resistance, and biocompatibility make Ti6Al4V a versatile and widely used titanium alloy.
Applications and Uses of Ti6Al4V Powder
The combination of high strength, relatively low density, corrosion resistance and biocompatibility of Ti6Al4V powder makes it an ideal choice for the following applications across industries like aerospace, medical, marine, and more:
Ti6Al4V Powder Applications
Industry | Applications |
---|---|
Aerospace | Structural components, aircraft landing gear, turbine blades, fasteners |
Biomedical | Orthopedic implants, dental implants, surgical instruments |
Automotive | Connecting rods, valves, springs, fasteners |
Chemical Plants | Pumps, valves, heat exchangers, reaction vessels |
Marine | Propellers, offshore platform parts, desalination plants |
Oil and Gas | Drill collars, subsurface well hardware |
Sports Equipment | Bicycle frames, golf clubs, lacrosse sticks |
Ti6Al4V powder is used across critical and demanding applications where high-performance under extreme conditions is required. Its versatility enables usage in load-bearing implants and devices, rotating components, corrosive environments, energy generation hardware, and high-end consumer products alike.
Ti6Al4V Powder Specifications
Ti6Al4V powder is available in different size ranges, compositions, production methods, and conformance to various standards for quality requirements:
Ti6Al4V Powder Specifications
Parameter | Specifications |
---|---|
Size range | 15-45 microns |
Production Method | Gas atomization |
Purity | Grade 23 per AMS 4911 |
Oxygen Content | <0.13% |
Nitrogen Content | <0.05% |
Hydrogen Content | <0.0125% |
Iron Content | <0.25% |
Standards | ASTM F2924, ASTM F3001 |
Controlling powder characteristics like particle size distribution, morphology, chemistry, and microstructure is critical to using Ti6Al4V powder feedstock in AM processes like laser/electron beam powder bed fusion and directed energy deposition.
How is Ti6Al4V Powder Produced?
There are three primary production methods for Ti6Al4V alloy powder:
- Gas Atomization – High pressure inert gas (Ar or N2) disintegrates molten Ti6Al4V alloy stream into fine droplets that solidify into spherical powders. Most common method.
- Plasma Rotating Electrode Process (PREP) – Electrodes of Ti6Al4V rotate at high speeds while being melted by plasma torches to disperse micro-droplets that solidify into spherical powders. Lower oxygen content.
- Hydriding-Dehydriding (HDH) – Hydrogenation and dehydrogenation of Ti6Al4V chips/turnings to make brittle flakes that are crushed and sieved into fine powders. Most economical process.
Gas atomized and PREP powders have higher sphericity and flowability suitable for AM processes while HDH powders meet requirements for pressing-and-sintering. Production method controls final particle characteristics.
How Much Does Ti6Al4V Powder Cost?
As a premium aerospace grade alloy powder, Ti6Al4V does not come cheap. Nonetheless, it is one of the most affordable titanium alloy options. Current pricing is:
Ti6Al4V Powder Pricing
Size Range | Price per Kg |
---|---|
15-45 microns | $75-$215 |
45-106 microns | $55-$195 |
106-150 microns | $35-$115 |
Prices vary based on:
- Quantity – Bulk orders get discounted rates
- Quality – Tighter chemistry and particle controls means higher cost
- Source – Domestic producers charge more than Chinese/Russian vendors
Consider total landed cost including logistics when comparing Ti6Al4V powder prices between global suppliers.
How to Choose Ti6Al4V Powder?
Here are the key considerations for choosing appropriate grade and quality of Ti6Al4V alloy powder:
Ti6Al4V Powder Selection Criteria
Parameter | Importance |
---|---|
Particle size range | Critical based on AM process requirements |
Powder morphology | Highly spherical and flowable powders preferred |
Purity level | Stricter controls for biomedical vs. industrial apps |
Oxygen/Nitrogen content | Lower the better for mechanical properties |
Production method | Significant impact on powder characteristics |
Sampling standards | Representative samples essential for quality |
Certificates | Review critically to verify compliance claims |
Application requirements for mechanical performance, post-processing needs, operating conditions, and safety factors determine exact powder grade selection.
Qualifying Ti6Al4V Powder Suppliers
With the growth of metal AM, many new entrants offer Ti6Al4V powder. However, aerospace/biomedical sectors have stringent requirements for quality documentation, sampling protocols, and traceability.
Here are key considerations in qualifying and approving Ti6Al4V powder suppliers:
Ti6Al4V Powder Supplier Checklist
Parameter | Details |
---|---|
Production capacity | Ensure stable long-term ability to deliver |
Quality certifications | AS9100, ISO 9001 required |
Testing capabilities | In-house chemical/mechanical testing essential |
Sampling standards | Representative sampling following ASTM guidelines |
Documentation | Complete banch-wise details for full traceability |
Change notifications | Communicate production process changes immediately |
Packaging and labels | Proper drum sealing and labels to avoid contamination |
Logistics infrastructure | Ability to store, handle, and ship sensitive powders |
Given high material cost and critical end-use, due diligence of powder suppliers is vital before approval and long-term contracts.
How to Store Ti6Al4V Powder Safely?
To prevent powder contamination, oxidation, or accidents, titanium alloy powders require careful storage and handling:
Ti6Al4V Powder Storage Guidelines
- Store unopened containers with original protective packaging
- Use sealed steel drums or bottles rather than bags
- Limit storage duration to 6-12 months for unused powder
- Store in a clean, dry location away from moisture
- Maintain temperatures below 25°C
- Avoid exposure to potential airborne contaminants
- Ensure proper grounding before handling powder containers
- Follow all standard safety guidelines for handling fine metallic powders
Adhering to ideal storage conditions ensures Ti6Al4V powder quality and suitable for critical AM applications even after months of storage.
Ti6Al4V Powder Safety
Like other fine metal powders, handling Ti6Al4V powder poses significant dust explosion and fire risks if not done carefully with necessary precautions:
Ti6Al4V Powder Safety Guidelines
- Use spark-resistant tools when handling powder drums
- Ensure adequate ventilation and dust collection
- Provide proper personal protective gear to workers
- Avoid powder spills during unpacking or transfers
- Follow equipotential earthing requirements
- Use approved relief valves on powder containers
- Employ inert gas purging if possible
- No ignition sources within 50 ft of handling
- Separate powder operations from other manufacturing
- Automate powder handling instead of manual processes
- Implement comprehensive fire and explosion measures
In powder-based AM area, safety is paramount. Proactive mitigation steps during Ti6Al4V storage, handling, operation and disposal prevent accidents.
Ti6Al4V Powder Recycling
Given high material costs, recycling Ti6Al4V powder used in AM processes like laser melting or electron beam melting provides significant cost savings – up to 65%. Steps include:
Ti6Al4V Powder Recycling
- Sieve and separate reusable powder from contamination
- Identify recyclable vs waste powder based on sampling
- Analyze recyclable powder for oxygen pickup during build
- Ensure mechanical properties meet specifications
- Blend recyclable powder with virgin Ti6Al4V powder
- Typically 30-50% recycled powder blended ratio is used
- Reuse blended powder for non-critical applications
- Do not use 100% recycled powder for aerospace parts
As recycling makes economic sense, many service bureaus and metal AM adopters are investing in powder recovery systems and reconditioning equipment.
Ti6Al4V Powder Handling Guide
Handling titanium alloy powder needs great care whether for shipping, storage, transferring to AM machines or post-processing:
Ti6Al4V Powder Handling Guide
- Transport in sealed containers with tamper-proof labels
- Store powder in a dedicated, controlled area only
- Protect containers from physical damage
- Personnel must wear nitrile gloves, lab coats, face masks
- Prevent exposure to hydrogen sources like grease
- Use ceramic, plastic or stainless-steel tools only
- Restrict access to avoid theft or contamination
- Account for used powder after each build
- Follow specific disposal guidelines of unused powder
Meticulous tracking, auditing and documentation builds confidence in feedstock quality – especially critical for high-value powders like Ti6Al4V.
Ti6Al4V Powder Finishing
As-fabricated Ti6Al4V parts using AM processes need finishing to achieve desired dimensional accuracy, surface finish and cleanliness. Typical techniques include:
Ti6Al4V Part Post-Processing
- CNC machining of selective laser melted components
- Abrasive flow machining for internal passages
- Tumbling and media finishing
- Glass bead peening
- Electropolishing for surface finish improvement
- Hot isostatic pressing to eliminate internal voids
- Ultrasonic cleaning for removal of excess powder
- Annealing heat treatments to relieve internal stresses
Finishing steps depend on final application requirements – the tighter the tolerances, the more extensive the processing needed on as-built Ti6Al4V hardware.
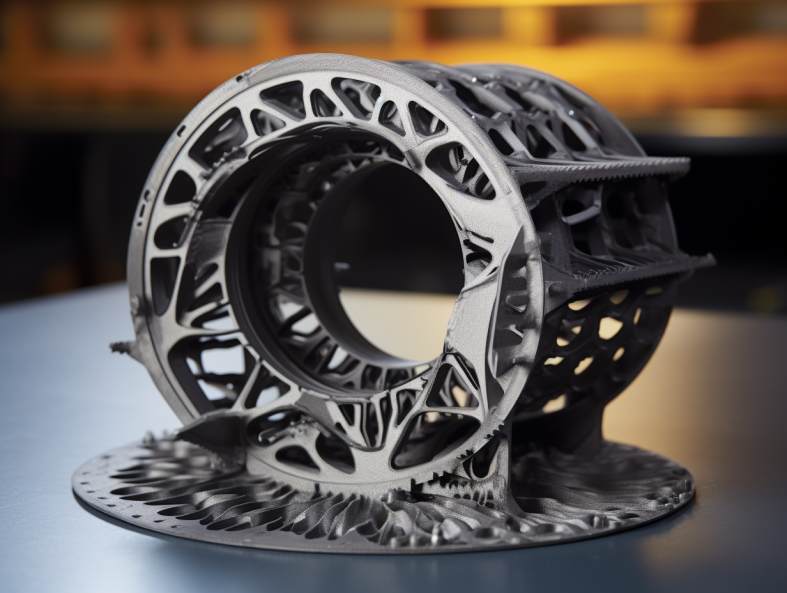
FAQ
Q: Does Ti6Al4V powder require special shipping or MSDS?
A: Ti6Al4V is classified as non-hazardous. However, being a fine metallic powder handling precautions are needed. Proper labels, spill containment kit and PPE should be used.
Q: What particle size is best suited for laser melting?
A: 15-45 microns is recommended. Smaller particles pack better but excess fines can cause challenges during part cake breakout. 45-100 microns is more appropriate for binder jetting or DED.
Q: Can you 3D print pure titanium powder?
A: Technically yes – but commercially pure titanium powder does not offer the well-balanced properties of workhorse alloys like Ti6Al4V in critical applications. CP-Ti is relatively soft with lower temperature capability.
Q: What is the difference between Ti6Al4V ELI vs standard Ti6Al4V?
A: Ti6Al4V ELI or extra low interstitial version has lower limits on oxygen (0.08%) and iron (0.12%) but comes at a 40-50% cost premium over standard Ti6Al4V powder.
Q: What is the easiest way to blend Ti6Al4V virgin and recycled powders?
A. Use a V-blender with intensifier bar. Blend for at least 4 hours with intermittent stops to prevent overheating. Manual blending should be avoided given variability. Automated tumble blending provides the most repeatable homogeneous Ti64 powder mix.
Conclusion
Ti6Al4V has cemented its place as the workhorse titanium alloy for the most demanding applications across aerospace, medical, automotive and energy industries where high-performance under extreme conditions is needed.
With its balanced mechanical properties, corrosion resistance, biocompatibility, relative affordability and advanced manufacturing capabilities, the future looks bright for increased adoption of parts fabricated using Ti6Al4V powder.
Leading metal AM companies bringing parts into mission-critical serial production are actively working with established and emerging Ti6Al4V powder vendors to secure stable long-term powder supply as market demand accelerates.