Introduction
What is metal powder for 3D printing?
Metal powder for 3D printing refers to the finely ground particles of various metals that are used as the raw material in the additive manufacturing process. These powders are specifically designed to have the right particle size, shape, and composition to ensure optimal performance during the 3D printing process. Metal powders for 3D printing are available in a wide range of materials, including stainless steel, titanium, aluminum, and nickel alloys, among others. They are used in various industries, such as aerospace, automotive, and healthcare, to create complex and highly durable metal components with intricate designs that would be difficult or impossible to produce using traditional manufacturing methods. The selection of the right metal powder is crucial in achieving the desired mechanical properties, surface finish, and dimensional accuracy of the final 3D printed part.
Importance of choosing the right metal powder
The importance of choosing the right metal powder for 3D printing cannot be overstated. The quality and properties of the metal powder used directly impact the final product’s strength, durability, and overall performance. Selecting the appropriate metal powder is crucial to achieve the desired characteristics, such as high precision, excellent surface finish, and mechanical integrity. Moreover, the right metal powder ensures compatibility with the specific 3D printing technology and equipment being utilized. By carefully considering factors like particle size distribution, composition, and purity, manufacturers can optimize the printing process and achieve exceptional results. Therefore, thorough research and analysis are essential when it comes to selecting the most suitable metal powder for 3D printing applications.
Overview of the guide
The article titled ‘A Comprehensive Guide to Choosing Metal Powder for 3D Printing’ provides a detailed overview of the various factors to consider when selecting metal powders for 3D printing applications. This guide aims to assist readers in understanding the importance of metal powder selection and its impact on the final printed product. It covers essential topics such as powder properties, particle size distribution, material compatibility, and post-processing requirements. By following this comprehensive guide, readers will gain valuable insights into making informed decisions and achieving optimal results in their 3D printing projects.
Types of Metal Powders
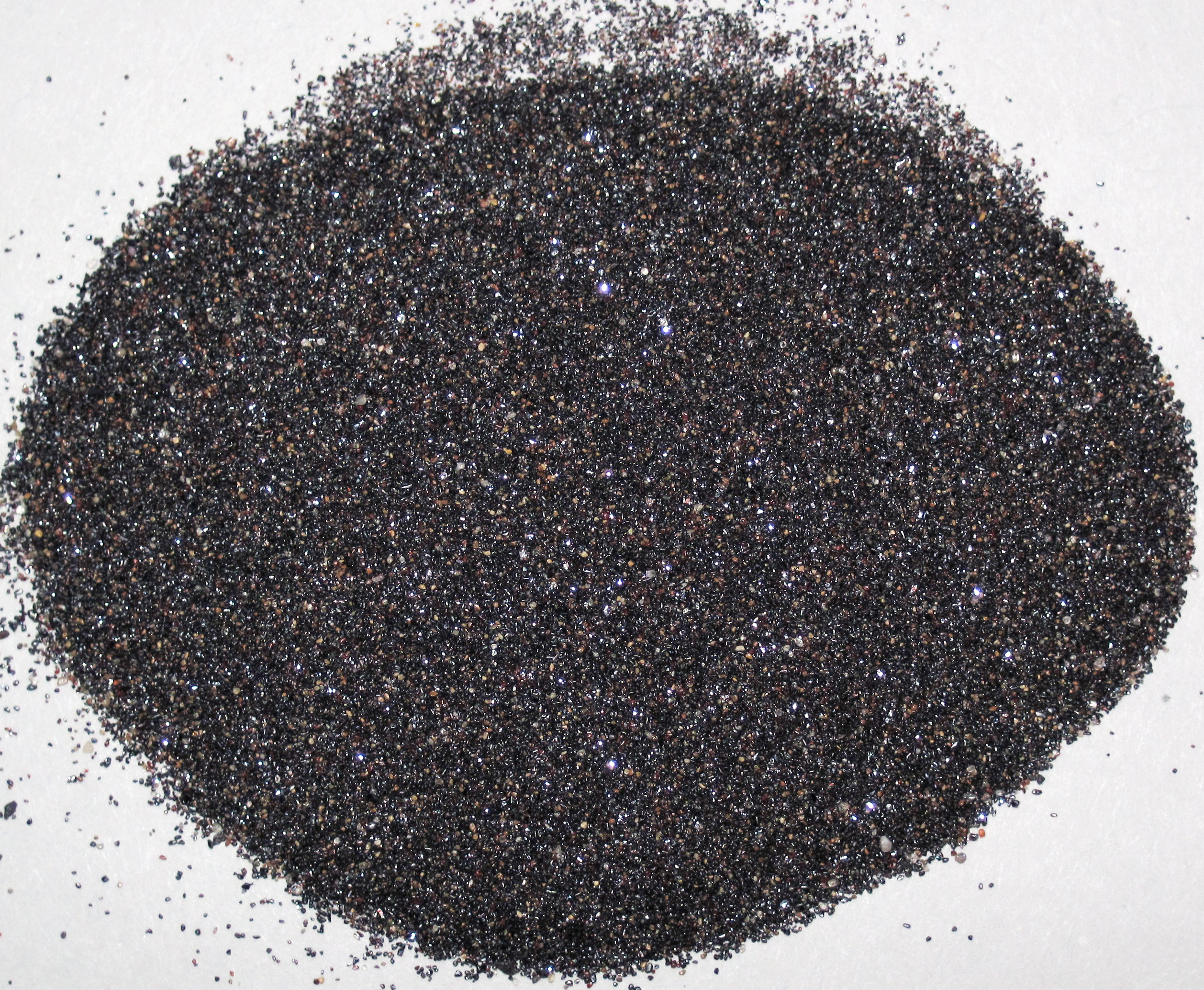
Stainless Steel
Stainless steel is a popular choice of metal powder for 3D printing due to its excellent mechanical properties and corrosion resistance. It is commonly used in various industries, including aerospace, automotive, and medical. The high strength and durability of stainless steel make it suitable for producing complex and intricate parts with precision. Additionally, stainless steel powders are readily available in different grades, allowing for a wide range of applications. Whether it’s for prototyping or end-use parts, stainless steel offers the reliability and performance required for 3D printing projects.
Aluminum
Aluminum is one of the most commonly used metals in 3D printing due to its excellent strength-to-weight ratio and corrosion resistance. It is a versatile material that can be easily shaped and manipulated, making it ideal for creating complex and intricate designs. In addition, aluminum powder is readily available and cost-effective, making it a popular choice for both hobbyists and professional 3D printing enthusiasts. Whether you’re looking to create functional prototypes or artistic sculptures, aluminum powder provides the durability and versatility needed to bring your ideas to life.
Titanium
Titanium is a popular choice of metal powder for 3D printing due to its exceptional strength-to-weight ratio and corrosion resistance. It is widely used in various industries, including aerospace, medical, and automotive. The unique properties of titanium make it ideal for applications that require high-performance components, such as aircraft parts, medical implants, and sports equipment. Additionally, titanium powder can be easily processed using different 3D printing technologies, allowing for the creation of complex and intricate designs. With its excellent mechanical properties and versatility, titanium powder is a top choice for 3D printing enthusiasts and professionals alike.
Properties to Consider
Particle Size
Particle size is a crucial factor to consider when choosing metal powder for 3D printing. The size of the particles can greatly impact the final quality and properties of the printed object. Smaller particle sizes generally result in smoother and more detailed prints, while larger particles may lead to a rougher surface finish. Additionally, the particle size distribution should be carefully controlled to ensure consistent and uniform printing. It is important to select a metal powder with the appropriate particle size range for the desired application and printing process. By understanding the importance of particle size, 3D printing enthusiasts can make informed decisions to achieve optimal results.
Chemical Composition
When it comes to choosing metal powder for 3D printing, one of the key factors to consider is the chemical composition. The chemical composition of the metal powder determines its properties, such as strength, durability, and corrosion resistance. Different metals have different chemical compositions, and each composition offers unique characteristics. For example, titanium powder has a chemical composition that provides excellent strength-to-weight ratio, making it ideal for aerospace applications. On the other hand, stainless steel powder has a composition that offers high corrosion resistance, making it suitable for applications in harsh environments. Understanding the chemical composition of the metal powder is crucial in selecting the right material for 3D printing projects.
Powder Morphology
Powder morphology plays a crucial role in the 3D printing process. The shape, size, and surface characteristics of the metal powder particles can significantly impact the final printed product’s quality and performance. Different powder morphologies, such as spherical, irregular, or dendritic, have their own advantages and disadvantages. Spherical powders, for example, are often preferred due to their uniformity and flowability, which can result in better packing density and improved printability. On the other hand, irregular or dendritic powders may offer enhanced material properties, such as higher strength or improved heat transfer capabilities. Understanding the powder morphology and selecting the appropriate type for specific applications is essential for achieving optimal results in metal 3D printing.
Powder Production Methods

Gas Atomization
Gas atomization is a widely used method in the production of metal powders for 3D printing. This technique involves injecting a high-pressure gas into a molten metal stream, causing it to break up into small droplets. These droplets solidify rapidly, forming fine metal powders with spherical shapes. Gas atomization offers several advantages, including high production rates, excellent powder purity, and control over particle size distribution. Additionally, it allows for the production of a wide range of metal powders, making it a versatile choice for 3D printing applications.
Water Atomization
Water atomization is a widely used method for producing metal powders used in 3D printing. This process involves spraying molten metal into a water-filled chamber, where it rapidly solidifies into fine particles. The water acts as a cooling medium, allowing for controlled solidification and preventing the formation of large grain structures. The resulting metal powders have excellent flowability and can be easily processed into complex shapes using additive manufacturing techniques. Water atomization offers several advantages, including high production rates, uniform particle size distribution, and the ability to produce powders with tailored properties for specific applications. This makes it a preferred choice for many industries that rely on metal powders for 3D printing.
Electrolytic Deposition
Electrolytic deposition is a crucial process in the world of 3D printing with metal powders. It involves the use of an electrolyte solution and an electric current to deposit metal ions onto a substrate, creating a thin layer of metal. This process is widely used in various industries, including aerospace, automotive, and medical, due to its ability to produce high-quality and complex metal parts. By carefully controlling the deposition parameters, such as current density and deposition time, manufacturers can achieve precise and uniform metal deposition, resulting in parts with excellent mechanical properties and dimensional accuracy. Electrolytic deposition offers a cost-effective and efficient method for producing metal components with intricate designs and intricate geometries, making it an essential technique in the field of 3D printing with metal powders.
Quality Control

Powder Purity
Powder purity is a crucial factor to consider when choosing metal powder for 3D printing. The purity of the powder directly affects the quality and integrity of the printed objects. Impurities in the powder can lead to defects, such as porosity or weak mechanical properties, in the final printed parts. Therefore, it is important to select metal powders that have a high level of purity. Manufacturers often provide information about the purity level of their powders, which can help in making an informed decision. Additionally, using powders with high purity can improve the overall printability and reliability of the 3D printing process, resulting in better end products.
Particle Size Distribution
Particle size distribution is an essential factor to consider when choosing metal powder for 3D printing. The particle size directly affects the quality and performance of the printed object. A narrow particle size distribution ensures uniformity in the powder bed, resulting in better layer adhesion and overall print accuracy. Additionally, a consistent particle size distribution allows for more precise control of the printing process, leading to improved part integrity and dimensional accuracy. It is crucial to select metal powders with the desired particle size distribution to achieve optimal print results and meet specific application requirements.
Flowability and Apparent Density
Flowability and apparent density are important factors to consider when choosing metal powder for 3D printing. Flowability refers to the ability of the powder to flow freely and evenly during the printing process. Powders with good flowability are essential for achieving high-quality prints with accurate details and smooth surfaces. On the other hand, apparent density refers to the mass of the powder per unit volume. It is an indicator of the packing efficiency of the powder particles. Powders with high apparent density are preferred as they can provide better packing and reduce the risk of voids or porosity in the printed parts. Therefore, when selecting metal powder for 3D printing, it is crucial to assess the flowability and apparent density to ensure optimal printing results.
Applications and Case Studies
Aerospace Industry
The aerospace industry is one of the key sectors that heavily relies on 3D printing technology. With its ability to produce complex and lightweight components, metal powder for 3D printing has become an essential material in the aerospace industry. From engine parts to structural components, 3D printed metal parts offer improved performance, reduced weight, and increased fuel efficiency. Moreover, the flexibility of 3D printing allows for rapid prototyping and customization, enabling aerospace companies to iterate and optimize their designs quickly. As a result, the use of metal powder for 3D printing has revolutionized the manufacturing processes in the aerospace industry, leading to advancements in aircraft performance and safety.
Medical Industry
The medical industry has greatly benefited from the advancements in 3D printing technology, particularly in the use of metal powder. Metal powders with specific properties are crucial for producing high-quality medical devices and implants. The ability to customize and fabricate complex geometries with precision has revolutionized the field of medical manufacturing. 3D printing using metal powders enables the production of patient-specific implants, such as cranial and orthopedic implants, which can improve patient outcomes and reduce surgical risks. Additionally, the use of biocompatible metal powders ensures that the implants are safe and compatible with the human body. With the continuous development of metal powders for 3D printing, the medical industry is poised to witness further advancements in personalized medicine and innovative healthcare solutions.
Automotive Industry
The automotive industry has been revolutionized by the introduction of 3D printing technology. With its ability to produce complex and lightweight parts, metal powder for 3D printing has become a crucial component in the manufacturing process. Automotive manufacturers are now able to create customized and high-performance components that were previously difficult or expensive to produce using traditional manufacturing methods. This has led to improved efficiency, reduced costs, and enhanced design flexibility. As the demand for more sustainable and fuel-efficient vehicles continues to grow, the use of metal powder for 3D printing in the automotive industry is expected to increase significantly.