Imagine a material that’s incredibly strong, unbelievably light, and versatile enough to be used in everything from sleek smartphones to powerful jet engines. That’s the magic of AlSi10Mg powder, a revolutionary material taking the world of additive manufacturing (3D printing) and beyond by storm. But what exactly is AlSi10Mg powder, and why is it causing such a stir? Buckle up, because we’re diving deep into the world of this metallic marvel.
Introduction of AlSi10Mg Powder
AlSi10Mg powder, also known as Aluminum Silicon Magnesium alloy powder, is a fine-grained metallic dust specifically designed for additive manufacturing processes like Selective Laser Melting (SLM) and Electron Beam Melting (EBM). It’s a concoction of aluminum, the ever-reliable lightweight metal, with a dash of silicon (around 10%) for enhanced strength and a sprinkle of magnesium (around 0.3%) for improved castability. This unique blend gives AlSi10Mg powder a combination of properties that make it a game-changer in the manufacturing industry.
Think of it like this: Picture a chef creating a masterpiece dish. Aluminum is the base ingredient, the foundation of the recipe. Silicon and magnesium are the secret spices, adding a distinct flavor and enhancing the overall experience. Just like the perfect dish, AlSi10Mg powder offers a powerful combination of elements for superior performance.
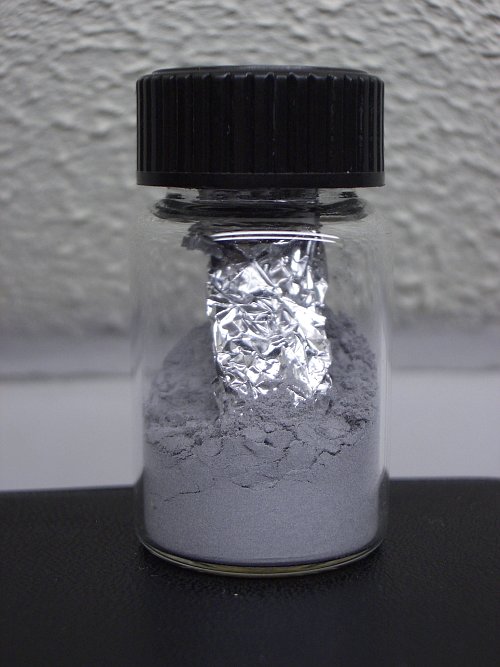
The Advantages of AlSi10Mg Powder
So, what makes AlSi10Mg powder such a hot commodity? Here are some of its key advantages that have manufacturers and engineers singing its praises:
- Lightweight Champion: Compared to traditional materials like steel, AlSi10Mg powder boasts a significantly lower density. This translates to lighter components without compromising strength, making it ideal for applications where weight reduction is crucial, like aerospace and automotive parts. Imagine airplanes shedding pounds, leading to increased fuel efficiency and longer flight ranges. That’s the power of AlSi10Mg powder in action!
- Strength in Numbers: Don’t be fooled by its featherweight nature. AlSi10Mg powder packs a punch when it comes to strength. The addition of silicon significantly enhances its mechanical properties compared to pure aluminum. This allows for the creation of robust, high-performance parts that can withstand demanding applications.
- Designed for Precision: AlSi10Mg powder boasts exceptional flowability, meaning the tiny particles move smoothly during the 3D printing process. This translates to highly accurate and intricate part production, ideal for complex geometries and designs that would be challenging with traditional manufacturing methods.
- The Heat is On (But Not in a Bad Way): AlSi10Mg powder demonstrates good thermal conductivity. This means it transfers heat efficiently, which can be beneficial in applications like heat sinks and engine components. Think of it as a tiny conductor, carrying heat away from critical areas and preventing overheating.
- Versatility is Key: AlSi1 Mg powder isn’t a one-trick pony. It’s compatible with various 3D printing techniques, offering manufacturers flexibility in their production processes. Additionally, post-processing techniques like heat treatment can further enhance the mechanical properties of AlSi10Mg parts, making them even more versatile for different applications.
Applications of AlSi10Mg Powder
With its impressive list of advantages, AlSi10Mg powder is finding its way into a vast array of industries. Here are some of the most exciting applications:
- Aerospace: The relentless pursuit of lightweight and high-strength materials makes AlSi10Mg powder a perfect fit for the aerospace industry. Components like aircraft brackets, housings, and even structural elements can be created using this powder, leading to lighter airplanes with improved fuel efficiency and payload capacity.
- Automotive: The automotive industry is constantly striving to reduce vehicle weight and improve fuel economy. AlSi10Mg powder is making waves here too. Components like wheels, engine parts, and even structural elements can be manufactured using this powder, leading to lighter, more fuel-efficient cars.
- Medical Devices: The medical field is also starting to embrace AlSi10Mg powder. Customized prosthetics and implants with intricate designs can be 3D printed using this powder, offering patients lightweight and biocompatible solutions.
- Consumer Electronics: From sleek smartphone cases to lightweight laptop components, AlSi10Mg powder is finding its way into consumer electronics. Its ability to create complex shapes and reduce weight makes it ideal for designing innovative and portable devices.
These are just a few examples, and as 3D printing technology continues to evolve, we can expect to see AlSi10Mg powder utilized in even more groundbreaking applications.
Technical Specifications of AlSi10Mg Powder
While we’ve explored the allure of AlSi10Mg powder, understanding its technical specifications is crucial for making informed decisions in various applications. Here, we’ll dissect some key aspects:
Chemical Composition: As the name suggests, AlSi10Mg powder is primarily composed of aluminum (Al), with a specific silicon (Si) content of around 10% and a magnesium (Mg) content of approximately 0.3%. This specific blend optimizes the balance between strength, castability, and weldability.
Physical Properties:
- Density: Around 2.65 – 2.7 g/cm³, significantly lower than steel (around 7.8 g/cm³). This translates to substantial weight reduction in components.
- Melting Point: Approximately 570°C (1058°F). This allows for processing using various 3D printing techniques.
- Thermal Conductivity: Around 100 W/m·K. This ensures efficient heat transfer, making it suitable for thermal management applications.
Mechanical Properties:
- Tensile Strength: Depending on the manufacturing process and post-processing techniques, the tensile strength of AlSi10Mg parts can range from 270 MPa to 450 MPa. This offers a good balance between strength and weight.
- Yield Strength: Similar to tensile strength, the yield strength can vary between 180 MPa and 350 MPa. This indicates the material’s ability to resist deformation under stress.
- Elongation at Break: This value represents the material’s ductility or its ability to stretch before breaking. AlSi10Mg powder typically exhibits an elongation at break of around 3-8%, which is moderate compared to other materials.
It’s important to note: These are general properties, and the specific values can vary depending on the manufacturing process, powder particle size distribution, and post-processing techniques employed.
Advantages and Limitations of AlSi10Mg Powder
We’ve sung the praises of AlSi10Mg powder, but like any material, it has its limitations. Here’s a balanced perspective to consider:
Advantages Recap:
- Lightweight Champion: Superior weight reduction compared to traditional materials.
- Strength in Numbers: Offers good mechanical properties for demanding applications.
- Designed for Precision: Enables creation of intricate and complex geometries.
- The Heat is On (But Not in a Bad Way): Good thermal conductivity for heat management.
- Versatility is Key: Compatible with various 3D printing techniques and allows for post-processing enhancements.
Limitations to Consider:
- Brittle Behavior: Compared to some materials, AlSi10Mg powder can exhibit a more brittle nature, meaning it may crack under sudden impact. This can be mitigated through proper design considerations and potentially exploring alternative Al-Si-Mg alloy variants with higher ductility.
- Surface Roughness: 3D printed parts using AlSi10Mg powder may have a slightly rougher surface finish compared to traditionally machined components. Post-processing techniques like polishing can address this concern.
- Cost Considerations: While the potential benefits are significant, AlSi10Mg powder itself and 3D printing processes can be more expensive compared to some conventional manufacturing methods. However, as technology advances and adoption increases, costs are expected to decrease.
Understanding these limitations helps in making informed decisions about whether AlSi10Mg powder is the right choice for a specific application.
The Road Ahead for AlSi10Mg Powder
The future of AlSi10Mg powder is brimming with promise. Here are some exciting trends to keep an eye on:
- Advanced Alloys: Researchers are constantly developing new Al-Si-Mg alloy variants with improved properties like higher ductility or enhanced corrosion resistance. This will broaden the applicability of AlSi10Mg powder for even more demanding applications.
- Powder Optimization: Developments in powder production techniques are leading to tighter control over particle size distribution and morphology. This can lead to even better flowability, improved surface finish, and potentially enhanced mechanical properties of 3D printed parts.
- Hybrid Manufacturing: The integration of 3D printing with traditional manufacturing techniques is gaining traction. AlSi10Mg powder can be used to create lightweight and complex components that can be seamlessly integrated with traditionally manufactured parts, opening doors for innovative product design.
As 3D printing technology matures and AlSi10Mg powder continues to evolve, we can expect to see this revolutionary material play a pivotal role in shaping the future of various industries.
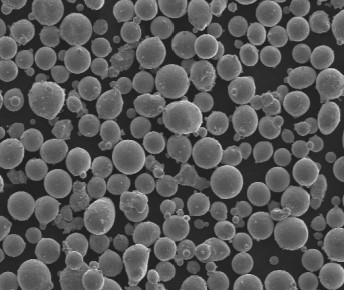
FAQ
Here are some of the most commonly asked questions regarding AlSi10Mg powder:
Q: What are the different types of AlSi10Mg powder available?
A: There aren’t necessarily distinct “types” of AlSi10Mg powder, but there can be variations in its properties depending on the manufacturer and processing techniques. Key factors to consider include:
- Particle size distribution: The size and distribution of the powder particles can impact flowability, printability, and the surface finish of the final part. Powders with a tighter size distribution tend to offer better results.
- Spherical versus irregular particle shapes: Spherical particles generally flow more smoothly and can lead to better packing density during printing, potentially improving mechanical properties.
- Alloying additions: Some manufacturers might offer AlSi10Mg powder with minor variations in silicon or magnesium content, or even the addition of other elements like copper for specific applications.
It’s advisable to consult with the powder supplier and discuss your specific application requirements to determine the most suitable AlSi10Mg powder for your needs.
Q: How does AlSi10Mg powder compare to other metal powders used in 3D printing?
A: Here’s a brief comparison of AlSi10Mg powder with some commonly used alternatives:
Material | Advantages | Limitations |
---|---|---|
AlSi10Mg Powder | Lightweight, good strength, versatile | Brittle compared to some materials, surface roughness |
Stainless Steel Powders | Excellent corrosion resistance, high strength | Heavier, may require higher processing temperatures |
Titanium Powders | High strength-to-weight ratio, biocompatible | Expensive, challenging to process |
Nickel Alloys | High-temperature performance, good corrosion resistance | Expensive, may require specialized printing environments |
Q: Can AlSi10Mg powder be recycled?
A: Yes, AlSi10Mg powder can be recycled to a certain extent. Unused powder can often be reused in the 3D printing process, minimizing waste. Additionally, some facilities offer recycling programs for scrap parts made from AlSi10Mg powder. However, the recycling process might introduce some limitations on the mechanical properties of the recycled powder compared to virgin material.
Q: What are the post-processing options for AlSi10Mg parts?
A: Several post-processing techniques can enhance the properties and aesthetics of AlSi10Mg parts:
- Heat treatment: Processes like annealing or T6 tempering can improve the strength and ductility of the parts.
- Support removal: Depending on the 3D printing method used, support structures might need to be removed carefully.
- Shot peening: This technique introduces compressive stress on the surface, improving fatigue strength and reducing crack initiation.
- Machining: AlSi10Mg parts can be machined for tighter tolerances or to achieve specific surface finishes.
- Polishing: This can improve the surface smoothness of the parts for aesthetic or functional purposes.
The choice of post-processing techniques depends on the desired outcome and the specific application.
Q: Where can I buy AlSi10Mg powder?
A: Several reputable metal powder suppliers offer AlSi10Mg powder. It’s recommended to research different suppliers, compare pricing, and inquire about the specific properties and certifications of the powder they offer.