Aluminides represent a class of intermetallic materials composed of aluminum plus one or more alloying elements. This guide serves as a reference on aluminides in powder format – overviewing types, manufacturing methods, key traits and parameters, suppliers and pricing, diverse end-use applications across industries, FAQs and more.
Overview of Aluminides Powder
aluminides powder comprises specialty aluminum-rich alloys containing a secondary metallic element such as nickel, iron, titanium, etc. Key attributes:
- Composition: Aluminum + alloying metal
- Production: Gas atomization into powder
- Form: Spherical particulate powder
- Grain sizes: From microns to millimeters
- Key traits: Heat and corrosion resistant
The combination of aluminum with compatible metals produces unique crystalline structures and enhanced properties over conventional alloys – lending versatility in high performance applications.
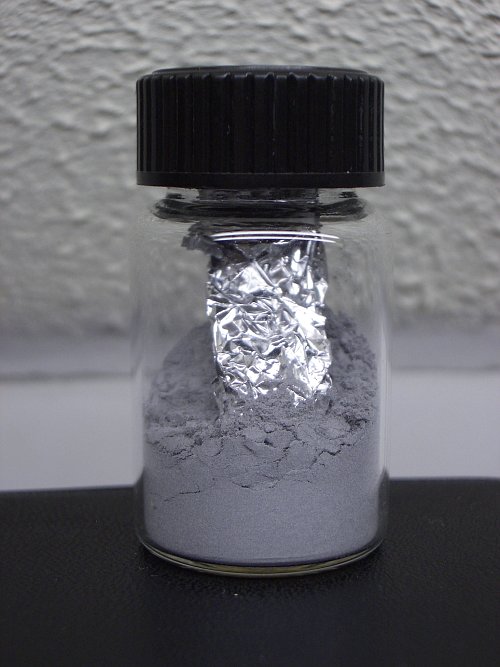
Types of Aluminides Powder
By incorporating different alloying metals, aluminides take on specific names and characteristics:
Alloy Type | Composition | Traits |
---|---|---|
Nickel Aluminide | Al3Ni, Al3Ni2 etc. | High strength Oxidation resistant |
Iron Aluminide | FeAl, Fe3Al etc | Good ductility Heat/corrosion proof |
Titanium Aluminide | TiAl, Ti3Al etc. | Lightweight Strong at high temps |
Chromium Aluminide | CrAl7, Cr2Al5 | Hot hardness Good wear performance |
Table 1: Common aluminide powder variants by metallic constituents
Al-Ni, Al-Fe and Al-Ti systems demonstrate utility in aerospace, automotive and energy applications leveraging tailored physical and mechanical properties.
Production Methods
Commercial manufacturing processes to create aluminide powder include:
- Gas Atomization – molten stream impinged by inert gas jets, produces spherical powders ideal for AM
- Plasma Rotating Electrode Process (PREP) – centrifugal disintegration of electrified molten material
- Inert Gas Condensation – vaporized alloy condensed into nanoparticles
- Mechanical Alloying – ball milling and repeated welding of metal powder mixes
Through tuning of processing conditions like thermal profiles, inert gas flows, rotational speeds and milling parameters, aluminide powder morphologies, grain structures, sizes and resulting capabilities can be dialed as per application requirements.
Aluminides Powder Properties
Physical Properties
Attribute | Characteristics |
---|---|
Melting Point | 500-1000°C depending on alloy |
Density | 2.5-4 g/cm3 |
Color | Grey metallic |
Magnetism | Paramagnetic |
Mechanical Properties
Measure | Value |
---|---|
Hardness | 200-500 HV typical |
Strength | 400-900 MPa |
Ductility | 10-25% elongation |
Thermal Properties
Metric | Rating |
---|---|
Thermal Conductivity | 50-180 W/mK |
Coefficient of Thermal Expansion | 12-25 x10-6 K-1 |
Max Service Temperature | 750-1050°C |
Table 2: Key physical, mechanical and thermal properties of aluminide powders
These attributes enable robust production, forming and performance in high heat, stress and wear environments.
Specifications
Commercial aluminides powders meet standard specifications:
Size Distribution
Standard | Microns | Common Production Method |
---|---|---|
Fine | 0-20 | Gas atomization |
Medium | 20-63 | Gas atomization |
Coarse | 63-105 | PREP, Mechanical alloying |
Purity Grades
Rating | Impurities | Usage |
---|---|---|
Standard | Up to 1% other | Testing, sampling |
High | <1000 ppm impurities | Industrial production |
Ultra high | <100 ppm contaminants | Aviation, medical |
Table 3: Typical size ranges and purity grades for aluminides powders
More stringent screening on particle size distributions and impurity levels supports precision performance but increases production costs.
Aluminides Powder Manufacturers
Specialized producers offer commercial scale volumes across grades:
Company | Brand Names | Price Range |
---|---|---|
Sandvik | Osprey® Al-alloys | $50-120/kg |
Praxair | Atomized Aluminides | $40-200/kg |
Carpenter Tech | CarTech Aluminal | $80-250/kg |
Fine Metals Corporation | FinessAl | $60-180/kg |
Special Metals Company | PrealloyTM | $75-160/kg |
Table 4: Leading commercial suppliers of aluminides powders
Pricing varies based on order quantity, powder morphology, screen testing/analysis services and alloy customization. Get quotes directly for precise costs. Some companies offer small samples for test and evaluation purposes.
Applications of Aluminides Powder
Industry | Uses | Benefits |
---|---|---|
Aerospace | Turbine blades Thermal management | High strength Lightweight Heat resistance |
Automotive | Pistons Engine parts Exhaust components | Wear resistance Dimensional capability |
Energy | Solid oxide fuel cells Solar receivers Heat exchangers | Extreme temperature handling Corrosion resistance |
Chemical | Equipment linings pipes reactors | Inert material of construction Improved safety |
Table 5: Major use case sectors and drivers for adoption of aluminides powders
Leveraging properties like high melting points, strength-to-weight ratios and corrosion endurance supports reliability in demanding environments. Formability into complex parts via AM facilitates usage.
Comparative Pros and Cons
Advantages of Aluminides
- Withstand higher service temperatures than steel alloys
- Better oxidation and corrosion resistance over conventional alloys
- Lower density versus comparably strong alloys
- Often less expensive than similar performing superalloys
- Processability into net shape parts using AM techniques
Limitations
- Inferior room temperature ductility and fracture toughness
- Require protective coatings in certain chemical environments
- Complex modeling needed for reliable AM part production
- Require hot isostatic pressing (HIP) for full density AM parts
Table 6: Key benefits and downsides to consider regarding aluminides adoption
While possessing some fabrication and service challenges, aluminides’ marked performance at high heat and against oxidation creates promising potential across industries. Further R&D targets improved ductility and fracture resistance.
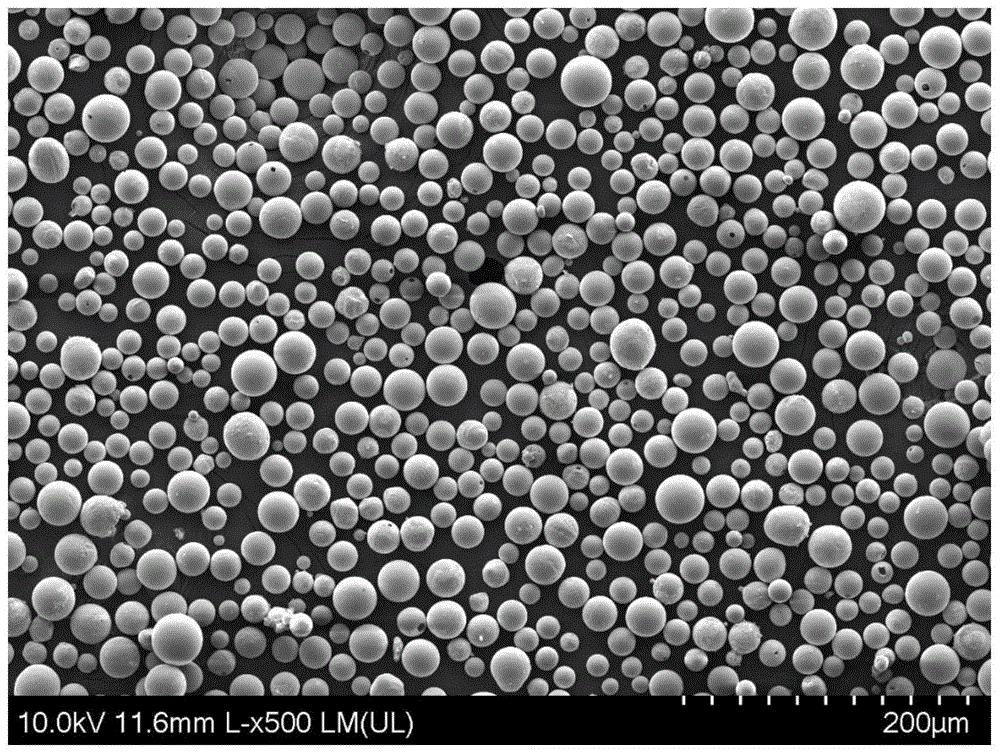
Aluminides Powder FAQs
Q: Do aluminides occur naturally?
A: No, aluminides do not form naturally. They are manufactured using advanced melting, powder production and alloying techniques.
Q: What is the difference between an aluminide and an aluminum alloy?
A: Aluminum alloys only contain aluminum as the key element while aluminides are a class of complex alloys containing aluminum plus one or more additional metallic element.
Q: What are common aluminide alloying elements beyond nickel, iron and titanium?
A: Other transition metals see usage including chromium, zirconium, hafnium, niobium, tantalum, molybdenum and tungsten. Specific combinations tune desired behavior.
Q: What industries adopt aluminide powders versus bulk aluminide materials?
A: Powder morphologies suit additive manufacturing of complex parts across aerospace, automotive and energy fields. Bulk forms are utilized for ingots, coatings and cast tooling applications.