Aluminum based alloy powders have become a game-changer in the world of manufacturing. Imagine taking the incredible strength-to-weight ratio and versatility of aluminum and transforming it into a format that allows for intricate 3D printing and innovative metal additive manufacturing. That’s the magic of aluminum based alloy powders!
But delve deeper, and you’ll discover a universe of possibilities. Different alloying elements, particle sizes, and manufacturing techniques all play a part in creating a diverse range of aluminum based alloy powders, each with its own unique set of properties and applications.
This comprehensive guide will equip you with everything you need to know about aluminum based alloy powders. We’ll explore the different types, delve into their characteristics, understand their uses, and even answer some frequently asked questions. So, buckle up and get ready to dive into the fascinating world of these metallic marvels!
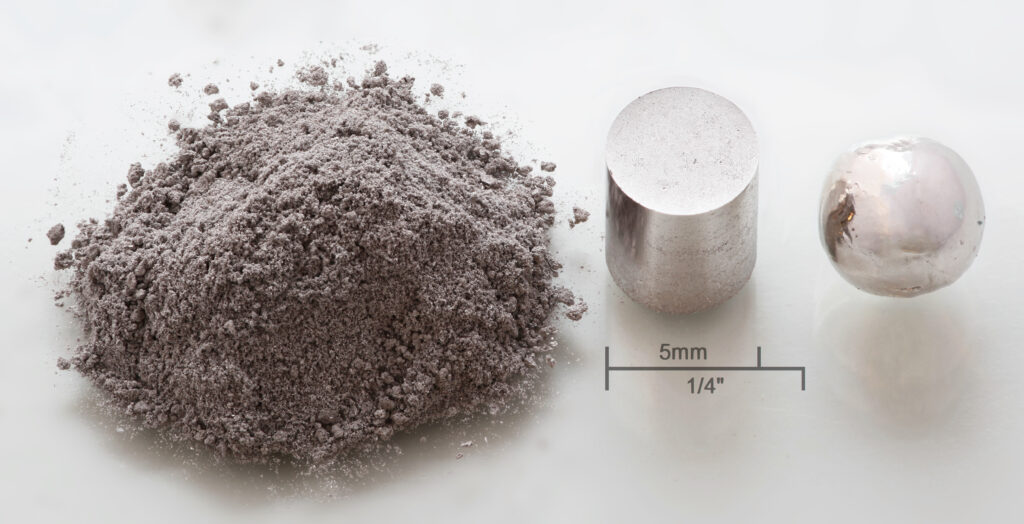
Types of Aluminum Based Alloy Powders
Aluminum based alloy powders are not created equal. By combining aluminum with various elements like silicon, magnesium, copper, and manganese, manufacturers create a spectrum of powders with specific properties. Here’s a breakdown to help you understand:
Type of Aluminum Based Alloy Powder | Composition | Key Properties | Characteristics |
---|---|---|---|
AlSi10Mg (LM6) | Aluminum (Al) with 9-13% Silicon (Si), 0.3-0.6% Magnesium (Mg) | Excellent castability, good weldability, high strength-to-weight ratio | Widely used in 3D printing for components requiring a balance of strength and weight reduction. Offers good machinability. |
AlSi7Mg0.3 (A356) | Aluminum (Al) with 7-9% Silicon (Si), 0.3% Magnesium (Mg) | Excellent castability, good corrosion resistance | A popular choice for applications requiring good castability and resistance to environmental factors. Offers moderate strength. |
AlSiMgMn (AA6061) | Aluminum (Al) with 0.5-1.0% Silicon (Si), 0.2-0.6% Magnesium (Mg), 0.15-0.4% Manganese (Mn) | High strength, good corrosion resistance, excellent machinability | A versatile powder used in aerospace, automotive, and other industries due to its good all-around properties. Offers superior machinability compared to other options. |
AlCu4Mg1 (2024) | Aluminum (Al) with 3.8-4.9% Copper (Cu), 1.5-2.0% Magnesium (Mg) | High strength, excellent fatigue resistance | An ideal choice for components requiring high strength and resistance to repeated stress. Offers good machinability but lower corrosion resistance compared to some options. |
AlZnMg1 (7075) | Aluminum (Al) with 5.1-6.1% Zinc (Zn), 2.1-2.9% Magnesium (Mg) | Very high strength, excellent wear resistance | The go-to powder for applications demanding exceptional strength and durability. Offers good machinability but comes with the trade-off of lower corrosion resistance. |
Aluminum-Nickel Catalyst Raney-Type Alloy | Aluminum (Al) and Nickel (Ni) in a 50/50 ratio | High surface area, excellent hydrogenation catalyst | Primarily used in chemical processing applications due to its ability to facilitate hydrogenation reactions. Not commonly used for structural purposes. |
Aluminum Bronze Powder | Aluminum (Al) with varying percentages of Copper (Cu) and other elements like Tin (Sn) and Iron (Fe) | Excellent corrosion resistance, good wear resistance | An interesting option for applications requiring resistance to wear and tear in harsh environments. Offers limited strength compared to pure aluminum based alloy powders. |
Spherical Aluminum Powder | Pure Aluminum (Al) | High packing density, excellent flowability | These powders boast near-perfect spherical shapes, leading to superior flow characteristics and improved printability in 3D printing applications. May not offer the same level of strength as alloyed powders. |
Pigment Grade Aluminum Powder | Pure Aluminum (Al) in fine flakes | Decorative and conductive properties | Primarily used for aesthetic purposes due to its shimmering appearance. Also finds use in applications requiring electrical conductivity. Offers limited structural strength. |
Nano Aluminum Powder | Ultra-fine Aluminum (Al) particles | High surface area, potential for unique properties | These cutting-edge powders consist of aluminum particles on the nanoscale, opening doors for innovative applications and potentially novel material properties. Research on their |
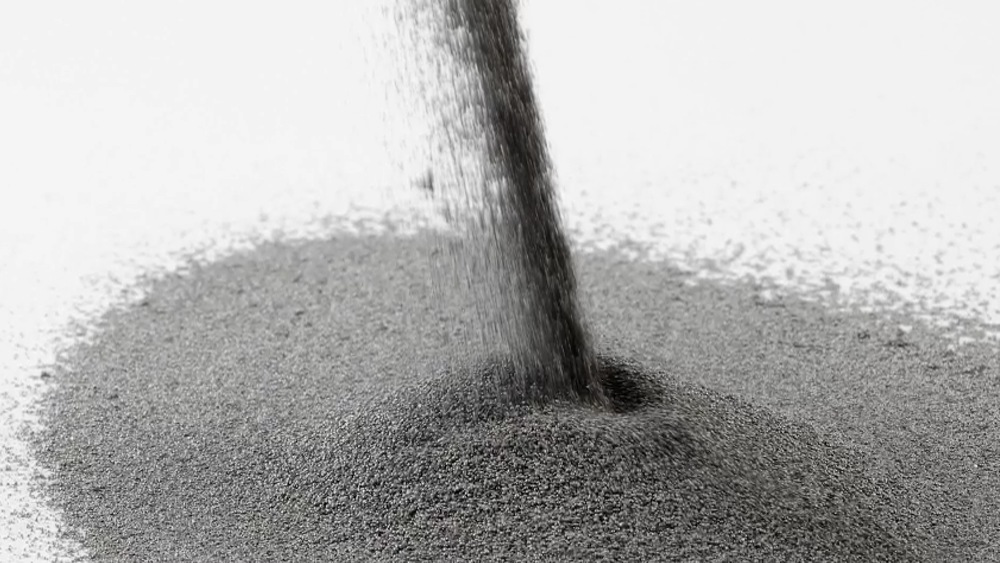
Common Grades of Aluminum Based Alloy Powders
We’ve seen how the composition of aluminum based alloy powders influences their properties. But within each type, there can be further variations depending on the specific grade. Here’s a closer look at some commonly encountered grades:
- AlSi10Mg (LM6): This grade strikes a good balance between strength and weight reduction. It’s popular for 3D printing components in automotive and aerospace applications where both factors are crucial. Grades like LM6 can further be sub-categorized based on factors like magnesium content (LM6 with higher magnesium offers improved weldability).
- AlSi7Mg0.3 (A356): This widely used grade excels in castability, making it ideal for applications requiring intricate shapes or complex geometries. Its moderate strength makes it suitable for components that don’t require the absolute strongest materials. A sub-category, A357, boasts slightly higher silicon content for even better castability.
- AlSiMgMn (AA6061): This versatile grade offers a good combination of strength, corrosion resistance, and machinability. It’s a popular choice across various industries, from aerospace and automotive to consumer electronics. Sub-categories like AA6063 offer improved strength through the addition of copper.
- AlCu4Mg1 (2024): Renowned for its high strength and excellent fatigue resistance, this grade is often used in components subjected to repeated stress, such as aircraft parts and high-performance automotive components. Sub-categories exist with slight variations in copper content for fine-tuning properties.
- AlZnMg1 (7075): The heavyweight champion of aluminum based alloy powders in terms of strength, 7075 finds application in demanding environments where exceptional durability is paramount. Think aircraft wing components, high-performance sporting goods, and military hardware. Sub-categories like 7050 offer a balance between strength and corrosion resistance.
Remember: When choosing an aluminum based alloy powder, consider the specific needs of your application. Do you prioritize strength, castability, corrosion resistance, or a combination of factors? Understanding the properties of different grades and consulting with material suppliers will help you make the optimal selection.
Characteristics of Aluminum Based Alloy Powder
Beyond the properties defined by their composition, aluminum based alloy powders possess some unique characteristics that set them apart from traditional manufacturing materials:
- High Flowability: Due to their small particle size and often spherical shape, aluminum based alloy powders boast excellent flowability. This characteristic makes them ideal for additive manufacturing processes like 3D printing, where precise powder deposition is crucial. Imagine tiny metal marbles smoothly flowing through a printer nozzle, building layer upon layer to create your desired object.
- Near-Net-Shape Manufacturing: Unlike traditional subtractive manufacturing techniques that involve removing material to create a desired shape, 3D printing with aluminum based alloy powders allows for near-net-shape manufacturing. This translates to less material waste and potentially more complex geometries compared to conventional methods.
- Lightweighting Potential: One of the biggest advantages of aluminum itself is its excellent strength-to-weight ratio. This advantage translates directly to aluminum based alloy powders, making them ideal for applications where weight reduction is a prime concern. Imagine an airplane wing component crafted from a high-strength aluminum powder – it can be incredibly strong yet significantly lighter than a traditional counterpart, leading to improved fuel efficiency and overall performance.
- Design Flexibility: 3D printing with aluminum based alloy powders unlocks a new level of design freedom. Complex internal features, intricate lattice structures, and even hollow components become achievable. This opens doors for innovative designs that were previously impossible or impractical with traditional manufacturing methods.
- Potential for Customization: The ability to tailor the composition of aluminum based alloy powders allows for some degree of customization. By adjusting the proportions of alloying elements, manufacturers can create powders with properties optimized for specific applications. Imagine a scenario where a component needs to be not only strong but also highly corrosion resistant – a customized aluminum based alloy powder with the right balance of elements could be the answer.
Method for Designating Grades of Aluminum Based Alloy Powders
There are two main international systems for designating grades of aluminum based alloy powders:
- American Aluminum Association (AA) Designation System: This system uses a four-digit code, where the first digit indicates the major alloying element (e.g., 1 for copper, 3 for silicon, 7 for zinc). The subsequent digits further specify the composition within that category. For instance, AA6061 powder signifies an aluminum-magnesium-silicon alloy.
- International Organization for Standardization (ISO) Designation System: This system employs a more complex alphanumeric code that incorporates information about the chemical composition, temper (heat treatment condition), and product form (e.g., powder).
Applications of Aluminum Based Alloy Powders
The versatility of aluminum based alloy powders shines through their diverse range of applications. Here are some prominent examples:
- Aerospace: The relentless pursuit of lightweight, high-strength materials makes aluminum based alloy powders a natural fit for the aerospace industry. From aircraft wing components and fuselage parts to engine mounts and brackets, these powders are used to create components that optimize performance and fuel efficiency.
- Automotive: Similar to aerospace, the automotive industry leverages aluminum based alloy powders to reduce vehicle weight and improve fuel economy. Think pistons, cylinder heads, and even intricate components within electric vehicle drive trains. Additionally, these powders are being explored for lightweight wheels and structural components.
- Consumer Electronics: The world of gadgets and gizmos is embracing aluminum based alloy powders for their ability to create complex geometries and intricate heat sinks. Imagine a sleek laptop chassis with improved thermal management or a lightweight camera body with internal structures that would be impossible to achieve through traditional manufacturing.
- Medical Implants: The biocompatible nature of certain aluminum alloys, coupled with the design flexibility of 3D printing, makes aluminum based alloy powders a promising option for some medical implants. Customized prosthetics, intricate bone repair cages, and even lightweight surgical instruments are potential applications in this field.
- Defense and Military: Aluminum based alloy powders are being explored for applications requiring a combination of strength, weight reduction, and ballistic resistance. Components for military vehicles, firearms, and even aerospace defense systems could potentially benefit from the unique properties of these powders.
- Prototyping and Low-Volume Production: The ability to create complex objects directly from a digital model makes aluminum based alloy powders ideal for rapid prototyping. This allows engineers and designers to iterate on designs quickly and efficiently. Additionally, for low-volume production runs of specialized parts, 3D printing with aluminum based alloy powders can be a cost-effective and time-saving solution.
Beyond these established applications, the potential uses of aluminum based alloy powders continue to expand. As research and development efforts progress, we can expect to see these versatile materials play an even greater role in various industries in the future.
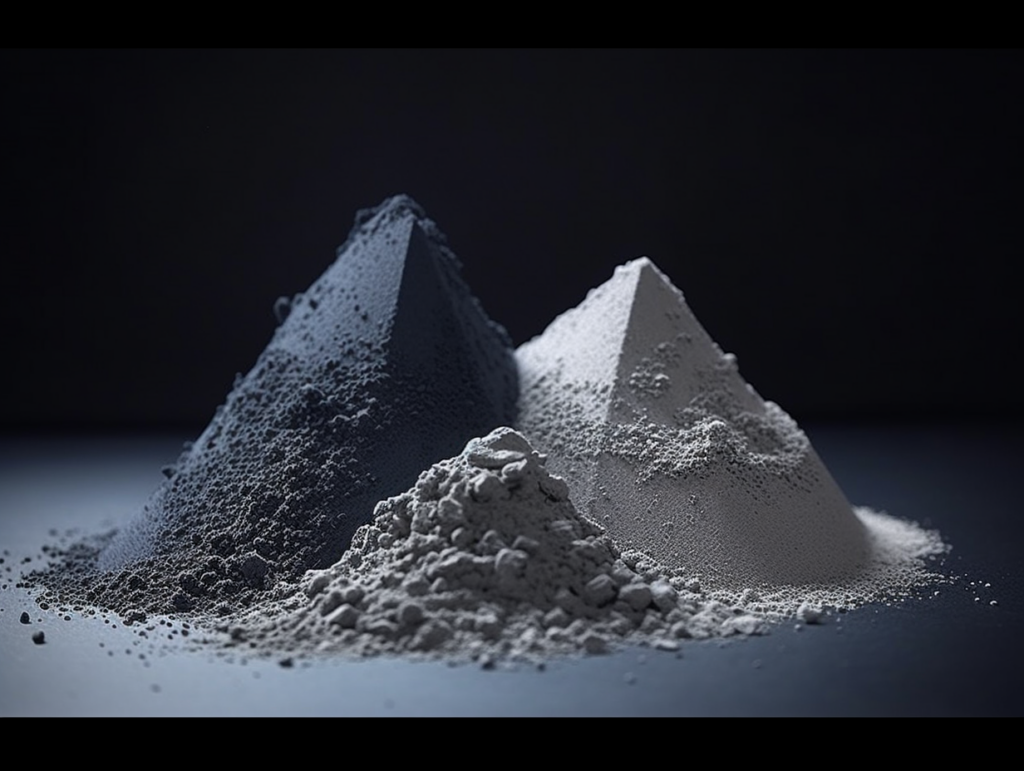
Specifications, Sizes, Grades, and Standards for Aluminum Based Alloy Powder
When selecting aluminum based alloy powder for your project, several factors come into play. Here’s a breakdown of some key specifications to consider:
- Particle Size and Distribution: Particle size significantly impacts the flowability, printability, and surface finish of the final product. Powders with a narrow particle size distribution (all particles are similar in size) tend to flow more smoothly and offer a finer surface finish. However, powders with a wider distribution can sometimes improve packing density.
- Powder Shape: Spherical powders generally offer superior flowability and packing density compared to irregularly shaped particles. This translates to better printability and potentially improved mechanical properties in the final product.
- Grades: As discussed earlier, the specific grade of aluminum based alloy powder determines its properties. Choosing the right grade depends on the application’s requirements for strength, castability, corrosion resistance, and other factors.
- Standards: Several international standards govern the specifications and testing methods for aluminum based alloy powders. Common standards include ASTM International (ASTM) and the International Organization for Standardization (ISO) standards. These standards ensure consistency and quality in the manufacturing and performance of the powders.
Here’s a table summarizing the typical specifications for some common aluminum based alloy powders:
Specification | Description | Example Values |
---|---|---|
Particle Size | Diameter of individual powder particles | 15-100 microns |
Particle Size Distribution | Variation in particle size within the powder | Narrow (<10 microns) or Wider (>20 microns) |
Powder Shape | Geometric form of the particles | Spherical, Irregular |
Grade | Specific composition of the alloy | AlSi10Mg (LM6), AlSi7Mg0.3 (A356), AlSiMgMn (AA6061) |
Standards | Regulatory guidelines for powder characteristics | ASTM B29, ISO 2076 |
Suppliers and Pricing of Aluminum Based Alloy Powders
The growing demand for aluminum based alloy powders has fostered a dynamic supplier landscape. Here’s a glimpse into the world of these vendors and how pricing typically works:
Types of Suppliers:
- Metal Powder Manufacturers: These companies specialize in the production of metal powders, including aluminum based alloy powders. They offer a wide range of options in terms of grades, particle sizes, and shapes.
- Alloy Manufacturers: Some companies that produce aluminum alloys may also offer them in powder form. This can be a good option if you require a specific, customized alloy composition.
- Metal Powder Distributors: These distributors act as intermediaries, sourcing aluminum based alloy powders from various manufacturers and supplying them to end-users. They can be a valuable resource for smaller companies that may not require large quantities of powder.
Pricing Considerations:
- Material Cost: The cost of the raw aluminum and alloying elements plays a significant role in the final price of the powder. Powders with higher concentrations of expensive elements like copper will typically command a premium.
- Manufacturing Process: The specific method used to produce the powder (e.g., atomization, gas atomization) can influence the cost. Generally, powders produced through more complex processes tend to be more expensive.
- Particle Size and Distribution: Powders with tighter particle size distribution and smaller particle sizes often carry a higher price tag due to the additional processing involved in achieving these characteristics.
- Volume: As with many materials, bulk purchases of aluminum based alloy powders typically benefit from economies of scale, leading to lower per-unit costs.
- Supplier Margins: Different suppliers will have varying pricing structures based on their overhead costs and profit margins. Comparing quotes from multiple vendors is essential to ensure you get the best value for your money.
Here’s a table showcasing some examples of aluminum based alloy powder suppliers, along with a general price range (be aware that these are estimates and can vary depending on factors mentioned earlier):
Supplier | Type | Example Powders | Price Range (per kg) |
---|---|---|---|
AMPA Metallpulver GmbH | Metal Powder Manufacturer | AlSi10Mg, AlSi7Mg0.3, AA6061 | €30 – €70 |
APEX Powder Company | Metal Powder Manufacturer | AlSi10Mg, AlCu4Mg1, AlZnMg1 | US$40 – US$80 |
SLM Solutions | Metal Additive Manufacturing Company | AlSi10Mg, AA6061 | Price upon request (often bundled with 3D printing machines) |
Metal Suppliers Online | Metal Powder Distributor | AlSi10Mg, Various Specialty Alloys | US$50 – US$150+ |
Remember: When sourcing aluminum based alloy powders, prioritize reputable suppliers who can provide detailed information about the material’s specifications, certifications, and safety data sheets (SDS). Building a good relationship with a reliable supplier can ensure consistent quality and timely delivery for your projects.
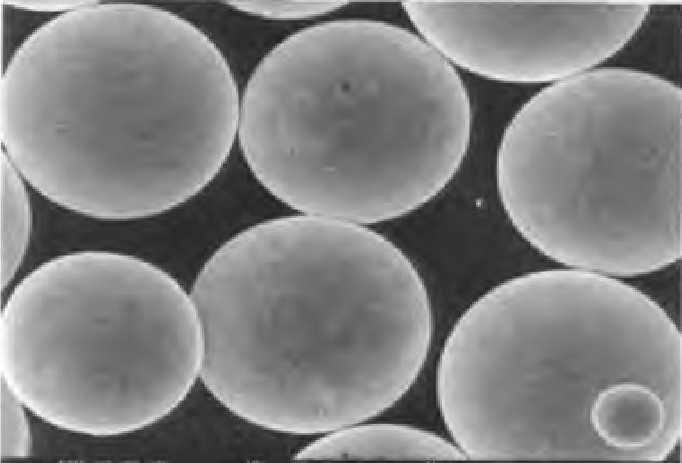
Pros and Cons of Aluminum Based Alloy Powders
Pros:
- Excellent Strength-to-Weight Ratio: Aluminum based alloy powders inherit this key advantage from aluminum itself, making them ideal for applications demanding both strength and weight reduction.
- Design Flexibility: 3D printing with aluminum based alloy powders unlocks a new world of design possibilities. Complex geometries, intricate internal features, and even hollow components become achievable.
- Near-Net-Shape Manufacturing: This translates to less material waste and potentially more complex geometries compared to conventional methods.
- Potential for Customization: The ability to tailor the composition of aluminum based alloy powders allows for some degree of customization for specific applications.
- Lightweighting Potential: This translates to improved fuel efficiency in vehicles and aircraft, and enhanced performance in various applications.
Cons:
- Cost: Aluminum based alloy powders can be more expensive than some traditionally used materials, especially when considering finer particle sizes or high-performance grades.
- 3D Printing Limitations: While offering greater design freedom than traditional methods, 3D printing with aluminum based alloy powders still has limitations in terms of build size and surface finish compared to some established techniques.
- Safety Considerations: Aluminum based alloy powders can be flammable and pose health risks if inhaled. Proper handling procedures and safety equipment are crucial when working with these materials.
- Limited Applications in Certain Industries: Due to factors like cost and printability limitations, aluminum based alloy powders may not be the best choice for all applications in every industry.
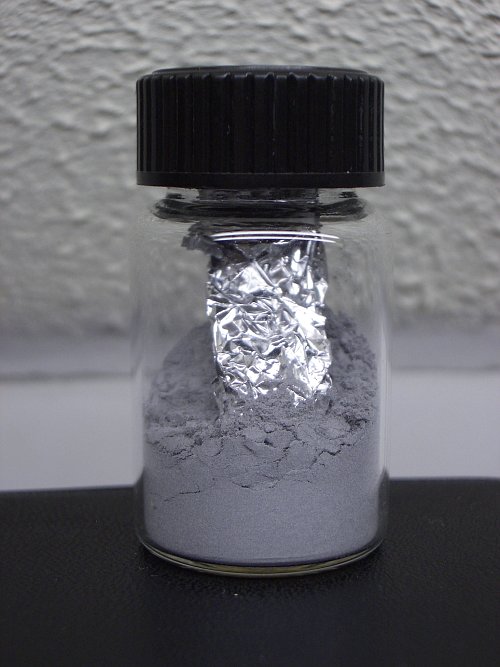
FAQ
Q: What are the advantages of using aluminum based alloy powders over traditional manufacturing methods?
A: Aluminum based alloy powders offer several advantages over traditional manufacturing techniques like machining, casting, and forging. Here’s a breakdown of some key benefits:
- Design Flexibility: 3D printing with aluminum based alloy powders allows for the creation of intricate geometries, internal features, and even hollow components that would be difficult or impossible to achieve through traditional methods. Imagine designing a lightweight component with internal channels for improved heat dissipation – this becomes a reality with 3D printing.
- Near-Net-Shape Manufacturing: Unlike traditional subtractive manufacturing (removing material to create a desired shape), 3D printing with aluminum based alloy powders allows for near-net-shape manufacturing. This translates to less material waste, reduced machining requirements, and potentially faster production times.
- Lightweighting Potential: The excellent strength-to-weight ratio of aluminum translates directly to aluminum based alloy powders. This makes them ideal for applications where weight reduction is a prime concern. Think of an airplane wing – components made from these powders can be incredibly strong yet significantly lighter than traditionally manufactured counterparts, leading to improved fuel efficiency and overall performance.
- Potential for Customization: By adjusting the composition of the alloying elements, manufacturers can create aluminum based alloy powders with properties optimized for specific applications. Need a component that’s not only strong but also highly corrosion resistant? A customized powder formulation might be the answer.
- Rapid Prototyping: The ability to create complex objects directly from a digital model makes aluminum based alloy powders ideal for rapid prototyping. This allows engineers and designers to iterate on designs quickly and efficiently, accelerating the product development process.
Q: What are some of the safety considerations when working with aluminum based alloy powders?
A: Aluminum based alloy powders can be flammable and pose health risks if inhaled. Here are some crucial safety considerations:
- Always wear appropriate personal protective equipment (PPE) when handling aluminum based alloy powders. This includes safety glasses, gloves, and a respirator with a dust filter suitable for aluminum particles.
- Work in a well-ventilated area. Dust particles can accumulate in poorly ventilated spaces, so proper ventilation is essential to minimize inhalation risks.
- Practice good housekeeping. Clean up spills promptly and avoid creating dust clouds. Regularly clean work surfaces and equipment to prevent powder accumulation.
- Store aluminum based alloy powders in a safe and dry location. Keep them away from heat sources and ignition points.
Q: How do I choose the right aluminum based alloy powder for my application?
A: Selecting the optimal aluminum based alloy powder requires considering several factors:
- The desired properties: Do you prioritize strength, weight reduction, corrosion resistance, or a combination of factors? Different grades offer different property combinations.
- The application requirements: What will the component be used for? Understanding the stresses and environmental conditions it will encounter will help narrow down your choices.
- The 3D printing process: Different 3D printing technologies may have specific requirements or limitations regarding powder characteristics. Consult your machine’s manual or the powder supplier for compatibility information.
- Cost considerations: Aluminum based alloy powders can vary in price. Determine your budget and find a powder that offers the required properties within your cost constraints.