In718 powder, also known as Inconel 718 powder, is a nickel-based alloy powder used in various metal additive manufacturing applications such as aerospace, automotive, and nuclear industries. This guide provides a comprehensive overview of In718 powder, including its properties, applications, suppliers, costs, installation, operation and maintenance.
Overview of In718 Powder
In718 powder is a precipitation-hardenable nickel-chromium alloy also containing significant amounts of iron, niobium, and molybdenum along with lesser amounts of aluminum and titanium. Key properties of In718 powder include:
- High strength and hardness maintained up to 700°C temperature
- Excellent corrosion resistance
- Good weldability and fabricability
- High fatigue strength and creep resistance at high temperatures
Table: Key Properties of In718 Powder
Properties | Details |
---|---|
Composition | Nickel 50-55%, Chromium 17-21%, Iron Balance, Niobium 4.75-5.5%, Molybdenum 2.8-3.3%, Aluminum 0.2-0.8%, Titanium 0.65-1.15%, Carbon 0.08% max |
Density | 8.19 g/cm3 |
Melting Point | 1260-1336°C |
Maximum Service Temperature | 700°C |
Tensile Strength | 1250 MPa (min) |
Yield Strength | 1000 MPa (min) |
Elongation | 12% (min) |
Thermal Conductivity | 11.4 W/m-K |
Thermal Expansion Coefficient | 13 μm/m-°C |
Modulus of Elasticity | 205 GPa |
Electrical Resistivity | 123 μΩ-cm |
In718 powder can be used to manufacture parts with complex geometries, thin walls, hidden voids and lattices using powder bed fusion techniques like selective laser melting (SLM) and electron beam melting (EBM). Key applications include aerospace components like turbine blades and discs, automotive turbocharger wheels and nuclear fuel claddings.
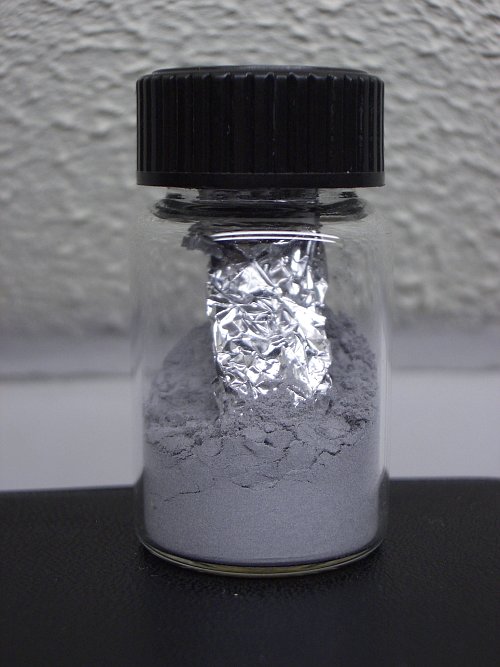
Applications and Uses of In718 Powder
In718 powder is commonly used in the following applications thanks to its high strength at elevated temperatures, corrosion resistance and ease of processing:
Table: Applications of In718 Powder
Application | Details |
---|---|
Aerospace | Turbine blades, discs, shafts, fasteners, casings, fittings |
Automotive | Turbocharger wheels, valves, exhaust components |
Oil and Gas | Downhole tools, valves, wellhead components |
Power Generation | Steam and gas turbine blades, heat exchangers |
Biomedical | Orthopedic and dental implants, prosthetics |
Tooling | Injection molds, forming dies, extrusion dies |
The key advantages of using In718 powder for these applications include:
- Withstands high pressure and temperatures in turbine and automotive uses
- Corrosion resistance for oil and gas parts
- High fatigue strength for dynamic components
- Biocompatibility for implants and prosthetics
- Can produce complex geometries not possible with machining
In718 is popular for aerospace applications like jet engine parts operating under extreme environments. Automotive uses benefit from turbocharger wheels made of In718 able to reach high speeds under high temperatures. The oil and gas industry leverages the material’s corrosion resistance in downhole tools and valves. These and other applications take advantage of In718’s unique combination of high strength, fatigue resistance, and oxidation resistance.
Specifications of In718 Powder
In718 powder for additive manufacturing use must meet strict specifications for composition, particle size distribution, flowability, and microstructure.
Table: Typical Specifications for In718 Powder
Parameter | Specification |
---|---|
Alloy Composition | Meets AMS 5663, AMS 5664 standards |
Particle Size | 15-45 μm |
Oxygen Content | <0.1 wt% |
Nitrogen Content | <0.1 wt% |
Apparent Density | >4.0 g/cm3 |
Flow Rate | >1.25 s/50g |
Particle Shape | Spherical, satellite-free |
Interior Porosity | Minimal |
Surface Chemistry | Passivated |
Key considerations when selecting In718 powder include:
- Particle size distribution tailored for chosen AM process
- High apparent density above 4 g/cm3
- Flowability matching printer requirements
- Spherical morphology with minimal satellites
- Low internal porosity inside particles
- Proper alloy composition and microstructure
Meeting powder specifications helps achieve consistent, high-density AM parts with the desired mechanical properties and material performance. Reputable suppliers will provide detailed documentation of powder analysis and properties.
In718 Powder Suppliers
Many leading metal powder manufacturers supply In718 powder suitable for AM processes like SLM and EBM:
Table: Select Suppliers of In718 Powder
Company | Powder Grade | Particle Size |
---|---|---|
LPW Technology | CARP-718 | 15-45 μm |
Praxair | 718 | 15-53 μm |
Carpenter Additive | CarTech In718 | 15-45 μm |
Sandvik Osprey | Osprey In718 | 15-45 μm |
AP&C | Plasma IN718 | 15-45 μm |
Oerlikon Metco | MetcoAdd In718 | 10-45 μm |
When selecting an In718 powder supplier, key factors to consider include:
- Experience producing aerospace-grade powder
- Capacity for large volume production
- Stringent quality control and documentation
- Powder customized for chosen AM process
- Competitive pricing and lead times
- Technical expertise and customer service
Work closely with suppliers to ensure the powder composition, particle characteristics and quality meet both application requirements and printer specifications.
Cost of In718 Powder
In718 powder costs between $50-$120 USD per kg based on quantity and supplier. Prices are higher for smaller quantities under 100 kg.
Table: Indicative Cost Ranges for In718 Powder
Purchase Quantity | Cost per kg |
---|---|
20-50 kg | $100-120 |
50-100 kg | $80-100 |
100-500 kg | $60-80 |
500-1000+ kg | $50-70 |
The powder cost contributes 15-30% to the total part cost in AM. Key factors affecting In718 powder pricing:
- Purity, quality and lot size
- Competition and availability
- Price volatility of elemental materials
- Order quantity and bulk discounts
- Geographic region and tariffs
Work with qualified suppliers to optimize cost through bulk orders without compromising powder quality. Consider recycling powder from AM builds to lower cost per part.
Installing and Operating In718 Powder Printers
Installing and operating metal powder bed fusion printers for In718 requires careful planning and preparation:
Table: In718 Printer Installation Guidelines
Parameter | Guidelines |
---|---|
Facility Requirements | Temperature control, dedicated power lines, compressed air, argon or nitrogen supply, ventilation and dust extraction |
Space Requirements | Allow clearance on all sides for maintenance access, powder handling, workflow |
Power Requirements | Supply capacity of 30-150 kW, stable voltage |
Exhaust Filtration | HEPA or ULPA filters for capture of fine particulates |
Powder Handling | Gloveboxes, sieving equipment, mixing hoppers, containers meeting safety standards |
Personal Protective Equipment | Fire safety gear, protective clothing, chemical gloves, face masks |
Staffing | Trained technicians for operation and maintenance, metallurgists, quality personnel |
Critical factors for operating In718 printers:
- Strictly follow manufacturer’s usage and maintenance instructions
- Ensure uninterrupted power supply and stable voltage
- Use high purity argon or nitrogen and controlling moisture levels
- Employ automated powder handling and sieving equipment to minimize contamination
- Implement safety procedures for handling reactive powder material
- Provide dedicated training on machine operation, post-processing steps, quality assurance
Careful installation, training and procedures are essential to achieve defect-free In718 parts consistently and cost-effectively using metal AM. Personnel involved must be experienced in both additive manufacturing processes and advanced nickel-based alloys to ensure success.
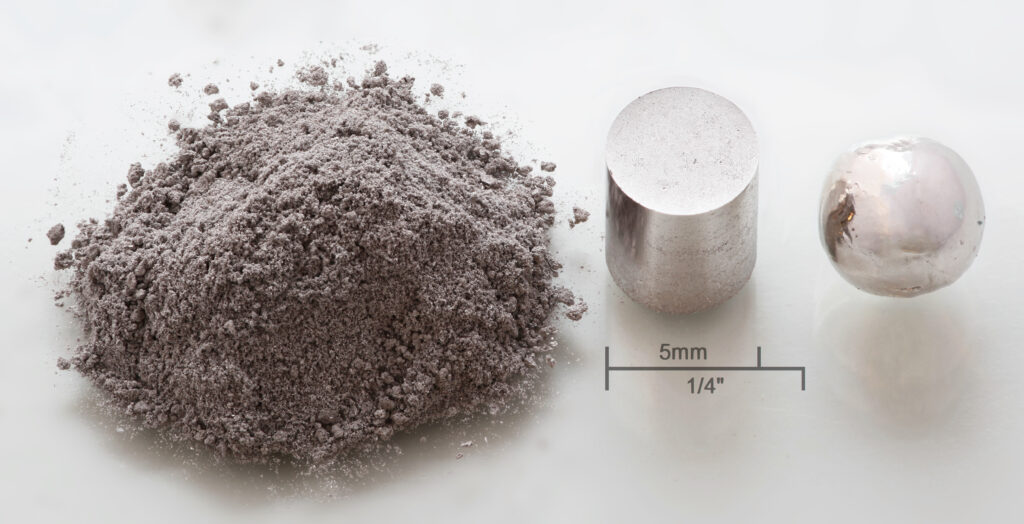
Maintaining In718 Printers
Proper maintenance is required to sustain uptime and performance of In718 printers. The table below provides general guidelines:
Table: Recommended Maintenance Tasks for In718 Printers
System | Maintenance Activities | Frequency |
---|---|---|
Laser optics | Cleaning, alignment checks | Daily to weekly |
Powder bed | Levelling calibration, recoating blade replacement | Weekly to monthly |
Filters | Cleaning and replacing HEPA/ULPA filters | 500 hours |
Powder delivery | Check seals, valves, replace damaged hoses | Weekly |
Cooling pumps | Flow rate testing, hose inspection | Monthly |
Motion system | Rail cleaning and lubrication, belt tensioning | 500-2000 hours |
Electronics | Firmware update checks, cable inspection | As needed |
Data backup | System settings and log file backups | Daily |
Full system | Major calibrations, hardware swap, alignments | Yearly or 2000 hours |
In addition, consumables like build plates, recoater blades, filters and seals require regular replacement every few hundred hours of operation based on condition and wear.
Use log sheets, preventive maintenance schedules, and real-time monitoring to ensure all critical printer components are maintained in peak condition. Partner with the machine OEM to perform major overhauls or diagnostics as needed.
Proactive maintenance paired with operator training is essential for maximizing printer availability, repeatability, and cost-effectiveness when working with specialized alloys like In718.
How to Select an In718 Powder Printer
Choosing an In718 powder bed fusion printer involves evaluating several key parameters:
Table: How to Select Suitable In718 Printer
Considerations | Guidelines |
---|---|
Build Size | Match maximum part dimensions, consider future needs |
Laser Power | >400 W fiber laser for pre-alloyed In718 powder |
Scanning Speed | >5 m/s for production throughput |
Precision Optics | Small laser spot size (~50 μm) for fine resolution |
Inert Gas Flow | Sealed, oxygen controlled chamber with argon or nitrogen |
Powder Handling | Automated powder sieving and recycling system |
Process Monitoring | In-situ melt pool and thermal monitoring for defect control |
Parameter Optimization | Established for In718 to ensure density and properties |
Controls Software | User-friendly interface for job preparation and process adjustment |
Cost | Factor in total cost of ownership over machine lifetime |
Service and Support | Responsive OEM support team for issues and maintenance |
Work closely with 3D printer OEM representatives to select a system optimized for In718 printing meeting your specific application requirements in terms of part size, throughput, quality control, operating cost and ease of use.
Advantages of In718 Powder Printers
Key benefits of using In718 powder bed fusion printers:
Table: Benefits of In718 Powder Bed Printers
Advantages | Details |
---|---|
Complex geometries | Internal channels, lattices and organic shapes unsupported by machining |
Customized properties | Locally vary composition, microstructure, density |
Reduced assemblies | Consolidate multiple components through topology optimization |
Weight savings | Lighter designs from topology optimization |
Increased efficiency | Less material waste than subtractive processes |
Rapid design iterations | Print design variants faster than machining |
Just-in-time production | Manufacture parts on demand with no tooling |
Part consolidation | Combine assemblies into single components |
Shorter lead times | Produce parts without lengthy casting process |
These advantages of powder bed AM enable innovative In718 component designs not feasible with conventional manufacturing. The technology is seeing rapid adoption across aerospace, automotive, medical and industrial markets to leverage these benefits.
Limitations of In718 Powder Printers
Despite the benefits, In718 AM printers have certain limitations to consider:
Table: Limitations of In718 Powder Bed Printers
Limitations | Detail |
---|---|
High machine cost | Printers have high upfront capital investment |
Limited sizes | Maximum part size typically under 500 mm |
Lower throughput | Production speeds slower than high-volume processes |
Post-processing | Additional steps like supports removal, heat treatment required |
Anisotropic properties | Mechanical properties vary based on build orientation |
Operator expertise | Specialized training needed to operate printers effectively |
Parameter optimization | Extensive development required for new alloy compositions |
Powder handling | Inert environment required to avoid contamination |
Safety procedures | Careful handling of reactive metal powder needed |
While the technology is rapidly evolving to overcome these challenges, end users should carefully factor in the current capabilities and constraints of In718 AM during adoption.
Comparing In718 Print Processes
The two main powder bed fusion processes used for In718 are selective laser melting (SLM) and electron beam melting (EBM).
Table: SLM versus EBM Process Comparison for In718
SLM | EBM | |
---|---|---|
Heat source | Fiber laser | Electron beam |
Atmosphere | Inert argon | Vacuum |
Scan speed | 100-500 mm/s | >2000 mm/s |
Beam size | 70-100 μm | 200-300 μm |
Layer thickness | 20-50 μm | 50-200 μm |
Surface finish | Fine | Medium to rough |
Accuracy | ±50 μm | ±150 μm |
Cost | $ | $$ |
Productivity | Low to moderate | High |
Commercial systems | Many established suppliers | Fewer suppliers |
Pros of SLM:
- Finer features and surface finish possible
- More materials options like Al, Ti optimized
- Lower beam current minimizes evaporation
- Established technology with multiple suppliers
Pros of EBM:
- Faster build rates improve productivity
- Larger build volumes possible
- Lower thermal stresses and less support needed
- High beam current suits high-conductivity alloys
Work with your application requirements and internal constraints to select the optimal powder bed process for In718 printing. Both SLM and EBM offer competitive advantages that continue to drive adoption in industry.
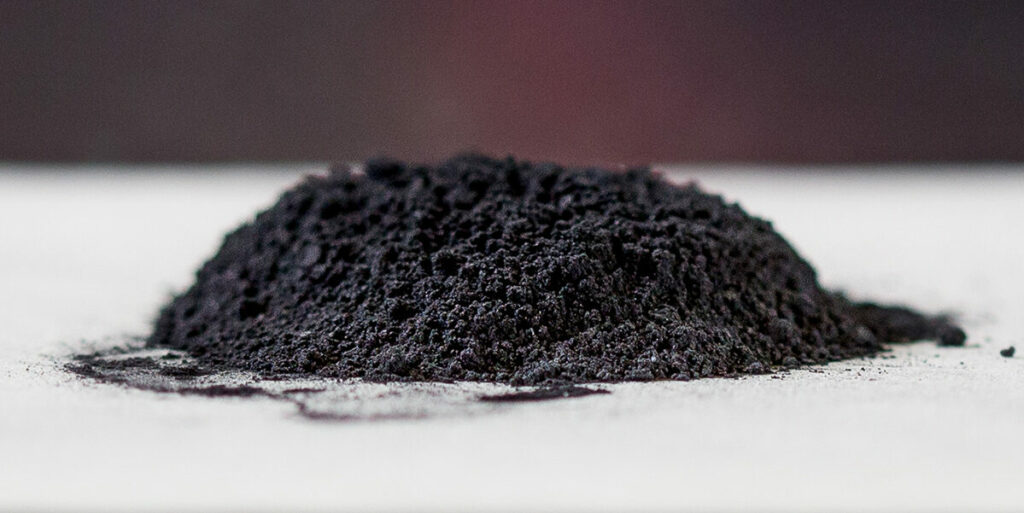
Achieving Optimal In718 Print Quality
To achieve high quality In718 prints, focus on:
- Parameters: Optimize laser power, speed, hatch, scan strategy for highest density without defects
- Powder: Use high purity powder with controlled particle size distribution
- Supports: Use optimized supports to minimize surface roughness
- Orientation: Minimize overhangs and orient parts to avoid anisotropy
- Inert gas: Ensure high purity argon or nitrogen atmosphere
- Preheating: Use hot powder bed to reduce stresses and cracking
- Melt pools: Adapt scan patterns and spacing to enable stable melt pools
- Post-processing: Apply heat treatment, HIP, and machining to enhance properties
Continuously monitoring density, microstructure, powder condition and mechanical performance with test geometries allows dialing in parameters and procedures over multiple builds until the desired repeatable print quality is reached.
Safety Precautions for In718 Powder
As a reactive metal, In718 powder requires careful handling to avoid fires and explosions:
- Store powder only in approved containers under inert gases
- Avoid ignition sources – no sparks, smoking, or open flames
- Employ grounding, bonding, inert gas blanketing to prevent static discharge
- Use appropriate PPE – fire retardant clothing, face mask, gloves
- Handle and sieve powder only in ventilated areas or gloveboxes
- Safely dispose of used powder in sealed containers
- Follow all recommended precautions from powder and printer suppliers
Establishing and enforcing rigorous safety protocols when handling the flammable powder is critical to mitigate operational risks when working with In718 and other reactive alloys.
Qualifying Parts Printed using In718 Powder
To validate quality, In718 printed parts must pass inspection and testing for:
- Dimensional accuracy – CMM and optical measurement
- Surface roughness – Optical and tactile profilometry
- Density – Archimedes method and porosity image analysis
- Microstructure – Optical and electron microscopy
- Composition – Chemical analysis like ICP-OES
- Mechanical properties – Tensile, fatigue, fracture toughness testing
- Non-destructive testing – Dye penetrant, X-ray tomography, ultrasonic
Compare results to stated design requirements as well as wrought properties specified in applicable AMS standards for In718. Implement a comprehensive quality program covering powder management, printer calibration, process monitoring, test geometries, and documentation to ensure printed parts meet the desired material performance in their intended service conditions.
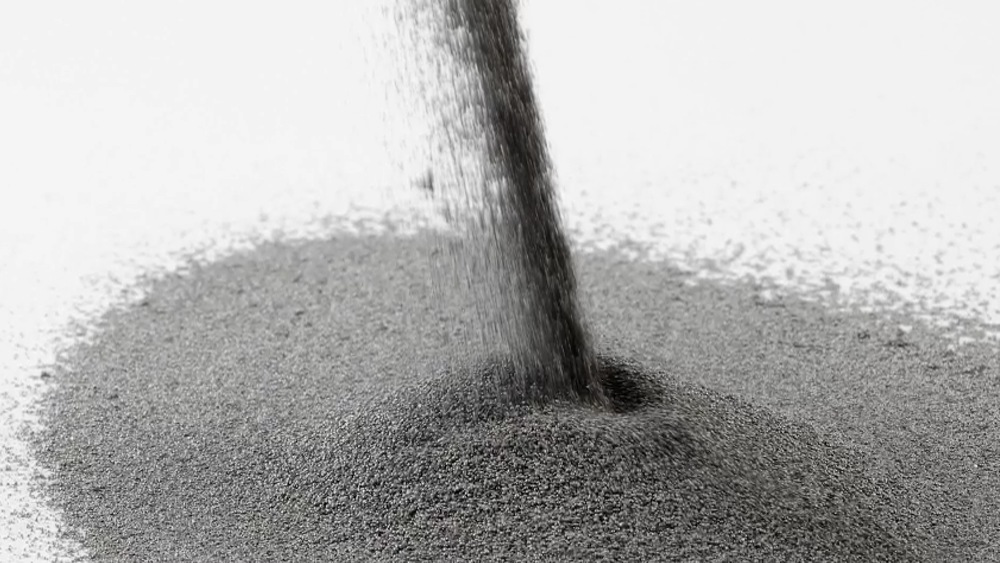
FAQ
Q: Does In718 powder require hot isostatic pressing (HIP) after AM?
A: HIP is recommended to close internal voids and improve fatigue life. But with tightly controlled parameters, HIP may not be required to meet design allowables.
Q: Can In718 parts be machined after printing?
A: Yes, machining and other subtractive processes can be used improve surface finish and achieve tighter tolerances on printed In718 components.
Q: What heat treatment is used for In718 AM parts?
A: Solution annealing at 980°C plus aging at 720°C and 620°C per AMS specs is typically used to achieve desired microstructure and properties.
Q: What types of post-processing are recommended for In718 AM parts?
A: In addition to heat treatment, hot isostatic pressing (HIP), surface machining, shot peening, and other finishing steps may be used to enhance final part properties. The post-processing plan depends on the application requirements.
Q: Does In718 powder oxidation during storage impact properties?
A: Yes, In718 powder can oxidize over time in normal atmosphere leading to increased oxygen content. Use of inert gas sealing and oxygen absorbers is recommended to maximize powder reuse life.
Q: What is the typical surface roughness of In718 as-printed parts?
A: In718 printed on a powder bed fusion machine typically has a surface roughness of Ra 5-15 microns depending on orientation and process parameters. Strategies like support structures and post-machining can further improve surface finish.
Q: Are there health and environmental risks specific to In718 powder?
A: Like other nickel-based alloys, In718 powder may cause skin sensitization with prolonged contact. Use of PPE is advised when handling powder. No specific environmental hazards are associated with In718.
Q: What are some alternatives to In718 for high-temperature aerospace applications?
A: Other nickel-based superalloys like In625, In792, and Haynes 282 offer similar oxidation resistance and can be alternatives depending on the exact operating conditions. Ti-6Al-4V is also widely used in aerospace components.