Introduction
Definition of Metal Powder
Metal powder refers to a finely divided form of metal that is used in various industries, including 3D printing technology. It is produced through processes such as atomization, where molten metal is sprayed into a gas or liquid medium to create small droplets that solidify into powder particles. Metal powder is characterized by its high surface area-to-volume ratio, which makes it ideal for applications where a large surface area is desired, such as in 3D printing. In this technology, metal powder is used as the raw material to create three-dimensional objects by selectively fusing the powder particles together layer by layer. The use of metal powder in 3D printing technology has revolutionized the manufacturing industry by enabling the production of complex and intricate metal parts with high precision and efficiency.
Overview of 3D Printing Technology
The overview of 3D printing technology provides a comprehensive understanding of the various applications and advancements in this rapidly evolving field. With the advent of metal powder in 3D printing, the possibilities have expanded exponentially. Metal powder, such as titanium, stainless steel, and aluminum, is being used to create intricate and durable components for a wide range of industries, including aerospace, automotive, and healthcare. The ability to print complex geometries and structures with metal powder has revolutionized the manufacturing process, enabling the production of lightweight yet strong parts that were previously impossible to create. This has led to significant cost savings, improved efficiency, and reduced waste in the production cycle. As the technology continues to advance, the applications of metal powder in 3D printing are only expected to grow, opening up new opportunities for innovation and design.
Importance of Metal Powder in 3D Printing
The importance of metal powder in 3D printing cannot be overstated. Metal powder is a key component in the additive manufacturing process, specifically in the production of metal parts using 3D printing technology. It serves as the raw material that is melted and fused together layer by layer to create intricate and complex metal structures. The quality and properties of the metal powder used directly impact the final product, including its strength, durability, and surface finish. Therefore, selecting the right metal powder is crucial in ensuring the desired characteristics of the printed metal parts. Additionally, metal powder in 3D printing enables the production of highly customized and unique metal objects that may not be achievable through traditional manufacturing methods. This opens up new possibilities in various industries, such as aerospace, automotive, and healthcare, where the ability to create complex metal components with precise geometries is essential. In conclusion, the use of metal powder in 3D printing technology plays a vital role in revolutionizing manufacturing processes and expanding the capabilities of metal additive manufacturing.
Types of Metal Powders Used in 3D Printing
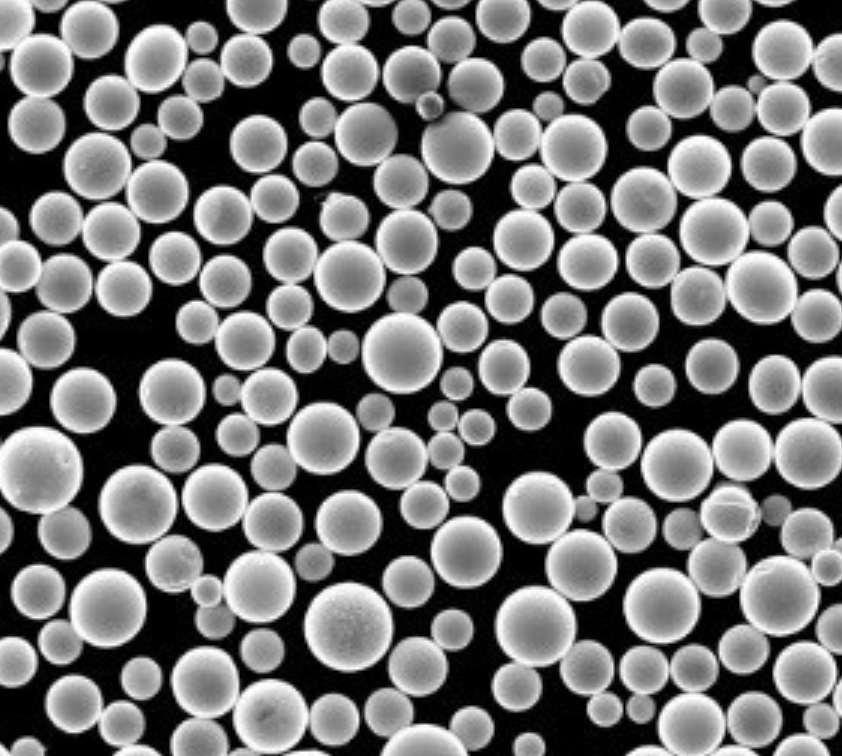
Stainless Steel Powder
Stainless steel powder is one of the most widely used metal powders in 3D printing technology. It offers excellent strength, durability, and corrosion resistance, making it suitable for a wide range of applications. The fine particles of stainless steel powder can be precisely deposited layer by layer to create complex and intricate designs with high precision. This makes it a popular choice for industries such as automotive, aerospace, and medical, where the production of intricate and durable parts is crucial. Additionally, stainless steel powder can be easily sintered to achieve the desired mechanical properties, further enhancing its versatility in 3D printing applications. With its outstanding properties and versatility, stainless steel powder continues to play a significant role in advancing the capabilities of 3D printing technology.
Titanium Powder
Titanium powder is widely used in 3D printing technology due to its unique properties. It has excellent strength-to-weight ratio, corrosion resistance, and biocompatibility, making it an ideal choice for various applications. In the aerospace industry, titanium powder is used to manufacture lightweight and durable components for aircraft and spacecraft. In the medical field, it is utilized to produce implants and prosthetics that can be customized to fit individual patients. Additionally, titanium powder is also employed in the automotive, defense, and energy sectors. With the advancements in 3D printing technology, the use of titanium powder is expected to further expand, revolutionizing various industries.
Aluminum Powder
Aluminum powder is widely used in 3D printing technology due to its excellent properties and versatility. It is a lightweight material with high strength-to-weight ratio, making it ideal for aerospace and automotive applications. Aluminum powder also has good thermal conductivity, allowing for efficient heat dissipation in electronic components. Additionally, it is corrosion-resistant, ensuring the longevity of printed parts. The ability of aluminum powder to be easily sintered or melted enables the production of complex and intricate designs. Overall, aluminum powder plays a crucial role in advancing the capabilities of 3D printing technology.
Advantages of Using Metal Powder in 3D Printing
Enhanced Strength and Durability
Enhanced Strength and Durability are key advantages of using metal powder in 3D printing technology. By incorporating metal powder into the printing process, the resulting objects exhibit superior strength and durability compared to those made from traditional materials. This is particularly beneficial in industries such as aerospace and automotive, where high-performance components need to withstand extreme conditions and heavy loads. The use of metal powder allows for the production of complex geometries and intricate designs that would be challenging or impossible to achieve with other manufacturing methods. Additionally, the ability to customize the composition of the metal powder further enhances the strength and durability of the printed objects, as specific alloys can be tailored to meet the desired mechanical properties. Overall, the application of metal powder in 3D printing technology offers a significant advancement in the strength and durability of printed objects, opening up new possibilities for various industries.
Design Flexibility
Design flexibility is one of the key advantages of using metal powder in 3D printing technology. With the ability to create complex geometries and intricate designs, metal powder allows for unprecedented freedom in design. Traditional manufacturing methods often have limitations in terms of the shapes and structures that can be produced, but with 3D printing using metal powder, these constraints are significantly reduced. This opens up a world of possibilities for industries such as aerospace, automotive, and healthcare, where intricate and customized parts are often required. Whether it’s creating lightweight components with intricate lattice structures or designing parts with complex internal channels, metal powder in 3D printing technology offers unparalleled design flexibility.
Cost-effectiveness
Cost-effectiveness is one of the key advantages of using metal powder in 3D printing technology. Compared to traditional manufacturing methods, such as casting or machining, 3D printing with metal powder offers significant cost savings. This is primarily due to the minimal material waste involved in the process. With traditional methods, excess material is often discarded, leading to higher costs. In contrast, 3D printing with metal powder allows for precise and targeted deposition of material, reducing waste and optimizing cost-efficiency. Additionally, the ability to create complex geometries and intricate designs with metal powder further enhances the cost-effectiveness of 3D printing technology. By eliminating the need for multiple manufacturing steps and reducing the amount of material required, metal powder in 3D printing offers a cost-effective solution for producing high-quality metal parts.
Applications of Metal Powder in 3D Printing
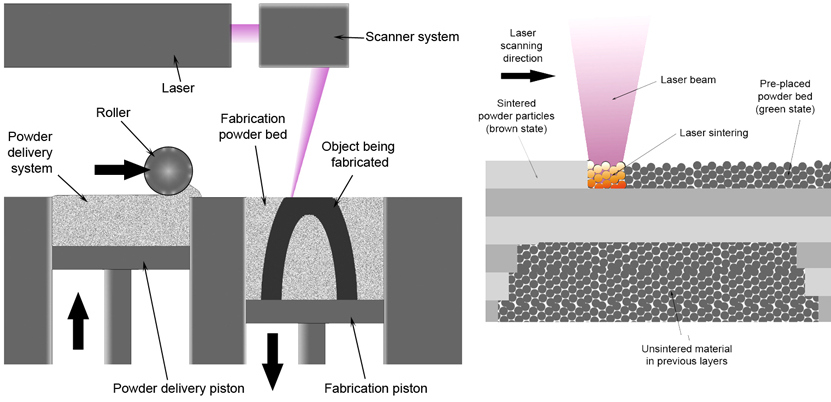
Aerospace Industry
The aerospace industry has been one of the key beneficiaries of the applications of metal powder in 3D printing technology. With its ability to produce complex and lightweight components, 3D printing has revolutionized the way aircraft and spacecraft are designed and manufactured. Metal powder, such as titanium and aluminum alloys, is used as the raw material in 3D printing processes, allowing for the creation of high-performance parts that are both strong and lightweight. This has resulted in improved fuel efficiency, reduced production costs, and enhanced overall performance of aerospace vehicles. Moreover, 3D printing has also enabled the production of customized components, tailored to specific needs and requirements, further enhancing the capabilities of the aerospace industry.
Medical Industry
The medical industry has greatly benefited from the applications of metal powder in 3D printing technology. With the ability to create complex and customized medical implants, 3D printing has revolutionized the field of healthcare. Metal powders such as titanium and stainless steel are used to create durable and biocompatible implants, ranging from orthopedic implants to dental prosthetics. This technology allows for precise and personalized solutions, improving patient outcomes and reducing recovery times. Additionally, 3D printing enables the production of intricate surgical tools and instruments, enhancing surgical precision and efficiency. The use of metal powder in 3D printing has opened up new possibilities in the medical industry, paving the way for advancements in patient care and treatment.
Automotive Industry
The automotive industry has been one of the key beneficiaries of the applications of metal powder in 3D printing technology. With the ability to create complex and lightweight parts, 3D printing has revolutionized the manufacturing process in the automotive sector. Metal powders, such as aluminum, titanium, and stainless steel, are used to fabricate components that are not only durable but also offer enhanced performance. From engine parts to customized car accessories, 3D printing has enabled automakers to optimize designs, reduce costs, and improve overall efficiency. As a result, the automotive industry has witnessed significant advancements in terms of innovation, sustainability, and production capabilities.
Challenges and Limitations of Metal Powder 3D Printing
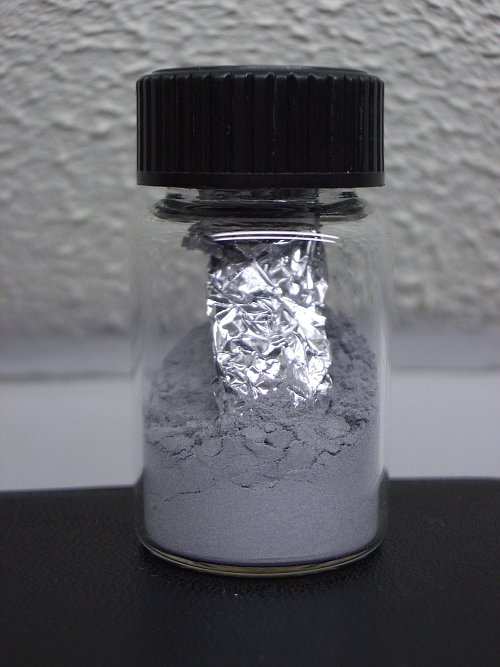
High Cost of Metal Powders
The high cost of metal powders is one of the major challenges in the widespread adoption of 3D printing technology. Metal powders used in 3D printing are often expensive due to the specialized manufacturing processes involved and the high purity requirements. Additionally, the limited availability of certain metal powders further drives up the cost. As a result, the high cost of metal powders can significantly impact the overall cost of 3D printing projects, making it less accessible for small businesses and individuals. However, efforts are being made to develop cost-effective alternatives and improve the efficiency of metal powder production, which could help reduce the cost barrier and accelerate the adoption of 3D printing technology in various industries.
Complex Post-Processing
Complex post-processing is an essential step in the 3D printing process that involves additional treatments and finishing techniques to achieve the desired final product. After the metal powder has been fused together to create the desired shape, there are often imperfections and rough surfaces that need to be addressed. This is where complex post-processing comes into play, as it allows for the refinement and improvement of the printed part. Various techniques such as sanding, polishing, and chemical treatments can be used to smoothen the surface, remove any remaining support structures, and enhance the overall appearance of the 3D printed object. Additionally, complex post-processing can also involve heat treatment processes to further strengthen the metal and improve its mechanical properties. By implementing these post-processing techniques, manufacturers can ensure that the final 3D printed products meet the required standards of quality and performance.
Limited Material Options
In the field of 3D printing technology, one of the limitations that manufacturers often encounter is the limited material options available. Traditionally, 3D printing has been primarily associated with plastic materials. However, with the advancements in metal powder technology, the range of materials that can be used in 3D printing has expanded significantly. Metal powder, such as titanium, aluminum, and stainless steel, offers enhanced strength, durability, and heat resistance compared to plastic. This opens up new possibilities for manufacturing complex and high-performance components in various industries, including aerospace, automotive, and healthcare. By utilizing metal powder in 3D printing, manufacturers can create parts with precise geometries and intricate designs that were previously unattainable with conventional manufacturing methods. Despite the progress, it is important to note that the cost of metal powders can be relatively higher than plastic materials, which can still limit the widespread adoption of metal powder in 3D printing. However, as research and development continue, it is expected that more cost-effective metal powder options will become available, further expanding the applications of 3D printing technology.
Future Trends in Metal Powder 3D Printing
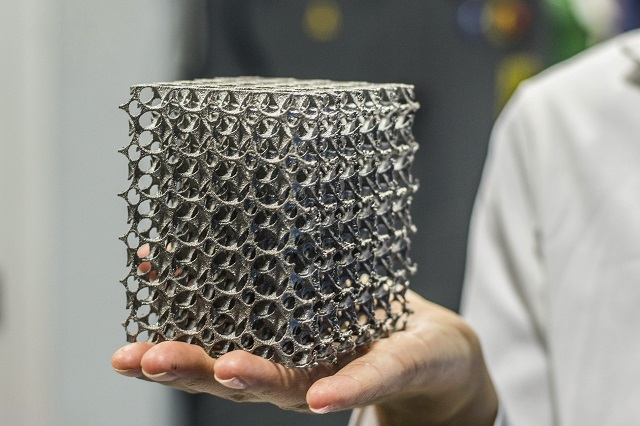
Development of New Metal Alloys
The development of new metal alloys has played a crucial role in the advancement of 3D printing technology. With the ability to create complex geometries and intricate designs, 3D printing has revolutionized various industries. Metal powders, such as titanium, aluminum, and stainless steel, are widely used in this process. These alloys offer improved mechanical properties, including high strength, durability, and corrosion resistance. Furthermore, the use of metal powders in 3D printing allows for the production of lightweight components with excellent structural integrity. As researchers continue to explore new alloy compositions and optimize printing parameters, the possibilities for the applications of metal powder in 3D printing technology are expanding rapidly.
Improved Printing Techniques
Improved printing techniques have revolutionized the field of 3D printing technology, especially when it comes to the applications of metal powder. With advancements in printing technology, manufacturers are now able to achieve higher precision and accuracy in printing metal objects. This has opened up a whole new realm of possibilities in various industries, including aerospace, automotive, and healthcare. The improved printing techniques allow for the creation of complex and intricate metal parts that were previously impossible to produce. Additionally, these techniques have also resulted in faster printing speeds, reducing production time and costs. As a result, the use of metal powder in 3D printing technology has become increasingly popular, offering numerous advantages over traditional manufacturing methods.
Integration with Other Manufacturing Processes
Integration with other manufacturing processes is a key advantage of using metal powder in 3D printing technology. By combining 3D printing with traditional manufacturing methods such as casting, forging, and machining, manufacturers can achieve complex geometries and enhance the overall strength and performance of the final product. This integration allows for the creation of components that were previously difficult or impossible to produce using conventional techniques. Additionally, the ability to seamlessly integrate different manufacturing processes enables greater flexibility and customization in product design, leading to improved efficiency and cost-effectiveness in various industries, including aerospace, automotive, and healthcare.