Inconel 718 is a high-strength, corrosion-resistant nickel chromium alloy used extensively in aerospace, nuclear, and other high-temperature applications. When in powder form, Inconel 718 can be used in metal additive manufacturing processes like selective laser melting (SLM) and electron beam melting (EBM) to create complex parts with superior mechanical properties compared to traditional manufacturing methods.
This guide will provide a detailed overview of Inconel 718 powder, its applications, advantages, buying considerations, top suppliers, and more.
Overview of Inconel 718 Powder
Inconel 718 powder is a fine metallic powder form of the nickel-chromium based superalloy. The key characteristics of Inconel 718 powder include:
Table 1: Overview of Inconel 718 Powder
Properties | Details |
---|---|
Composition | Nickel, Chromium, Iron, Niobium, Molybdenum, Titanium, Aluminum |
Particle Shape | Spherical, satellite, truncated spheroidal |
Size Range | 15-45 microns |
Melting Point | 1260-1336°C |
Density | 8.19 g/cm3 |
Key Advantages | High strength, Good corrosion resistance, Excellent creep and fatigue resistance, Outstanding weldability and machinability, Retains mechanical properties at elevated temperatures |
Common Applications | Aerospace components – blades, discs, shafts, Airframes, Rocket motors, Nuclear reactors, Petrochemical equipment, Gas turbines |
The unique combination of properties like high tensile strength, resistance to creep, stress rupture, and outstanding corrosion resistance make Inconel 718 suitable for extreme operating conditions. The fine particle size allows intricate shapes and components to be 3D printed.
Applications and Uses of Inconel 718 Powder
Inconel 718 powder has become indispensable in industries like aerospace, nuclear, oil & gas, chemical processing, and power generation due to its capability to withstand prolonged exposure to high temperatures and pressures.
Table 2: Applications and Uses of Inconel 718 Powder
Industry | Components and Parts |
---|---|
Aerospace | Turbine blades, discs, shafts, casings, fasteners, bellows, rocket motors |
Nuclear | Reactor vessels, heat exchangers, fasteners, springs |
Oil & Gas, Petrochemical | Wellhead equipment, downhole tools, valves, heat exchangers, piping, reaction vessels |
Power Generation | Gas turbine hot section parts, combustors, transition ducts, heat shields |
Automotive | Turbocharger rotors, valves, exhaust manifolds |
Biomedical | Joint replacements, surgical instruments, dental implants |
The ability to additively manufacture intricate, mission-critical components using Inconel 718 has expanded its applications further. Parts with conformal cooling, lightweight lattice structures, and complex geometries can now be fabricated more easily.
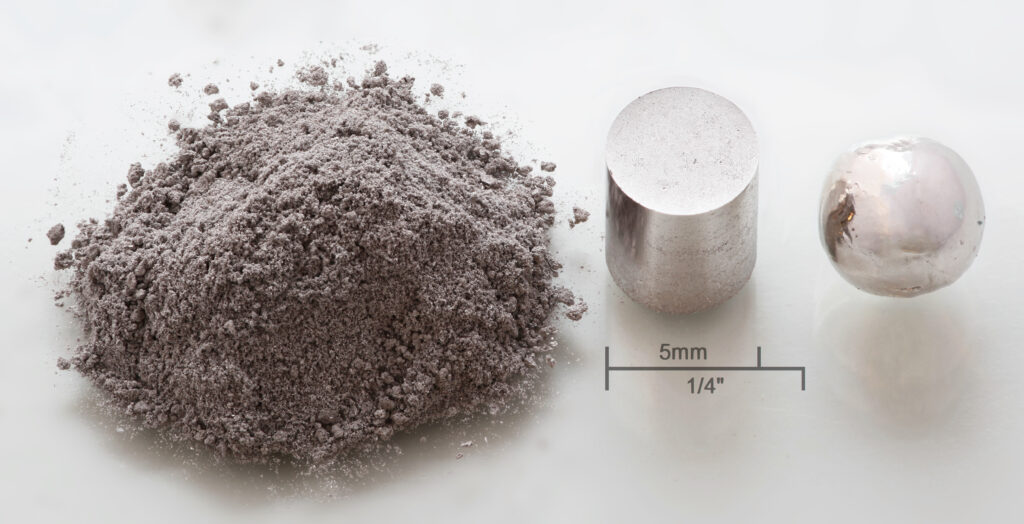
Types of Inconel 718 Powder
Inconel 718 powder is commercially available in several particle size distributions, shapes, and manufacturing processes.
Table 3: Types of Inconel 718 Powder
Type | Description | Characteristics |
---|---|---|
Gas Atomized | Made by inert gas atomization process | Spherical morphology, Smooth surface, Narrow particle size distribution 15-45 μm |
Water Atomized | Water atomization method | Irregular shape, Satellite particles, Wide distribution 5-150 μm |
Plasma Atomized | Plasma heating and gas atomization | Very spherical particles, Satellite free, 15-45 μm distribution |
Rotating Electrode Process | Electrode rotated at high speeds and melted by arc/plasma | Truncated spheroidal shape, Smooth surface, 15-106 μm distribution |
Hydride-Dehydride | Alloy is hydrogenated and dehydrogenated | Irregular shape, Porous surface, Wide size range |
Gas atomized and plasma atomized powders with high sphericity and smooth surface produce best additive manufacturing results. However, cost is a key factor in selecting the ideal Inconel 718 powder type.
Specifications of Inconel 718 Powder
Inconel 718 powder must conform to exacting standards for chemical composition, particle characteristics, microstructure, and quality checks.
Table 4: Specifications of Inconel 718 Powder
Parameter | Specification |
---|---|
Chemical Composition (wt%) | Ni 50-55%, Cr 17-21%, Nb 4.75-5.5%, Mo 2.8-3.3%, Ti 0.65-1.15%, Al 0.2-0.8%, C 0.08% max |
Particle shape | Spherical, spheroidal |
Apparent density | 4-5 g/cm3 |
Tap density | 7-8 g/cm3 |
Flowability | Angle of repose ≤ 30° |
Particle size | 15-45 μm |
Oxygen content | 0.1% max |
Nitrogen content | 0.1% max |
Microstructure | Homogeneous, few satellite particles |
Surface morphology | Smooth, little to no porosity |
Certification | ISO 9001, AS9100 |
Maintaining powder to these specifications ensures repeatable, high-quality printing results. Trusted global brands continuously conduct quality assurance testing to verify powder composition and characteristics.
Design Considerations for Inconel 718 Parts
Several design factors must be optimized when additive manufacturing components from Inconel 718 powder:
Table 5: Inconel 718 Part Design Considerations
Factor | Description |
---|---|
Part orientation | Optimal orientation for residual stress reduction and mechanical performance. |
Support structures | Use thin, optimized supports to minimize raw material use. |
Wall thickness | 1-2 mm range allows good properties and reduced weight. |
Surface finish | May require post-processing like machining, grinding, or shot peening. |
Hot isostatic pressing | Can close internal pores and enhance tensile strength. |
Heat treatment | Solution annealing and aging achieves optimal microstructure. |
Surface treatment | Apply suitable coatings or surfaces if wear/corrosion resistance needed. |
Simulating builds virtually, testing parameters, and working closely with experts is key to designing high-performance end-use parts with Inconel 718.
Standards and Codes for Inconel 718 Powder
Globally recognized standards for composition, testing methods, quality control, powder production, and part qualification govern Inconel 718 powder.
Table 6: Major Standards for Inconel 718 Powder
Standard | Description |
---|---|
AMS 5662 | Chemical composition and manufacturer testing |
AMS 5663 | Heat treatment procedures |
ASTM B899 | Analysis and chemical requirements |
ISO 9001 | Quality management system |
AS9100D | Aerospace quality management |
ASTM F3056 | Standard specification for additive manufacturing powder |
ASTM F3301 | Properties for laser powder bed fusion |
ASTM F3318 | Particle characterization, flow properties |
Compliance with standards assures users that the Inconel 718 powder and printed parts will perform reliably and safely in service.
Inconel 718 Powder Suppliers
Many leading metal powder manufacturers supply Inconel 718 powder for additive manufacturing and thermal spray processes.
Table 7: Major Suppliers of Inconel 718 Powder
Company | Powder Type | Particle Size | Key Properties |
---|---|---|---|
Sandvik | Gas atomized | 15-45 μm | High purity, Spherical, Smooth surface |
Carpenter Additive | Gas atomized | 15-53 μm | Excellent flowability |
Praxair | Atomized | 15-106 μm | Spherical, Low oxygen content |
AP&C | Plasma atomized | 10-45 μm | High dense prints, No satellites |
Höganäs | Gas atomized | 53-180 μm | Tight size distribution |
SLM Solutions | Gas atomized | 15-45 μm | Optimized for SLM process |
When selecting a supplier, consider technical expertise, industry reputation, range of atomization processes offered, particle size ranges, strict quality control, and metal powder safety.
How to Choose an Inconel 718 Powder Supplier
Follow these steps for choosing a suitable Inconel 718 powder supplier:
Table 8: How to Choose an Inconel 718 Powder Supplier
Step | Action |
---|---|
1 | Determine application, industry, part specifications |
2 | Research capabilities of various suppliers |
3 | Evaluate available powder varieties – atomization method, size range, morphology |
4 | Assess supplier experience, expertise level with Inconel alloys |
5 | Consider location, logistics, delivery times |
6 | Review conformance to major powder and printing standards |
7 | Compare pricing, minimum order quantities |
8 | Check supplier quality certifications like ISO 9001, AS9100D |
9 | Validate product quality data, inspection reports |
10 | Run trial prints with powder samples if possible |
Choosing an established industry leader helps ensure optimal powder quality and properties for superior end-use part performance.
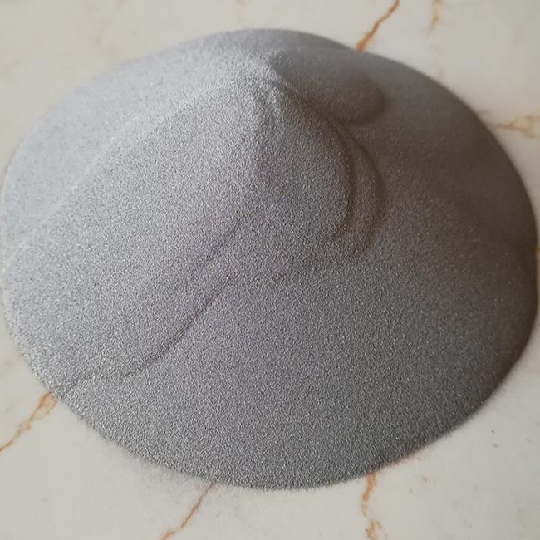
Installing and Maintaining Powder Bed Printers
Proper installation and maintenance is key to achieving consistent, high-quality 3D printed parts with Inconel 718 powder:
Table 9: Installation and Maintenance of Printers for Inconel 718
Activity | Description |
---|---|
Installation | Level printer, connect utilities, remove transport locks per manufacturer instructions |
Chamber purge | Use argon or nitrogen to reduce oxygen level below 25 ppm |
Leak check | Test for leaks to prevent contamination during builds |
Parameter optimization | Establish ideal laser power, speed, hatch spacing, layer thickness for material through test builds |
Storage and handling | Store powder in sealed containers under inert gas, minimize exposure to air and moisture |
Sieving | Regularly sieve powder to break up agglomerates and improve flowability |
Metal powder safety | Use protective equipment, minimize fire risks, dispose according to regulations |
System calibration | Validate laser power meter, optical focuser, powder layer thickness device periodically |
Maintenance | Follow OEM service schedule, replace filters, clean optics, lubricate moving parts |
Partnering with the printer manufacturer for installation, training, and preventative maintenance ensures maximum printer productivity and performance.
Operating Procedures for Inconel 718 Printing
Standard operating procedures for printing with Inconel 718 powder help achieve consistent, quality parts:
Table 10: Operating Procedures for Inconel 718 Printing
Stage | Procedure |
---|---|
Pre-print | Confirm powder quantity, seal containers, check build platform, nozzle, recoater blade condition |
Printing | Verify inert gas levels, preheat printer, load optimized parameters, setup monitoring cameras |
Powder spreading | Level powder bed, ensure uniform thickness across full area |
Post-print | Allow components and powder bed to cool fully before removing parts |
Powder recovery | Carefully sieve and collect un-melted powder for reuse |
Post-processing | Remove supports, shot peen, machine critical surfaces, apply finishing treatment if needed |
Part inspection | Check dimensions, internal structure with CT scans, verify mechanical properties through testing |
Documenting the entire workflow beginning from powder receipt helps identify improvements to the printing process over time for maximum efficiency.
Procuring and Managing Inconel 718 Powder Inventory
Efficiently managing Inconel 718 powder inventory and costs involves:
Table 11: Inconel 718 Powder Inventory Management
Activity | Description |
---|---|
Forecasting demand | Estimate upcoming projects and part quantities needed |
Optimizing orders | Order during lead time, factoring shipping, but minimize stock holding |
Secured storage | Store unopened containers in inert gas storage cabinet |
Inventory tracking | Log powder receipts, builds, reuse and disposals |
FIFO method | Use oldest powder first to avoid waste from expiry |
Monitoring stock | Replenish inventory when it approaches reorder point |
Recycling powder | Sieve and reuse un-melted powder up to 5-10 times |
Disposal | Follow regulations like 30 CFR 250.300 for spent metallic powder |
Order quantities based on a 6-12 month demand forecast balance low inventory costs and production flexibility.
Cost Analysis of Inconel 718 Powder
Inconel 718 powder is more expensive than stainless or tool steel powders due to material rarity and complex processing:
Table 12: Inconel 718 Powder Cost Analysis
Cost Component | Details |
---|---|
Material | Niobium content drives alloy raw material costs |
Atomization | Inert gas atomization has high capital and operating costs |
Additional processing | Plasma atomization, RH degassing, gas purification add costs |
Quality control | Maintaining powder specifications requires extensive testing |
Certification | ISO 9001 registration and ongoing audit fees |
Inventory and logistics | High value material ties up working capital, transport costs |
Prices range from $80-150 per kg depending on order size, supplier capabilities, and geographic region. Printer OEMs may offer discounted pricing for high volume contracts.
While expensive, Inconel 718 powder delivers superior performance justifying the higher price for critical applications.
Advantages and Limitations of Inconel 718 Powder
Some key advantages and limitations when using Inconel 718 powder include:
Table 13: Advantages and Limitations of Inconel 718 Powder
Advantages | Limitations |
---|---|
Excellent tensile, fatigue and creep resistance at high temperatures | Relatively high material cost |
Outstanding corrosion resistance in various environments | Higher density increases component weight |
High hardenability for greater strength | More difficult to fully dense prints requiring optimized parameters |
Perform well under prolonged stress and service | Limited suppliers compared to steels |
Retains room temperature properties up to 700°C | Higher tendency for cracking during printing |
Can be forged, welded and machined | Subject to natural aging, reducing shelf life |
Powder recyclability lowers costs | Susceptible to porosity issues in prints |
For critical high-performance applications where failure is not an option, Inconel 718’s superb capabilities justify the higher price and challenging printing process.
Frequently Asked Questions about Inconel 718 Powder
Q: What particle size range is optimal for printing Inconel 718 powder?
A: 15-45 microns is recommended, ensuring good powder bed density and flowability. Ultrafine <15 um powder can cause dust issues while large >45 um powder negatively affects resolution.
Q: Does Inconel 718 require hot isostatic pressing (HIP) post-processing?
A: HIP helps close internal pores and optimizes mechanical properties. But well-calibrated printers can achieve near full density without HIP.
Q: How many times can Inconel 718 powder be reused?
A: With proper handling and sieving, Inconel 718 powder can be reused 5-10 times before renewed. This improves cost-efficiency.
Q: Which provides better properties – wrought or printed Inconel 718?
A: Printed parts perform comparably or better than wrought properties after proper heat treatment and HIP. However surface finish is lower without machining.
Q: Can Inconel 718 parts be welded to themselves or other metals?
A: Yes, Inconel 718 has excellent weldability. Special nickel-alloy filler material must be used for best results.
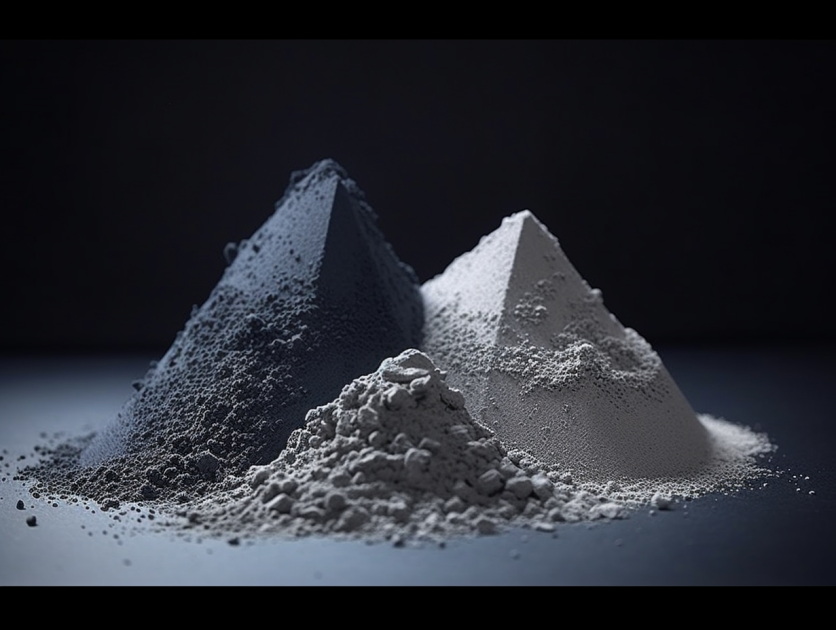
Conclusion
With its high strength across a wide temperature range, outstanding corrosion properties, and suitability for additive manufacturing, Inconel 718 has become a staple in aerospace, nuclear, and high performance applications. Using fine Inconel 718 powder allows intricate, optimized geometries to be fabricated through laser or e-beam printing.
However, properties and performance are highly dependent on source material quality, appropriate printer settings, rigorous quality control, and standardized post-processing. By choosing a reputable supplier, following best practices, and optimizing part design, users can leverage the full potential of this versatile nickel superalloy for their specific needs. The higher powder costs are justified for critical applications where failure is unacceptable.