Multi-Laserdruck revolutioniert die Fertigungslandschaft, insbesondere in der additiven Fertigung von Metallen (AM). Dieses Verfahren bietet zahlreiche Vorteile, wie z. B. hohe Bauraten, komplizierte Konstruktionen und eine effiziente Nutzung von Materialien. Die Qualität und Leistung der Endprodukte hängt jedoch von den im Prozess verwendeten Metallpulvern ab. Die Wahl des Pulvers ist von entscheidender Bedeutung - sie beeinflusst alles, von der Oberflächenbeschaffenheit bis hin zu den mechanischen Eigenschaften des gedruckten Teils. In diesem Leitfaden tauchen wir tief in die Welt der Pulver für den Multilaserdruck ein und stellen verschiedene Metallpulvermodelle, ihre Eigenschaften, Anwendungen und vieles mehr vor.
Überblick über Pulver für den Multilaserdruck
Der Begriff "Multilaserdruck" bezieht sich auf eine Untergruppe der additiven Fertigungstechniken für Metall, bei denen mehrere Laser gleichzeitig eingesetzt werden, um Metallpulver zu festen Teilen zu verschmelzen. Diese Methode wird häufig in Branchen wie der Luft- und Raumfahrt, der Automobilindustrie und der Medizintechnik eingesetzt, wo Präzision, Festigkeit und Materialeffizienz von größter Bedeutung sind. Die bei diesen Verfahren verwendeten Metallpulver sind in der Regel sehr feinkörnig und müssen strenge Kriterien erfüllen, um eine gleichbleibende Qualität zu gewährleisten.
Hauptmerkmale von Metallpulvern für den Multilaserdruck:
- Partikelgröße: Liegt in der Regel zwischen 10-50 Mikrometer.
- Sphärizität: Eine hohe Sphärizität ist entscheidend für eine gute Fließfähigkeit und eine gleichmäßige Schichtung.
- Reinheit: Pulver müssen hochrein sein, mit einem minimalen Sauerstoff- und Stickstoffgehalt.
- Materialzusammensetzung: Je nach Anwendung werden unterschiedliche Legierungen verwendet.
Zu den häufig verwendeten Metallpulvern gehören:
- Nichtrostende Stähle (z. B. 316L, 17-4 PH)
- Titanlegierungen (z. B. Ti6Al4V)
- Aluminiumlegierungen (z. B. AlSi10Mg)
- Superlegierungen auf Nickelbasis (z. B. Inconel 718)
- Kobalt-Chrom-Legierungen
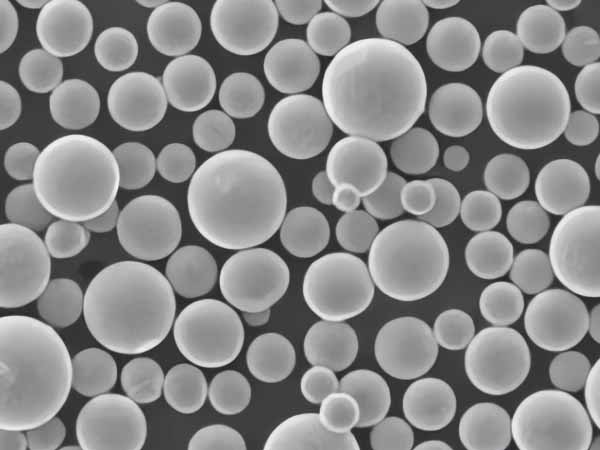
Zusammensetzung von Pulvern für Multi-Laser-Druck
Die Zusammensetzung von Metallpulvern ist ein grundlegender Aspekt, der ihr Verhalten während des Druckprozesses und die Eigenschaften des fertigen Teils bestimmt. Verschiedene Metallpulver werden so entwickelt, dass sie bestimmte Anforderungen in Bezug auf Festigkeit, Korrosionsbeständigkeit und thermische Stabilität erfüllen.
Gängige Metallpulver-Zusammensetzungen:
Metall-Pulver | Zusammensetzung | Eigenschaften |
---|---|---|
316L-Edelstahl | Eisen (Fe), Chrom (Cr), Nickel (Ni), Molybdän (Mo), Mangan (Mn) | Ausgezeichnete Korrosionsbeständigkeit, gute mechanische Eigenschaften, häufig in medizinischen Anwendungen verwendet |
17-4 PH Edelstahl | Eisen (Fe), Chrom (Cr), Nickel (Ni), Kupfer (Cu), Niobium (Nb) | Hohe Festigkeit, gute Korrosionsbeständigkeit, ausscheidungsgehärtet |
Ti6Al4V (Titan-Legierung) | Titan (Ti), Aluminium (Al), Vanadium (V) | Hohes Verhältnis von Festigkeit zu Gewicht, ausgezeichnete Korrosionsbeständigkeit, biokompatibel |
AlSi10Mg (Aluminium-Legierung) | Aluminium (Al), Silizium (Si), Magnesium (Mg) | Leichtes Gewicht, gute Wärmeleitfähigkeit, hohe Festigkeit |
Inconel 718 (Nickel-Superlegierung) | Nickel (Ni), Chrom (Cr), Eisen (Fe), Molybdän (Mo), Niob (Nb), Titan (Ti), Aluminium (Al) | Ausgezeichnete Hochtemperaturfestigkeit, Korrosionsbeständigkeit |
CoCr (Kobalt-Chrom-Legierung) | Kobalt (Co), Chrom (Cr), Molybdän (Mo), Nickel (Ni) | Hohe Verschleißfestigkeit, biokompatibel, ausgezeichnete Festigkeit bei hohen Temperaturen |
Martensitaushärtender Stahl | Eisen (Fe), Nickel (Ni), Kobalt (Co), Molybdän (Mo), Titan (Ti) | Sehr hohe Festigkeit, gute Zähigkeit, Einsatz in der Luft- und Raumfahrt und im Werkzeugbau |
Hastelloy X (Nickellegierung) | Nickel (Ni), Molybdän (Mo), Chrom (Cr), Eisen (Fe) | Hervorragende Hochtemperaturfestigkeit, gute Oxidationsbeständigkeit |
CuNi2SiCr (Kupferlegierung) | Kupfer (Cu), Nickel (Ni), Silizium (Si), Chrom (Cr) | Hohe elektrische Leitfähigkeit, gute mechanische Eigenschaften |
Werkzeugstahl (z. B. A2, D2) | Eisen (Fe), Kohlenstoff (C), Chrom (Cr), Molybdän (Mo), Vanadium (V) | Hohe Härte, Verschleißfestigkeit, Verwendung im Werkzeug- und Formenbau |
Merkmale von Pulvern für den Multilaserdruck
Die Leistung von Metallpulvern beim Multilaserdruck wird durch verschiedene Merkmale wie Partikelgrößenverteilung, Morphologie, Fließfähigkeit und Reinheit beeinflusst. Diese Faktoren wirken sich direkt auf die Druckqualität, die mechanischen Eigenschaften der gedruckten Teile und die Effizienz des Gesamtprozesses aus.
Wesentliche Merkmale:
Charakteristisch | Beschreibung | Auswirkungen auf den Druck |
---|---|---|
Partikelgrößenverteilung | Normalerweise im Bereich von 10-50 Mikron. Feine Pulver führen zu einer besseren Auflösung, während gröbere Pulver schnellere Aufbauraten bieten. | Beeinflusst die Schichtdicke, die Oberflächenbeschaffenheit und die mechanischen Eigenschaften. |
Morphologie | Sphärische Partikel werden wegen ihrer besseren Fließfähigkeit und Packungsdichte bevorzugt. | Gewährleistet eine gleichmäßige Schichtung und verringert das Risiko von Fehlern. |
Fließfähigkeit | Die Pulver müssen frei fließen können, damit sie beim Wiederbeschichten gleichmäßige Schichten bilden. | Eine schlechte Fließfähigkeit kann zu Mängeln wie Porosität und unvollständiger Verschmelzung führen. |
Reinheit | Entscheidend ist eine hohe Reinheit mit minimaler Verunreinigung durch Sauerstoff, Stickstoff oder andere Elemente. | Verunreinigungen können zu Schwachstellen, verminderten mechanischen Eigenschaften und schlechter Korrosionsbeständigkeit führen. |
Sphärizität | Eine hohe Sphärizität verbessert die Fließfähigkeit und die Packungsdichte des Pulvers. | Verbessert die Gleichmäßigkeit des Pulverbetts, was zu einer höheren Druckqualität führt. |
Schüttdichte | Die Schüttdichte des Pulvers beeinflusst die Menge des Materials, die in ein bestimmtes Volumen gepackt werden kann. | Beeinflusst die Effizienz des Pulververbrauchs und das Gewicht des Endprodukts. |
Anwendungen von Pulvern für den Multilaserdruck
Die Vielseitigkeit des Multilaserdrucks und die breite Palette der verfügbaren Metallpulver machen diese Technologie für verschiedene Branchen geeignet. Jede Anwendung erfordert spezifische Materialeigenschaften, von hoher Festigkeit und Verschleißfestigkeit bis hin zu Biokompatibilität und Wärmeleitfähigkeit.
Industrieanwendungen:
Industrie | Anmeldung | Bevorzugte Metallpulver |
---|---|---|
Luft- und Raumfahrt | Leichte Strukturkomponenten, Turbinenschaufeln und Wärmetauscher. | Ti6Al4V, Inconel 718, Hastelloy X |
Automobilindustrie | Motorkomponenten, leichte Strukturen und hitzebeständige Teile. | AlSi10Mg, 316L-Edelstahl, Maraging-Stahl |
Medizinische | Implantate, Prothesen und chirurgische Instrumente, die Biokompatibilität und Korrosionsbeständigkeit erfordern. | Ti6Al4V, CoCr, 316L Edelstahl |
Öl und Gas | Komponenten für raue Umgebungen, die eine hohe Korrosions- und Verschleißfestigkeit erfordern. | Inconel 718, Hastelloy X, 17-4 PH Edelstahl |
Werkzeuge und Gussformen | Hochfeste Werkzeuge und Formen mit präzisen Eigenschaften und langer Lebensdauer. | Werkzeugstahl, martensitaushärtender Stahl, rostfreier Stahl 17-4 PH |
Energie | Teile für Turbinen, Generatoren und andere Energieerzeugungsanlagen. | Inconel 718, Hastelloy X, CoCr |
Elektronik | Wärmesenken, Leiterbahnen und andere Komponenten, die gute thermische und elektrische Eigenschaften erfordern. | CuNi2SiCr, AlSi10Mg, 316L Edelstahl |
Schmuck | Individuelles, kompliziertes Design mit hohem ästhetischen Wert. | CoCr, Ti6Al4V, 316L Edelstahl |
Verteidigung | Hochleistungsteile für Militärfahrzeuge, Waffen und Schutzausrüstung. | Inconel 718, Maraging-Stahl, Ti6Al4V |
-
CM247LC Pulver | Nickellegierungspulver
-
0# Reines Nickelpulver
-
Pulver aus NiCoCrAlY-Legierungen
-
Rene 142 Legierung-Rene Pulver
-
Haynes 25 Haynes-Pulver
-
Bestes Hastelloy C-22-Pulver-Hochtemperaturlegierungspulver für den 3D-Druck
-
Bestes Hastelloy C-276-Pulver-Hochtemperaturlegierungspulver für den 3D-Druck
-
Bestes Hastelloy N-Pulver-Hochtemperaturlegierungspulver für den 3D-Druck
-
Bestes Hastelloy B-Pulver丨Hochtemperaturlegierungspulver für den 3D-Druck
Spezifikationen, Größen, Güteklassen und Normen
Bei der Auswahl von Metallpulvern für MultilaserdruckBei der Auswahl des Pulvers ist es wichtig, die für das Pulver geltenden Spezifikationen, Größen, Qualitäten und Normen zu berücksichtigen. Diese Faktoren gewährleisten, dass das Pulver die Anforderungen für die vorgesehene Anwendung erfüllt und den Industrienormen entspricht.
Spezifikationen und Normen:
Metall-Pulver | Spezifikation/Standard | Partikelgrößenbereich | Klasse |
---|---|---|---|
316L-Edelstahl | ASTM F138, F139, F3184 | 15-45 Mikrometer | Medizinische Qualität, industrielle Qualität |
17-4 PH Edelstahl | ASTM A564, A693 | 10-50 Mikrometer | Niederschlag gehärtet |
Ti6Al4V | ASTM F1472, F2924 | 20-45 Mikrometer | Klasse 5 (ELI) |
AlSi10Mg | ISO 9001, ASTM F3318 | 20-63 Mikrometer | AM-grade, hochrein |
Inconel 718 | ASTM B637, AMS 5662 | 15-53 Mikrometer | Superlegierung |
Martensitaushärtender Stahl | AMS 6514, ASTM A646 | 15-45 Mikrometer | 18Ni-300 |
Hastelloy X | ASTM B435, AMS 5754 | 15-53 Mikrometer | Hochwarmfeste Legierung |
CuNi2SiCr | DIN 17666, ASTM B422 | 20-63 Mikrometer | Hoher Leitfähigkeitsgrad |
Werkzeugstahl | ASTM A681, ISO 4957 | 15-45 Mikrometer | A2, D2 |
Lieferanten und Preisangaben
Der Markt für Metallpulver für den Multilaserdruck ist riesig, und es gibt zahlreiche Anbieter, die eine breite Palette von Produkten anbieten. Die Preise können je nach Material, Partikelgröße, Reinheit und Anbieter stark variieren.
Lieferanten und Preisgestaltung:
Anbieter | Verfügbare Metallpulver | Preisgestaltung (pro kg) | Kommentare |
---|---|---|---|
LPW-Technologie | Rostfreier Stahl, Titan, Aluminium, Inconel | $150 – $600 | Hochwertige Pulver, maßgeschneiderte Lösungen |
Zimmerer-Zusatzstoff | Rostfreier Stahl, Titan, Nickellegierungen, Kobalt-Chrom | $200 – $800 | Breite Palette an Legierungsoptionen, weltweiter Anbieter |
Sandvik Fischadler | Titan, Aluminium, Werkzeugstähle, rostfreier Stahl | $180 – $750 | Gleichbleibende Qualität, umfassende F&E-Kapazitäten |
AP&C (GE-Zusatzstoff) | Titan, Aluminium, Nickellegierungen | $250 – $1000 | Spezialisiert auf hochwertige, kugelförmige Pulver |
Höganäs AB | Rostfreier Stahl, Werkzeugstähle, Kobalt-Chrom | $150 – $500 | Starker Fokus auf Nachhaltigkeit und Innovation |
Tekna | Titan, Aluminium, Nickellegierungen | $200 – $900 | Fortschrittlicher Plasma-Zerstäubungsprozess |
Aubert & Duval | Superlegierungen auf Nickelbasis, Rostfreier Stahl, Titan | $300 – $1000 | Hochwertige, für die Luft- und Raumfahrt geeignete Puder |
EOS | Titan, Aluminium, Nickellegierungen, Kobalt-Chrom | $250 – $1200 | Hochleistungspulver optimiert für EOS-Maschinen |
CarTech | Martensitaushärtender Stahl, Nickellegierungen, Rostfreier Stahl | $200 – $900 | Spezialisiert auf hochfeste Legierungen |
Ametek | Titan, Nickellegierungen, rostfreier Stahl | $180 – $850 | Umfassendes Angebot an Metallpulvern für verschiedene Branchen |
Vorteile und Beschränkungen von Metallpulvern für Multi-Laser-Druck
Die Wahl des richtigen Metallpulvers ist entscheidend für die Optimierung des Multi-Laser-Druckverfahrens. Jeder Pulvertyp hat seine eigenen Vorteile und Einschränkungen, die sich auf die Gesamtleistung der gedruckten Teile auswirken können.
Vergleich der Vorteile und Grenzen:
Metall-Pulver | Vorteile | Beschränkungen |
---|---|---|
316L-Edelstahl | Ausgezeichnete Korrosionsbeständigkeit, gute mechanische Eigenschaften, weithin verfügbar | Geringere Festigkeit im Vergleich zu anderen Legierungen wie 17-4 PH |
17-4 PH Edelstahl | Hohe Festigkeit, gute Korrosionsbeständigkeit, ausscheidungsgehärtet | Teurer als 316L, komplexe Wärmebehandlung erforderlich |
Ti6Al4V | Hohes Verhältnis von Festigkeit zu Gewicht, ausgezeichnete Korrosionsbeständigkeit, biokompatibel | Hohe Kosten, schwieriges Druckverfahren aufgrund der Sauerstoffempfindlichkeit |
AlSi10Mg | Leichtes Gewicht, gute Wärmeleitfähigkeit, hohe Festigkeit | Geringere Ermüdungsfestigkeit im Vergleich zu Titanlegierungen |
Inconel 718 | Ausgezeichnete Hochtemperaturfestigkeit, Korrosionsbeständigkeit | Teuer, schwierig nachzudrucken |
CoCr | Hohe Verschleißfestigkeit, biokompatibel, ausgezeichnete Festigkeit bei hohen Temperaturen | Sehr teuer, schwierig zu verarbeiten |
Martensitaushärtender Stahl | Sehr hohe Festigkeit, gute Zähigkeit, Einsatz in der Luft- und Raumfahrt und im Werkzeugbau | Erfordert Alterungsbehandlung, begrenzte Korrosionsbeständigkeit |
Hastelloy X | Hervorragende Hochtemperaturfestigkeit, gute Oxidationsbeständigkeit | Extrem teuer, wegen des hohen Nickelgehalts schwer zu drucken |
CuNi2SiCr | Hohe elektrische Leitfähigkeit, gute mechanische Eigenschaften | Begrenzte Festigkeit, nicht für Hochtemperaturanwendungen geeignet |
Werkzeugstahl | Hohe Härte, Verschleißfestigkeit, Verwendung im Werkzeug- und Formenbau | Neigt bei unsachgemäßer Verarbeitung zur Rissbildung, erfordert Wärmebehandlung nach dem Druck |
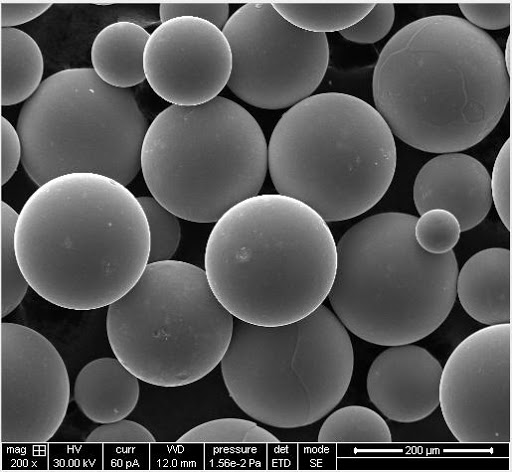
FAQs
Frage | Antwort |
---|---|
Welches ist das beste Metallpulver für Luft- und Raumfahrtanwendungen? | Ti6Al4V und Inconel 718 werden wegen ihrer hohen Festigkeit und Korrosionsbeständigkeit häufig in der Luft- und Raumfahrt verwendet. |
Kann der Multilaserdruck mit Aluminiumpulvern verwendet werden? | Ja, AlSi10Mg ist ein gängiges Pulver aus einer Aluminiumlegierung, das im Multilaserdruck verwendet wird, insbesondere für leichte Strukturen. |
Wie wirkt sich die Partikelgröße auf die Qualität der gedruckten Teile aus? | Feinere Partikel führen zu einer besseren Auflösung und Oberflächengüte, während gröbere Partikel die Baugeschwindigkeit erhöhen können. |
Was sind die Herausforderungen bei der Verwendung von Titanpulvern? | Titan-Pulver wie Ti6Al4V sind sauerstoffempfindlich, so dass es schwierig ist, sie ohne Verunreinigung zu verarbeiten. |
Welches Pulver ist am besten für medizinische Implantate geeignet? | Ti6Al4V und CoCr werden aufgrund ihrer Biokompatibilität und Korrosionsbeständigkeit für medizinische Implantate bevorzugt. |
Sind Metallpulver für den Multilaserdruck teuer? | Ja, die Kosten können von $150 bis über $1200 pro Kilogramm reichen, je nach Material und Reinheit. |
Ist nach dem Druck mit Metallpulvern eine Nachbearbeitung erforderlich? | Häufig, ja. Nachbearbeitungen wie Wärmebehandlung oder maschinelle Bearbeitung können erforderlich sein, um die gewünschten Eigenschaften zu erreichen. |
Wie wähle ich das richtige Pulver für meine Anwendung? | Berücksichtigen Sie die erforderlichen Eigenschaften wie Festigkeit, Korrosionsbeständigkeit und thermische Stabilität und stimmen Sie diese mit der Zusammensetzung des Metallpulvers ab. |
Kann ich Metallpulver im Multilaserdruck wiederverwenden? | Ja, aber das Pulver sollte vor der Wiederverwendung gesiebt und auf Verunreinigungen untersucht werden, um eine gleichbleibende Qualität zu gewährleisten. |
Welche Sicherheitsvorkehrungen sind beim Umgang mit Metallpulvern erforderlich? | Richtige Belüftung, persönliche Schutzausrüstung (PSA) und Handhabungsprotokolle sind unerlässlich, um die Gefahr des Einatmens und der Staubexplosion zu vermeiden. |
Schlussfolgerung
Metallpulver für Multilaserdruck spielen eine entscheidende Rolle bei der Bestimmung der Qualität, Leistung und Kosteneffizienz der endgültigen gedruckten Teile. Bei der großen Auswahl an Materialien, die von rostfreien Stählen und Titanlegierungen bis hin zu Superlegierungen und Spezialgüten reicht, muss bei der Auswahl des richtigen Pulvers sorgfältig auf die spezifischen Anforderungen der jeweiligen Anwendung geachtet werden. Wenn die Hersteller die Zusammensetzung, die Eigenschaften und die Anwendungen dieser Pulver kennen, können sie ihre Prozesse optimieren, die Kosten senken und hervorragende Ergebnisse erzielen.
Egal, ob Sie in der Luft- und Raumfahrt, der Automobilindustrie, der Medizintechnik oder einer anderen Branche tätig sind, die die additive Fertigung von Metallen nutzt, dieser Leitfaden dient als umfassende Ressource zur Navigation in der komplexen Landschaft der Pulver für den Multilaserdruck.