AlSi10Mg-Pulver ist ein graues Pulver und findet breite Anwendung im 3D-Druck und in der additiven Fertigung in den Bereichen Luft- und Raumfahrt, Automobil, Industrie und Medizin.
Das Laserschmelzverfahren ist eine Art der additiven Laser-Metall-Fertigungstechnologie, die sowohl mit Draht als auch mit Pulver betrieben werden kann. Sein Vorteil ist, dass dichte Struktur, feine Körner, einheitliche Zusammensetzung und hervorragende Leistung, und auch für die Reparatur und Cladding angewendet werden. Derzeit ist die Forschung im Bereich des Laserschmelzens von Titanlegierungen, Superlegierungen und anderen Legierungen gut vorangekommen, aber die Forschung im Bereich des Laserschmelzens von Aluminiumlegierungen ist aufgrund der hohen Wärmeleitfähigkeit und der hohen Laserreflexion von Aluminiumlegierungen noch sehr begrenzt.
Die Forschungs- und Entwicklungsabteilung von Truer hat einige Untersuchungen zur ausgewählten Laserschmelztechnologie (SLM) von AlSi10Mg durchgeführt, und die Ergebnisse zeigten, dass die Zugfestigkeit von SLM-AlSi10Mg-Teilen 300 MPa erreichen kann, nach der Wärmebehandlung sogar 406 MPa. Und einige Wissenschaftler fanden die Laser-Ressource hat einen großen Einfluss auf die Eigenschaften von AlSi10Mg abgeschiedenen Teile.
Die chemische Zusammensetzung und die Partikelgröße (45-105 um) des in dieser Studie von Truer hergestellten AlSi10Mg-Pulvers sind in Tabelle 1 aufgeführt. Und das REM-Foto ist in Abb. 1 zu sehen.
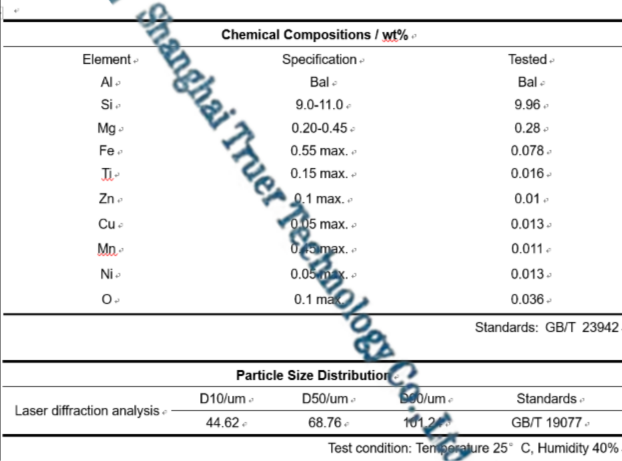
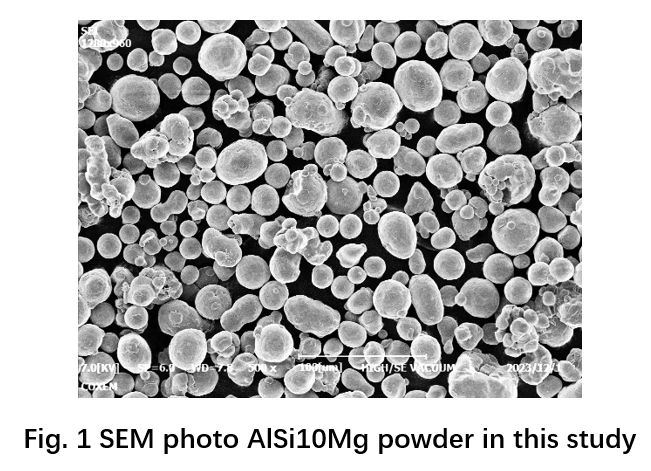
Das in diesem Experiment verwendete Laserschmelzbeschichtungssystem besteht aus einem IPG-Faserlaser, einer GTV-Pulverzuführung und einer Argon-Füllkammer. Im Prozess des Laserschmelzens und -auftragens beträgt der fokussierte Punkt 5 mm und der Durchmesser des defokussierten Punktes etwa 0,6 mm. Die Leistung des Testlasers betrug 920 W, die Scanrichtung war unidirektional, die Scangeschwindigkeit betrug 1,2 m/min, die Pulverbeschickungsgeschwindigkeit 3,6 g/min, und die Beschichtungshöhe jeder Schicht betrug 0,42 mm. Es wurde eine einzelne Wandprobe mit einer Dicke von 2 mm hergestellt. Anschließend wurden die Porosität und die mechanischen Eigenschaften der Teile analysiert.
Abb. 2 zeigt die Abmessungen des Probekörpers für die Prüfung der mechanischen Eigenschaften.
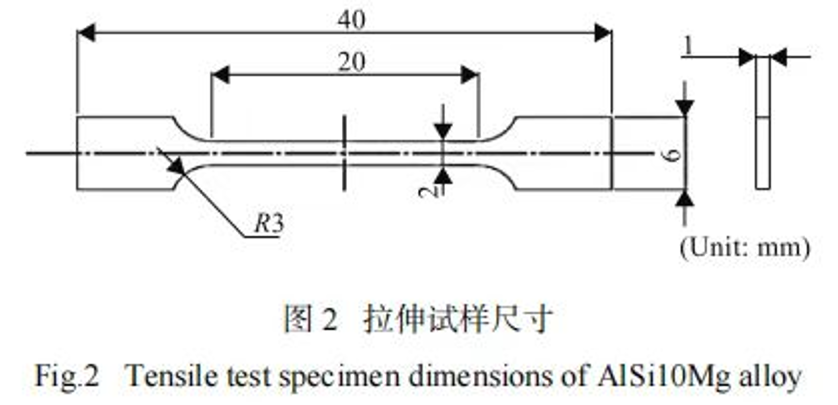
Die Dichte des Probekörpers wird nach der archimedischen Methode mit 2,66 g/cm3 bestimmt, während die Dichte der AlSi10Mg-Legierung im Gusszustand 2,68 g/cm3 beträgt und sich auf 99,3% des Gussstücks bezieht.
Bei diesem Test war ein gewisser Sauerstoffgehalt in der mit Argon gefüllten Kammer beteiligt. So zeigte es Mikrostruktur einige Porosität in Abb. 3 gezeigt.
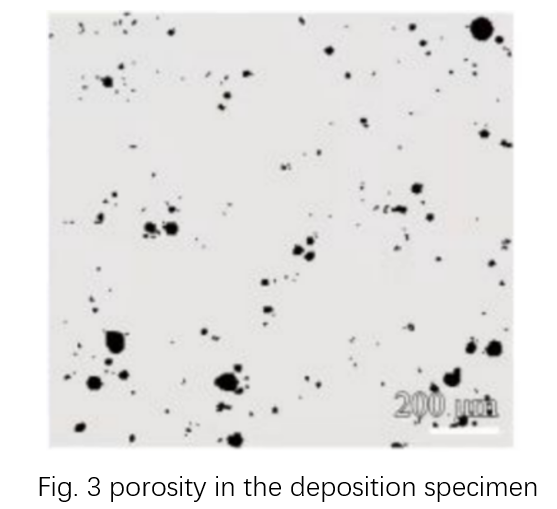
Im Zugversuch wurde die Zugkurve wie in Abb. 4 dargestellt ermittelt. Die Zugfestigkeit beträgt 248 MPa und die Dehnung 6,2%.
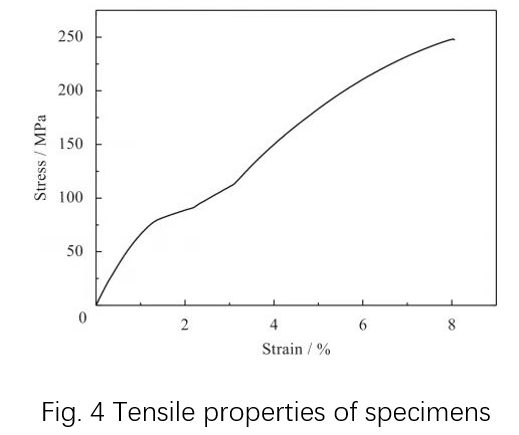
Die Bruchmorphologie der Zugprobe ist in Abb. 5 dargestellt. Es ist zu erkennen, dass die Rissausbreitung dazu neigt, sich entlang der dünnen Wand zwischen der Porosität und der Porosität auszudehnen.
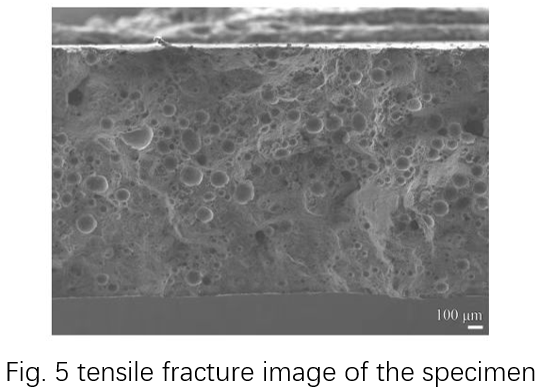
Daher wird empfohlen, die additive Fertigung von Aluminiumlegierungen mittels Laserschmelzen in einer mit Argon gefüllten Kammer durchzuführen, um die Kontrolle der inneren Poren zu gewährleisten, was die Zugfestigkeit der abgeschiedenen Teile aus AlSi10Mg verbessert.
Einige Wissenschaftler kamen zu dem Schluss, dass der Hauptgrund für die hohen mechanischen Eigenschaften von AlSi10Mg-Abscheidungsteilen darin liegt, dass sich im Abscheidungszustand sehr feine sekundäre Alpha-Al-Dendriten gebildet haben.
Daraus lässt sich schließen, dass eine strenge Kontrolle des Sauerstoffgehalts in der Kammer der Schlüssel zur Verbesserung der mechanischen Eigenschaften von AlSi10Mg-Teilen aus der additiven Fertigung mittels Laserschmelzen ist.