Im Bereich der High-End-Fertigung hat sich M42-Legierungspulver aufgrund seiner ausgezeichneten Warmhärte, Verschleißfestigkeit und Hochtemperaturfestigkeit zum wichtigsten Werkstoff für Schneidwerkzeuge, Luft- und Raumfahrtkomponenten und Präzisionsformen entwickelt. Seine Leistungsfähigkeit hängt jedoch stark von der Zusammensetzung und der Prozesssteuerung ab. Unter anderem wirkt sich die Zugabemenge von WC (Wolframkarbid) als Schlüsselvariable direkt auf die Mikrostruktur und die Eigenschaften aus. In diesem Artikel wurde die Auswirkung des WC-Zusatzes auf die Leistung von M42-Legierungspulver untersucht und seine Schlüsselrolle bei der Wärmebehandlung, dem Sinterprozess und dem Design von Verbundwerkstoffen aufgezeigt.
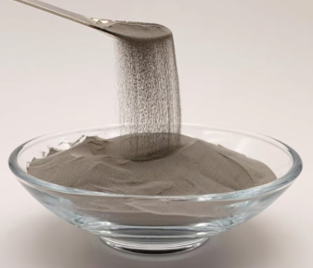
Auswirkung des WC-Zusatzes auf die Härte von M42-Pulver
Wie gesintert:
Die Auswirkung des WC-Zusatzes auf die Härte nach dem Sintern zeigt einen Trend, der zunächst abnimmt und dann zunimmt. Bei einem WC-Gehalt von 5% sinkt die Härte um etwa 9,83% (niedriger als bei M42 ohne WC-Zusatz); steigt der WC-Gehalt auf 10%, erhöht sich die Härte deutlich um 13,2 HRC und übertrifft die Härte von M42-Pulver ohne WC-Zusatz.
Wärmebehandelt:
Die gesinterten Teile werden durch 1180℃ Abschrecken und 560℃ Anlassen wärmebehandelt, die Härte erreicht einen Maximalwert von 65,1 HRC, wenn der WC-Zusatz 10% beträgt, was darauf hindeutet, dass die Wärmebehandlung die Wirkung von WC auf die Verbesserung der Härte effektiv optimieren kann.
Entwicklung der Mikrostruktur
Vertrieb von Hartmetall:
Bei niedrigem WC-Gehalt (2%) sind die Karbide in der Matrix reduziert, aber es treten Netzwerkkarbide auf; bei mittlerem WC-Gehalt (5%) sind die Karbide an den Korngrenzen konzentriert, was zu Aggregation und Wachstum führt; bei hohem WC-Gehalt (10%) sind die Karbide weiter aggregiert, aber sekundäre Karbide (wie M7C3) werden nach der Wärmebehandlung ausgefällt und bilden eine Dispersionsverfestigung.
REM-Aufnahmen von WC/M42-Verbundwerkstoffen mit verschiedenen WC% |
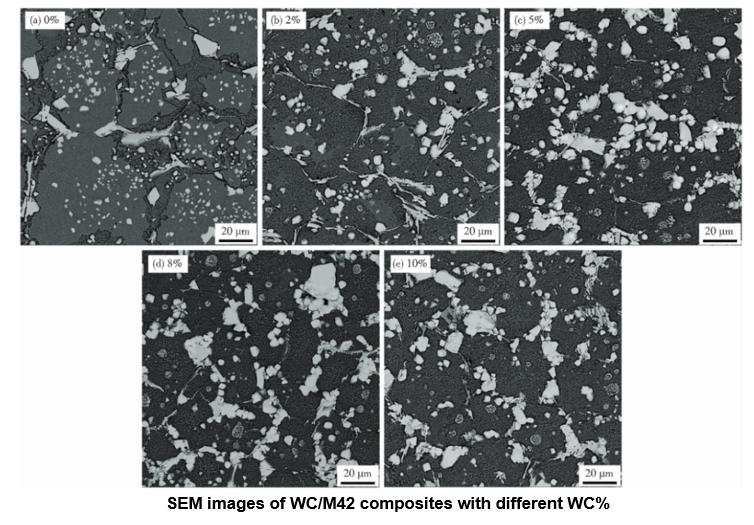
Dichte der Sinterung:
Mit zunehmender Menge an zugesetztem WC (0-10%) steigt die relative Dichte des gesinterten Verbundwerkstoffs zunächst an und neigt dann zur Stabilisierung.
Dichte von WC/M42-Verbundwerkstoffen mit unterschiedlichem WC% bei verschiedenen Sintertemperaturen |
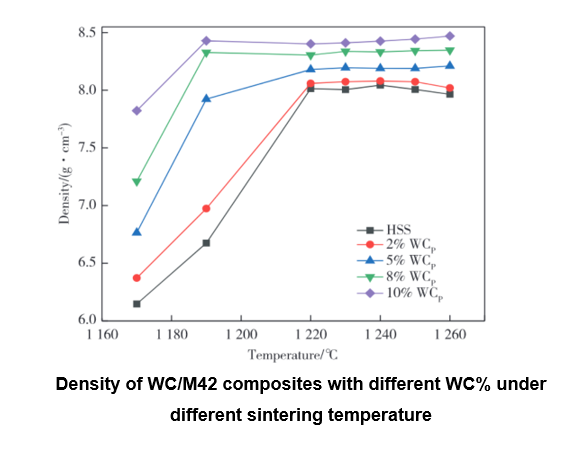
Schlussfolgerung:
Bei einem WC-Zusatz von 8-10% eignen sich WC/M42-Verbundwerkstoffe für Anwendungen mit hohen Anforderungen an Härte und Verschleißfestigkeit (z. B. Fräser und Bohrer), aber Festigkeit und Zähigkeit müssen durch Wärmebehandlung optimiert werden.
Wenn der WC-Zusatz weniger als 8% beträgt, kann er die Ausdehnung der spröden Phase, die durch die Karbidaggregation verursacht wird, vermeiden und gewährleistet eine hohe Temperaturfestigkeit und Stabilität. Es ist besser geeignet für die Anwendung bei hohen Temperaturen.
Künftige Trends:
Entwicklung eines WC/TiC-M42-Gradientenmaterials für ein ausgewogenes Verhältnis zwischen Härte und Zähigkeit.
Optimieren Sie die Parameter des Kugelmahlens/Sinterns, sagen Sie die Karbidgröße und -verteilung voraus und erreichen Sie eine präzise Kontrolle der Karbidgröße und -verteilung.
Entwicklung von WC/M42-Verbundpulvern speziell für die additive Fertigung.
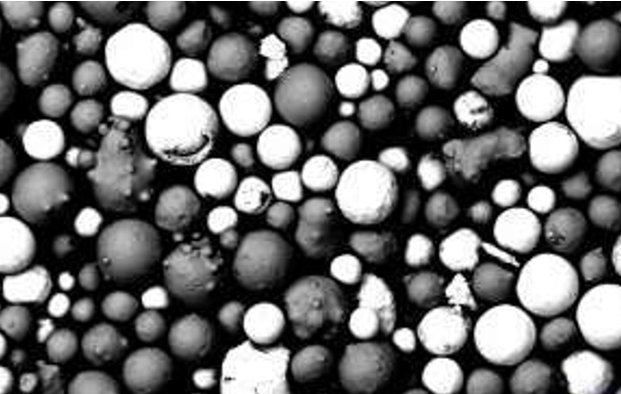