Introduction
What is metal 3D printing?
Metal 3D printing, also known as additive manufacturing, is a revolutionary technology that allows for the creation of complex metal parts through the layer-by-layer deposition of metal powder. Unlike traditional manufacturing methods, metal 3D printing offers numerous advantages, such as the ability to produce highly intricate designs, reduce material waste, and achieve faster production times. This innovative process has opened up new possibilities in various industries, including aerospace, automotive, and healthcare, where the demand for lightweight, high-performance metal components is on the rise.
History of metal 3D printing
Metal 3D printing has a rich history that dates back to the 1980s. The first metal 3D printer was developed by researchers at the Massachusetts Institute of Technology (MIT). Since then, the technology has evolved significantly, with advancements in materials, printing techniques, and machine capabilities. Metal 3D printing has revolutionized various industries, including aerospace, automotive, and healthcare, by enabling the production of complex and customized metal parts with high precision and efficiency. Today, metal 3D printing with powder materials offers numerous advantages, such as reduced material waste, faster production times, and the ability to create intricate designs that were previously impossible with traditional manufacturing methods. As the technology continues to advance, the potential applications of metal 3D printing are only expected to grow, further pushing the boundaries of what is possible in the world of manufacturing.
Advancements in metal 3D printing technology
Metal 3D printing has seen significant advancements in technology, particularly with the use of powder materials. This innovative approach allows for the creation of complex and intricate metal parts with high precision and accuracy. One of the main advantages of metal 3D printing with powder materials is the ability to produce parts with superior strength and durability. Additionally, this technology offers increased design flexibility, as it enables the production of geometries that are impossible to achieve through traditional manufacturing methods. Furthermore, metal 3D printing with powder materials reduces material waste and allows for cost-effective production, making it an attractive option for various industries such as aerospace, automotive, and healthcare. With continuous advancements in this field, metal 3D printing with powder materials is revolutionizing the manufacturing industry and opening up new possibilities for the production of complex metal components.
Benefits of Metal 3D Printing
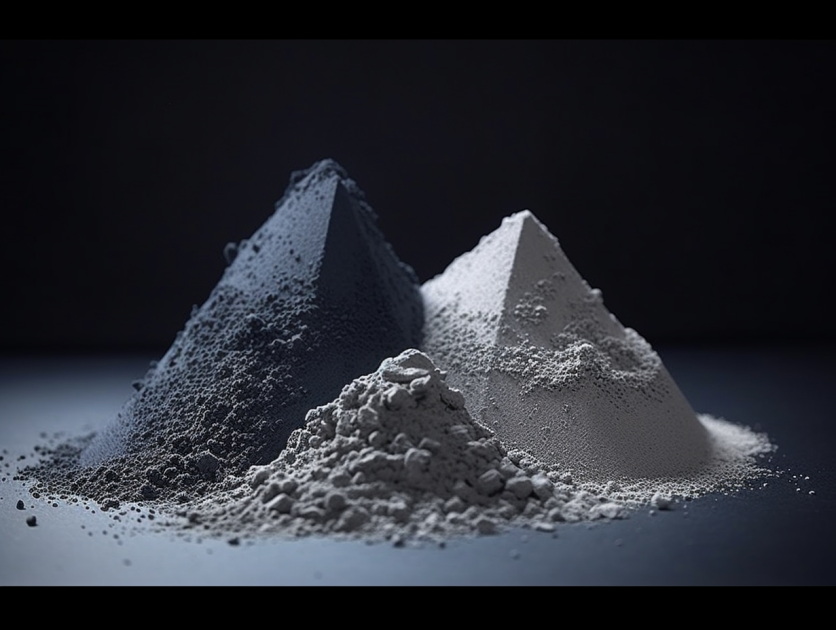
Design freedom
Design freedom is one of the key advantages of metal 3D printing with powder materials. Unlike traditional manufacturing methods, such as casting or machining, 3D printing allows for complex and intricate designs to be created with ease. This opens up a world of possibilities for engineers and designers, as they are no longer limited by the constraints of traditional manufacturing processes. With metal 3D printing, it is possible to create parts with intricate geometries, internal channels, and lightweight structures that would be impossible or extremely difficult to achieve using other methods. This level of design freedom not only enables the production of highly customized and optimized parts but also reduces material waste and manufacturing time. Metal 3D printing with powder materials truly revolutionizes the way we think about design and manufacturing, pushing the boundaries of what is possible.
Reduced material waste
Metal 3D printing with powder materials offers numerous advantages, one of which is reduced material waste. Unlike traditional manufacturing methods, where excess material is often discarded, metal 3D printing allows for precise and efficient use of materials. The powder used in the printing process can be recycled, minimizing waste and saving costs. This not only benefits the environment but also makes metal 3D printing a more sustainable and cost-effective option. By reducing material waste, manufacturers can optimize their production processes and achieve higher levels of efficiency.
Complex geometries
Metal 3D printing with powder materials offers numerous advantages, especially when it comes to creating complex geometries. This technology allows for the production of intricate and intricate designs that would be difficult or even impossible to achieve with traditional manufacturing methods. The ability to print metal parts layer by layer enables the creation of intricate internal structures, intricate lattice designs, and complex shapes with ease. This opens up new possibilities for industries such as aerospace, automotive, and healthcare, where lightweight and complex components are in high demand. Metal 3D printing with powder materials is revolutionizing the way we manufacture and design products, pushing the boundaries of what is possible in terms of shape complexity and functionality.
Applications of Metal 3D Printing
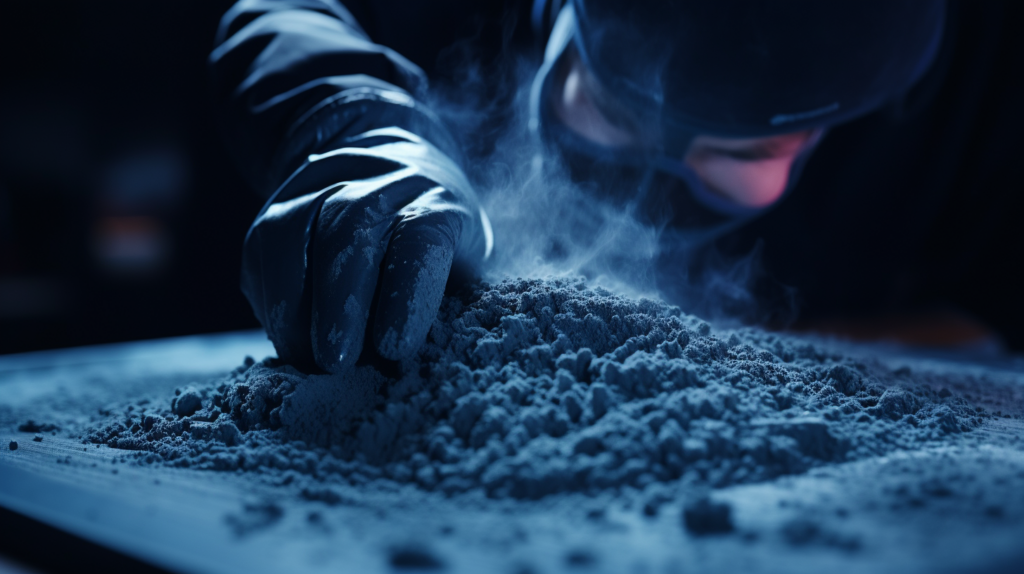
Aerospace industry
Metal 3D printing with powder materials has revolutionized the aerospace industry in numerous ways. With this advanced technology, aerospace engineers are able to create complex and lightweight components that were previously impossible to manufacture. The ability to print parts with intricate geometries and optimized designs has led to significant improvements in fuel efficiency and overall performance of aircraft. Additionally, metal 3D printing allows for rapid prototyping and customization, reducing production time and costs. This has opened up new possibilities for innovation and accelerated the development of cutting-edge aerospace technologies. As a result, metal 3D printing has become an indispensable tool in the aerospace industry, enabling the production of high-quality, reliable, and efficient aerospace components.
Medical industry
Metal 3D printing with powder materials has revolutionized various industries, including the medical industry. With its ability to create complex and customized designs, metal 3D printing has opened up new possibilities in the field of medicine. From creating patient-specific implants to producing intricate surgical instruments, this technology offers unparalleled precision and accuracy. Moreover, metal 3D printing enables the production of lightweight and durable medical devices that are biocompatible and can withstand the harsh conditions of the human body. As a result, it has significantly improved patient outcomes and reduced the risk of complications. The medical industry is embracing metal 3D printing as a game-changer, as it allows for faster and more cost-effective production of medical devices, ultimately benefiting both healthcare providers and patients alike.
Automotive industry
The automotive industry has been revolutionized by the advancements in metal 3D printing with powder materials. This innovative technology has paved the way for faster and more efficient production processes, allowing automakers to create complex and lightweight components with ease. Metal 3D printing offers numerous advantages to the automotive industry, including the ability to produce customized parts on-demand, reduced material waste, and improved design flexibility. With metal 3D printing, automakers can optimize the performance and durability of their vehicles, leading to enhanced fuel efficiency and overall customer satisfaction. Furthermore, this technology enables the production of intricate and intricate designs that were previously impossible to achieve using traditional manufacturing methods. As the automotive industry continues to embrace metal 3D printing, we can expect to see even more innovative and groundbreaking developments in the future.
Types of Powder Materials Used in Metal 3D Printing
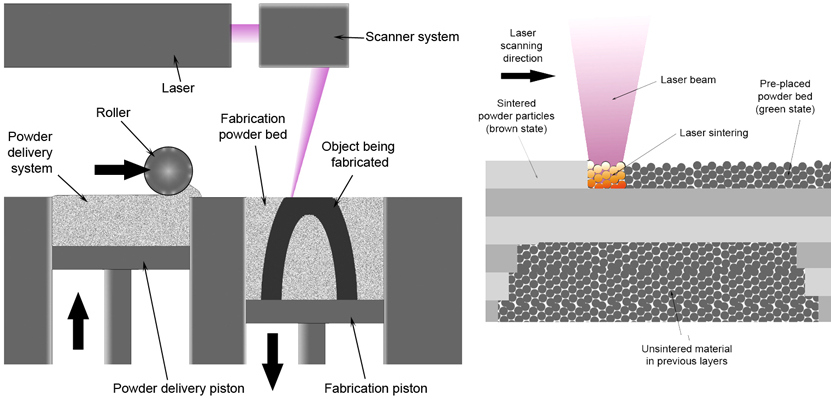
Stainless steel
Stainless steel is one of the most popular materials used in metal 3D printing with powder materials. It offers numerous advantages that make it a preferred choice for various applications. Firstly, stainless steel is known for its high strength and durability, making it suitable for producing robust and long-lasting parts. Additionally, it has excellent corrosion resistance, which is crucial for applications in industries such as aerospace and automotive. Moreover, stainless steel can be easily machined and post-processed, allowing for greater design flexibility and customization. With its ability to withstand high temperatures and maintain dimensional stability, stainless steel is an ideal material for demanding applications that require both strength and performance in metal 3D printing.
Titanium
Titanium is a highly versatile metal that has gained significant popularity in the field of 3D printing. With its exceptional strength-to-weight ratio and excellent corrosion resistance, titanium offers numerous advantages for metal 3D printing with powder materials. The use of titanium in 3D printing allows for the creation of complex geometries and intricate designs that were previously unattainable. Additionally, titanium’s biocompatibility makes it an ideal choice for medical applications, such as implants and prosthetics. The ability to 3D print titanium parts also enables cost-effective production and reduces material waste. Overall, titanium plays a crucial role in pushing the boundaries of metal 3D printing and unlocking new possibilities in various industries.
Aluminum
Aluminum is a widely used material in various industries due to its exceptional properties. When it comes to metal 3D printing, aluminum offers several advantages that make it a popular choice. Firstly, aluminum is lightweight yet strong, making it ideal for applications where weight reduction is crucial. Additionally, aluminum has excellent thermal conductivity, allowing for efficient heat dissipation in 3D printed components. Moreover, aluminum is highly corrosion-resistant, ensuring the durability and longevity of the printed parts. With its versatility and superior properties, aluminum is undoubtedly a valuable material for metal 3D printing with powder materials.
Challenges and Limitations of Metal 3D Printing
High cost of equipment
Metal 3D printing with powder materials offers numerous advantages, but one of the main drawbacks is the high cost of equipment. The specialized machines and materials required for metal 3D printing can be significantly more expensive compared to traditional manufacturing methods. This cost can be a barrier for many businesses and individuals looking to adopt metal 3D printing technology. However, despite the initial investment, the long-term benefits of metal 3D printing, such as increased design freedom, reduced lead times, and the ability to create complex geometries, can outweigh the high equipment costs. As the technology continues to advance and become more widely adopted, it is expected that the cost of equipment will decrease, making metal 3D printing a more accessible option for a wider range of applications.
Post-processing requirements
Post-processing requirements are an essential aspect of metal 3D printing with powder materials. After the printing process is complete, the printed parts often require additional steps to achieve the desired final properties and appearance. These post-processing steps can include heat treatment, machining, polishing, and surface finishing. Heat treatment is commonly used to enhance the mechanical properties of the printed parts, such as strength and hardness. Machining is necessary to remove excess material and refine the dimensions of the printed parts. Polishing and surface finishing techniques are employed to improve the surface quality and aesthetics of the parts. Overall, post-processing requirements play a crucial role in ensuring the success and usability of metal 3D printed parts with powder materials.
Limited material options
Limited material options is one of the main challenges of metal 3D printing with powder materials. Unlike traditional manufacturing methods, where a wide range of materials can be used, metal 3D printing is often limited to specific types of metal powders. This limitation can restrict the design possibilities and functional properties of the printed parts. However, advancements in metal 3D printing technology are constantly expanding the range of available materials, allowing for more diverse applications. Researchers and manufacturers are actively working on developing new metal powders with improved properties and compatibility for 3D printing, which will further enhance the advantages of this innovative manufacturing technique.
Future Trends in Metal 3D Printing
Improved speed and efficiency
Metal 3D printing with powder materials offers improved speed and efficiency compared to traditional manufacturing methods. By using a layer-by-layer additive manufacturing process, metal parts can be produced with intricate designs and complex geometries at a faster rate. This technology eliminates the need for costly tooling and reduces the time required for prototyping and production. Additionally, metal 3D printing allows for the optimization of material usage, minimizing waste and reducing overall production costs. With its ability to produce high-quality parts with shorter lead times, metal 3D printing with powder materials is revolutionizing the manufacturing industry.
Development of new materials
The development of new materials is a crucial aspect in the field of metal 3D printing with powder materials. As technology advances, researchers and engineers are constantly exploring and innovating new materials that can be used in the 3D printing process. These new materials offer numerous advantages, such as enhanced mechanical properties, improved heat resistance, and increased durability. By developing and utilizing these materials, manufacturers can create complex and intricate metal parts with high precision and quality. Additionally, the development of new materials opens up possibilities for the production of customized and unique designs that were previously unachievable. With ongoing research and development, the future of metal 3D printing with powder materials holds immense potential for further advancements in material science and manufacturing capabilities.
Integration with other manufacturing processes
Metal 3D printing with powder materials offers numerous advantages, especially when it comes to integration with other manufacturing processes. One of the key benefits is the ability to create complex geometries that are difficult or impossible to achieve with traditional manufacturing methods. This opens up new possibilities for designing and producing intricate parts that can enhance the performance and functionality of various products. Additionally, metal 3D printing allows for seamless integration with other manufacturing techniques, such as CNC machining or post-processing treatments. This means that parts produced through metal 3D printing can be further refined or customized to meet specific requirements. The integration of metal 3D printing with other manufacturing processes enables manufacturers to optimize production workflows, reduce costs, and improve overall product quality.