Metal powders are essential in various industries like aerospace, electronics, and additive manufacturing. They form the backbone of many technological advances we see today. One such highly versatile and fascinating powder alloy is FeCoNiCrMn, a high-entropy alloy (HEA) made up of five core elements: Iron (Fe), Cobalt (Co), Nickel (Ni), Chromium (Cr), and Manganese (Mn). You may have heard of this powder being used in 3D printing or for high-strength, corrosion-resistant parts in industries. But what is it exactly? What makes it stand out in the world of metal powders? Let’s break it down.
Overview of FeCoNiCrMn Powder
At first glance, FeCoNiCrMn powder might sound like just another metal alloy. But this alloy is special, mainly because of its unique properties resulting from its multi-component nature. Unlike traditional alloys, which are typically composed of one or two primary metals, FeCoNiCrMn is a high-entropy alloy (HEA), meaning it contains near-equimolar amounts of five different metals. This multi-element composition offers significant advantages in terms of durability, corrosion resistance, and strength, making it a go-to material for industries that demand high performance under harsh conditions.
FeCoNiCrMn powder’s importance continues to grow with the rise of additive manufacturing (AM) and powder metallurgy, where this alloy serves as a material of choice for parts that need a balance of mechanical properties and stability at elevated temperatures.
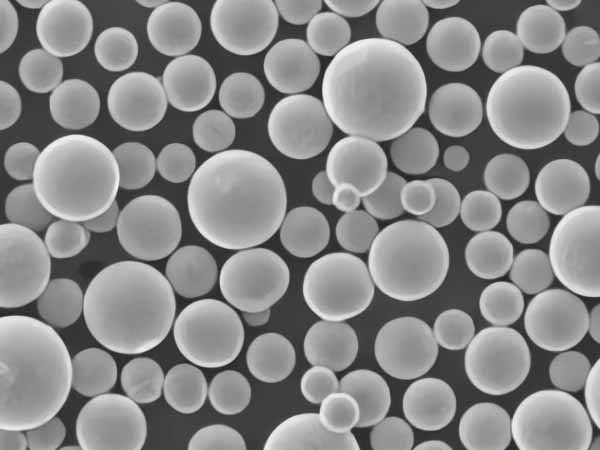
Key Characteristics of FeCoNiCrMn Powder
Property | Details |
---|---|
Composition | Iron (Fe), Cobalt (Co), Nickel (Ni), Chromium (Cr), Manganese (Mn) |
Density | 7.9 – 8.0 g/cm³ |
Melting Point | ~1370°C – 1420°C |
Corrosion Resistance | Excellent in acidic and basic environments |
Strength | High tensile strength and yield strength |
Ductility | Excellent, better than many conventional alloys |
Hardness | Can vary, generally 200-400 HV depending on processing |
Thermal Stability | Maintains mechanical properties up to 900°C |
Oxidation Resistance | Superior due to high Chromium content |
Magnetic Properties | Moderate, with high permeability from Fe, Co, and Ni content |
Composition of FeCoNiCrMn Powder
The beauty of FeCoNiCrMn powder lies in its equal contribution from five elements: Iron, Cobalt, Nickel, Chromium, and Manganese. The high-entropy nature of this alloy enhances its mechanical and thermal properties due to the multiple principal elements that interact at an atomic level, offering a solid solution strengthening effect.
- Iron (Fe): Provides strength and durability.
- Cobalt (Co): Adds magnetic properties and improves wear resistance.
- Nickel (Ni): Enhances toughness and corrosion resistance.
- Chromium (Cr): Contributes to oxidation resistance and corrosion protection.
- Manganese (Mn): Improves ductility and helps stabilize the austenitic structure.
By balancing these elements in near-equal atomic ratios, FeCoNiCrMn powder achieves a perfect equilibrium between strength, ductility, and corrosion resistance, which is something that traditional alloys can’t easily achieve.
Table of Elemental Composition of FeCoNiCrMn Powder
Element | Approximate Atomic % |
---|---|
Iron (Fe) | 20% |
Cobalt (Co) | 20% |
Nickel (Ni) | 20% |
Chromium (Cr) | 20% |
Manganese (Mn) | 20% |
This equal distribution of elements helps ensure that no single element dominates the material’s properties, providing synergy between all components for enhanced performance.
Specific Models of FeCoNiCrMn Powder
FeCoNiCrMn powder isn’t one-size-fits-all. Different manufacturers and industries create specific models of this alloy tailored for various applications. Below are ten FeCoNiCrMn powder models that are widely used:
1. Model: FeCoNiCrMn-AM01
- Application: Optimized for additive manufacturing (3D printing).
- Properties: Excellent printability, low porosity, and superior mechanical strength.
- Strength: Enhanced tensile strength and yield strength, ideal for complex geometries.
2. Model: FeCoNiCrMn-HT02
- Application: High-temperature environments, like aerospace parts.
- Properties: Superior thermal stability, maintains integrity up to 900°C.
- Strength: Strong resistance to high-temperature oxidation.
3. Model: FeCoNiCrMn-WR03
- Application: Wear-resistant coatings for industrial machinery.
- Properties: High wear resistance with good corrosion protection.
- Strength: Offers a tough, durable coating for long-lasting machine parts.
4. Model: FeCoNiCrMn-CR04
- Application: Corrosion-resistant parts for chemical industries.
- Properties: Excellent resistance to acidic and basic environments.
- Strength: High resistance to stress corrosion cracking.
5. Model: FeCoNiCrMn-MP05
- Application: Multi-purpose industrial applications.
- Properties: Balanced mechanical properties, suitable for a variety of applications.
- Strength: Offers both ductility and strength for versatility.
6. Model: FeCoNiCrMn-AL06
- Application: Aerospace lightweight parts.
- Properties: Reduced density, while maintaining high strength.
- Strength: Ideal for aerospace structures where weight is a critical factor.
7. Model: FeCoNiCrMn-HP07
- Application: High-pressure vessels and components.
- Properties: High strength, excellent pressure resistance, and fatigue strength.
- Strength: Enhanced yield strength for high-stress applications.
8. Model: FeCoNiCrMn-MS08
- Application: Medical instruments.
- Properties: Biocompatibility, excellent surface finish, and corrosion resistance.
- Strength: Ideal for surgical tools and implants.
9. Model: FeCoNiCrMn-TS09
- Application: Turbine blades in power generation.
- Properties: High strength at elevated temperatures, superior oxidation resistance.
- Strength: Ensures durability in high-temperature environments like gas turbines.
10. Model: FeCoNiCrMn-MT10
- Application: Marine applications.
- Properties: High corrosion resistance in saltwater environments.
- Strength: Ideal for marine hardware and ship components.
-
NiCoCrAlY alloys powders
-
Rene 142 alloy-Rene Powder
-
Haynes 25 Haynes Powder
-
Best Hastelloy C-22 Powder-High temperature alloy Powder for 3D Printing
-
Best Hastelloy C-276 Powder-High temperature alloy Powder for 3D Printing
-
Best Hastelloy N Powder-High temperature alloy Powder for 3D Printing
-
Best Hastelloy B Powder丨High temperature alloy Powder for 3D Printing
-
FGH95 Ni-base Alloy Powder | Nickel Alloy Powder
-
CMSX-4 Nickel Alloy Powder | Nickel Alloy Powder
Characteristics of FeCoNiCrMn Powder
Why is FeCoNiCrMn powder gaining traction across industries? Its standout characteristics make it an appealing option for engineers and manufacturers alike.
Mechanical Properties
FeCoNiCrMn powder offers an excellent balance of strength and ductility. Unlike other alloys that might become brittle under stress, this alloy maintains its form, making it an ideal candidate for parts that will endure high mechanical loads. Its tensile strength and yield strength outperform many traditional stainless steels.
Thermal Stability
Another key characteristic is its thermal stability. FeCoNiCrMn can maintain its mechanical properties even when exposed to high temperatures, with good creep resistance. This makes it ideal for industries such as aerospace and power generation, where parts must endure high heat and stress.
Corrosion Resistance
The addition of Chromium, Nickel, and Cobalt makes this alloy highly resistant to corrosion. It’s particularly effective in resisting corrosion in acidic and alkaline environments, which is why it’s popular in the chemical processing industry.
Oxidation Resistance
Thanks to its Chromium content, FeCoNiCrMn powder offers superior oxidation resistance, even at elevated temperatures. This property is beneficial in applications like turbines, where parts are exposed to both heat and oxygen.
Advantages of FeCoNiCrMn Powder
So, what makes FeCoNiCrMn powder stand out compared to other metal powders? Let’s explore some of the advantages.
1. Versatility in Applications
FeCoNiCrMn powder is a multi-purpose alloy that can be tailored to suit various industries, from aerospace to medical, depending on the processing and element ratios.
2. High Mechanical Strength
FeCoNiCrMn provides exceptional mechanical properties that rival traditional metal powders. Its high tensile and yield strength ensure that parts made from this powder can withstand rigorous use, especially in industries like automotive and aerospace.
3. Corrosion and Oxidation Resistance
The composition of FeCoNiCrMn offers unparalleled resistance to both corrosion and oxidation, making it a great choice for applications exposed to harsh environments. Its Chromium and Nickel content helps protect parts from rust and chemical damage, reducing maintenance costs and extending lifespan.
4. Temperature Stability
FeCoNiCrMn powder maintains its structural integrity at high temperatures. This makes it ideal for high-temperature applications, where many materials would degrade or fail.
5. Additive Manufacturing Friendly
The powder’s fine granulation makes it perfect for 3D printing. It offers low porosity, excellent printability, and smooth surface finishes, enabling intricate part design with high detail and precision.
Applications of FeCoNiCrMn Powder
The properties of FeCoNiCrMn powder make it a material of choice in various industries. Here’s where it shines:
Application Area | Key Uses |
---|---|
Aerospace Industry | Lightweight structural components, turbine blades, heat-resistant parts |
Medical Devices | Surgical tools, implants, biocompatible components |
Additive Manufacturing | 3D printing for complex, high-strength parts |
Chemical Processing | Corrosion-resistant components for reactors, tanks, pipes |
Power Generation | High-temperature components for gas and steam turbines |
Marine Industry | Corrosion-resistant marine components |
Automotive Industry | Engine components, heat exchangers, wear-resistant parts |
Specifications, Sizes, and Standards of FeCoNiCrMn Powder
FeCoNiCrMn powders come in a variety of grades, sizes, and specifications depending on the application and manufacturer. Below is a comparison of the most common specifications:
Parameter | Details |
---|---|
Particle Size | 15µm to 150µm |
Purity | ≥ 99.9% |
ISO Standards | ISO 9001:2015, ISO 14001:2015 |
Shape | Spherical, irregular |
Density (Bulk) | 7.8 g/cm³ – 8.0 g/cm³ |
Grade Types | FeCoNiCrMn-AM01, FeCoNiCrMn-HT02, etc. |
Surface Area (BET) | 0.1 – 10 m²/g depending on particle size |
Suppliers and Pricing of FeCoNiCrMn Powder
When it comes to purchasing FeCoNiCrMn powder, several suppliers stand out for their high-quality products. Here’s a quick look at some popular suppliers and general pricing for the powder:
Supplier | Product Type | Price (per kg) |
---|---|---|
Tekna Powders | AM-Grade FeCoNiCrMn Powder | $300 – $450 |
Höganäs AB | High-Purity FeCoNiCrMn Alloy | $350 – $480 |
Carpenter Technology | Industrial-Grade FeCoNiCrMn Powder | $280 – $420 |
Sandvik Additive | FeCoNiCrMn for 3D Printing | $320 – $470 |
EOS GmbH | Powder for Metal Additive Manufacturing | $310 – $460 |
Pros and Cons of FeCoNiCrMn Powder
Every material has its strengths and weaknesses. Let’s compare the advantages and limitations of FeCoNiCrMn powder:
Pros | Cons |
---|---|
High mechanical strength | More expensive than traditional alloys |
Excellent corrosion and oxidation resistance | Limited availability due to specialized manufacturing |
Superior thermal stability | Difficult to process in traditional manufacturing methods |
Versatile, can be tailored to different applications | Powder processing requires specialized equipment |
Ideal for additive manufacturing | High raw material costs due to multiple metal components |
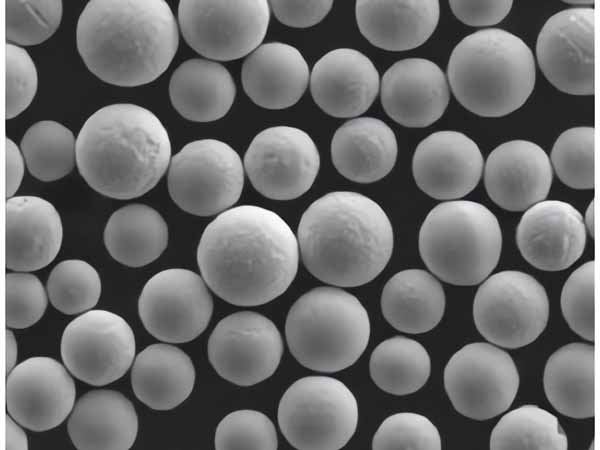
FAQs
Question | Answer |
---|---|
What industries benefit most from FeCoNiCrMn powder? | Aerospace, chemical processing, additive manufacturing, and marine industries benefit the most from its strength, corrosion resistance, and durability. |
Is FeCoNiCrMn powder suitable for 3D printing? | Yes, it is highly suitable for 3D printing due to its fine granulation, excellent printability, and mechanical properties. |
How does FeCoNiCrMn compare to traditional stainless steel? | FeCoNiCrMn offers better high-temperature strength, corrosion resistance, and mechanical performance compared to many stainless steel variants. |
What is the melting point of FeCoNiCrMn powder? | The melting point ranges between 1370°C to 1420°C, depending on its exact composition and processing. |
Is FeCoNiCrMn powder expensive? | It is generally more expensive than conventional alloys due to its complex composition, but the performance justifies the cost in many applications. |
Can FeCoNiCrMn powder be used in medical applications? | Yes, it’s biocompatible and ideal for surgical tools, implants, and other medical devices. |
Conclusion
FeCoNiCrMn powder is a material that’s changing the game across various industries. Whether you’re in aerospace, additive manufacturing, or even the medical field, the alloy’s high strength, corrosion resistance, and versatility make it a standout choice. Its combination of multiple elements allows it to meet stringent mechanical and environmental requirements, making it far superior to many traditional alloys. Sure, it may be more expensive, but the investment pays off with longer-lasting, higher-performing parts.
If you’re looking for a material that can withstand the toughest conditions, FeCoNiCrMn powder is worth considering.