Hastelloy X is a premium nickel-based superalloy powder designed for extreme high temperature resistance and structural stability in aggressive environments. This guide covers Hastelloy X powder metallurgy including composition, properties data, manufacturing methods, applications, availability, pricing, product specifications, usage guidelines, alternatives comparison and expert advice.
Overview
Nickel-chromium-iron-molybdenum Hastelloy X alloy powder possesses an exceptional combination of oxidation and creep resistance properties up to 1300°C (2400°F), suited for demanding heat exchanger tubing, combustion cans, spray coatings and component repair. Key features:
- Excellent high temperature strength and structure stability
- Resists hot corrosion and oxidation
- High thermal fatigue and stress rupture resistance
- Retains properties across cryo to elevated temperatures
- Can be welded, sintered, spray formed or 3D printed
- Enables lighter, smaller and high performance designs
Continue reading for in-depth technical data on specification, processing and applications for this versatile and robust superalloy powder.
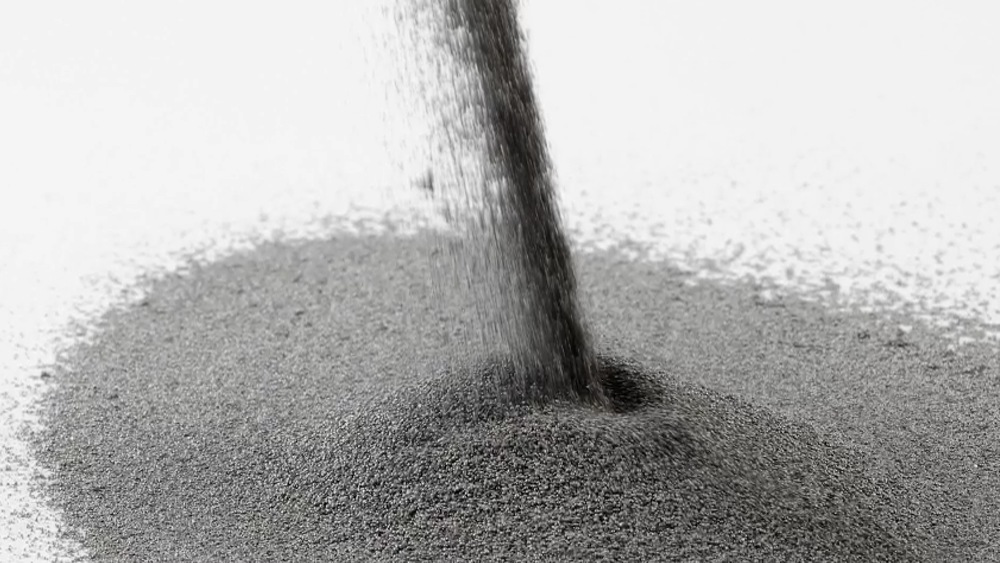
Composition and Characteristics
Hastelloy X powder composition comprises nickel, chromium, iron and molybdenum as the main constituents:
Element | Weight % | Role |
---|---|---|
Nickel (Ni) | Balance, ~47% | Corrosion resistance, ductility |
Chromium (Cr) | 21-23% | Oxidation resistance |
Iron (Fe) | 18.5% max | Hardening, cost reduction |
Molybdenum (Mo) | 8-10% | Strength and stiffness |
Cobalt (Co) | 1% max | Grain structure control |
Others (Mn,Si,C) | <1% total | Residual traces |
Key Properties
- Density: 8.22 g/cc
- Melting Point: 1375°C
- Electrical Resistivity: 0.76 microOhm-cm
- Thermal Conductivity: 11.7 W/m-K at 500°C
Hastelloy X is first vacuum induction melted to refine composition, then gas atomized into fine spherical powder suitable for consolidated part fabrication via methods like hot isostatic pressing and sintering.
Manufacturing Process
Hastelloy X powder is produced via vacuum induction melting and inert gas atomization followed by size classification:
Steps | Details |
---|---|
Alloy Casting | Electric arc furnace smelting then vacuum oxygen decarburization to achieve chemistry specs |
Vacuum Induction Melting (VIM) | Refining step to improve cleanliness; 5-10%overmelt removes inclusions |
Electroslag Remelting (ESR) | Optional further polishing for mission critical applications |
Atomization | High velocity inert nitrogen/argon gas impinges on molten stream creating fine droplets that solidify into powder |
Sieving | Specific particle size distributions obtained via air classification and sieves |
Testing | Chemical analysis, particle size distribution, flow rates, SEM imaging |
Packaging | Sealed containers with dry nitrogen atmosphere |
Key characteristics:
- Spherical morphology with satellite particles from rapid solidification
- Flowable non-agglomerated powder with controlled size ranges
- Chemistries tailored for oxidation or corrosion resistance
- Custom particle engineering from 5 microns to 150 microns
Hastelloy powder is ready for direct usage in additive manufacturing or for consolidation into bulk components.
Applications and Uses
Hastelloy X’s exceptional elevated temperature properties enable diverse usages:
Additive Manufacturing
- 3D printing complex geometries using laser or electron beam systems
- Low volume parts without tooling costs
Thermal Spraying
- Wear and corrosion resistant coatings using plasma transferred arc
- Rebuild worn parts economically
Sintering
- Hot isostatic pressing into fully dense blocks and shapes
- High performance cast turbine blades
Metal Injection Molding
- Net shape small intricate components with thin walls
- Corrosion resistant valves and fittings
Welding
- Weld overlays on boiler tubes, pumps and valves
- Repair cracks and damaged components
Hastelloy X alloys thus serve critical roles across heat exchangers, chemical reactors, industrial gas turbines, pollution control, nuclear fuel cells and molten salt solar receivers.
Specifications
Hastelloy X powder is commercially available tuned to application requirements:
Parameter | Options |
---|---|
Particle Size Distribution | -325 mesh, -100/+325 mesh etc. |
Particle Shape | Predominantly spherical |
Size Range (μm) | 5 to 150 μm |
Apparent Density | Typically 2.5 to 4 g/cc |
True Density | 8.1 to 8.3 g/cc |
Hall Flow Rate | Flowable > 25 s/50g |
Chemical Composition | Table above |
Surface Area (m2/g) | 0.1 to 0.8 |
Packaging | Double sealed under N2 |
Particle sizing – Smaller than 5 microns can be requested custom but affects flowability. Larger above 120μm drops densification.
Apparent density – Higher is better for powder spreading. Values can be increased through treatments.
Surface area – Governs dissolution kinetics. Higher needs more binding during sintering.
Chemistry – Tolerances between melt batches rarely exceed +/- 1%
Availability and Pricing
As a specialized superalloy, Hastelloy X powder is costlier than mass market alternatives. But minor usages enable major performance gains and downstream economies.
Description | Quantity | Price |
---|---|---|
Research sample | 50g | $200+ |
Prototyping | 1 kg | $1000+ |
Commercial | 10+ kg | $650+ per kg |
Larger bulk orders above 100 kg offer discounted rates, especially for qualified long term agreements. However MOQ applies on custom particle engineering.
High purity medical or aerospace sector variants with additional ESR melt purification fetch higher costs.
Around 8-12 week typical lead times for custom production runs and large quantity fabrication. Fast turnaround small samples usually ready for shipment within 2 weeks.
-
0# Pure Nickel powder
-
NiCoCrAlY alloys powders
-
Rene 142 alloy-Rene Powder
-
Haynes 25 Haynes Powder
-
Best Hastelloy C-22 Powder-High temperature alloy Powder for 3D Printing
-
Best Hastelloy C-276 Powder-High temperature alloy Powder for 3D Printing
-
Best Hastelloy N Powder-High temperature alloy Powder for 3D Printing
-
Best Hastelloy B Powder丨High temperature alloy Powder for 3D Printing
-
FGH95 Ni-base Alloy Powder | Nickel Alloy Powder
Comparing Hastelloy X Powder vs Alternatives
Hastelloy X competes against other superalloys along with ceramics in extreme temperature material selection:
Material | Oxidation Resistance | Phase Stability | Tensile Strength | Cost |
---|---|---|---|---|
Hastelloy X | Excellent | Excellent | Medium | $$$ |
Inconel 625 | Good | Good | High | $ |
Inconel 718 | Good | Fair | Very High | $$ |
Tungsten | Medium | Excellent | High | $-$$ |
Molybdenum | Low | Excellent | Low | $$ |
Tungsten Carbide | Low | Excellent | High | $$$ |
Hafnium Carbide | Excellent | Excellent | Low | $$$$ |
Key Pros
- Unmatched hot corrosion resistance
- Retains stiffness and hardness over time
- Consistent long term phase structure
- Forgiving to minor compositional fluctuations
Limitations
- Not the strongest monolithic alloy available
- Difficult to completely eliminate minor impurities
- Brittle phases can emerge during improper heat treatments
- Relatively expensive feedstock powder pricing
For alloy stability across demanding thermal profiles without sudden property variations, Hastelloy X powder becomes the trusted solution.
and powder vendors to tailor procurement and processing for engineering targets.
Research and Development
Current initiatives improving Hastelloy X powder include:
Alloy Design
- Computational thermodynamic simulations assessing elemental interactions
- Validating property data from thin films up to large castings
Modeling
- Physics-based multi-physics predictions of lifetime thermo-mechanical performance
- Accelerated testing protocols copying operating conditions
Additive Manufacturing
- In situ electron microscopy revealing microstructure evolution
- Integrating cold spray, welding and post-treatments
Powder Processing
- Plasma spheroidization and flow aids to ease deposition
- Parameter studies on effects of size distribution and porosity
Applications
- Qualifying prototypes against application key performance indicators
- Growth into emerging sectors like molten salts and microreactors
Continual improvements now enable tapping the full capabilities of Hastelloy X as production scales catch up with demand.
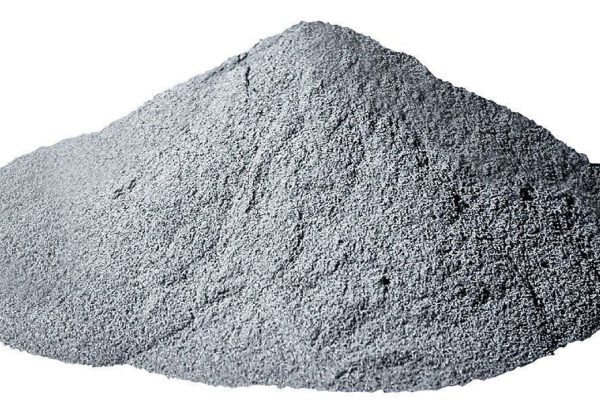
FAQs
Q: Is Hastelloy X powder reusable after additive manufacturing?
A: Yes, used powder can be harvested and reused typically 2-3 times if handled correctly to prevent oxidation or contamination in handling. But varying powder bed exposure can cause changes needing analysis before mixing with fresh batches.
Q: Does Hastelloy X become brittle over time?
A: The alloy retains exceptional ductility and fracture toughness during prolonged exposures above 1000°C for 10,000+ hours unlike other competing options which can become prone to cracking due to carbide formations over aging. Proper heat treatments ensure stable microstructures.
Q: What particle size is optimal?
A: Generally between 15-45 microns works well for most additive manufacturing or pressing equipment now. But advances are enabling consistent dense builds from 5 to 100 micron powder depending on application geometries and surface finishes specified.
Q: What are common impurities needing avoidance?
A: Sulfur is most detrimental – just 20 ppm can instigate grain boundary weakness and accelerate creep formation. Tight melt practice controls along with thermal treatments preserve functionality.
Q: Does Hastelloy X rust or corrode?
A: It offers exceptional resistance to aqueous corrosion across acids, alkalis and salts up to high temperatures exceeding the limits of stainless steels and nickel alloys. It depends passivation protective chromium oxide films.
Summary
With outstanding high temperature strength, phase stability and oxidation resistance unmatched by competing alloys, Hastelloy X superalloy powder enables next generation components and coatings pushing performance envelopes further in demanding chemical, nuclear, aerospace and industrial heat exchanger environments up to 1300°C. As additive manufacturing proliferates, research continues improving microstructures and qualifying more applications leveraging Hastelloy X’s multifunctional capabilities over conventional materials. Careful verification of powder quality and integrating heat treatments into fabrication processes allows harnessing the full potential of this versatile nickel-based superalloy.