Haynes 25, also known as L605 powder, is a cobalt-based superalloy engineered for extreme conditions. It’s renowned for its robust heat resistance, wear protection, and corrosion resilience, making it indispensable in demanding sectors like aerospace, medical, and industrial manufacturing. This article unpacks everything about Haynes 25 powder—its composition, types, unique properties, and how it stacks up in various applications.
Overview of Haynes 25 (L605) Powder
What is Haynes 25 (L605) Powder?
Haynes 25, or L605 powder, is a high-performance alloy containing a mix of cobalt, chromium, tungsten, and nickel. This alloy is specially designed to withstand high temperatures, intense friction, and corrosive environments, ideal for parts that need to maintain their integrity and durability under stress. In powder form, Haynes 25 offers manufacturing flexibility for precision components, coating, and additive manufacturing applications.
Why Use Haynes 25 Powder?
- Extreme Temperature Tolerance: Can sustain mechanical integrity beyond 1,000°C.
- Superior Wear Resistance: Withstands high friction and repetitive wear.
- Corrosion Resistance: Offers protection in marine, medical, and chemical exposure environments.
- Flexible Manufacturing: Powder form supports 3D printing, sintering, and coating applications.
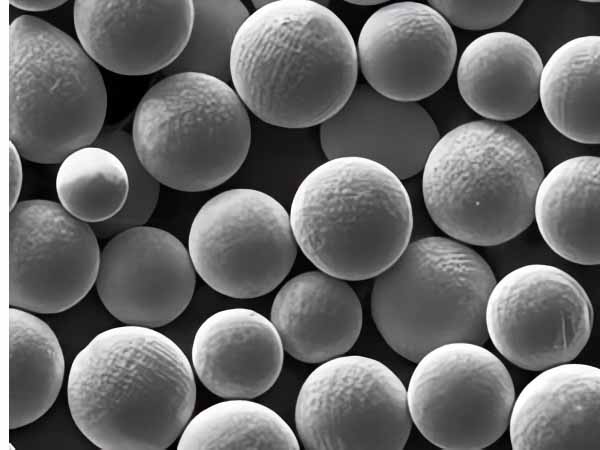
Composition of Haynes 25 (L605) Powder
Haynes 25 is defined by a carefully balanced mix of metals, each contributing specific strengths to the alloy.
Element | Typical Composition (%) | Role in Alloy |
---|---|---|
Cobalt (Co) | 50-52% | Base element, provides strength and stability at high temperatures. |
Chromium (Cr) | 19-21% | Enhances oxidation and corrosion resistance. |
Tungsten (W) | 14-16% | Increases wear resistance and high-temperature strength. |
Nickel (Ni) | 9-11% | Improves ductility and corrosion resistance. |
Others | Remaining balance | Small quantities of iron, manganese, silicon, and carbon, each tailored for unique alloy characteristics. |
The alloy’s cobalt-heavy composition ensures that it can resist creep deformation at high temperatures, while chromium and tungsten boost its resilience to oxidation and wear.
Types of Haynes 25 (L605) Powder: Specific Models and Variants
Haynes 25 powder is available in several variants, each tailored to different applications, from coating components to manufacturing high-stress parts.
Model | Description |
---|---|
Haynes 25-PF | Ultra-fine powder, excellent for high-precision applications such as coatings on turbine blades. |
Haynes 25-SF | Super-fine particle size, optimal for 3D printing and intricate metal fabrication. |
Haynes 25-DF | Dense flow model, designed for applications requiring solid metal mass, like automotive parts. |
Haynes 25-HS | High-strength variant, ideal for aerospace where durability is critical under high stress. |
Haynes 25-MT | Medium-temperature model, suitable for components exposed to moderate heat, e.g., industrial valves. |
Haynes 25-HT | Designed for extreme temperatures over 1,000°C, ideal for gas turbine applications. |
Haynes 25-EX | Extreme durability version, enhanced for use in highly corrosive environments. |
Haynes 25-MF | Metal-forming grade, allowing complex part manufacturing with high detail accuracy. |
Haynes 25-WP | Wear-proof model, designed for components with heavy wear, such as industrial machinery. |
Haynes 25-XC | Extra-coarse, suitable for applications where larger particles provide structural benefits. |
Each variant is engineered to meet specific needs, giving manufacturers flexibility in using Haynes 25 across diverse industries.
Characteristics of Haynes 25 (L605) Powder
Haynes 25 powder’s unique properties make it invaluable for high-performance parts. Here’s a closer look at its standout characteristics:
1. Heat Resistance
Haynes 25’s cobalt and tungsten content allow it to operate in temperatures over 1,000°C without deformation, a critical factor for aerospace and turbine applications. Unlike some alloys that become brittle or weak, Haynes 25 maintains both its shape and tensile strength, which is essential in high-stress situations like jet engines and power turbines.
2. Corrosion Resistance
The high chromium content in Haynes 25 enables it to resist oxidation in harsh environments. This is why it’s popular in the marine industry, as well as in chemical processing plants where equipment is often exposed to corrosive chemicals.
3. Wear Resistance
Tungsten, a key component, increases Haynes 25’s wear resistance, making it ideal for parts that undergo constant friction or repetitive motion, such as mechanical seals and bearing components. This resistance extends the life of parts, saving costs in replacement and downtime.
4. Mechanical Strength and Malleability
Haynes 25 strikes a balance between strength and malleability. Despite being a high-strength alloy, it remains ductile enough to be formed into complex shapes. This is beneficial for intricate components requiring high structural integrity without brittleness.
Applications of Haynes 25 (L605) Powder
Haynes 25 powder is indispensable across various industries, with applications often involving extreme conditions or high-precision requirements.
Industry | Applications |
---|---|
Aerospace | Turbine blades, combustion chamber liners, exhaust ducts. |
Medical | Implants and surgical instruments, especially those requiring biocompatibility and durability. |
Automotive | High-performance valves, turbocharger components. |
Power Generation | Gas turbines, heat exchangers, power plant hardware exposed to high temperatures. |
Industrial | Bearings, valves, pumps, chemical processing components requiring corrosion resistance. |
Marine | Fasteners, marine engine components exposed to saltwater and corrosive conditions. |
With such a diverse range of uses, Haynes 25 powder is a go-to material wherever durability, temperature tolerance, and corrosion resistance are paramount.
Advantages of Haynes 25 (L605) Powder
Haynes 25 powder stands out in several ways compared to other materials:
Advantage | Description |
---|---|
High-Temperature Stability | Operates effectively at temperatures over 1,000°C, essential for aerospace and turbines. |
Exceptional Durability | Offers superior wear resistance, saving on part replacement and reducing downtime. |
Corrosion Resistance | Chromium and cobalt protect against oxidation, valuable in harsh chemical or marine settings. |
Versatile Manufacturing | Powder form supports applications from 3D printing to casting and coatings. |
Malleability | Can be shaped into intricate components without losing structural integrity. |
However, Haynes 25 does come with some limitations, such as its cost compared to simpler alloys, and its machining can be challenging due to the high-strength properties.
Specifications and Standards for Haynes 25 (L605) Powder
Specification | Details |
---|---|
Particle Size | Available in various sizes, from super-fine to extra-coarse. |
Density | Approximately 9.1 g/cm³ |
Melting Point | 1,336°C |
Hardness | 200-300 HB (Brinell Hardness) |
Standards | ASTM F90, AMS 5537, AMS 5759, DIN 2.4964 |
This table highlights some common specifications for Haynes 25 powder, which are critical in ensuring it meets the needs of specific industrial applications.
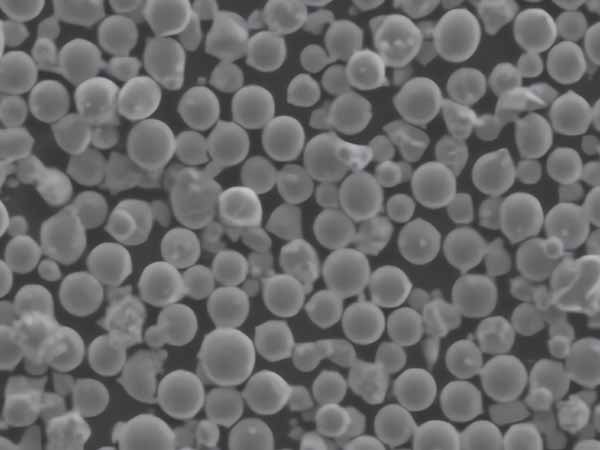
FAQ
Question | Answer |
---|---|
Is Haynes 25 suitable for 3D printing? | Yes, several models like Haynes 25-SF are optimized for 3D printing. |
What industries use Haynes 25 powder the most? | Aerospace, medical, automotive, and marine industries are primary users due to the alloy’s properties. |
What temperature can Haynes 25 withstand? | Haynes 25 can operate above 1,000°C without losing structural integrity. |
Is Haynes 25 biocompatible? | Yes, it’s used in medical implants due to its biocompatibility and corrosion resistance. |
How does Haynes 25 compare to stainless steel? | Haynes 25 offers superior heat and wear resistance but is generally more expensive than stainless steel. |