Overview of Highly Spherical Powder
Highly spherical powder refers to a type of metal powder characterized by its uniform, spherical shape. This powder is commonly used in various industries, such as additive manufacturing, metal injection molding (MIM), and powder metallurgy, due to its superior flowability, packing density, and consistency. The spherical shape of these powders ensures a higher packing density, leading to enhanced mechanical properties in the final product. Whether you’re an engineer, manufacturer, or simply interested in materials science, understanding the intricacies of highly spherical powder can greatly influence your decision-making process.
Introduction
Imagine you’re trying to fit marbles into a jar. If the marbles are perfectly round and uniform in size, they’ll fit together snugly, leaving minimal gaps. This is essentially what highly spherical powders do in various industrial applications. Their uniform shape allows for better packing and flowability, making them ideal for processes that require precision and consistency.
In this article, we will dive deep into the world of highly spherical powders, exploring their composition, characteristics, applications, and much more. We’ll also take a closer look at specific metal powder models, comparing them based on their properties, advantages, and limitations. By the end, you’ll have a thorough understanding of what makes highly spherical powders so valuable in today’s manufacturing processes.
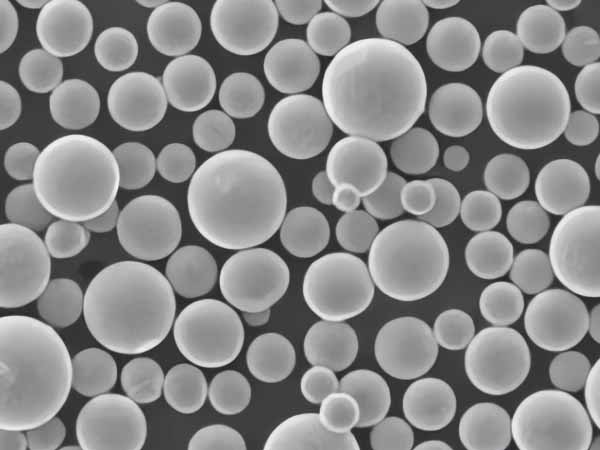
Composition of Highly Spherical Powder
The composition of highly spherical powders varies depending on the metal or alloy used. Common materials include aluminum, titanium, stainless steel, and cobalt-chromium alloys. Each material offers unique properties that make it suitable for specific applications. For instance, aluminum is lightweight and corrosion-resistant, making it ideal for aerospace components, while titanium is known for its strength and biocompatibility, making it perfect for medical implants.
Common Metal Powder Models and Their Compositions
Metal Powder Model | Composition | Characteristics |
---|---|---|
AlSi10Mg | Aluminum (90%), Silicon (10%), Magnesium (0.1-0.4%) | Lightweight, excellent corrosion resistance, good thermal conductivity |
Ti6Al4V | Titanium (90%), Aluminum (6%), Vanadium (4%) | High strength, biocompatible, excellent corrosion resistance |
316L Stainless Steel | Iron (64%), Chromium (17%), Nickel (12%), Molybdenum (2-3%) | Excellent corrosion resistance, good mechanical properties |
Inconel 718 | Nickel (50-55%), Chromium (17-21%), Iron (balance), Molybdenum (2.8-3.3%) | High temperature resistance, corrosion resistance, strength |
CoCrMo Alloy | Cobalt (60-65%), Chromium (27-30%), Molybdenum (5-7%) | High wear resistance, corrosion resistance, biocompatibility |
CuNi2SiCr | Copper (98%), Nickel (2%), Silicon (0.5%), Chromium (0.5%) | Good electrical conductivity, corrosion resistance |
FeSi | Iron (90%), Silicon (9.5-10.5%) | High magnetic permeability, low electrical conductivity |
NiTi (Nitinol) | Nickel (55%), Titanium (45%) | Shape memory effect, superelasticity, biocompatibility |
WC-Co | Tungsten Carbide (88-93%), Cobalt (6-12%) | High hardness, wear resistance, toughness |
Al2O3 | Aluminum Oxide (99.5% or higher) | High hardness, wear resistance, good electrical insulation |
These powders are produced through processes such as gas atomization, plasma atomization, or centrifugal atomization, which ensure that the particles are uniformly spherical.
Characteristics of Highly Spherical Powder
The main characteristics of highly spherical powders include:
- Flowability: Due to their smooth, round shape, these powders flow more easily compared to irregularly shaped powders. This property is crucial in applications like additive manufacturing, where consistent layer deposition is essential.
- Packing Density: The spherical shape allows for closer packing, resulting in higher density and better mechanical properties in the final product.
- Reduced Surface Area: Spherical powders have a lower surface area compared to irregularly shaped particles, which can reduce oxidation and improve the powder’s shelf life.
- Consistency in Particle Size Distribution: Uniform particle size distribution ensures predictable behavior during the manufacturing process, leading to higher quality end products.
Applications of Highly Spherical Powder
Highly spherical powders are employed in a wide range of industries due to their unique properties. Below are some common applications:
Application | Powder Type | Description |
---|---|---|
Additive Manufacturing (3D Printing) | Ti6Al4V, Inconel 718 | Used for producing complex, lightweight parts with high strength and durability |
Metal Injection Molding (MIM) | 316L Stainless Steel, CoCrMo | Ideal for producing small, intricate parts with high precision |
Thermal Spraying | AlSi10Mg, Inconel 718 | Provides protective coatings with high wear and corrosion resistance |
Biomedical Implants | Ti6Al4V, CoCrMo Alloy | Used for producing biocompatible implants with excellent mechanical properties |
Aerospace Components | AlSi10Mg, Ti6Al4V | Lightweight and strong, ideal for aerospace applications |
Electrical Conductors | CuNi2SiCr | Good electrical conductivity, used in electrical components |
Magnetic Applications | FeSi | High magnetic permeability, used in magnetic cores and sensors |
Tooling and Cutting Tools | WC-Co | High hardness and wear resistance, ideal for cutting tools and wear-resistant parts |
Ceramic Components | Al2O3 | High hardness and wear resistance, used in wear-resistant coatings and insulators |
-
CM247LC Powder | Nickel Alloy Powder
-
0# Pure Nickel powder
-
NiCoCrAlY alloys powders
-
Rene 142 alloy-Rene Powder
-
Haynes 25 Haynes Powder
-
Best Hastelloy C-22 Powder-High temperature alloy Powder for 3D Printing
-
Best Hastelloy C-276 Powder-High temperature alloy Powder for 3D Printing
-
Best Hastelloy N Powder-High temperature alloy Powder for 3D Printing
-
Best Hastelloy B Powder丨High temperature alloy Powder for 3D Printing
Advantages of Highly Spherical Powder in Manufacturing
- Enhanced Flowability: Spherical powders flow better through feed systems, reducing the risk of clogging and ensuring consistent material deposition.
- Improved Mechanical Properties: The high packing density achieved by spherical powders leads to improved mechanical properties in the final product, such as higher strength and toughness.
- Better Surface Finish: The uniformity of spherical powders results in smoother surfaces, reducing the need for post-processing.
- Reduced Oxidation: With a lower surface area, spherical powders are less prone to oxidation, which can be critical for maintaining material properties during storage and processing.
- Versatility: These powders are suitable for a wide range of applications, from aerospace to biomedical, making them a versatile choice for manufacturers.
Disadvantages and Limitations
While highly spherical powders offer many benefits, they are not without their limitations:
- Cost: The production processes used to create highly spherical powders, such as gas atomization, are often more expensive than those for irregular powders. This can increase the overall cost of the material.
- Limited Material Availability: Not all metals or alloys can be easily produced in a spherical form, limiting the selection of materials available in this format.
- Processing Challenges: In some cases, the very properties that make spherical powders desirable (such as high packing density) can also make them more challenging to process, particularly in applications requiring specific porosity or bonding characteristics.
Specifications, Sizes, Grades, and Standards
Highly spherical powders are available in various specifications, sizes, and grades, depending on the intended application. Below is a summary of some common specifications:
Metal Powder Model | Size Range (µm) | Purity (%) | Standard/Grade |
---|---|---|---|
AlSi10Mg | 15-45 | 99.5 | ASTM B918 |
Ti6Al4V | 20-63 | 99.9 | ASTM F2924, ISO 5832-3 |
316L Stainless Steel | 15-53 | 99.8 | ASTM B243, ISO 22068 |
Inconel 718 | 15-45 | 99.5 | ASTM F3055 |
CoCrMo Alloy | 10-45 | 99.7 | ASTM F75, ISO 5832-4 |
CuNi2SiCr | 10-45 | 99.9 | ASTM B243 |
FeSi | 20-63 | 99.5 | ISO 6301 |
NiTi (Nitinol) | 20-53 | 99.5 | ASTM F2063 |
WC-Co | 10-45 | 99.8 | ISO 23356 |
Al2O3 | 5-25 | 99.5 | ASTM B243 |
Understanding the Importance of Specifications
Why are these specifications important? Well, imagine you’re baking a cake, and the recipe calls for a specific type of flour. Using the wrong kind, or one that’s not ground finely enough, could result in a cake that doesn’t rise properly. Similarly, the size, purity, and grade of highly spherical powders can significantly impact the performance and quality of the final product. For example, a powder with a broader particle size distribution might not pack as tightly, leading to lower density and reduced mechanical properties in the finished part.
Suppliers and Pricing Details
When sourcing highly spherical powders, it’s important to consider both quality and cost. Below is a summary of some reputable suppliers along with their pricing details:
Supplier | Metal Powder Model | Price (per kg) | Comments |
---|---|---|---|
Höganäs AB | Ti6Al4V | $350 | High-quality, consistent particle size distribution |
Carpenter Technology | 316L Stainless Steel | $220 | Known for high purity and consistent quality |
EOS GmbH | AlSi10Mg | $200 | Optimized for additive manufacturing |
Sandvik | Inconel 718 | $450 | Excellent high-temperature properties |
ATI Metals | CoCrMo Alloy | $500 | Used widely in medical applications |
Tekna | WC-Co | $600 | Superior wear resistance and toughness |
LPW Technology | NiTi (Nitinol) | $800 | High-quality shape memory alloy powders |
AP&C | Ti6Al4V | $400 | Consistent, high-purity powders |
Makin Metal Powders | CuNi2SiCr | $150 | Excellent electrical conductivity |
Saint-Gobain | Al2O3 | $100 | High-quality ceramic powders |
Comparing Pros and Cons of Various Suppliers
When choosing a supplier, consider the following:
- Price vs. Quality: Some suppliers offer lower prices, but the quality of the powder may not be as consistent. For high-precision applications, investing in a higher-quality product may be worth the additional cost.
- Lead Time: Depending on the supplier, lead times can vary significantly. Make sure to choose a supplier who can meet your production schedule.
- Customer Support: Reliable customer support can be invaluable, especially when dealing with technical issues or questions about the material.
Advantages and Limitations of Highly Spherical Powder
Advantages
- Consistency: The uniformity of highly spherical powders ensures consistent performance across different batches, which is crucial for maintaining product quality in mass production.
- Better Flowability: As mentioned earlier, the spherical shape of these powders allows them to flow more easily through hoppers, nozzles, and other equipment, reducing the risk of clogging and improving the efficiency of the manufacturing process.
- Improved Surface Finish: Spherical powders tend to produce smoother surfaces, which can be particularly beneficial in applications such as additive manufacturing, where post-processing is often required to achieve the desired surface finish.
- Higher Packing Density: The spherical shape allows the powder particles to pack more tightly, leading to higher density and better mechanical properties in the final product.
Limitations
- Higher Cost: The processes used to produce highly spherical powders are typically more expensive than those used to produce irregularly shaped powders, resulting in a higher cost per kilogram.
- Limited Material Availability: Not all metals or alloys can be easily produced in a spherical form, which may limit the selection of materials available for specific applications.
- Processing Challenges: The high packing density of spherical powders can make them more challenging to process in some applications, particularly those that require a specific porosity or bonding characteristic.
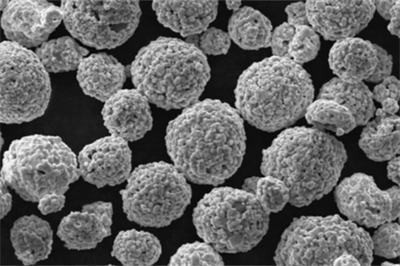
FAQs
Question | Answer |
---|---|
What is highly spherical powder used for? | Highly spherical powders are used in a variety of applications, including additive manufacturing, metal injection molding, and thermal spraying. They are prized for their flowability, packing density, and consistency. |
Why is the shape of the powder important? | The shape of the powder affects its flowability, packing density, and surface area. Spherical powders offer superior performance in these areas compared to irregularly shaped powders. |
How is highly spherical powder made? | Highly spherical powders are typically produced through processes like gas atomization, plasma atomization, or centrifugal atomization, which ensure that the particles are uniformly spherical. |
Are highly spherical powders more expensive? | Yes, the production processes for highly spherical powders are generally more costly than those for irregular powders, which can result in higher prices. |
Can all metals be made into highly spherical powders? | Not all metals can be easily produced in a spherical form. Some materials, due to their physical or chemical properties, may be more challenging to atomize into spherical particles. |
What are the benefits of using highly spherical powder in 3D printing? | Highly spherical powders offer better flowability, higher packing density, and improved surface finish, all of which are critical for high-quality 3D printing. |
What industries benefit the most from highly spherical powders? | Industries like aerospace, medical, automotive, and electronics benefit the most from highly spherical powders due to their need for precision, strength, and consistency. |
How does the purity of the powder affect its performance? | Higher purity powders generally offer better performance in terms of mechanical properties, corrosion resistance, and overall material behavior during processing. |
Is there a difference between different suppliers? | Yes, suppliers can vary in terms of the quality, consistency, and price of their powders. It’s important to choose a supplier that meets your specific needs. |
What are the challenges of working with highly spherical powders? | Some challenges include the higher cost, limited material availability, and potential processing difficulties due to the powder’s high packing density. |
Conclusion
Highly spherical powders are a critical component in modern manufacturing, offering numerous advantages in terms of flowability, packing density, and consistency. From additive manufacturing to metal injection molding, these powders play a vital role in producing high-quality, reliable parts across a range of industries. However, they are not without their challenges, including higher costs and processing complexities. By understanding the unique properties and applications of highly spherical powders, manufacturers can make informed decisions that optimize their production processes and final products.
As technology continues to advance, we can expect the demand for highly spherical powders to grow, particularly in industries where precision and performance are paramount. Whether you’re looking to improve the quality of your 3D printed parts, enhance the durability of medical implants, or simply stay ahead in the competitive world of manufacturing, highly spherical powders offer a pathway to success.