Imagine building a part for a jet engine that can withstand scorching temperatures and relentless wear. Or crafting a heat exchanger that laughs in the face of corrosion and fatigue. This isn’t science fiction; it’s the reality of IN738 powder, a revolutionary material taking the world of 3D printing by storm.
What is IN738 Powder?
IN738 powder, also known as Inconel 738 powder, is a nickel-based superalloy specifically designed for additive manufacturing (AM), the fancy term for 3D printing. It boasts an impressive cocktail of properties that make it the go-to choice for demanding applications:
- Exceptional Strength: Imagine a tiny, metallic Hercules. IN738 powder retains its remarkable strength even at high temperatures, making it perfect for parts under immense stress.
- Undeniable Heat Resistance: Think of a material that shrugs off scorching temperatures like a walk in the park. IN738 powder thrives in environments that would melt lesser materials, making it ideal for jet engines, gas turbines, and other high-heat applications.
- Impregnable Corrosion Resistance: Picture a material that scoffs at rust and corrosion. IN738 powder stands strong against harsh chemicals and extreme environments, ensuring long-lasting performance.
- Superb Oxidation Resistance: Imagine a material that says “no thanks” to oxidation, the process that weakens metals over time. IN738 powder maintains its integrity even at elevated temperatures, extending its lifespan.
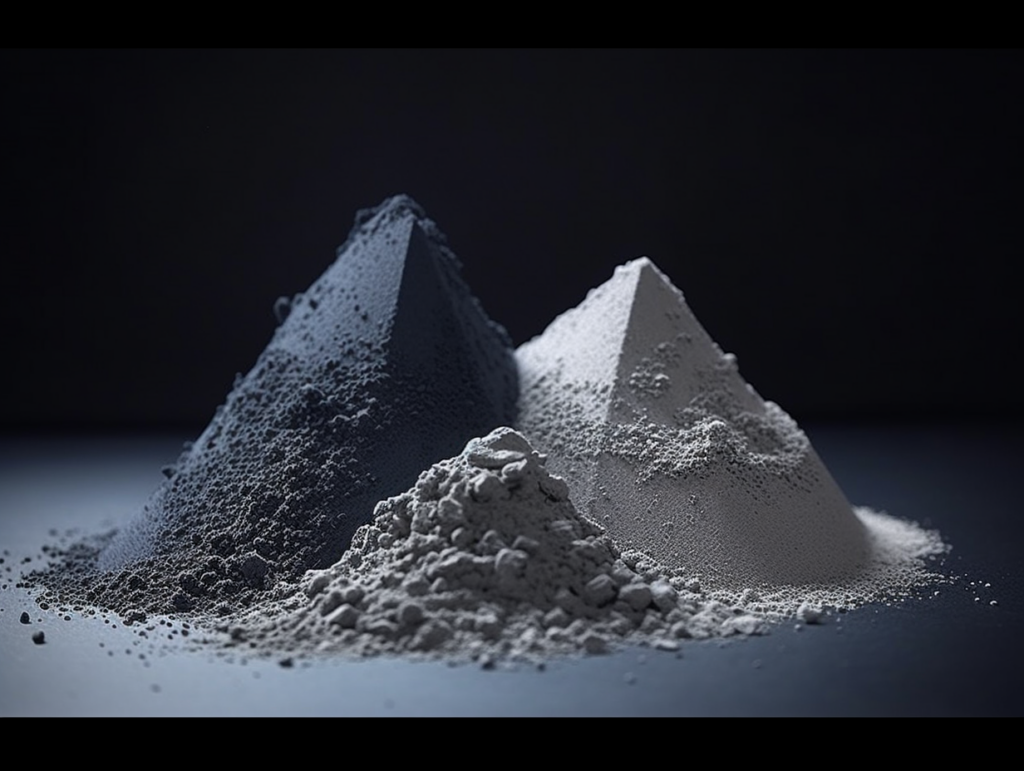
Composition and Properties of IN738 Powder
Property | Description |
---|---|
Base Material | Nickel |
Key Alloying Elements | Chromium, Cobalt, Tungsten, Molybdenum, Aluminum, Titanium |
Melting Point | Around 1390°C (2535°F) |
Density | Approximately 8.2 g/cm³ (0.29 lb/in³) |
Tensile Strength | Up to 1500 MPa (217,500 psi) at room temperature |
Yield Strength | Up to 1300 MPa (189,000 psi) at room temperature |
Elongation | Up to 25% at room temperature |
Applications of IN738 Powder
IN738 powder isn’t a one-trick pony. Its versatility shines through in a wide range of applications, pushing the boundaries of what’s possible:
Application Area | Specific Examples |
---|---|
Aerospace | Turbine blades, combustor liners, afterburner components |
Energy | Heat exchangers, pipes for harsh environments, components for nuclear reactors |
Oil & Gas | Downhole tools, wellhead components, parts for pipelines |
Automotive | High-performance exhaust components, turbocharger housings |
Medical | Implants for extreme loading scenarios |
Specifications, Sizes, and Grades of IN738 Powder
When choosing IN738 powder, it’s crucial to consider the specific requirements of your project. Here’s a breakdown of key factors:
Specification | Description |
---|---|
Particle Size | Typically ranges from 15 to 150 micrometers, impacting flowability and printability |
Sphericity | Ideally, perfectly spherical particles ensure even packing and optimal printing results |
Flowability | Plays a vital role in smooth powder feeding during the 3D printing process |
Grades | Different grades may offer variations in chemical composition and mechanical properties |
Standards | Look for powders adhering to industry standards like AMS 5662 for guaranteed quality |
-
CM247LC Powder | Nickel Alloy Powder
-
0# Pure Nickel powder
-
NiCoCrAlY alloys powders
-
Rene 142 alloy-Rene Powder
-
Haynes 25 Haynes Powder
-
Best Hastelloy C-22 Powder-High temperature alloy Powder for 3D Printing
-
Best Hastelloy C-276 Powder-High temperature alloy Powder for 3D Printing
-
Best Hastelloy N Powder-High temperature alloy Powder for 3D Printing
-
Best Hastelloy B Powder丨High temperature alloy Powder for 3D Printing
A Spectrum of Choices: Popular IN738 Powder Models
The market offers a diverse range of IN738 powder options. Here are ten prominent players to consider:
- AMPA IN738 Powder: Known for excellent flowability and consistent particle size distribution.
- Höganäs AM Hyperion IN738: Boasts superior surface quality and minimal oxygen content.
- LPW IN738 Powder: A favorite for its tight particle size control and high packing density.
- SLM Solutions IN738 Powder: Optimized for laser beam melting processes, ensuring superior printability.
- Carpenter Additive AM 738: Offers a balance between cost and performance, making it a budget-friendly choice.
- Materion IN738 Powder: Renowned for its exceptional mechanical properties
- GE Additive IN738 Powder: Backed by the reputation of GE, this powder promises high quality and consistency.
- Sandvik Osprey IN738: Engineered for demanding aerospace applications, offering exceptional high-temperature performance.
- ExOne IN738CavityMax: Specially formulated for binder jetting additive manufacturing, enabling intricate geometries.
- Proto Labs In738 AM Powder: A reliable option for rapid prototyping needs, ensuring fast turnaround times.
the Pros and Cons Analysis of IN738 Powder
IN738 powder is a game-changer, but like all superheroes, it has its own set of strengths and weaknesses:
Pros
- Unmatched Performance: IN738 powder delivers exceptional strength, heat resistance, corrosion resistance, and oxidation resistance, making it ideal for demanding applications.
- Design Freedom: 3D printing unlocks unparalleled design possibilities. IN738 powder allows for the creation of complex, lightweight parts that would be impossible with traditional manufacturing.
- Reduced Waste: Unlike traditional methods that generate significant scrap, 3D printing with IN738 powder minimizes material waste.
- Rapid Prototyping: The ability to create functional prototypes quickly allows for faster design iterations and product development cycles.
Cons
- Higher Cost: Compared to traditional manufacturing techniques, 3D printing with IN738 powder can be more expensive, especially for larger parts.
- Surface Finish: While improving, the surface finish of 3D printed parts may require additional post-processing compared to machined components.
- Limited Availability: Although gaining traction, IN738 powder availability might be restricted compared to more common materials.
- Printing Expertise: Successful 3D printing with IN738 powder requires specialized equipment and skilled operators.
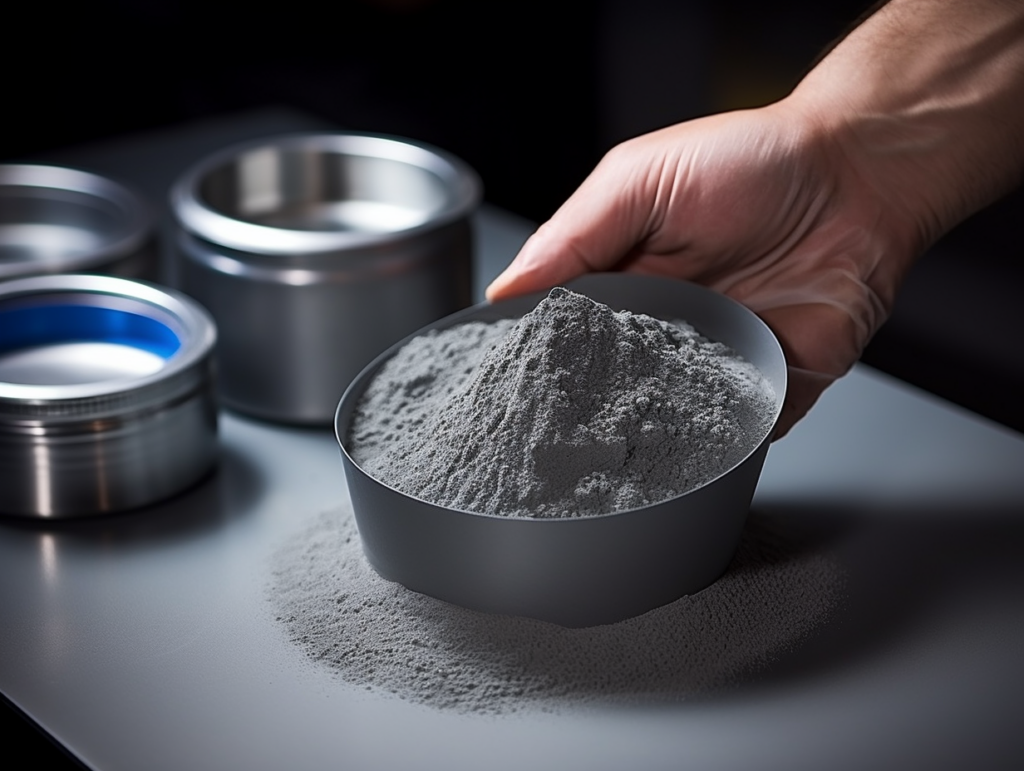
FAQ
Here are some frequently asked questions to help you decide if IN738 powder is the right fit for your project:
Q: What are the alternatives to IN738 powder?
A: Several other metal powders are suitable for 3D printing, each with its own advantages and limitations. Common alternatives include stainless steel powders, titanium alloys, and aluminum alloys. The best choice depends on the specific requirements of your application.
Q: How is IN738 powder processed after 3D printing?
A: IN738 parts may undergo various post-processing steps such as heat treatment, hot isostatic pressing (HIP), and machining to achieve the desired final properties and surface finish.
Q: What are the safety considerations when working with IN738 powder?
A: IN738 powder, like most metal powders, can be hazardous if inhaled. Proper handling procedures, including using a fume hood and personal protective equipment, are crucial.
The Future of IN738 Powder
IN738 powder is revolutionizing the way we design and manufacture high-performance parts. As technology advances, we can expect to see:
- Reduced Cost: As production scales up and technology improves, the cost of IN738 powder is expected to decrease, making it more accessible for a wider range of applications.
- Improved Printability: Advancements in 3D printing techniques will lead to even better printability of IN738 powder, enabling faster printing speeds and finer feature details.
- New Applications: The unique properties of IN738 powder will continue to unlock new possibilities in industries like medicine, aerospace, and energy.
IN738 powder isn’t just a material; it’s an opportunity to push the boundaries of what’s possible. With its exceptional performance and ever-expanding potential, IN738 powder is poised to play a starring role in the future of 3D printing.