If you’re diving into the world of metallurgy or looking into materials for high-performance engineering, you might have stumbled upon a term that sounds futuristic—Inconel 718 powder. This marvel of modern metallurgy is widely known for its impressive properties, making it a favorite in industries where heat, stress, and corrosion are constant threats. But what is Inconel 718, and what makes it so special? In this article, we’ll explore everything you need to know about Inconel 718 powder, including its properties, types, applications, pros and cons, and more.
Let’s break it down piece by piece and make this as engaging and informative as possible.
Overview of Inconel 718 Powder
Inconel 718 is a nickel-based superalloy that’s highly resistant to corrosion, oxidation, and high temperatures. But the real magic lies in its powdered form, which offers exceptional flexibility for advanced manufacturing methods like 3D printing, metal injection molding, and additive manufacturing. Used widely in aerospace, automotive, and oil and gas industries, Inconel 718 powder can take on the most demanding environments with ease.
Here’s a quick summary of why this metal powder is such a game-changer:
- Heat Resistance: Inconel 718 maintains its strength at temperatures up to 700°C (1292°F), making it ideal for extreme conditions.
- Corrosion Resistance: Perfect for high-saline or corrosive environments like those found in deep-sea or oil extraction industries.
- Formability: In powdered form, Inconel 718 can be used in various advanced manufacturing processes, offering near-net shape forming and reducing waste.
- High Strength: Thanks to its precipitation-hardening properties, Inconel 718 offers excellent tensile strength even at elevated temperatures.
Now, let’s delve into the specifics.
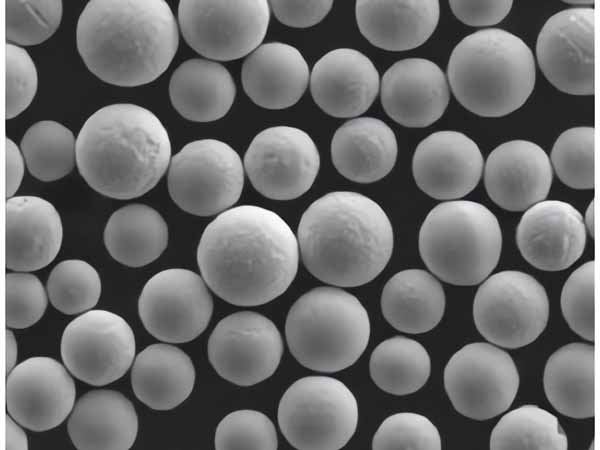
Composition of Inconel 718 Powder
What exactly is Inconel 718 made of? Like any superalloy, the composition is meticulously designed to give it its superpowers. The following table breaks down the primary elements in Inconel 718 powder:
Element | Percentage (%) |
---|---|
Nickel (Ni) | 50-55 |
Chromium (Cr) | 17-21 |
Iron (Fe) | Balance |
Niobium (Nb) | 4.75-5.5 |
Molybdenum (Mo) | 2.8-3.3 |
Titanium (Ti) | 0.65-1.15 |
Aluminum (Al) | 0.2-0.8 |
Carbon (C) | 0.08 max |
Cobalt (Co) | 1.0 max |
This unique composition is precisely what gives Inconel 718 its remarkable mechanical properties.
How does this composition affect performance?
- Nickel (Ni) and Chromium (Cr) provide corrosion and oxidation resistance.
- Niobium (Nb) contributes to the strengthening mechanism, thanks to precipitation hardening.
- Molybdenum (Mo) enhances the alloy’s ability to handle heat and stress.
Each of these elements works in harmony, allowing Inconel 718 powder to excel where other materials fall short.
Characteristics of Inconel 718 Powder
Now that we’ve broken down its composition, let’s dive into the key characteristics that make Inconel 718 powder stand out.
Characteristic | Description |
---|---|
High-Temperature Stability | Maintains strength and performance up to 700°C (1292°F). |
Corrosion Resistance | Excellent in harsh environments, including seawater and acids. |
Oxidation Resistance | Withstands oxidative conditions without degrading. |
Fatigue Resistance | Endures stress and fatigue over time without cracking. |
Precipitation Hardening | Achieves high strength through heat treatment. |
Formability in Powdered State | Ideal for 3D printing and advanced manufacturing methods. |
In simple terms, this superalloy can take on extreme environments that would degrade or weaken other materials.
Types of Inconel 718 Powder
There’s more than one type of Inconel 718 powder to consider, depending on the specific application and manufacturing method. Here are some popular models:
Model | Description |
---|---|
Inconel 718 AM | Optimized for Additive Manufacturing, particularly for 3D printing applications. |
Inconel 718 HD | High-density variant, perfect for metal injection molding (MIM). |
Inconel 718 LP | Low porosity, ideal for aerospace components that require tight tolerances. |
Inconel 718 FG | Fine-grained powder, best suited for detailed and high-precision components. |
Inconel 718 H | Hot isostatic pressing (HIP) powder for parts that need high mechanical properties and density. |
Inconel 718 PW | Powder Welding model for welding applications, designed to reduce oxidation during the welding process. |
Inconel 718 SP | Specialized powder for powder bed fusion, ideal for laser sintering and electron beam melting (EBM). |
Inconel 718 GP | General-purpose variant, cost-effective for broader applications. |
Inconel 718 R | Refractory-grade powder, optimized for high-temperature and high-stress environments. |
Inconel 718 M | Machinable-grade powder, specifically for high-precision machining. |
Each model has been tailored to meet specific industry needs, whether it’s advanced manufacturing, welding, or extreme environmental conditions.
Applications of Inconel 718 Powder
Where can you find Inconel 718 powder being used? This superalloy is truly versatile and finds applications in numerous industries. Below is a table showcasing its common applications.
Industry | Application |
---|---|
Aerospace | Jet engines, turbine blades, exhaust systems, fasteners, and rocket engines. |
Automotive | Turbocharger rotors, exhaust manifolds, and other high-temperature components. |
Oil and Gas | Downhole tools, tubing, valves, and offshore drilling equipment. |
Power Generation | Gas turbines, heat exchangers, and other high-efficiency power components. |
Marine | Seawater pumps, valves, and submersible components. |
Nuclear | Reactor core components and cooling systems. |
3D Printing | Additive manufacturing of complex parts and prototypes. |
Medical Devices | High-strength, corrosion-resistant surgical tools and implants. |
The versatility of Inconel 718 powder stems from its combination of heat and corrosion resistance, high strength, and fatigue resistance. It’s no surprise that it’s used in industries ranging from aerospace to nuclear power.
Specifications, Sizes, and Standards of Inconel 718 Powder
For engineers and manufacturers, understanding the technical specifications, sizes, and standards of Inconel 718 powder is crucial. Here’s an overview of key specs:
Specification | Details |
---|---|
Particle Size Range | 15-53 µm, 45-150 µm, depending on application. |
Density | 8.19 g/cm³ (at room temperature). |
Melting Range | 1260-1340°C. |
Tensile Strength | 1000 MPa to 1400 MPa, depending on heat treatment. |
Hardness | 330-370 HB (Brinell Hardness). |
Standards | ASTM B637, AMS 5662, AMS 5663, AMS 5596, UNS N07718. |
Understanding these specs helps in choosing the right type of Inconel 718 powder for your application, whether you’re 3D printing a turbine blade or designing a valve for deep-sea exploration.
Inconel 718 Powder: Pros and Cons
Like any material, Inconel 718 has its advantages and limitations. Let’s break them down to give you a clear comparison.
Pros | Cons |
---|---|
High temperature resistance | Cost: Inconel 718 is relatively expensive. |
Exceptional corrosion resistance | Difficulty in machining: Needs specialized tools. |
Fatigue resistance | High density: Heavier than some alternative alloys. |
Great for additive manufacturing | Long lead times for specialized powder grades. |
Versatile across industries | Requires expertise for handling and processing. |
When it comes to performance in extreme environments, Inconel 718 is tough to beat. However, it’s not always the easiest or cheapest material to work with.
Suppliers and Pricing Details for Inconel 718 Powder
Finding the right supplier and understanding the pricing of Inconel 718 powder can vary depending on the model,
particle size, and quantity you need. Below is a list of potential suppliers and general pricing info.
Supplier | Price per kg (USD) | Notes |
---|---|---|
Carpenter Technology | $150-$300 | High-quality, aerospace-grade powders. |
Höganäs | $180-$350 | Offers fine particle sizes for 3D printing. |
ATI Metals | $160-$320 | Known for consistency in metal powders. |
LPW Technology | $170-$340 | Specializes in additive manufacturing powders. |
Sandvik | $150-$310 | Strong focus on powder metallurgy. |
Prices can fluctuate depending on the order size, custom requirements, and the supplier’s location. Typically, higher precision powders designed for additive manufacturing tend to cost more.
Inconel 718 Powder vs. Other Metal Powders
How does Inconel 718 powder compare to other metal powders used in high-performance applications? Here’s a quick breakdown.
Feature | Inconel 718 Powder | Stainless Steel 316L Powder | Titanium Ti6Al4V Powder |
---|---|---|---|
Temperature Resistance | Up to 700°C (1292°F) | Up to 500°C (932°F) | Up to 600°C (1112°F) |
Corrosion Resistance | Excellent | Good | Excellent |
Density | 8.19 g/cm³ | 8.0 g/cm³ | 4.43 g/cm³ |
Strength at High Temps | High | Medium | High |
Cost | High | Medium | High |
Compared to stainless steel and titanium powders, Inconel 718 offers superior temperature resistance but comes with a higher price tag and greater density.
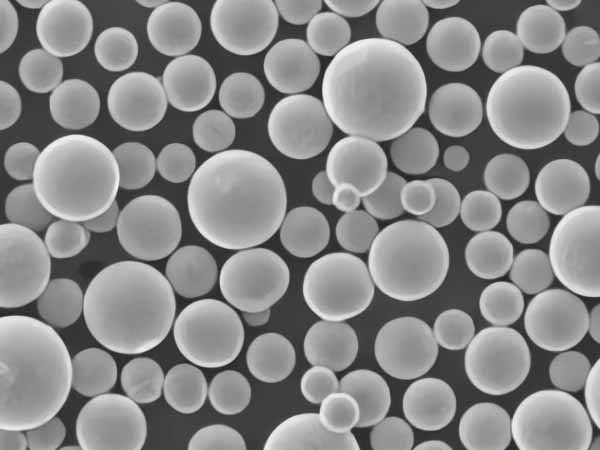
FAQ
Question | Answer |
---|---|
What is Inconel 718 powder mainly used for? | Inconel 718 powder is used in aerospace, automotive, oil & gas, power generation, and 3D printing for parts that require high strength and corrosion resistance. |
How is Inconel 718 powder manufactured? | It is typically made through gas atomization, where molten metal is sprayed into fine particles and cooled quickly. |
What are the advantages of Inconel 718 over other superalloys? | Inconel 718 offers a unique combination of high strength, corrosion resistance, and the ability to withstand high temperatures. |
Is Inconel 718 powder expensive? | Yes, Inconel 718 powder is more expensive than other metal powders like stainless steel but is often necessary for high-performance applications. |
Can Inconel 718 be 3D printed? | Yes, Inconel 718 is commonly used in additive manufacturing (3D printing) for creating complex and high-performance parts. |
Conclusion
Inconel 718 powder is a metallurgical wonder, engineered for environments where other materials fail. Its heat resistance, corrosion resistance, and adaptability to advanced manufacturing methods make it a go-to material in industries like aerospace, oil & gas, and power generation. Whether you’re 3D printing an intricate turbine blade or forging components for deep-sea exploration, Inconel 718 powder offers unmatched performance. However, its high cost and specialized handling requirements mean it’s not always the best option for every project.
If you’re considering Inconel 718 powder for your next project, carefully weigh its pros and cons and consider your specific needs. With its range of models and applications, it’s clear that Inconel 718 is not just another material—it’s a superalloy designed for the toughest jobs on earth.